A8 mod. / Chipper Knife Steel - ~1.2360 - ~X48CrMoV8-1-1
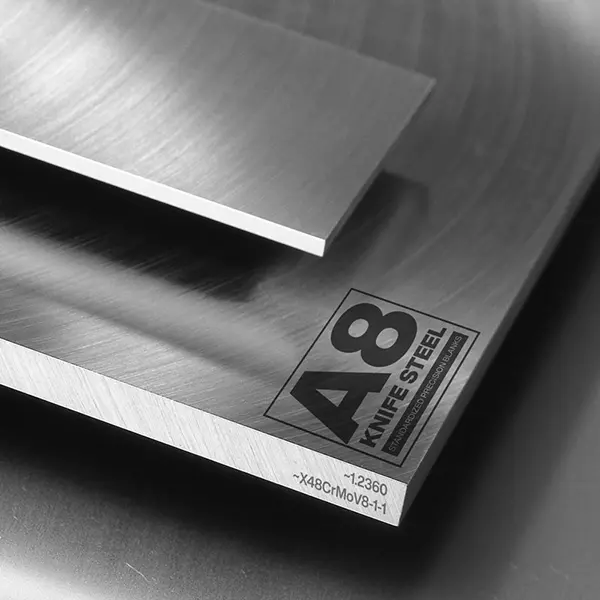
A8 mod. / Chipper Knife Steel - ~1.2360 - ~X48CrMoV8-1-1
Back to Steel OverviewGround Flat Stock and $mart Flat Stock comes always in a machined condition, that means:
NO decarburization on the surfaces (decarburization leads to unreliable components and tools)
Less dirt on your machines during further processing – nothing but clean chips
Stress-relieved flat steel avoids warping of components during further machining
Get the close-to-finish-size thickness and width you need for the components you plan
Ground Flat Stock and $mart Flat Stock comes always in a machined condition, that means:
NO decaburization on the surfaces (decarburization leads to unreliable components and tools)
Less dirt on your machines during further processing – nothing but clean chips
Stress-relieved flat steel avoids warping of components during further machining
Get the close-to-finish-size thickness and width you need for the components you plan
Ground Flat Stock and $mart Flat Stock comes always in a machined condition, that means:
NO decaburization on the surfaces (decarburization leads to unreliable components and tools)
Less dirt on your machines during further processing – nothing but clean chips
Stress-relieved flat steel avoids warping of components during further machining
Get the close-to-finish-size thickness and width you need for the components you plan
A8 MOD. STEEL / CHIPPER PRICE CHART

A8 STEEL MOD. / CHIPPER STANDARD VALUES
C
Si
Mn
P
S
Cr
Mo
V
~X48CrMoV8-1-1
50 HRC - 60 HRC
max. 250 HB
~X48CrMoV8-1-1
50 HRC - 60 HRC
max. 250 HB
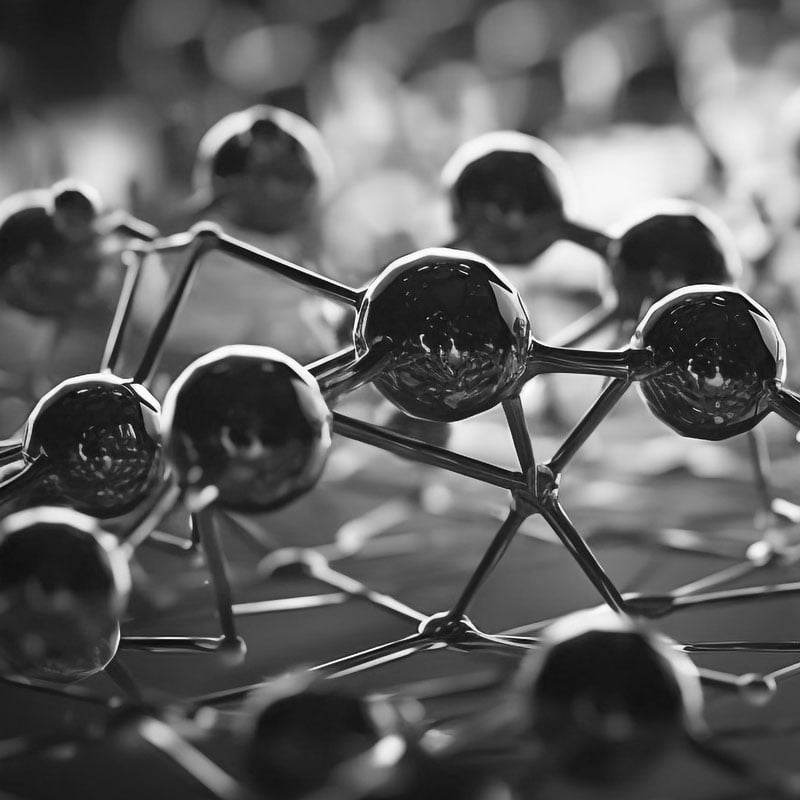

A8 STEEL MOD. / CHIPPER PHYSICAL PROPERTIES
A8 mod., also known as Chipper Knife steel, an air hardening, 8% chromium, cold work tool steel.
