420RM Stainless Steel - DIN 1.4122 - X39CrMo17-1 - Data
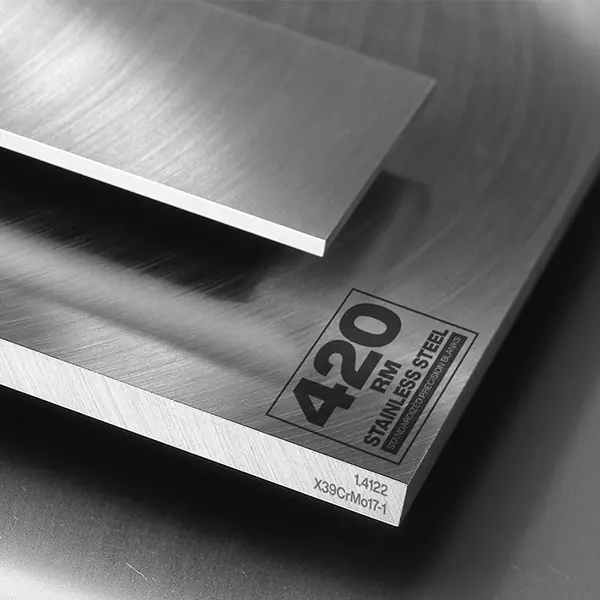
420RM Stainless Steel - DIN 1.4122 - X39CrMo17-1 - Data
Back to Steel OverviewGround Flat Stock and $mart Flat Stock comes always in a machined condition, that means:
NO decarburization on the surfaces (decarburization leads to unreliable components and tools)
Less dirt on your machines during further processing – nothing but clean chips
Stress-relieved flat steel avoids warping of components during further machining
Get the close-to-finish-size thickness and width you need for the components you plan
Ground Flat Stock and $mart Flat Stock comes always in a machined condition, that means:
NO decaburization on the surfaces (decarburization leads to unreliable components and tools)
Less dirt on your machines during further processing – nothing but clean chips
Stress-relieved flat steel avoids warping of components during further machining
Get the close-to-finish-size thickness and width you need for the components you plan
Ground Flat Stock and $mart Flat Stock comes always in a machined condition, that means:
NO decaburization on the surfaces (decarburization leads to unreliable components and tools)
Less dirt on your machines during further processing – nothing but clean chips
Stress-relieved flat steel avoids warping of components during further machining
Get the close-to-finish-size thickness and width you need for the components you plan
420RM STEEL PRICE CHART

420RM STANDARD VALUES
C
Si
Mn
P
S
Cr
Mo
Ni
X39CrMo17-1
approx. 30 HRC (delivery condition) - 48 HRC
max. 325 HB
X39CrMo17-1
approx. 30 HRC (delivery condition) - 48 HRC
max. 325 HB
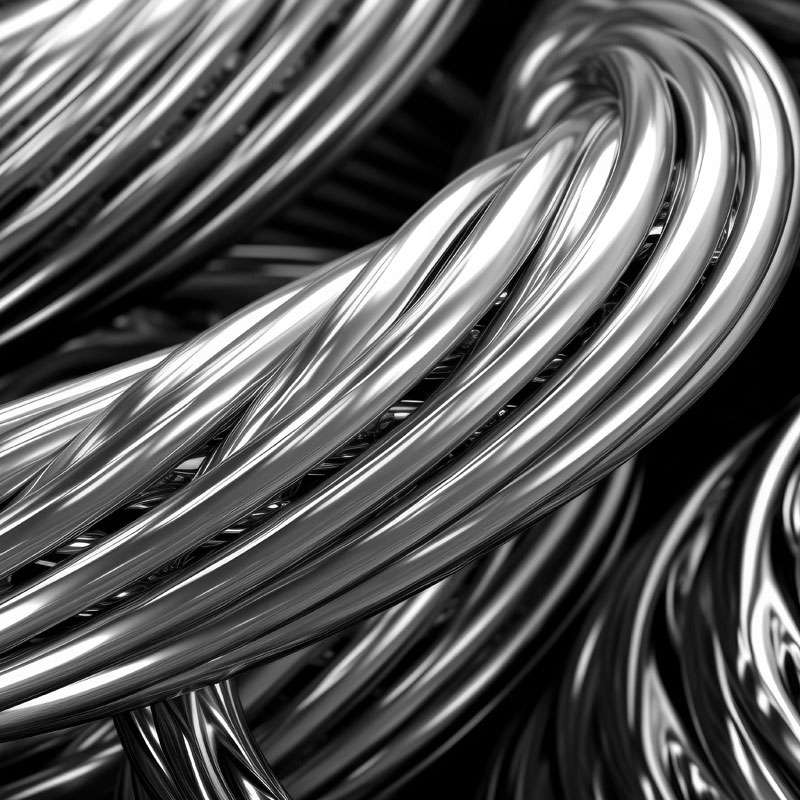

420RM PHYSICAL PROPERTIES
420RM shows outstanding mechanical properties with good corrosion resistance that can be polished to a high gloss finish. Due to the added chromium, up to 17%, it has a higher corrosion resistance compared to stainless steels with for example 13% of chromium.
