1018 / A36 Tool Steel - 1.9413 / ~1.0044 - SAE 1018 / ~1020
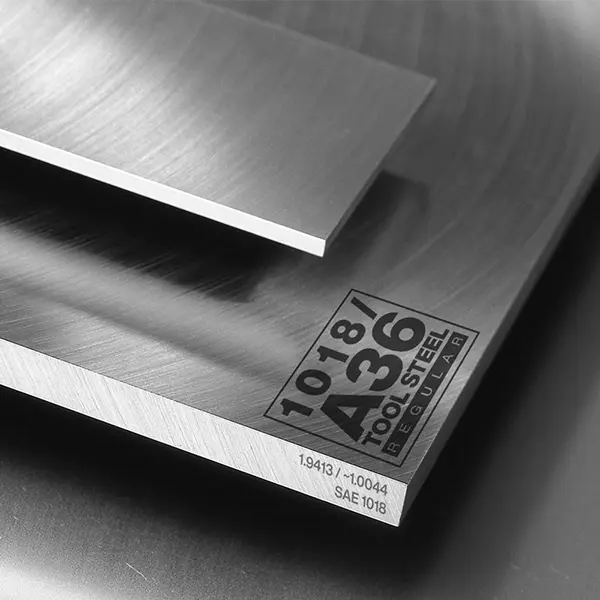
1018 / A36 Tool Steel - 1.9413 / ~1.0044 - SAE 1018 / ~1020
Back to Steel OverviewGround Flat Stock and $mart Flat Stock comes always in a machined condition, that means:
NO decarburization on the surfaces (decarburization leads to unreliable components and tools)
Less dirt on your machines during further processing – nothing but clean chips
Stress-relieved flat steel avoids warping of components during further machining
Get the close-to-finish-size thickness and width you need for the components you plan
Ground Flat Stock and $mart Flat Stock comes always in a machined condition, that means:
NO decaburization on the surfaces (decarburization leads to unreliable components and tools)
Less dirt on your machines during further processing – nothing but clean chips
Stress-relieved flat steel avoids warping of components during further machining
Get the close-to-finish-size thickness and width you need for the components you plan
Ground Flat Stock and $mart Flat Stock comes always in a machined condition, that means:
NO decaburization on the surfaces (decarburization leads to unreliable components and tools)
Less dirt on your machines during further processing – nothing but clean chips
Stress-relieved flat steel avoids warping of components during further machining
Get the close-to-finish-size thickness and width you need for the components you plan
1018 / A36 STEEL PRICE CHART

1018 / A36 STANDARD VALUES
C
Si
Mn
P
S
SAE 1018
50 HRC - 60 HRC
max. 162HB
SAE 1018
50 HRC - 60 HRC
max. 162HB
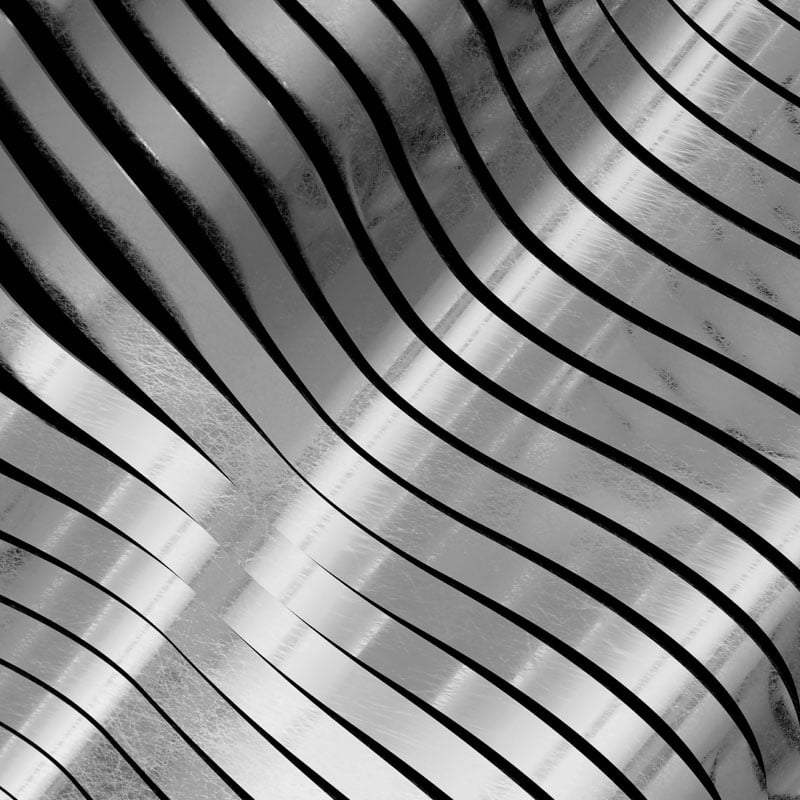