This steel is suited for applications which need the combination of high toughness and good wear resistance. It has an excellent dimensional stability during heat treatment.
On a scale where 1 is weak and 6 is good, the corrosion resistance for A8 mod. Steel stands at 3.
Apart from the aforementioned alloys, A8 Steel mod. contains a high carbon content giving it a high hardness.
The working temperature of the A8 mod. steel allows a working temperature in the range of 68 - 932°F (20 - 500°C).

A8 STEEL MOD. / CHIPPER TECHNICAL PROPERTIES
A knife or blade from A8 mod. chipper knife steel is not used for everyday kitchen knives but used as industrial and heavy duty knives.
Typically the density of A8 Steel modified is 0.282 lb/in3 (7.8g/cm3) at room temperature.
When the point has been passed it will be deformed permanently or even break.
The thermal conductivity for A8 mod. chipper steel is at 26.1 W/(m*K) (15090 BTU/(h-ft*°F)) at room temperature.
Heat conductivity table | |
Value | By temperature |
26.1 | 68°F |
27.1 | 392°F |
28.6 | 752°F |
Medium thermal expansion coefficient | |
10-6m/(m • K) | At a temperature of |
11.6 | 68 - 392°F |
11.3 | 68 - 752°F |
The specific heat capacity of A8 mod. at room temperature is 0.460J/g-°C (0.110BTU/lb-°F).
This value shows how much heat is needed to heat 1lb of material by 1 Fahrenheit.
Table of the specific electrical resistivity | |
Value | At a temperature of |
0.19 (Ohm*mm²)/m | 68°F |
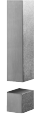
FASTEST POSSIBLE DELIVERY!
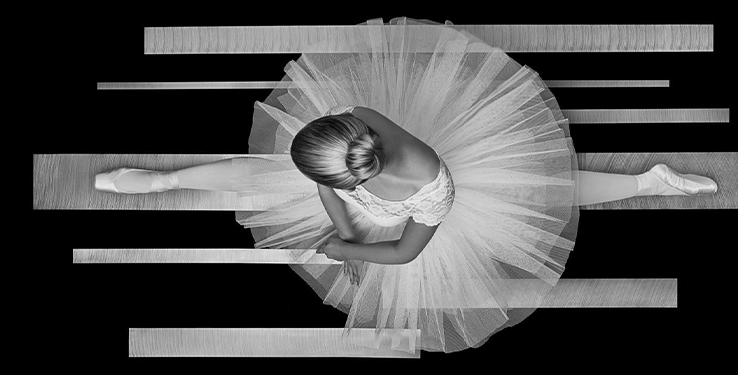
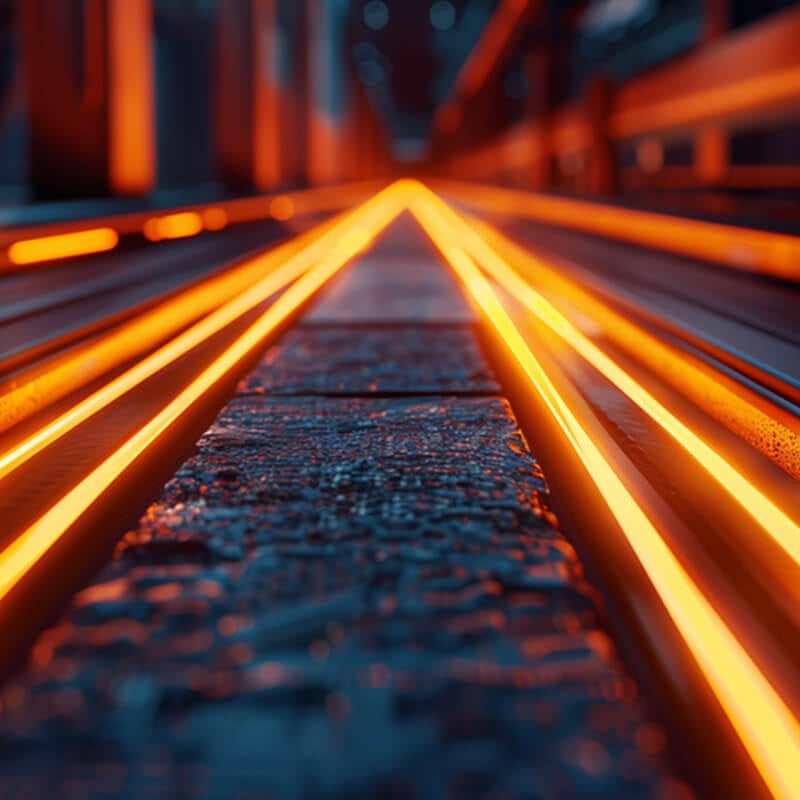

A8 STEEL MOD. / CHIPPER PROCEDURE
