P20 Tool Steel - ~1.2311 - ~40CrMnMo7 - Plastic mold steel
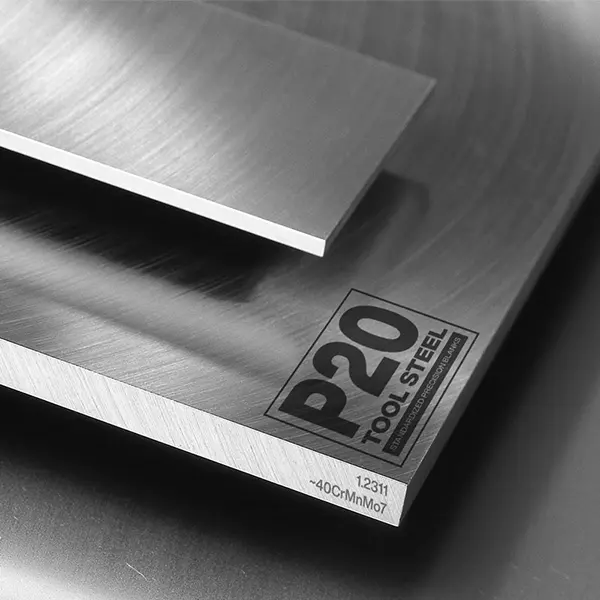
P20 Tool Steel - ~1.2311 - ~40CrMnMo7 - Plastic mold steel
Back to Steel OverviewGround Flat Stock and $mart Flat Stock comes always in a machined condition, that means:
NO decarburization on the surfaces (decarburization leads to unreliable components and tools)
Less dirt on your machines during further processing – nothing but clean chips
Stress-relieved flat steel avoids warping of components during further machining
Get the close-to-finish-size thickness and width you need for the components you plan
Ground Flat Stock and $mart Flat Stock comes always in a machined condition, that means:
NO decaburization on the surfaces (decarburization leads to unreliable components and tools)
Less dirt on your machines during further processing – nothing but clean chips
Stress-relieved flat steel avoids warping of components during further machining
Get the close-to-finish-size thickness and width you need for the components you plan
Ground Flat Stock and $mart Flat Stock comes always in a machined condition, that means:
NO decaburization on the surfaces (decarburization leads to unreliable components and tools)
Less dirt on your machines during further processing – nothing but clean chips
Stress-relieved flat steel avoids warping of components during further machining
Get the close-to-finish-size thickness and width you need for the components you plan
P20 STEEL PRICE CHART

P20 STANDARD VALUES
C
Si
Mn
P
S
Cr
Mo
~40CrMnMo7
32 HRC - 50 HRC
max. 225 HB
~40CrMnMo7
32 HRC - 50 HRC
max. 225 HB
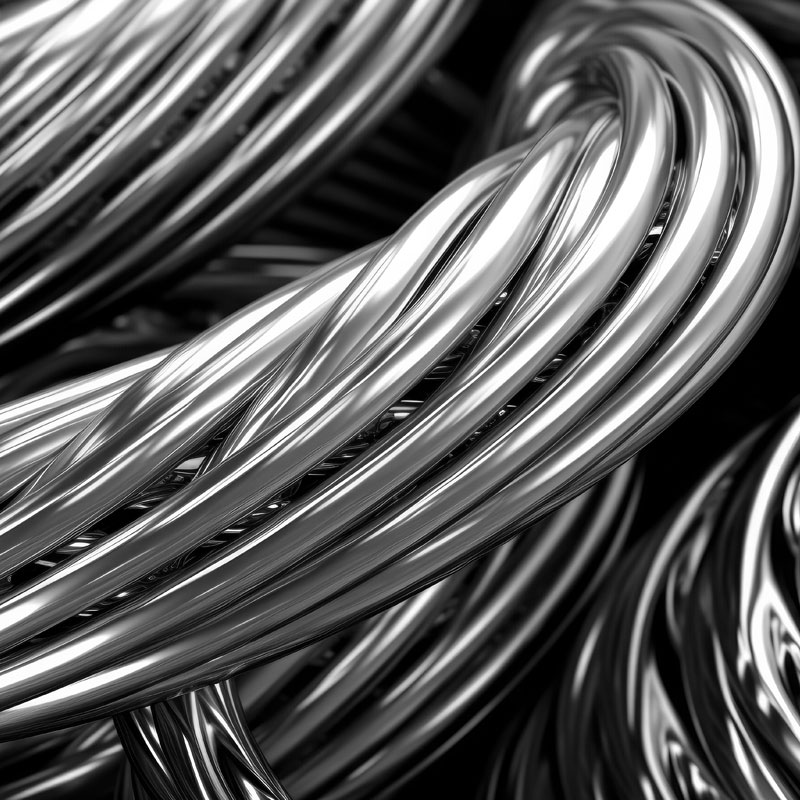

P20 PHYSICAL PROPERTIES
Delivered in its annealed condition, the P20 tool steel can be hardened as explained below as well as used in its delivered condition. In general, P20 is mainly used for plastic molds, die casts and tools but is also suitable for applications such as rails and shafts. The steel grade has good weldability and can be polished to an excellent finish, for applications which require a high surface hardness the P20 tool steel can be case hardened or nitrated.