1018 / A36 PHYSICAL PROPERTIES
1018 / A36 belong to the family of low carbon steel (also called mild steel), the most commonly available grades in the world. This steel family has good strength, weldability, ductility, surface hardening quality, good mechanical properties, and a very good machinability.
1018 and A36 are usually both used for high performance applications and therefore can be combined or substituted easily. The raw material for 1018 Steel is often cold-rolled, while A36 Steel is often produced hot-rolled.
Cold drawing increases tensile- and yield strength, torsional strength, surface hardness and wear resistance as well as better tolerances and improved smoothness compared to hot-finished steel.
Hot rolled it has good toughness, strength, ductility, formability, weldability, and workability.
In its annealed condition 1018 / A36 Tool steel can be easily formed.
Though both are mild low carbon steels there are a few differences between 1018 and A36. Most often as mentioned above, 1018 ist cold rolled steel whereas A36 is hot rolled. 1018 has a carbon content of 0.15 - 0.20%, whereas A36 has a content of 0.25 - 0.29%.
Both can easily be welded, though A36 can have more impurities as it is hot rolled. Hot rolled A36 will also have a rougher surface compared to the cold drawn 1018. A36 has a higher strength, where 1018 is more ductile which means it can be bent easier.
A36 can be flame hardened but has not got a high enough carbon content for the usual quenching and tempering. 1018 but also A36 can be carburized, which gives either steel grade a harder surface.
In the classic sense of a stainless steel 1018 / A36 is not a stainless steel.
1018 / A36 has a moderate corrosion resistance as it does not contain enough of the alloying elements to promote full corrosion resistance.
1018 / A36 is susceptible to pitting and crevice corrosion in acids and chloride rich environments as well as intergranular corrosion when exposed to high temperature over a longer time.
Apply a protective coating to 1018 / A36 like oil or black oxide to protect this material from corrosion.
A36 is a structural steel and has good hot forming characteristics and can be hot worked.
In the annealed condition, the microstructure of the 1018 consists of ferrite and small amounts of pearlite, its strength and hardness are low, its plasticity and toughness are better. As a result, the cold formability is good and it can be cold formed into shape by cold drawing, stamping, bending and crimping for example. To overcome the tendency to work hardening, intermediate annealing is required.

1018 / A36 TECHNICAL PROPERTIES
At room temperature the density for 1018 / A36 is 0.284lb/in3 (7.85g/cm3).
The modulus of rigidity for steel at room temperature is at 79.3GPa (11,501 KSI), where aluminum at the same temperature has for example 25.5 GPa (3698 KSI).
The heat conductivity for 1018 / A36 is at 51.9 W/(m*K) (360 BTU/(h-ft*°F)) at room temperature.
Heat conductivity table | |
Value | By temperature |
51.9 | 68°F |
50.8 | 212°F |
48.9 | 392°F |
Medium thermal expansion coefficient | |
10-6m/(m • K) | At a temperature of |
12.0 | 68 - 212°F |
13.5 | 68 - 752°F |
14.5 | 68 - 1112°F |
The specific heat capacity for 1018 / A36 for temperatures in the range of 122 - 212°F (50 - 100°C) is at 486 J/kg-K (0.116Btu/lbm-°F).
This value shows how much heat is needed to heat 1 lb of material by 1 fahrenheit.
Table of the specific electrical resistivity | |
Value | At a temperature of |
~ 0.159 (Ohm*mm²)/m | ~ 32°F |
~ 0.219 (Ohm*mm²)/m | ~ 212°F |
~ 0.293 (Ohm*mm²)/m | ~ 392 °F |
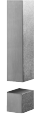
365 DAYS A YEAR – WE ARE HERE FOR YOU – VISIT OUR ONLINE SHOP
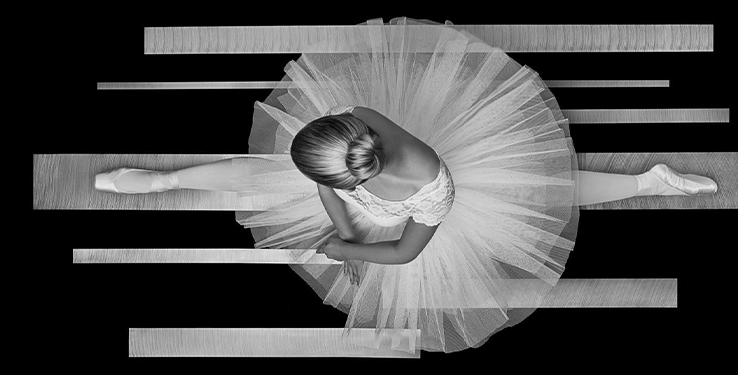
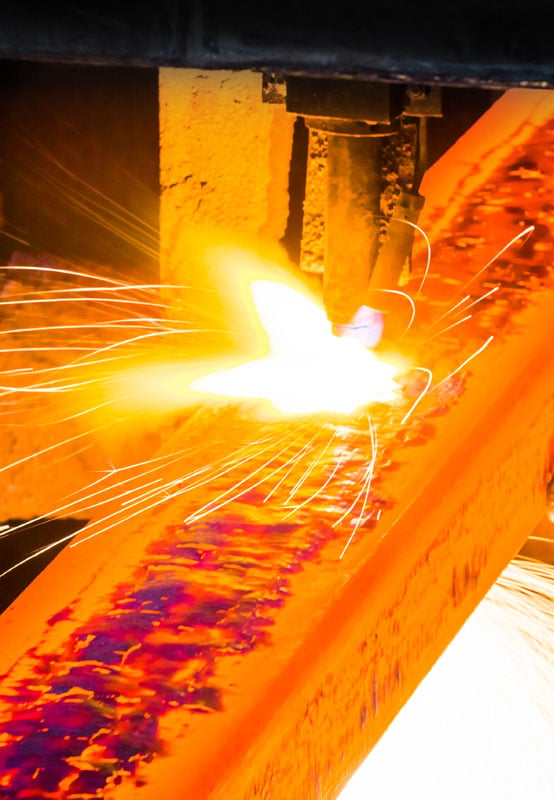