Heat parts to no more than 400°F (222°C) per hour until a temperature of 1625°F (885°C) has been reached. Then hold the temperature for 1 hour per inch (25.4 mm) of thickness but no less than 2 hours minimum.
Finish the process by cooling the material down slowly in the furnace in steps of 20°F (10°C) per hour to 1200°F (649°C). Continue to room temperature in the furnace or air.
The process of normalizing is not usually done for this material grade.
Continue to the austenitizing temperature of 1886-1958 (1030-1070°C) in a furnace or in salt and soak for 30 minutes for the first inch (25.4 mm) of thickness and 15 minutes for any further inch (25.4 mm) of thickness.
Size alterations and / or distortion can be avoided by using the softest quenching medium possible. Quench immediately after hardening.
When quenching in oil make sure to preheat the oil to a temperature of approx. 125 - 150°F (50 - 65°C).
• Hot bath (workpiece cooled down to approx. 1022°F (550°C))
• Air
• Pressure gas
• Oil, quench until black at approx. 900°F (482°C), then cool to 150-125°F (66-51°C) in still air
A8 mod. workpieces should be tempered immediately after quenching at a temperature range of 300-600°F (149-316°C).
Hold for 1 hour per inch (25.4 mm) of thickness, but a minimum of 2 hours and cool in air to room temperature.
To double temper any workpieces use a temperature of 900°F (483°C) and over.
For material used for EDM or with a greater cross section of 6 inches (152.4 mm) a soaking time of 4-6 hours is strongly recommended.
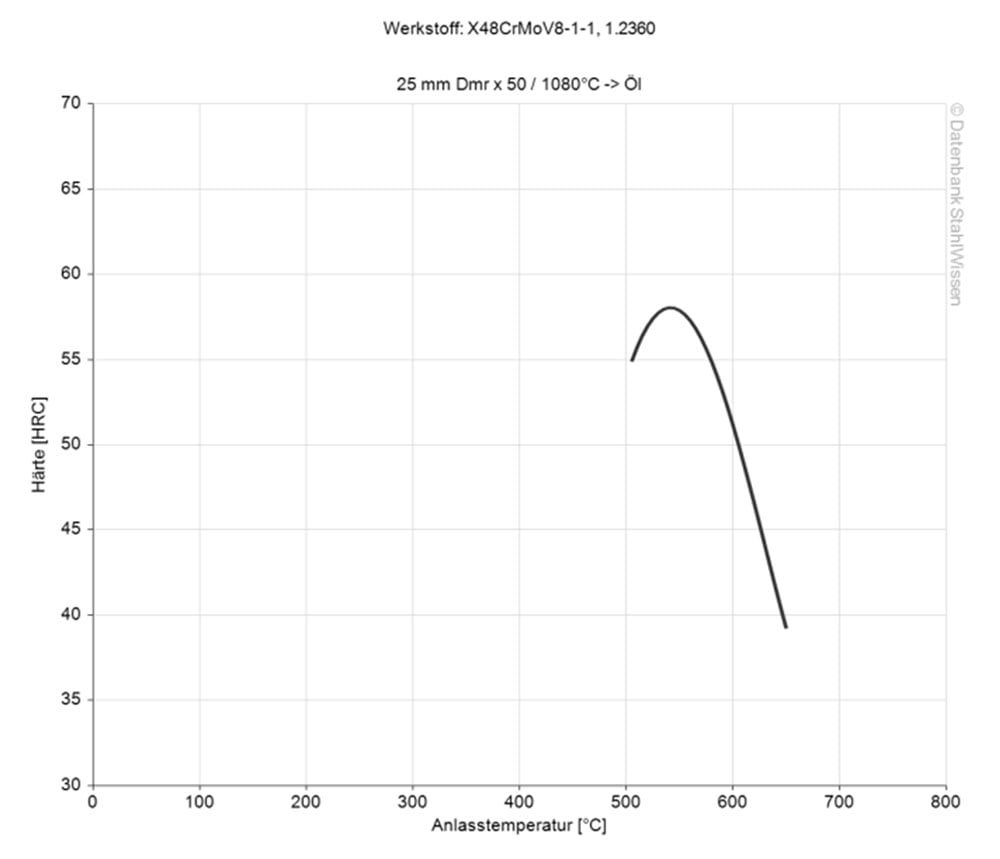
Sub-zero treatment can increase the wear resistance of the A8 mod. as well as improve the dimensional stability and toughness.
