410 Stainless Steel - 1.4006 - X12Cr13 - S41000 - ~SUS 410
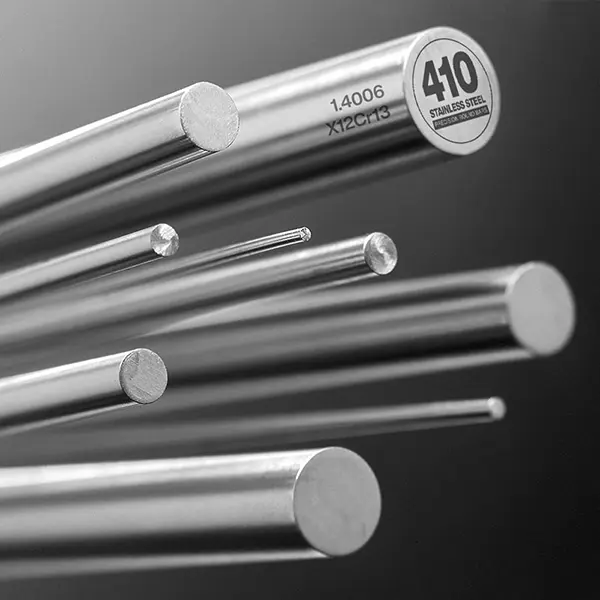
410 Stainless Steel - 1.4006 - X12Cr13 - S41000 - ~SUS 410
Back to Steel OverviewGround Flat Stock and $mart Flat Stock comes always in a machined condition, that means:
NO decarburization on the surfaces (decarburization leads to unreliable components and tools)
Less dirt on your machines during further processing – nothing but clean chips
Stress-relieved flat steel avoids warping of components during further machining
Get the close-to-finish-size thickness and width you need for the components you plan
Ground Flat Stock and $mart Flat Stock comes always in a machined condition, that means:
NO decaburization on the surfaces (decarburization leads to unreliable components and tools)
Less dirt on your machines during further processing – nothing but clean chips
Stress-relieved flat steel avoids warping of components during further machining
Get the close-to-finish-size thickness and width you need for the components you plan
Ground Flat Stock and $mart Flat Stock comes always in a machined condition, that means:
NO decaburization on the surfaces (decarburization leads to unreliable components and tools)
Less dirt on your machines during further processing – nothing but clean chips
Stress-relieved flat steel avoids warping of components during further machining
Get the close-to-finish-size thickness and width you need for the components you plan
410 STEEL PRICE CHART

410 STANDARD VALUES
C
Si
Mn
P
S
Cr
Ni
X12Cr13
approx. 25 HRC (delivery condition) - 31 HRC
max. 252HB
X12Cr13
approx. 25 HRC (delivery condition) - 31 HRC
max. 252 HB
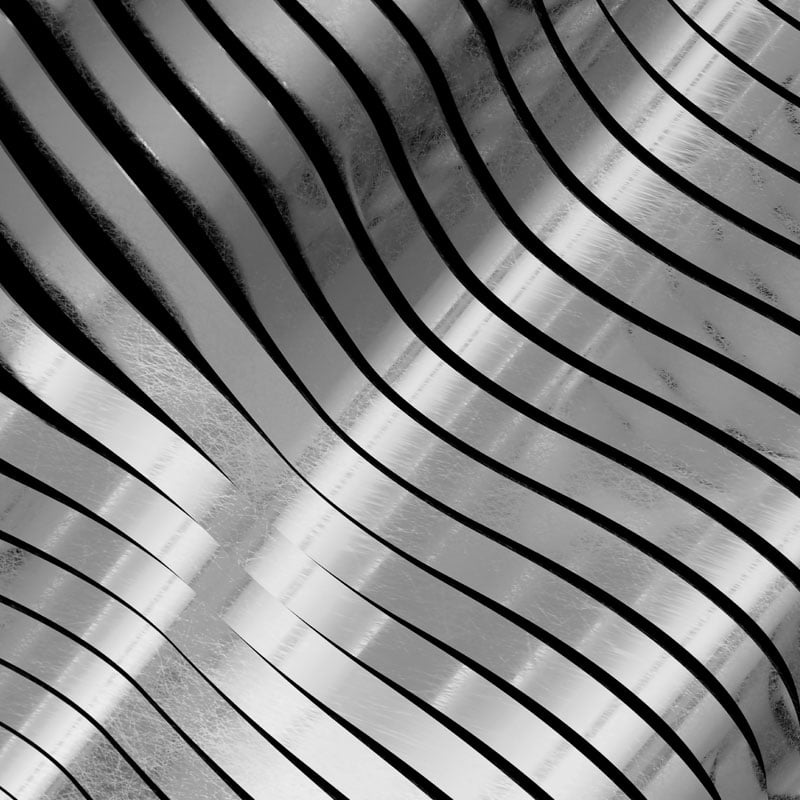

410 PHYSICAL PROPERTIES
410 stainless steel, here in its tempered condition, is machinable and can be used for applications needing high strength, medium heat- and corrosion resistance.