1018 / A36 PROCEDURE
Both steel grades can be surface hardened by flame hardening and carburization as the normal heat treating process, quenching and tempering is not followed.
1018 / A36 is an unalloyed low carbon steel with approx. 0.29% carbon content. It is difficult to quench, and is not usually used directly after quenching.
To reduce grinding cracks or improve case toughness, temper the steel at a range of 302 – 392°F (150 – 200°C), this process has little or no effect on the hardness of the work pieces.
Both grades can be sub-zero treated but as both have a low carbon content they do not build much austenite that needs transforming back into martensite. Sub-zero treating 1018 and A36 can relieve stress and might benefit the dimensional stability.
This process is optional, heat 1018 / A36 to 1436 – 1508°F (780 – 820°C) and moisten in oil or water.
Heat the material at 1616 – 1680°F (880 – 920°C) for about 8 hours, then furnace cool it.
Carburized steel offers a high surface hardness (up to 572 Hardness Brinell (56 Hardness Rockwell)) and a soft core (lower than 277 BHN (30 HRC)) to the work pieces.
It is used to improve drilling, machining, threading, and punching processes and prevents cracking when bending severely.
The continuous time-temperature-transformation-diagram (short TTT) shows how the micro structure changes over time at different temperatures. This information is important during heat treatment and provides information about the optimum conditions for processes such as hardening, annealing and normalizing.
The isothermal time-temperature-transformation-diagram shows how the structure of the steel at micro level changes over time at a constant temperature.
The isothermal TTT-diagram typically shows various phases and conditions as well and show at what temperature and after what time different phases (e.g., perlite, bainite or martensite) start building.

1018 / A36 SURFACE TREATMENT
Apart from not getting the wear resistance other steel grades get by nitriding, this process can cause the material dimensional changes.
1018 / A36 can be carburized and carbonitrided as shown.
Normalizing 1018 / A36 can refine the grain structure and relieve internal stresses. If specific mechanical properties are needed or the material is prepared for further heat treatment, normalizing these material grades can be helpful.

1018 / A36 PROCESSING
1018 / A36 has a machinability score of 6 on a scale where 1 is low and 6 is high.
Machining 1018 / A36 gives this low carbon steel a great finish, continuous and hard chips and it can be machined in all conditions.
1018 / A36 steels can be machined by EDM even if they have been case- or surface hardened. As these are naturally soft steels they can be easily machined in the traditional way.
EDM can be used when more complex parts or a smooth surface finish is needed.
1018 and A36 are soft and ductile steels and may not need the higher end of the range added for machining. If a tight finish is required it should be considered to add a little more.
The same should be considered for a high quality finish. This can ensure that by machining to the required specifications there is enough material for each machining operation.
Dimensional changes, like thermal expansion, thermal contraction, residual stresses, stress relieving, mechanical deformation, machining and finishing can affect 1018 carbon steel. A36 mild steel might warp or distort while welding.
Welding 1018 / A36 can be done by most conventional practices, e.g., resistance, submerge melt, oxyacetylene and gas welding. It is recommended to weld the material after carburizing or carbonitriding.
Post- and pre-heating is not necessary; though pre-heating can be done for sections over 1 31/32 inches (50mm) and post-heating can be stress relieving.