Though it has a good corrosion resistance, this stainless steel should not be used in seawater but can be used in freshwater for valves or pump shafts for marine- or mechanical engineering for instance.
On a scale where 1 is weak and 6 is good, the corrosion resistance for 420RM stands at 6.
Due to its high chromium content this stainless steel grade does offer a corrosion resistance to organic and citric acids. Corrosion resistance can further be enhanced if the surface is finely ground or polished.

420RM TECHNICAL PROPERTIES
These properties will give a knife a sharp edge with good edge retention and chipping or breaking resistance. The 420RM can be used for knife making due to those well balanced properties.
Typically the density of stainless steel 420 RM is 0.278 lb/in3 (7.7g/cm3) at room temperature.
The yield strength shows how much stress can be applied to a material before it plastically deforms. Beyond this point it does not return to its original form when the stresses have been removed.The material deforms permanently or breaks past that point.
The thermal conductivity for the 420RM stainless steel is at 29 W/(m*K) (201 BTU/(h-ft*°F)) at room temperature.
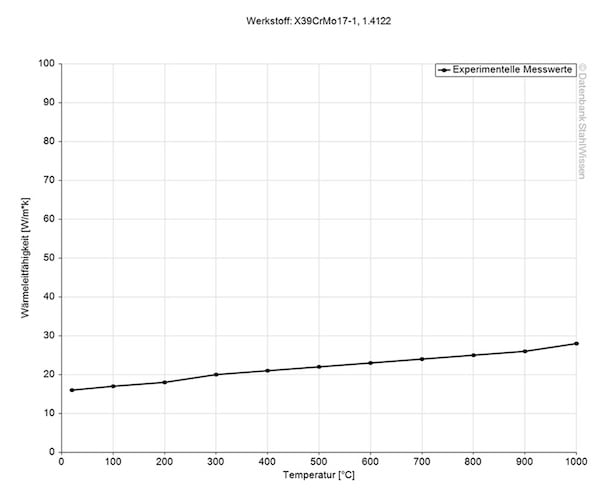
Medium thermal expansion coefficient | |
10-6m/(m • K) | At a temperature of |
10.4 | 68 - 212°F |
10.8 | 68 - 392°F |
11.2 | 68 - 572°F |
11.6 | 68 - 752°F |
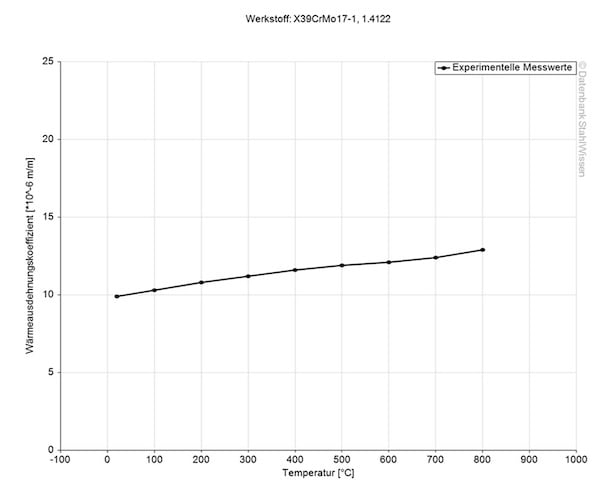
The specific heat capacity of the 420 stainless steel at room temperature is at 0.43 J/g-°C (0.103 BTU/lb-°F).
This value shows how much heat is needed to heat 1lb of material by 1 Fahrenheit.