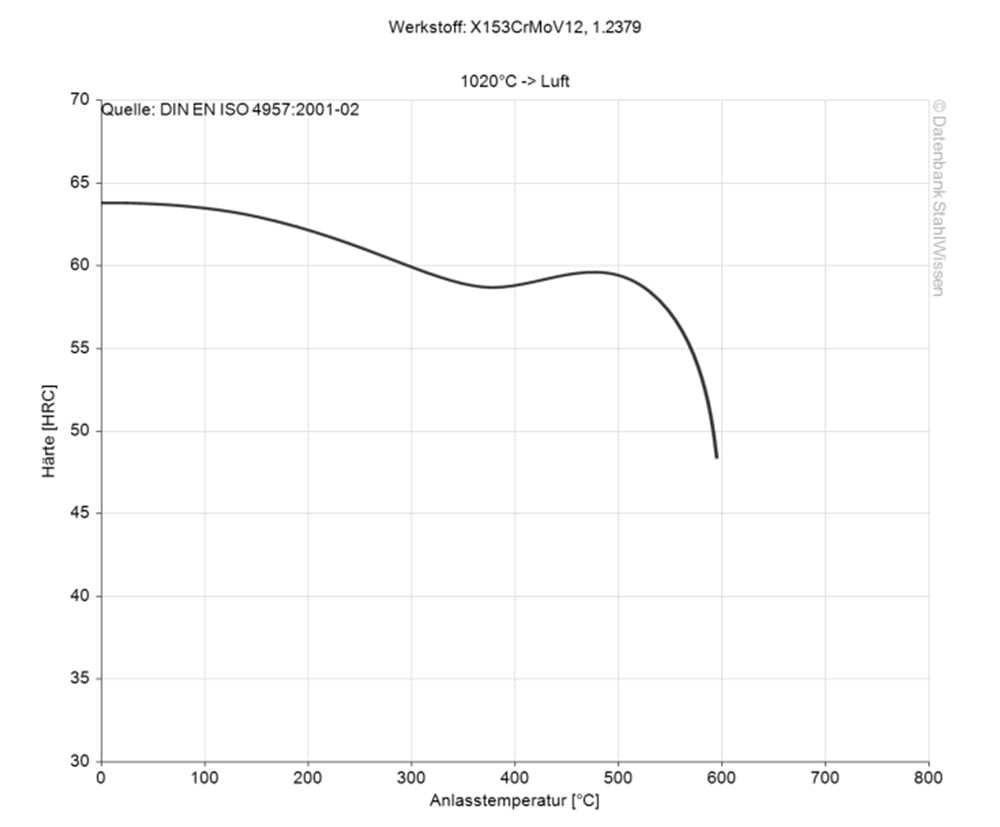
This diagram shows the micro changes at different temperatures which are important during heat treatment. They show the optimum condition for the hardening, annealing and normalizing process.