Annealed material is easier to machine, it reduces wear on tools and is more malleable. When using annealed material it is important to make sure it is suitable for the application as it might not perform as well in high wear or high load applications as a hardened steel would.
The P20 is not a stainless steel in the classic sense. Stainless steel has a chromium content of a minimum of 10.5% which makes it corrosion resistant.
P20 has a chromium content of 1.8 - 2.1% and is therefore not a corrosion resistant steel in the classic sense like stainless steel. Additional surface treatment and maintenance as well as keeping parts in a dry environment may prolong the resistance to corrosion but can not hold it back completely.
The iron in the P20 makes it ferromagnetic and therefore the P20 is magnetizable.
On a scale where 1 is low and 6 is high, the P20 scores a 3.
P20 can be readily cold worked using regular tooling methods.

P20 TECHNICAL PROPERTIES
P20 tool steel is not commonly used for knife making. While it has some of the attributes like edge retention, toughness, corrosion resistance or hardness, it does not have enough.
The working hardness for the P20 is in the range of 300 - 469 BHN (32 - 50 HRC).
Typically the density of P20 tool steel is 0.284 lb/in3 (7.85g/cm3) at room temperature.
The P20 has a tensile strength of approx. 108.8 KSI on delivery (0.145 KSI = 1MPa). In order to reach this value, a tensile test is performed to show how much force is needed to stretch or elongate a sample before it breaks
The yield strength shows how much stress has to be applied to plastically deform and when the point is reached for the material not to return to its original state after stresses have been removed. It then either stays in the mischaped form or breaks.
The P20 range for this tool steel is between 120 - 125 KSI (827 - 862 MPa).
The heat conductivity for the P20 tool steel is at 34.5 W/(m*K) (239 BTU/(h-ft*°F)) at room temperature.
Heat conductivity table | ||
Value W/(m*K) | Value BTU/(h-ft*°F) | By temperature |
34.5 | 19.95 | 68°F |
33.5 | 19.37 | 662°F |
32.0 | 18.50 | 1292°F |
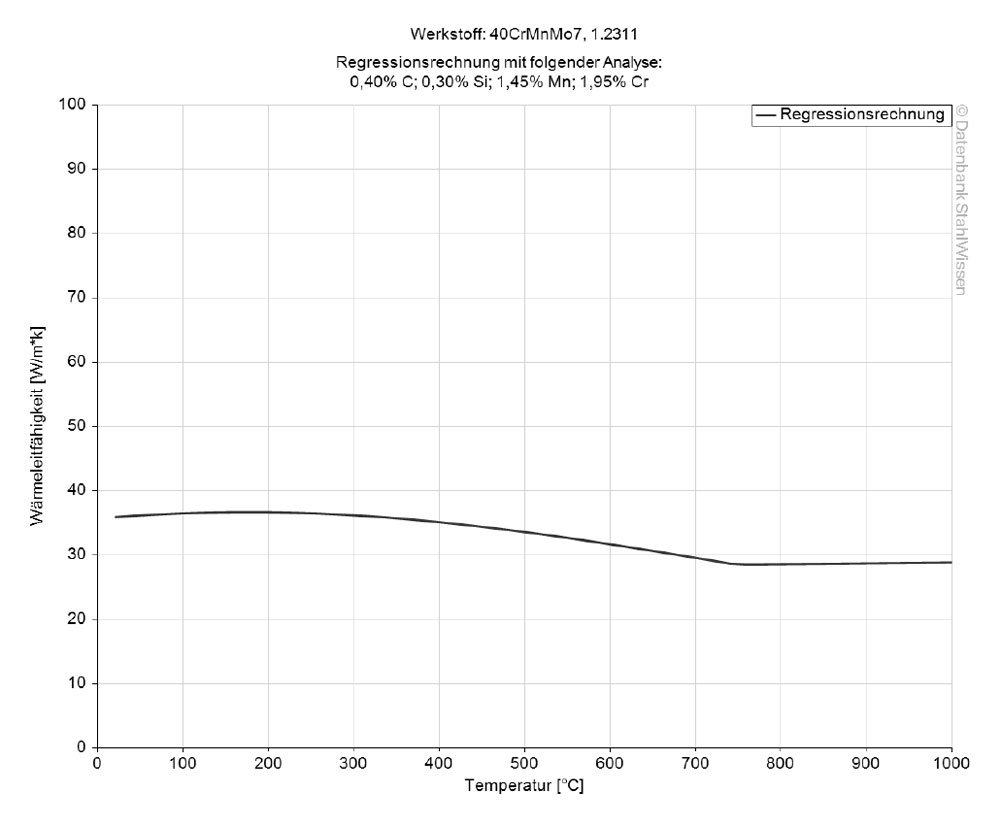
The following table shows expansion or contraction at various temperatures, which may be very important for high temperature works or when working with high temperature changes.