As a martensitic stainless steel it has less corrosion resistance than an austenitic stainless steel, and its useful operating temperature range is limited by loss of ductility at temperatures below zero and loss of strength due to over-tempering at higher temperatures as well as further reducing its corrosion resistance.
By polishing the surface as well as hardening and tempering the corrosion resistance is enhanced.
On a scale where 1 is weak and 6 is good, the corrosion resistance for 410 steel stands at 5.
This process is done at the temperature of 1382 - 2102°F (750 - 1150°C) and then cooled in air.
If smaller plates are being deformed the material should be preheated to 212 - 572°F (100 - 300°C). Heavier deformations should be re-annealed or stress relieved at a temperature of 1202°F (650°C).
In the annealed condition, 410 can be moderately formed by cold working it.

410 TECHNICAL PROPERTIES
Though it has a good corrosion resistance the low carbon content means that it does not hold an edge very well. The 410 has a decent toughness if chipping and breaking stands at the forefront.
In general 410 can be used for low end knives when corrosion resistance and toughness are important and cutting performance is less important.
Typically the density of tool steel 410 is 0.282 lb/in3 (7.80g/cm3) at room temperature.
The yield strength shows how much stress can be applied before a material plastically deforms. Beyond that point the material will not return to its original form if the stresses are taken away but will stay deformed or even break.
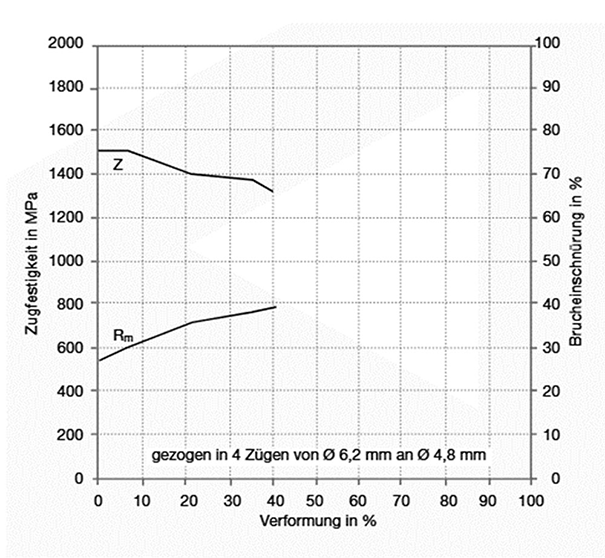
The thermal conductivity for stainless steel 410 is at 30.0 W/(m*K) (208 BTU/(h-ft*°F)) at room temperature.
Medium thermal expansion coefficient | |
10-6m/(m • K) | At a temperature of |
10.5 | 68 - 212°F |
11.0 | 68 - 392°F |
11.5 | 68 - 572°F |
12.0 | 68 - 752°F |
The specific heat capacity of the AISI 410 at room temperature is 0.46 J/g-°C (0.109 BTU/lb-°F). This value shows how much heat is needed to heat 1lb of material by 1 Fahrenheit.
Table of the specific electrical resistivity | |
Value | At a temperature of |
0.60 (Ohm*mm²)/m | 68°C |
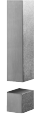
HIGHEST PRECISION!