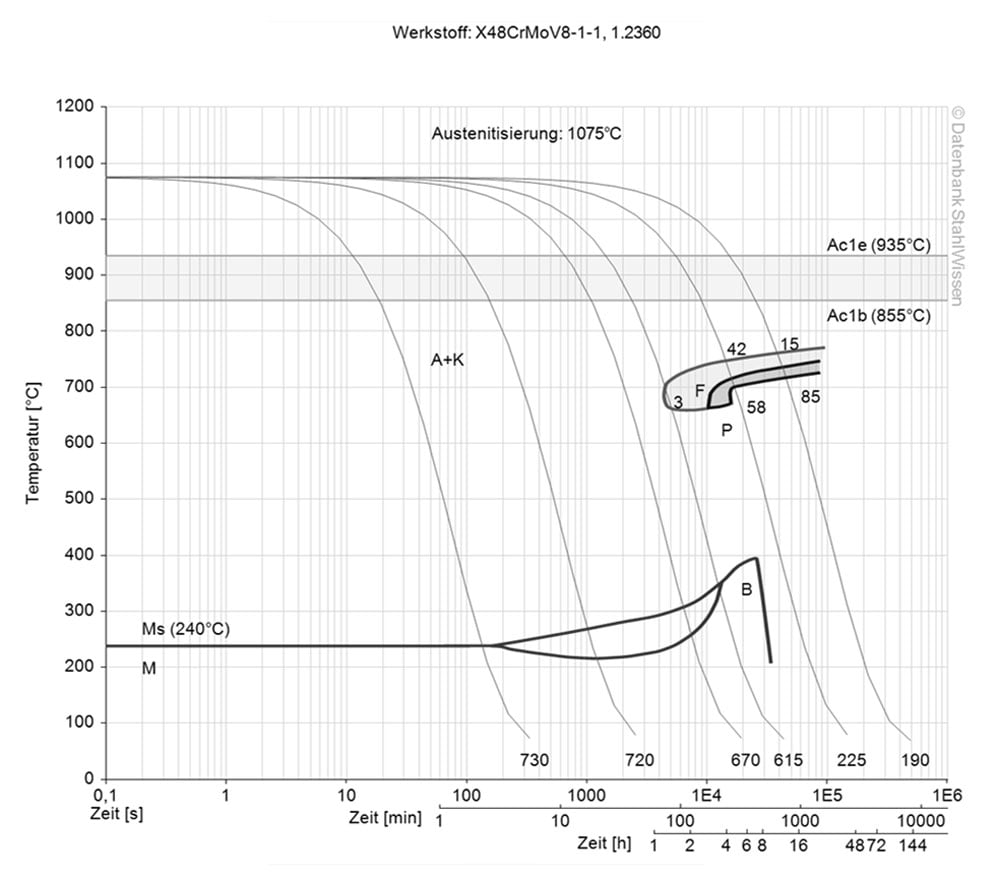

A8 STEEL MOD. / CHIPPER SURFACE TREATMENT

A8 STEEL MOD. / CHIPPER PROCESSING
On a scale where 1 is weak and 6 is good, the machinability of A8 mod. reaches a score of 3.
Care should be taken when machining A8 mod. tool steel. As an air hardening steel removing material should be done swiftly. Machining can produce significant heat and consequently material might harden while being worked.
As A8 mod. is a very hard material that may need specialized tools to machine it. The high wear resistance means that tools might need to be changed or sharpened more often.
EDM can be used for A8 mod. even though the material can be extremely hard at times. As for other material grades EDM can be used for intricate shapes and as there is no physical contact with the material there are no more mechanical forces applied.
EDM is a good choice for parts needing a tighter tolerance or better surface finish. The recast layer has to be removed, if this is not done it might affect the lifespan and performance of the parts.
As a cold work tool steel care has to be taken during heat treatment to avoid overheating and the right quenching medium as well as the quenching method should be considered. To lessen inner stresses pre- and post heating the material is advised.
Forging should be done above the temperature of 1832°F (1000°C) but should never be dropped below 1652°F (900°C). Work pieces should be cooled slowly to avoid possible cracking.
A8 modified chipper steel is generally not suitable for welding.

A8 STEEL MOD. / CHIPPER APPLICATION OPTIONS
A8 modified chipper knives are often chosen for the combination of its wear resistance and toughness of the steel. Workpieces are exposed to forces like shock and impact as well as wear when e.g., chipping trees.