Medium thermal expansion coefficient | |
10-6m/(m • K) | At a temperature of |
11.1 | 68 - 212°F |
12.9 | 68 - 392°F |
13.4 | 68 - 572°F |
13.8 | 68 - 752°F |
14.6 | 68 - 932°F |
14.9 | 68 - 1292°F |
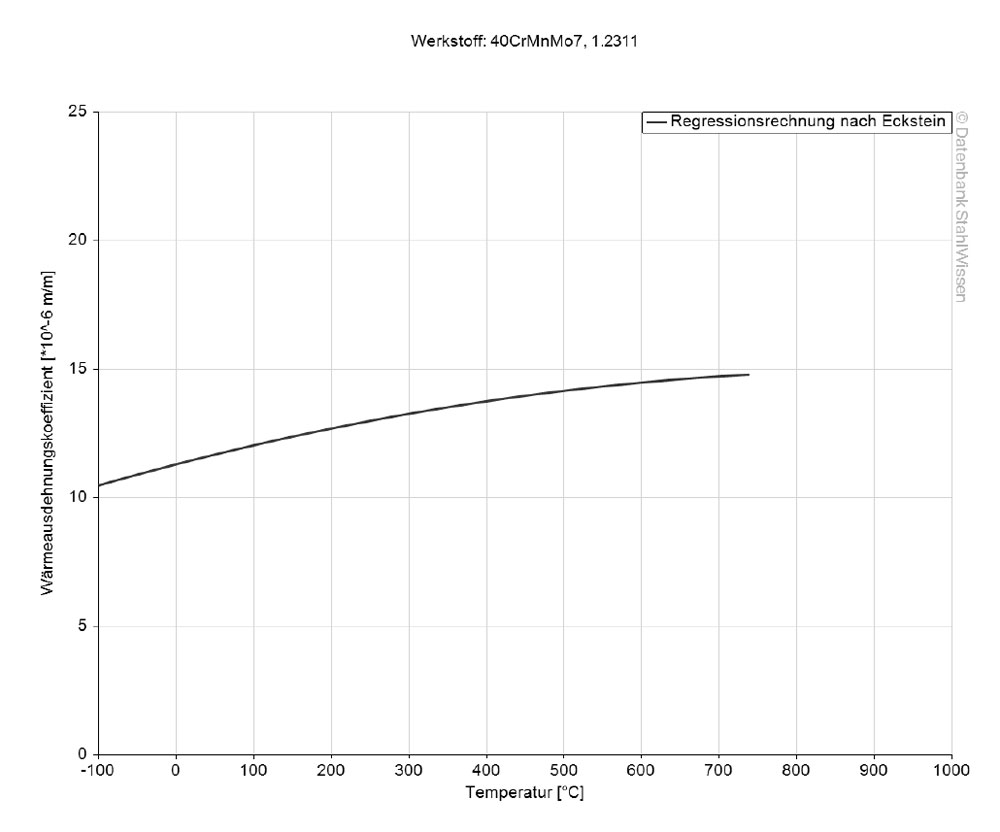
The specific heat capacity of the P20 at room temperature is 0.43 J/g-°C (0.103 BTU/lb-°F). This value shows how much heat is needed to heat 1lb of material by 1 Fahrenheit.
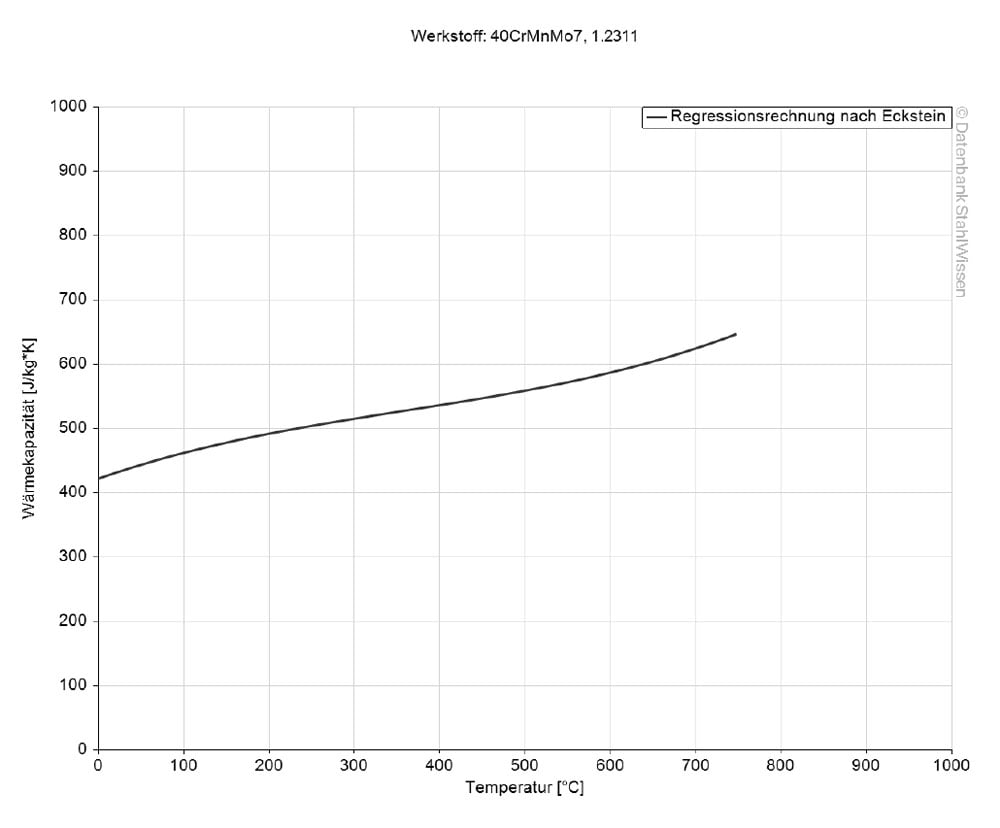
The following table shows the electrical resistivity of the P20 tool steel.