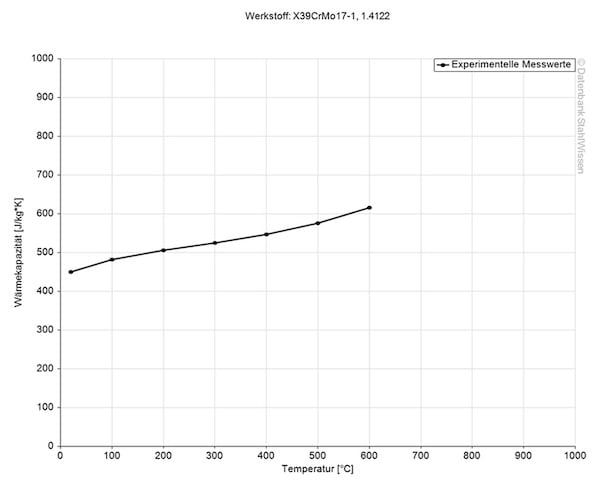
Table of the specific electrical resistivity | |
Value | At a temperature of |
0.65 (Ohm*mm²)/m | 68°F |
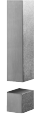
FASTEST POSSIBLE DELIVERY!
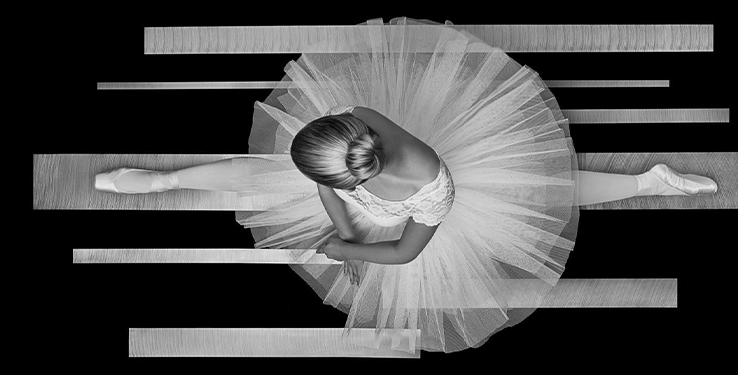
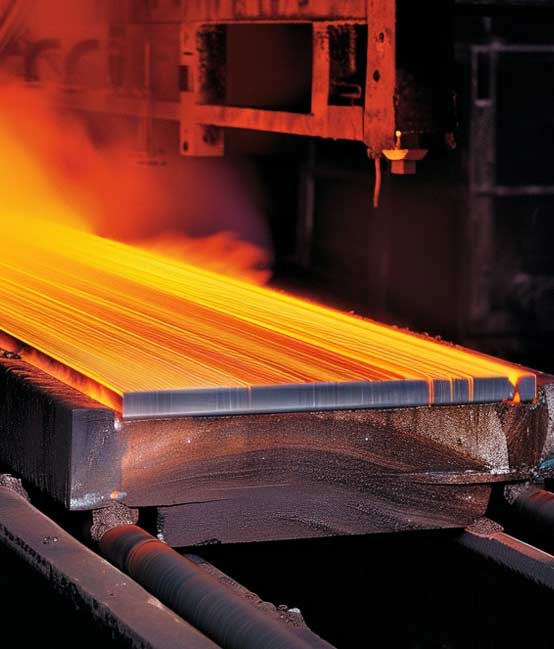

420RM PROCEDURE
The chosen quenching medium depends on the complexity and size of the workpiece to avoid warping and/or cracking.
• Air
• Oil
• Salt- or polymer bath
Heat the material to a tempering range of 1202 - 1382°F (650 - 750°C) then cool in air.
Care must be taken to temper the material as soon as possible after hardening to avoid possible cracking.
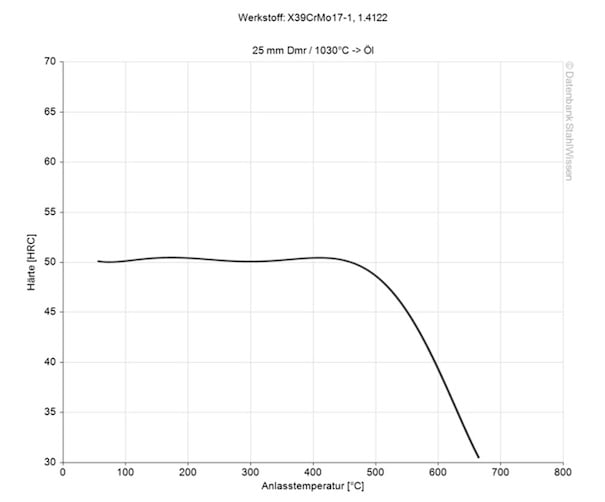
This diagram shows the micro changes at different temperatures which are important during heat treatment. They show the optimum condition for the hardening, annealing and normalizing process.