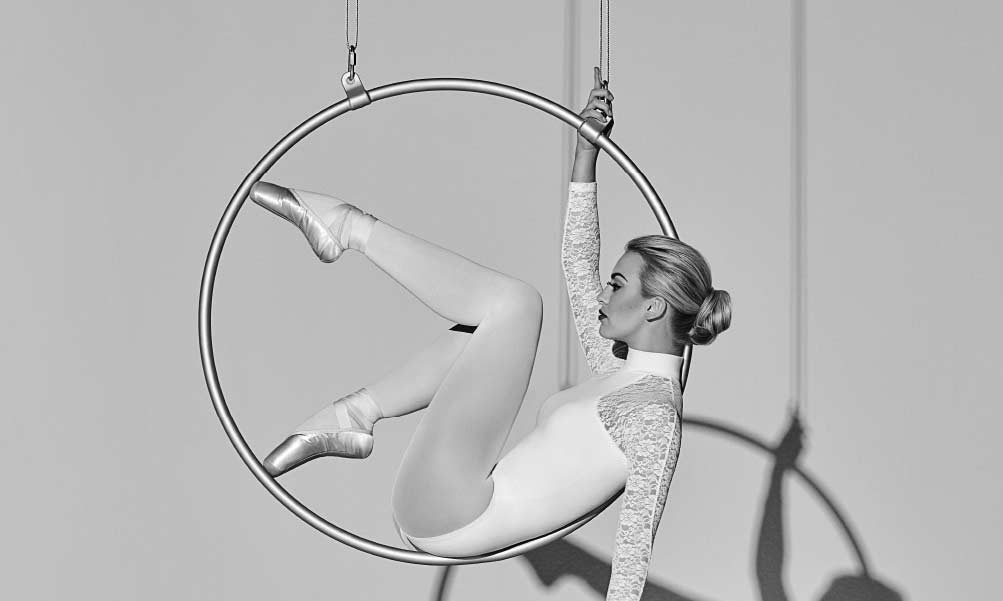
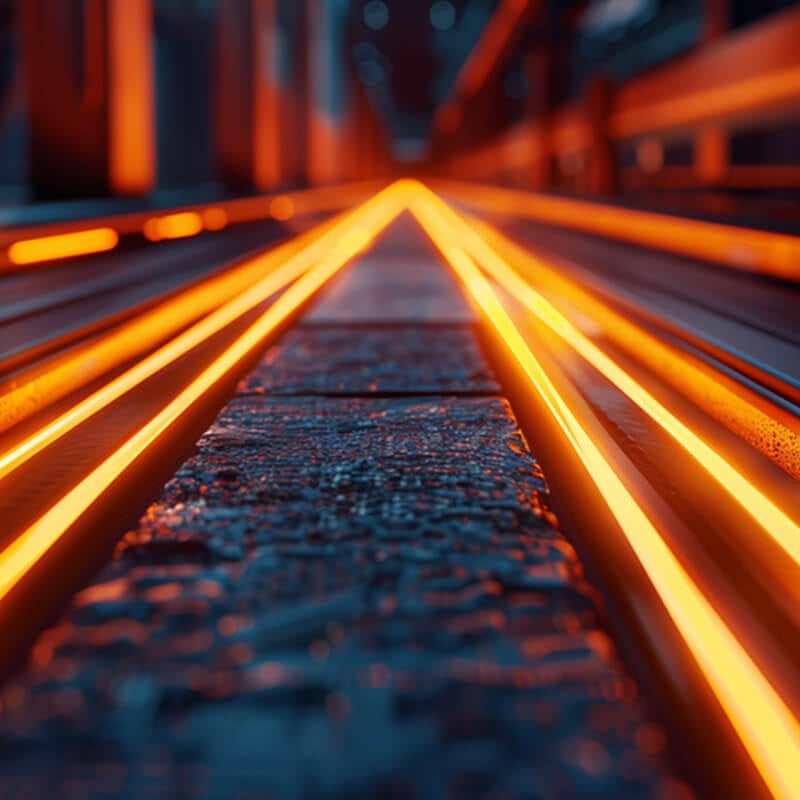

410 PROCEDURE
Quenching needs to be done rapidly to achieve hardening.