Table of the specific electrical resistivity | |
Value | At a temperature of |
0.47 (Ohm*mm²)/m | 68°F |
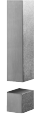
P20 AS $mart Flat Stock
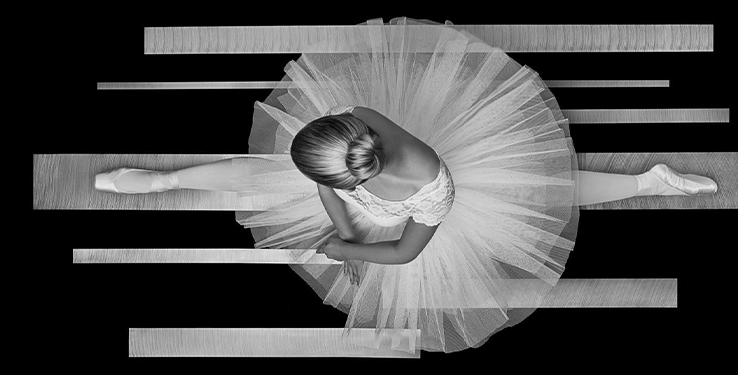
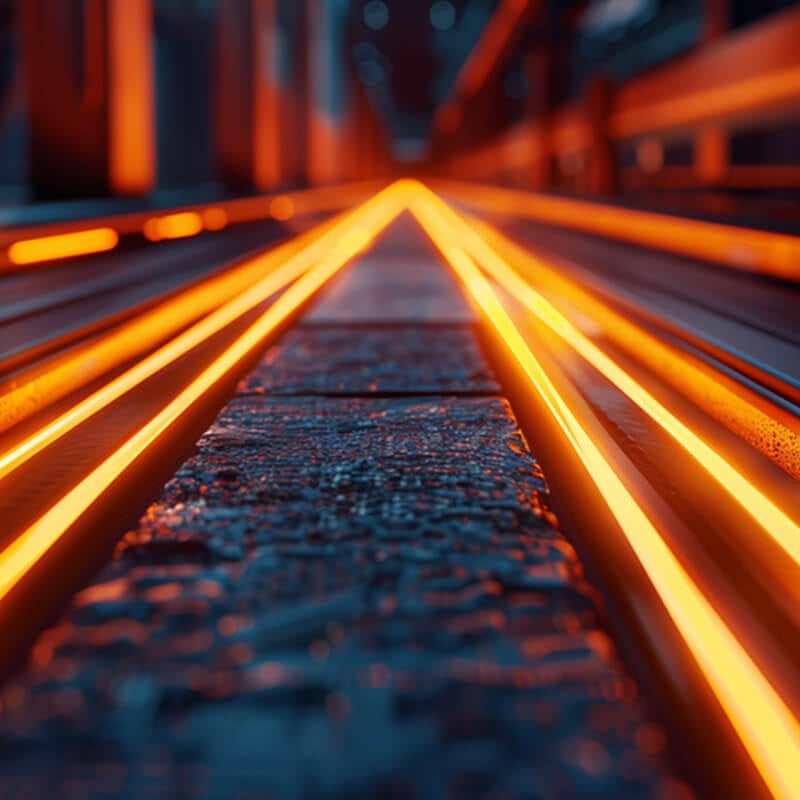

P20 PROCEDURE
Heat the material uniformly to a temperature of 1310 - 1364°F (710 - 740°C), then cool it in the furnace.
In general when stress relieving P20 parts, after machining, they are soaked for 1 hour per 1 inch (25.4 mm) of thickness at a temperature of 1022 - 1112°F (550 - 600°C) and then cooled down in still air. Cooling in still air is a controlled way to ensure that no stresses are reintroduced.
Reducing stresses prevents the P20 from distorting or cracking, improves the mechanical properties of the material and it enhances the dimensional stability which is important for molds.
To harden the P20 , heat the parts uniformly to a temperature of 1544 - 1598°F (840 - 870°C), soak them for 30 minutes for the first inch (25.4 mm) and any additional inch of thickness for 15 minutes.