1018 / A36 APPLICATION OPTIONS
The steel grades 1018 CF and A36 HR can be used when a high surface hardness and a ductile core are needed. The steel grades can be cold drawn, swaged, crimped and bend without cracking in the process.
• Mounting plates and separators
• Tool holders
• Spindles
• Sprockets
• Gears
• Jigs
• Fixtures
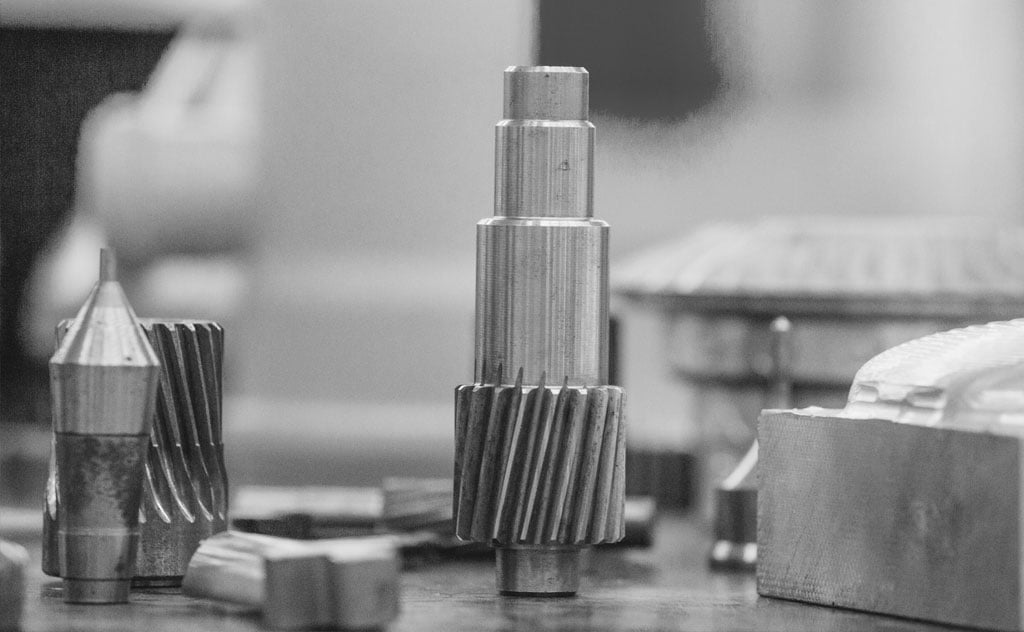

1018 / A36 CONCLUSION
The 1018 has, compared to the A36, a smoother finish as it is cold drawn which makes it ideal for precision parts. The 1018 has excellent machinability, whereas the A36 is harder to machine. 1018 and A36 both have a good weldability. A36 has got a good tensile- and yield strength compared to 1018. A36 can get brittle when cooled too quickly.
When making a choice which material grade to use, it is recommended to have a close look at the needed properties and what applications they will be used for.
To conclude both steel grades have their advantages and disadvantages. It is important to consider what the materials should be able to withstand and to understand the differences before choosing which grade to use.
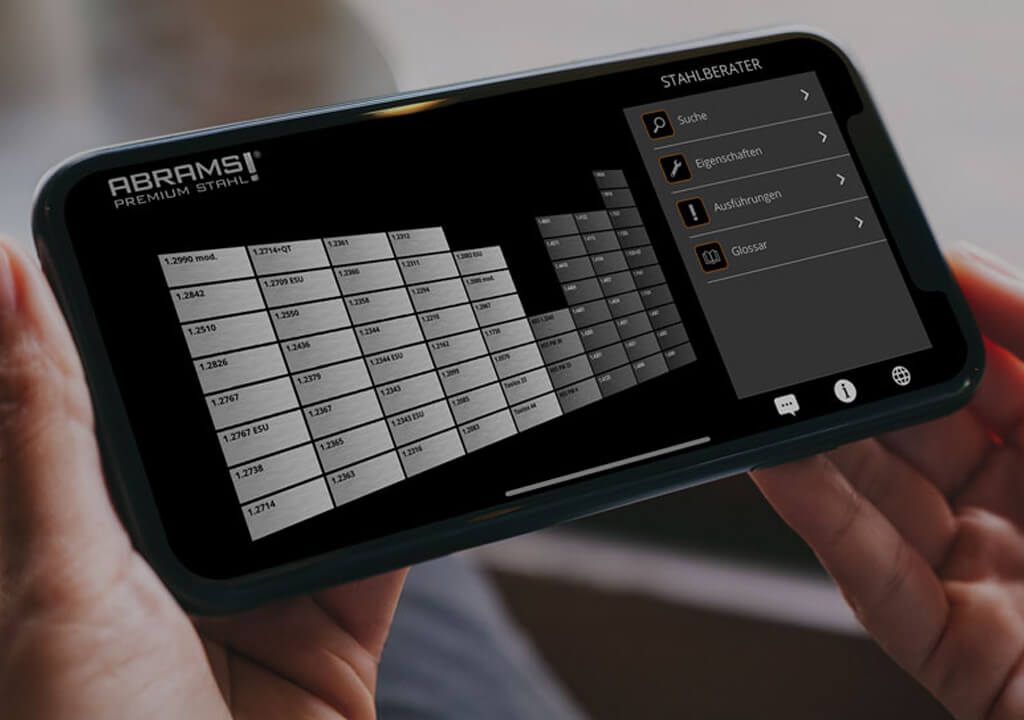