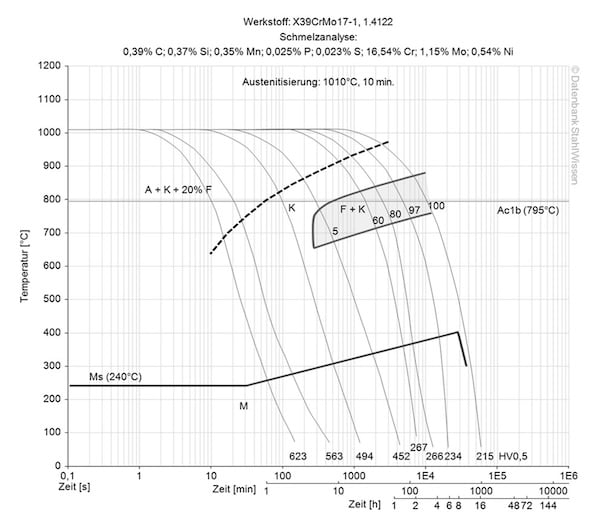
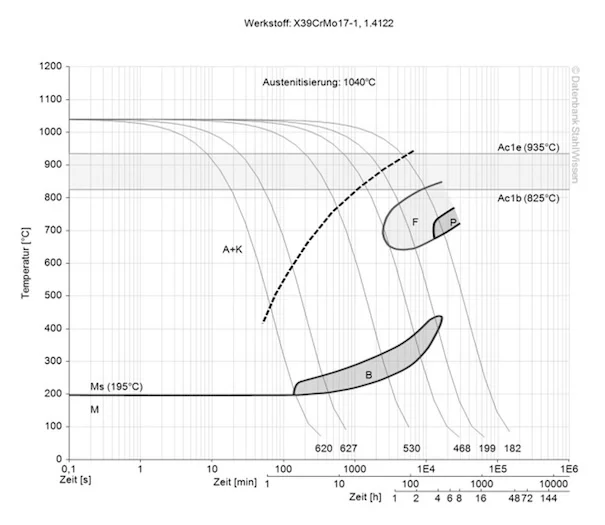
The following diagram shows the structural changes at micro levels over time at a constant temperature. It shows at what temperatures the different phases, e.g., perlite, martensite and bainite start to form.
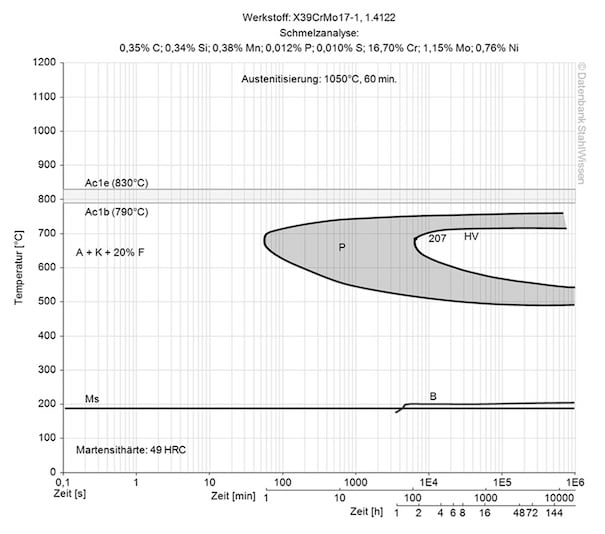

420RM SURFACE TREATMENT
Brushing and polishing will leave a satin finish which is, like black oxide coating, aesthetically appealing but may also reduce product adhesion to the surface.
By polishing, minute groves might be smoothed out which will give contaminants less room to attach and cannot create a starting point to corrosion for example.

420RM PROCESSING
On a scale where 1 is weak and 6 is good, the machinability of 420RM reaches a score of 2.