The parts should be quenched in the following media with a temperature of 356 - 392°F (180 - 200°C):
• Oil
• Saltbath
Immediately after quenching the workpieces should be tempered. The tempering temperature should be held for a minimum of 2 hours or 1 hour per inch (25.4 mm) of thickness and then the workpieces should be cooled in air to room temperature.
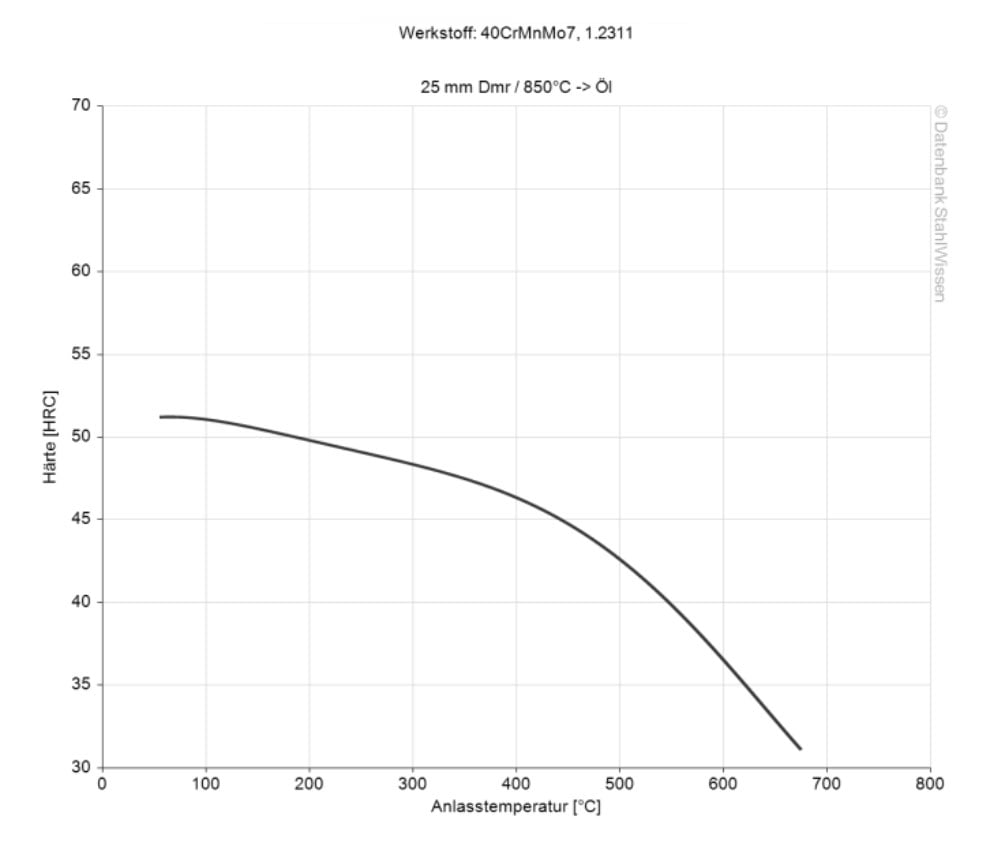
Normalizing will refine the grain structure and give the steel a uniform microstructure. It can help to improve machinability and can relieve internal stresses which may have been introduced during former heat treatment, forging or casting for example.
Heat the material uniformly above its critical temperature and soak for approx. 1 hour per 1 inch (25.4 mm) of thickness. Then remove the parts from the furnace and cool them in still air.
Finish the process with a thorough inspection that the parts have the desired microstructure and properties.
Immediately after quenching the workpieces should be tempered. The tempering temperature should be held for a minimum of 2 hours or 1 hour per inch (25.4 mm) of thickness and then the workpieces should be cooled in air to room temperature.
This diagram shows micro changes over time at different temperatures. Those are important during heat treatment as they show information about the optimum conditions for processes such as hardening, annealing and normalizing.