• Air: Forced air is used for more intricate or thinner parts or where the quenching speed is not as important.
• Oil: A common method for martensitic steel. Oil extracts the heat out of the parts and cools them. It may be preheated which allows a more uniform quenching.
• Water/Water Polymer Mixture: These quenching mediums are used when a higher hardness is wanted. Care has to be taken as these mediums can lead to higher stresses and may lead to cracking.
Heat the material to 1100 - 1400°F (593 - 760°C) and hold for 1 - 4 hours and finish with air cooling. Exact temperatures and holding times depend on the final mechanical properties that should be achieved.
Tempering the 410 aids to improve toughness and reduces brittleness left by quenching.
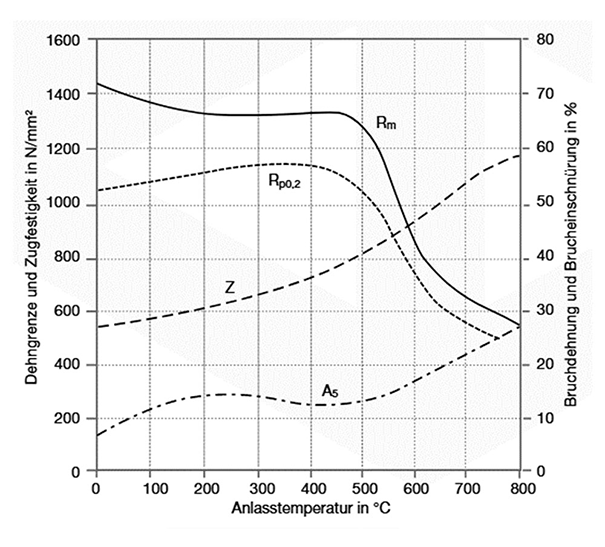

410 SURFACE TREATMENT
Note:
Care has to be taken during this process as the process produces dust and small parts might be propelled back. Protective gear like masks, helmets and protective clothing should be worn and adequate ventilation or dust extraction should be provided.

410 PROCESSING
On a scale where 1 is weak and 6 is good, the machinability of 410 reaches a score of 3.
In the annealed or tempered condition this steel grade is easily machined. It is not recommended to machine this material when hardened to more than 30 HRC as machining becomes difficult then.
EDM is used for parts made from one individual piece, for cutting dies or when making intricate shapes. There are various methods to erode various materials, some of them are for example wire erosion, spark erosion or die sink erosion.
Dimensional changes happen naturally while heating, where steel expands, and cooling, where it contracts, during stress relieving or by uneven heating or cooling where the material may distort.
The 410 stainless undergoes phase changes during the heat treatment and transforms from ferrite to austenite during heating and from austenite to martensite while being quenched. The changes in the crystal structure can lead to dimensional changes.
Dimensional changes can be prevented or reduced by controlled heating and cooling processes, using a pretreatment stress relieving before the heat treatment, choosing the quenching medium carefully and where possible manufacturing parts with a machining allowance before heat treatment and then machining them to the final dimension after the heat treatment.
Forge the work piece in the temperature range of 2156 - 1742°F (1180 - 950°C) and finish the process with a slow cool in the furnace or in dry ash or other material promoting a slow cooling period.
Pre-heat the work piece to 302 - 500°F (150 - 260°C), post-weld annealing should be done to reduce possible cracking.
As coarse grain formation is expected in the heat affected zone, welding should be carried out with an, as low operating energy as possible.
Due to the high strength that can be achieved with this steel and because of the possibility of embrittlement, the use of gas containing hydrogen and nitrogen must be avoided during the welding process.

410 APPLICATION OPTIONS
As a martensitic stainless steel, not as corrosion resistant as an austenitic steel, it has a good corrosion resistance which is often used for cutlery, surgical instruments, valve parts, fasteners, pump shafts, and ball bearings. It can also be used for machine parts, mine ladder rungs, bolts, bushings, screws, and nuts.