Forging is done in the temperature range of 2156 - 1742°F (1180 - 950°C), do not let the temperature drop below 1742°F (950°C). Cool the parts in the furnace, dry ash or similar materials promoting slow cooling.
420RM is not normally welded.
If welding is necessary the steel should be preheated to a temperature range of 572 - 752°F (300 - 400°C).
Since a large proportion of non-tempered martensite form in the heat affected zones, it is necessary to temper the material after. As during the tempering treatment, the martensite of the rest of the workpieces are being over-tempered, it is advisable to follow the hardening and tempering processes as stated above.
As in the tempering step, it is important to commence with the heat treatment as close as possible to finishing the welding process to reduce the possibility of cracking.

420RM APPLICATION OPTIONS
The 420RM stainless steel has a good combination of mechanical properties and corrosion resistance which lends itself in applications like cutting tools, mechanical components, pump and valve parts, surgical and dental instruments, the food industry as well as for machine parts.
As a martensitic steel it can be hardened to a high level to provide good wear resistance and a long lasting cutting edge. Care should be taken when exposing the material to environments with chlorides and extreme pH levels.
• Mechanical engineering
• Marine engineering
• Apparatus engineering
• Plastic processing
• Plastic molds
• Extrusion tools
• Press molds
• Fitting tools
• Shafts
• Spindles
• Bolts
• Pistons
• Valves
• Steam valves
• Water valves
• Beater bars
• Fittings parts
• Pump construction
• Pump rods
• Compressor construction
• Compressor parts
• Surgical Instruments
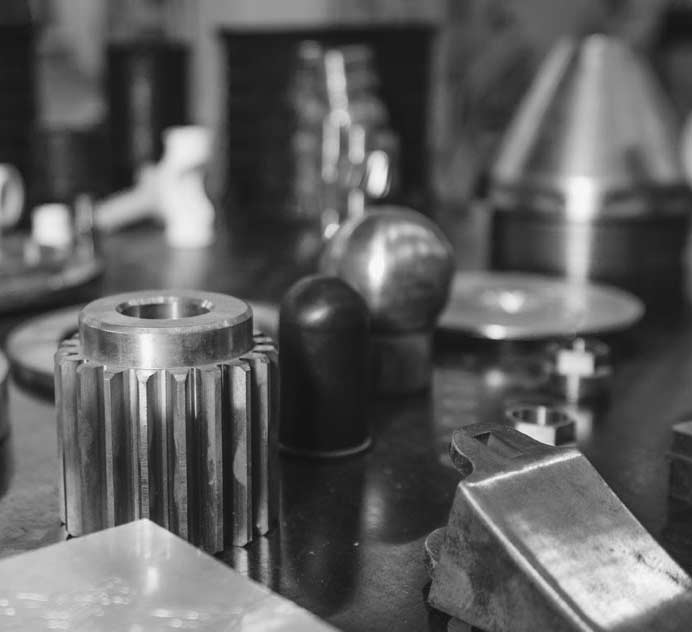

420RM CONCLUSION
- Quenched and tempered chromium steel
- Good polishability
- Good heat resistance
- Good wear resistance
- Very good mechanical properties
- Acid resistant
- Corrosion resistant
- Magnetizable
- Nitridable
- Polishable
- Poor weldability
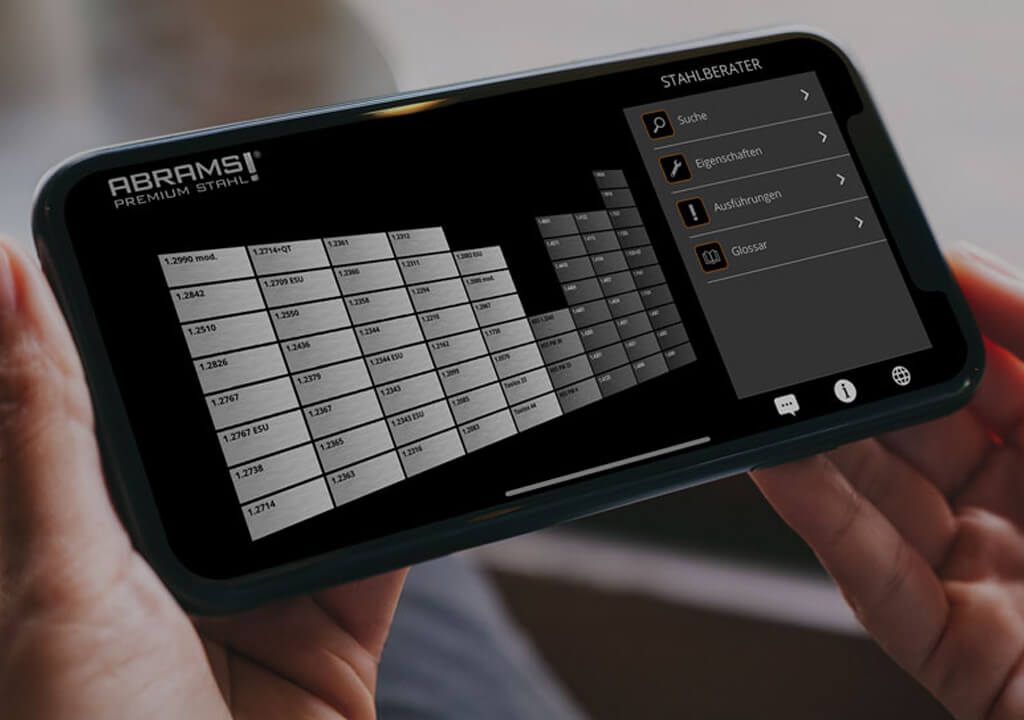

420RM ALTERNATIVES
Are you looking for an alternative steel grade?
WE HAVE THE SOLUTION!
With the ABRAMS STEEL GUIDE, you can obtain an alternative or equivalent steel grade with just a few clicks.

420RM DATASHEET
Download the technical data sheet in PDF format here.
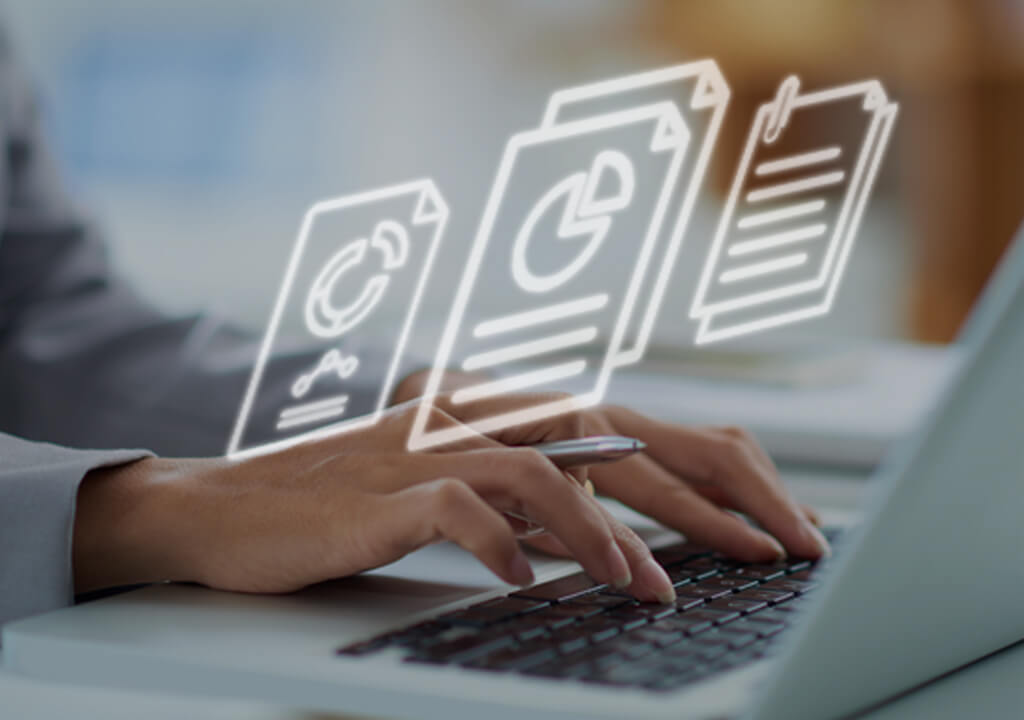
The data shown here has been compiled with the greatest diligence and is regularly updated with regard to the correctness and completeness of its content. The content is indicative only and should not be taken as a warranty of specific properties of the product described or a warranty of suitability for a particular purpose. All information presented is given in good faith and no liability will be accepted for actions taken by third parties in reliance on this information. ABRAMS Industries reserves the right to change or amend the information given here in full or parts without prior notice.