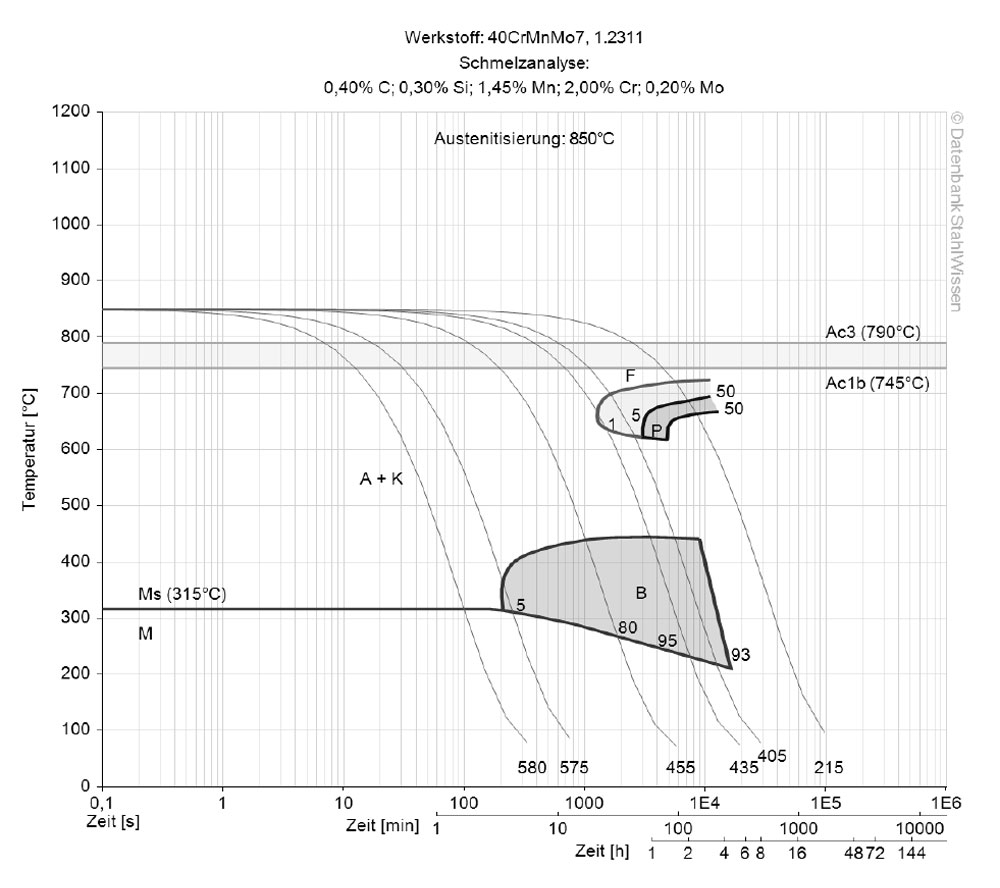
This diagram shows the structural changes at micro level over time at a constant temperature. It shows at what temperature and after what time different phases, e.g., perlite, martensite or bainite start to build.
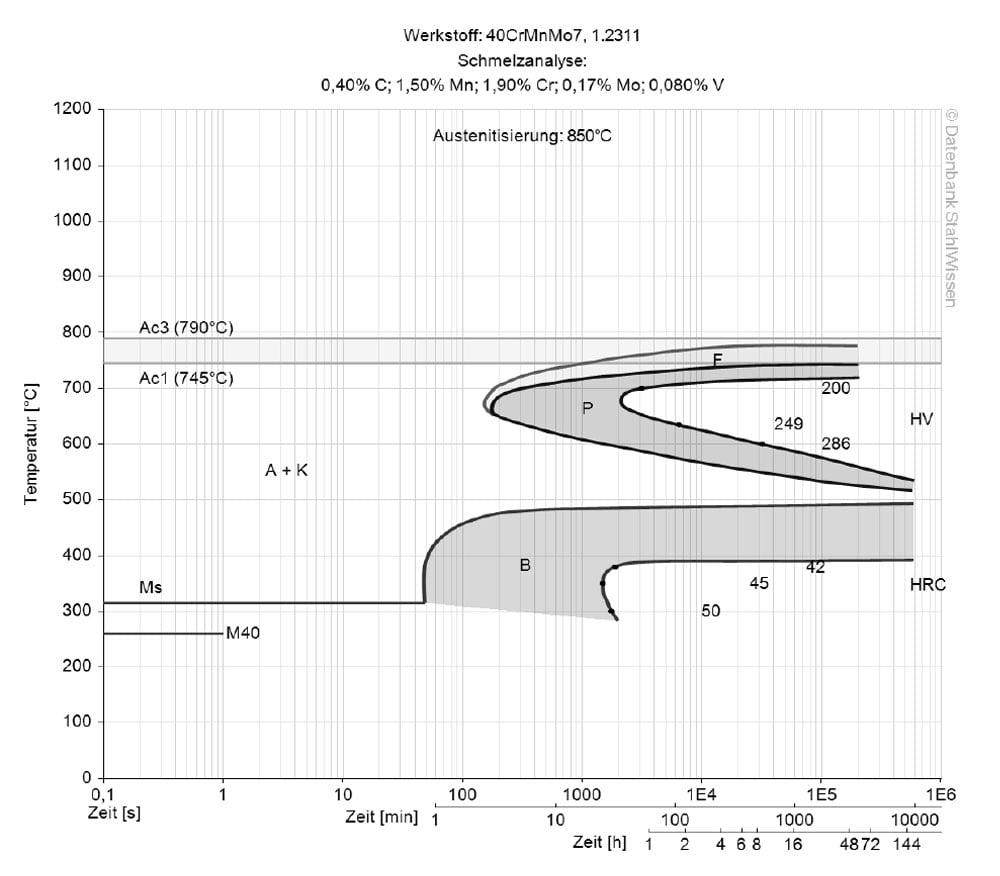

P20 SURFACE TREATMENT
P20 can be nitrated, this treatment introduces nitrogen into the surface, to add a hard and abrasion resistant surface to the depth of 1/16 inch (0.40 mm).
Physical Vapor Deposition (PVD) deposits a thin film on the surface of the material, this treatment enhances wear resistance and can reduce friction.