1018 / A36 ALTERNATIVES
Are you looking for an alternative steel grade?
WE HAVE THE SOLUTION!
With the ABRAMS STEEL GUIDE, you can obtain an alternative or equivalent steel grade with just a few clicks.

1018 / A36 DATASHEET
Download the technical data sheet in PDF format here.
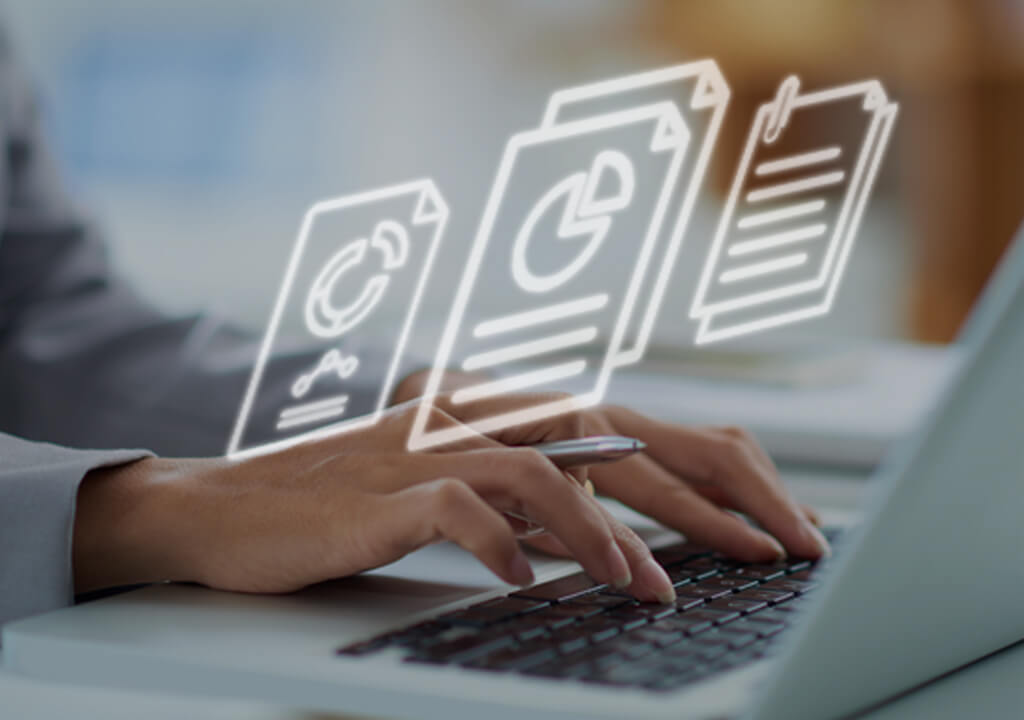
The data shown here has been compiled with the greatest diligence and is regularly updated with regard to the correctness and completeness of its content. The content is indicative only and should not be taken as a warranty of specific properties of the product described or a warranty of suitability for a particular purpose. All information presented is given in good faith and no liability will be accepted for actions taken by third parties in reliance on this information. ABRAMS Industries reserves the right to change or amend the information given here in full or parts without prior notice.