• Hydraulic engineering
• Mechanical engineering
• Pump industry
• Oil industry
• Petrochemical industry
• Decorative uses
• Kitchen equipment
• Food industry
• Environmental technology
• Energy technology (hydroelectric power)
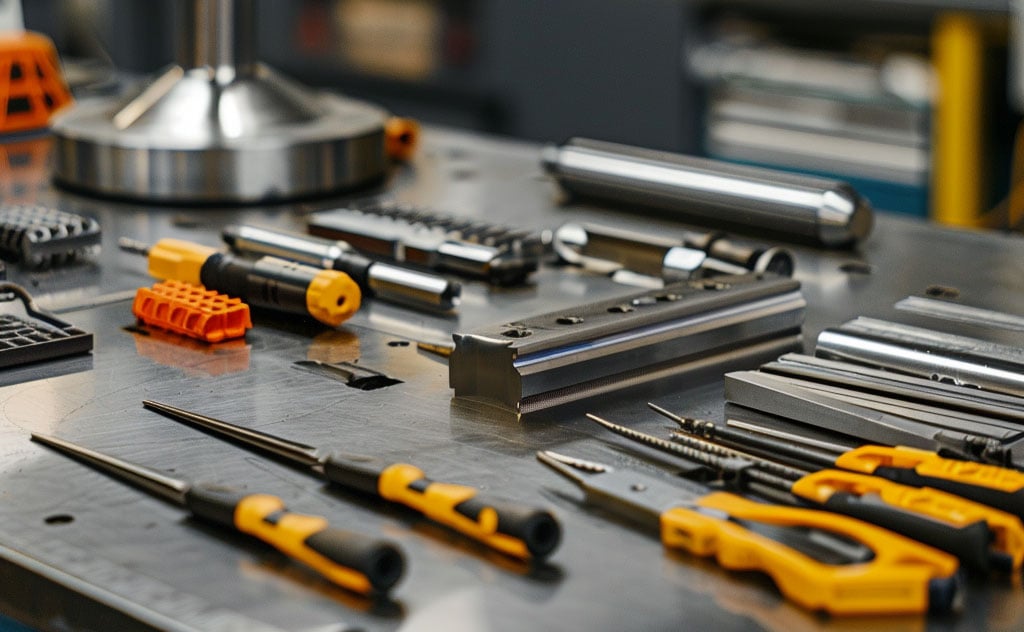

410 CONCLUSION
Practically, this means:
- Martensitic steel
- Hardenable, can achieve high hardness
- High strength
- Medium heat and corrosion resistance
- Can be magentized
- Stainless
- Highly polishable
- Conditionally acid-resistant
- Nitridable
- Erodible
- Working hardness is 25 - 31 HRC
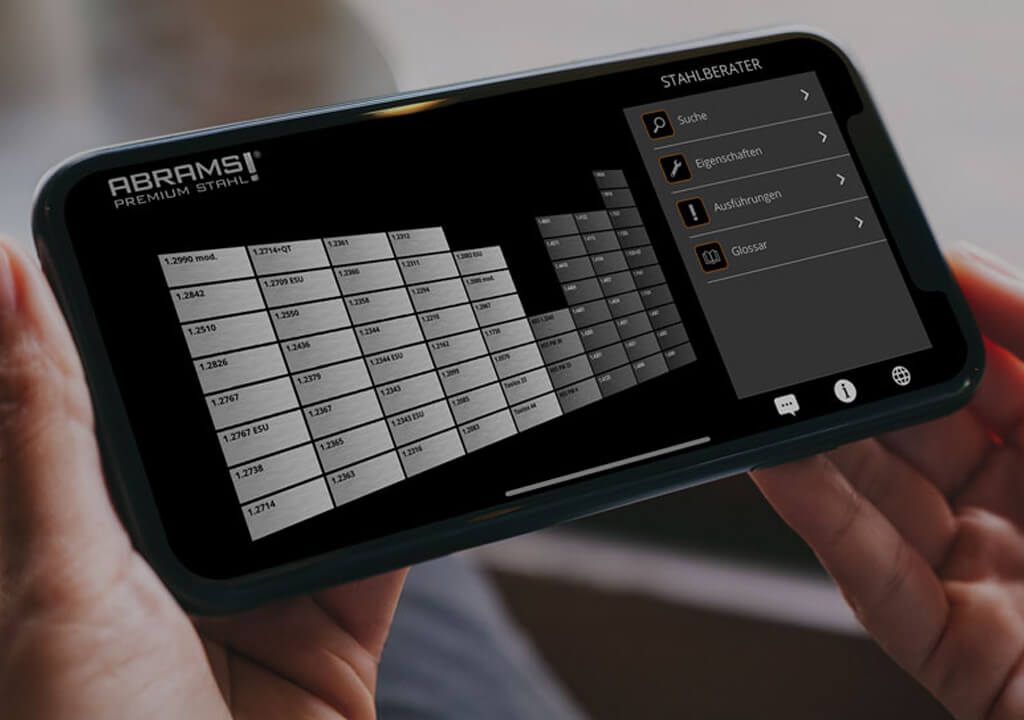

410 ALTERNATIVES
Are you looking for an alternative steel grade?