This process deposits a nickel alloy coating, without the electrical current, by chemical reduction onto the surface of the material.
Black oxide coating can enhance the corrosion resistance of the parts but is mostly done for esthetic purposes. It will give parts a blue-black coloring that will reduce light reflecting off the surface.
Laser surface hardening can localize surface hardening without affecting the properties of the steel and provides better wear resistance in those areas. This is done by using a high powered laser that heats certain surface areas and rapidly cooling those areas again.
Surface treating the P20 tool steel has benefits like extended service life, improved performance, corrosion resistance or to enhance the visual appeal of parts made from this steel grade.

P20 PROCESSING
The P20 tool steel has a good balance of machinability and toughness.
When this steel grade is quenched in oil from a hardening temperature of 1550°F (843°C) this material normally expands by 0.003inch/inch (0.0762mm/mm). However dimensional changes during heat treatment are largely impacted by size and shape of the parts. To minimize dimensional changes, it is important to adhere to good heat treatment practices.
P20 can be forged within a temperature range of 1650 - 2000°F (899 - 1093°C). Do not let the forging temperature drop below 1600°F (871°C).
P20 can be welded using all conventional methods. Preheat the material to a temperature of 600 - 700°F (316 - 371°C). Do not drop the welding temperature below 600°F (316°C). Fillers should be matched to the hardness of the base metal. Cool slowly to 100 - 150°F, then post heat to a temperature of 1000°F (538°C) for one hour per inch (25.4 mm) of weld depth and do not exceed 1050°F (566°C) as this will result in losing hardness. Double temper if possible.

P20 APPLICATION OPTIONS
P20 tool steel, in its annealed condition, is easier and faster to machine to develop for example prototypes or for tools with low wear and stresses, it can be cold formed and engraved.
• Mechanical engineering
• Jigs
• Base plates
• Assembling parts
• Molding frames
• Plastic molds
• Plastic processing
• Injection molds
• Die casting molds
• Hydroforming tools
• Recipient sleeves,
• Intermediate sleeves
• Folding bars
• Tool holders
• Extrusion presses
• Tube presses
• Die holders
• Die insert
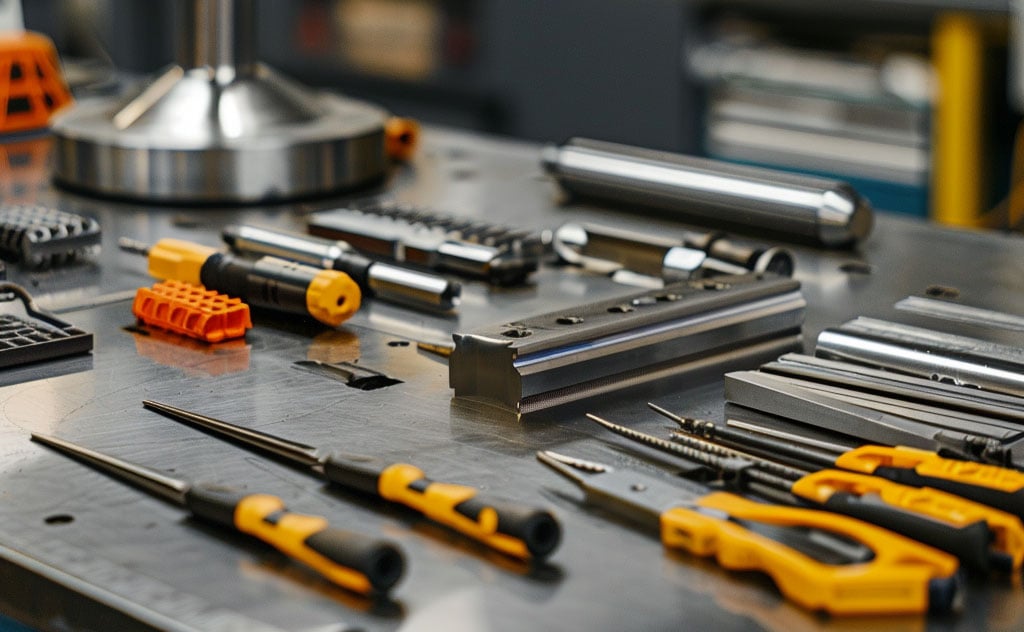

P20 CONCLUSION
As a tool steel, P20 is a reliable and proven choice when it comes to molds, dies and tools. It has a good balance between machinability and toughness and is easy to polish, which has a positive effect on the surface of molded parts.