• Punches, Dies and Forming Tools: Breaking and chipping while using the A8 mod. is prevented due to its good wear resistance and excellent toughness. At room temperature A8 mod. is easily formed / shaped as done for cold heading. The toughness of A8 mod. prevents punches and dies from splitting or cracking as well as deformation under pressure.
• Knives, Blades and Cutting Tools: Shearing, slitting or cutting knives and blades need to have a good edge retention but have to handle some impact too. Again the wear resistance and toughness of A8 mod. lends itself for cutting tools, shear blades and slitter knives.
• Blanking tools
• Stamping tools
• Embossing tools
• Forming dies
• Press dies
• Die inserts
• Extrusion dies
• Reinforcements
• Cold extrusion tools
• Tube tools
• Cutting tools
• Industrial knives
• Wood chipping knives
• Veneer knives
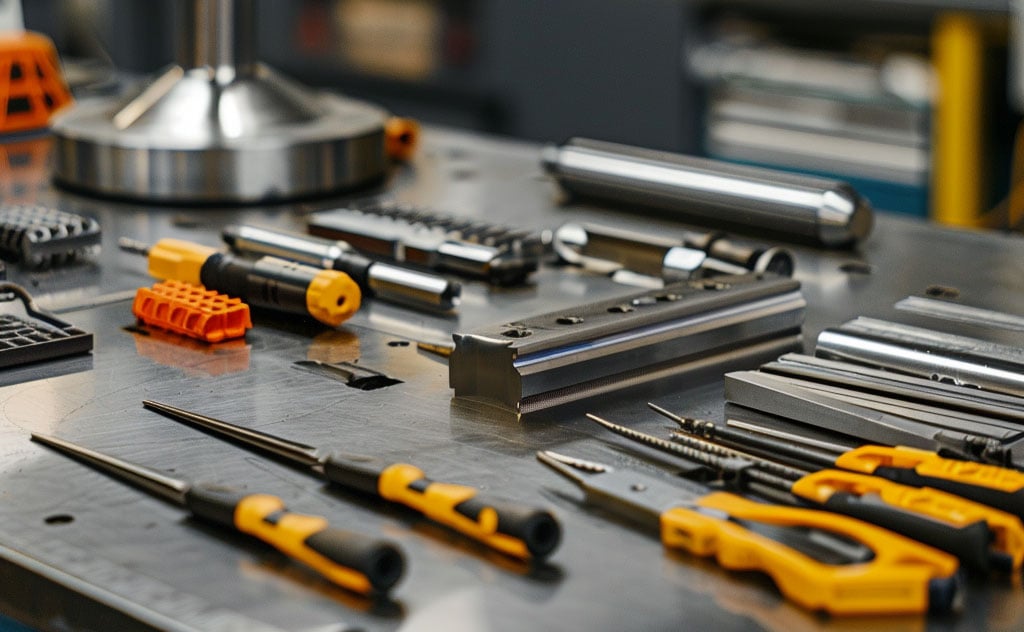

A8 STEEL MOD. / CHIPPER CONCLUSION
- Tool steel
- Chipper-Knife-Steel
- Cold work steel
- Air-hardenable steel
- High wear resistance
- Good tempering resistance
- Universally applicable
- Erodible
- Nitridable
- Not weldable
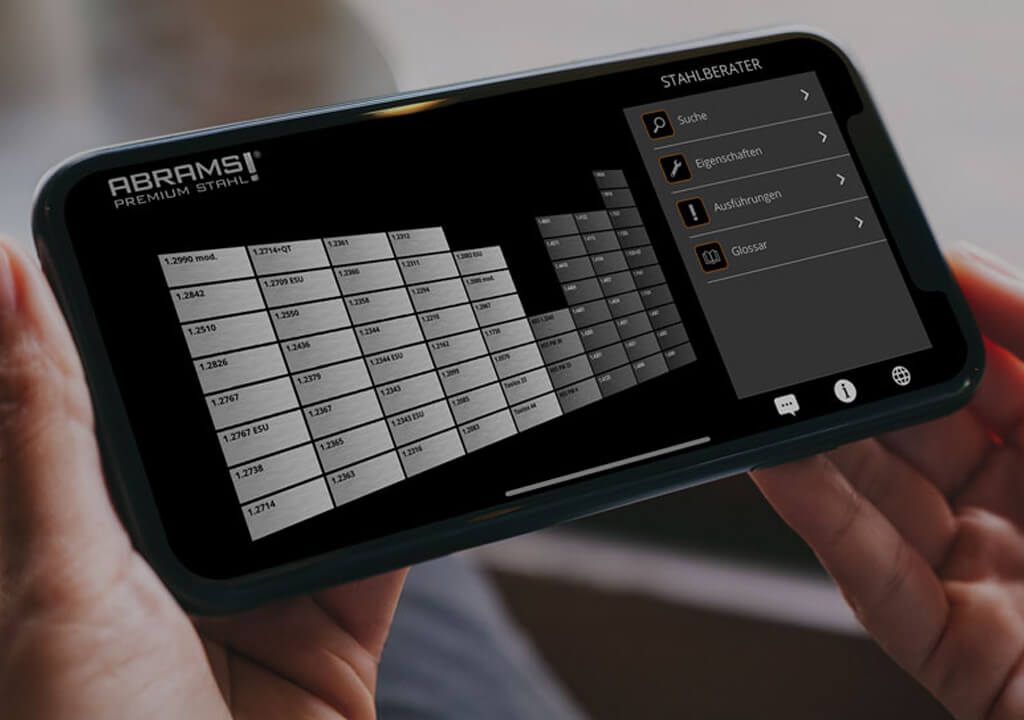

A8 STEEL MOD. / CHIPPER ALTERNATIVES
Are you looking for an alternative steel grade?