WE HAVE THE SOLUTION!
With the ABRAMS STEEL GUIDE, you can obtain an alternative or equivalent steel grade with just a few clicks.

410 DATASHEET
Download the technical data sheet in PDF format here.
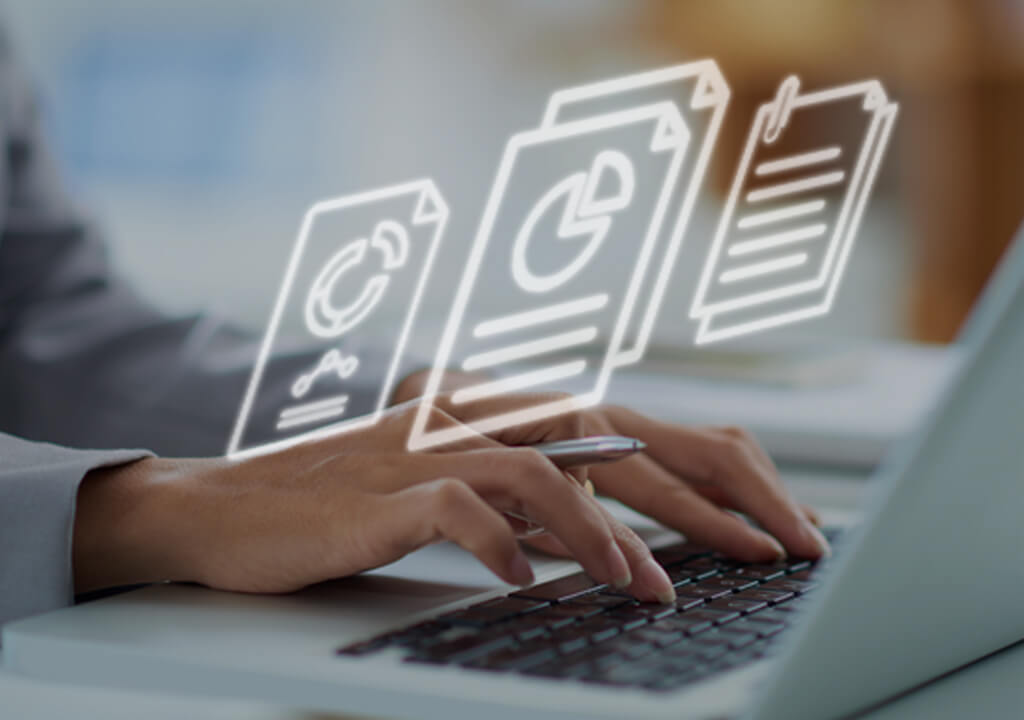
The data shown here has been compiled with the greatest diligence and is regularly updated with regard to the correctness and completeness of its content. The content is indicative only and should not be taken as a warranty of specific properties of the product described or a warranty of suitability for a particular purpose. All information presented is given in good faith and no liability will be accepted for actions taken by third parties in reliance on this information. ABRAMS Industries reserves the right to change or amend the information given here in full or parts without prior notice.