- Quenched and tempered cold work steel
- Plastic mold steel
- Polishable
- Etchable
- High through-hardening
- Uniform component strength
- Nitridable
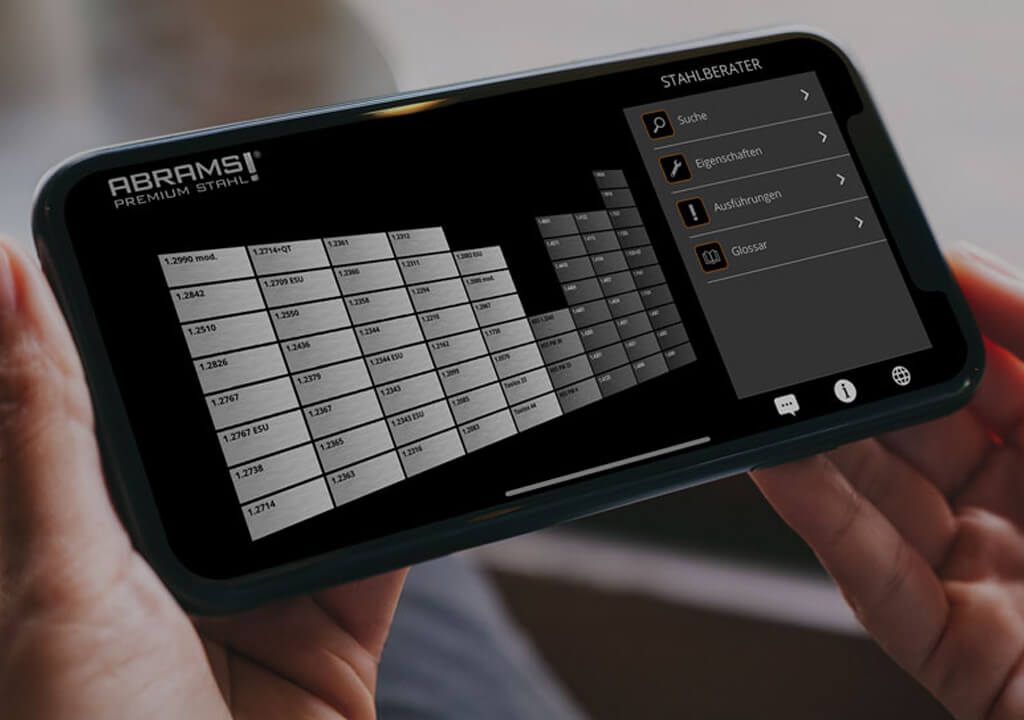

P20 ALTERNATIVES
Are you looking for an alternative steel grade?
WE HAVE THE SOLUTION!
With the ABRAMS STEEL GUIDE, you can obtain an alternative or equivalent steel grade with just a few clicks.

P20 DATASHEET
Download the technical data sheet in PDF format here.
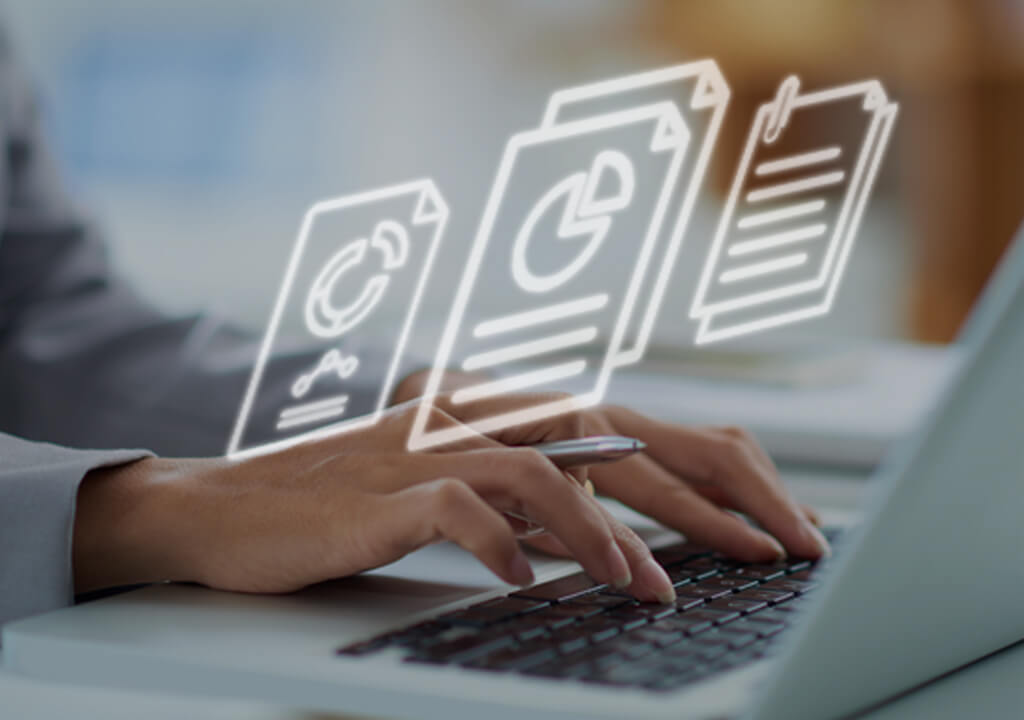
The data shown here has been compiled with the greatest diligence and is regularly updated with regard to the correctness and completeness of its content. The content is indicative only and should not be taken as a warranty of specific properties of the product described or a warranty of suitability for a particular purpose. All information presented is given in good faith and no liability will be accepted for actions taken by third parties in reliance on this information. ABRAMS Industries reserves the right to change or amend the information given here in full or parts without prior notice.