WE HAVE THE SOLUTION!
With the ABRAMS STEEL GUIDE, you can obtain an alternative or equivalent steel grade with just a few clicks.

A8 STEEL MOD. / CHIPPER DATASHEET
Download the technical data sheet in PDF format here.
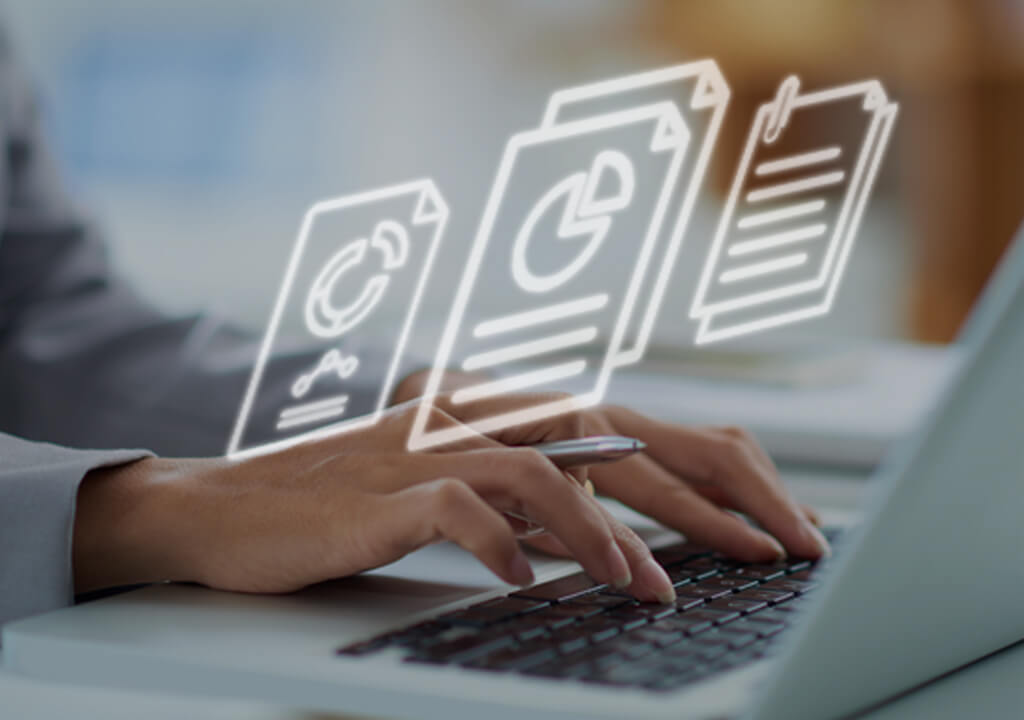
The data shown here has been compiled with the greatest diligence and is regularly updated with regard to the correctness and completeness of its content. The content is indicative only and should not be taken as a warranty of specific properties of the product described or a warranty of suitability for a particular purpose. All information presented is given in good faith and no liability will be accepted for actions taken by third parties in reliance on this information. ABRAMS Industries reserves the right to change or amend the information given here in full or parts without prior notice.