1045 Carbon Tool Steel - DIN 1.1730 - C45U - SAE 1045
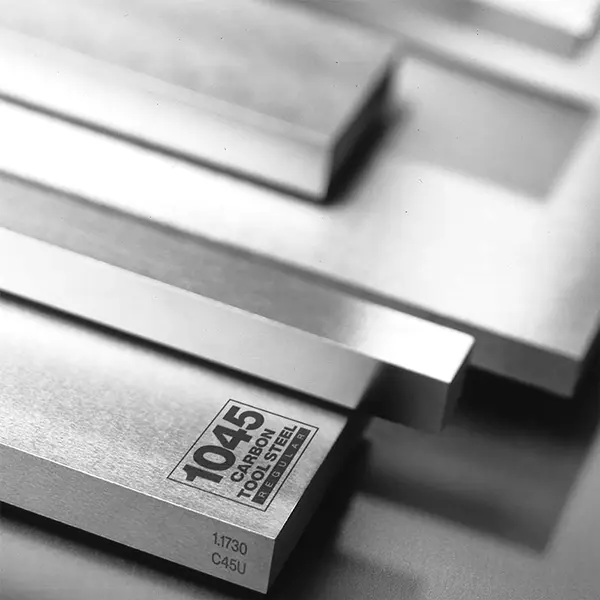
1045 Carbon Tool Steel - DIN 1.1730 - C45U - SAE 1045
Back to Steel OverviewGround Flat Stock and $mart Flat Stock comes always in a machined condition, that means:
NO decarburization on the surfaces (decarburization leads to unreliable components and tools)
Less dirt on your machines during further processing – nothing but clean chips
Stress-relieved flat steel avoids warping of components during further machining
Get the close-to-finish-size thickness and width you need for the components you plan
Ground Flat Stock and $mart Flat Stock comes always in a machined condition, that means:
NO decaburization on the surfaces (decarburization leads to unreliable components and tools)
Less dirt on your machines during further processing – nothing but clean chips
Stress-relieved flat steel avoids warping of components during further machining
Get the close-to-finish-size thickness and width you need for the components you plan
Ground Flat Stock and $mart Flat Stock comes always in a machined condition, that means:
NO decaburization on the surfaces (decarburization leads to unreliable components and tools)
Less dirt on your machines during further processing – nothing but clean chips
Stress-relieved flat steel avoids warping of components during further machining
Get the close-to-finish-size thickness and width you need for the components you plan
1045 STEEL PRICE CHART

1045 STANDARD VALUES
C
Si
Mn
P
S
C45U
approx. 190 HB (annealed) - 54 HRC (surface hardness)
max. 190HB
C45U
approx. 190 HB (annealed) - 54 HRC (surface hardness)
max. 190 HB
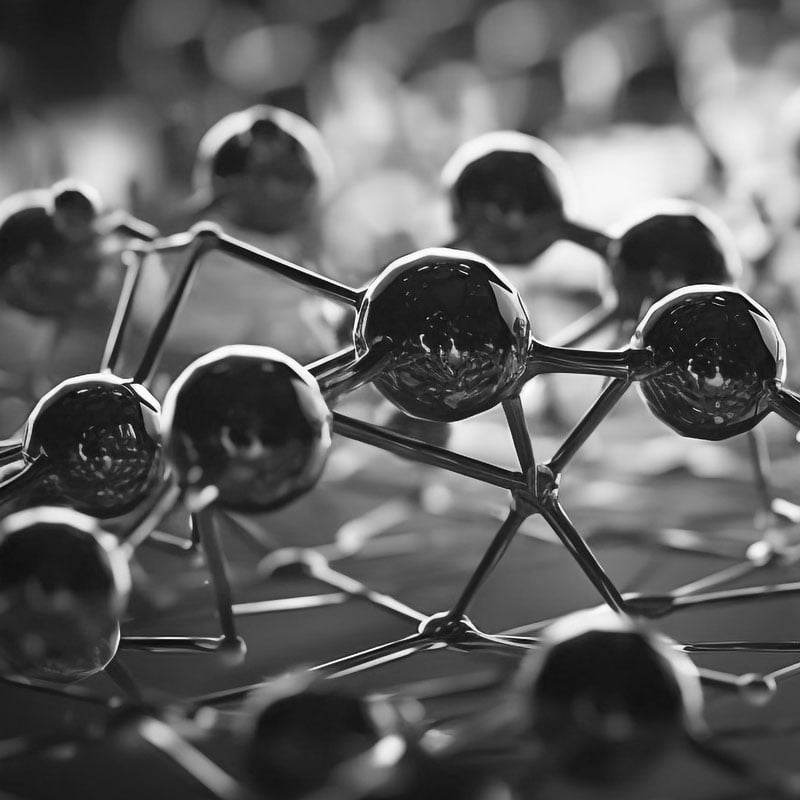

1045 PHYSICAL PROPERTIES
1045 is an unalloyed tool steel with a medium carbon content (0.45%) that can be hardened, but only has a low depth of hardening. The designation 1045 explains what kind of steel 1045 is and what its main alloy is, the first two numbers, 10 shows a user that this is a plain/ unalloyed steel whereas the 45 shows the mass fraction of the carbon content of 0.45%.
As a versatile, carbon-based cold work steel, 1045 has good strength and impact properties, as well as good machinability and reasonable weldability. It is a case-hardening steel with a shallow depth of hardening. With a hard surface and a tough core it is used by many industry sectors for its good mechanical strength and good machinability and mainly used in its as-delivered condition. It can be hardened by quenching and tempering to receive parts with a good combination of strength and wear resistance.
1045 medium carbon steel does not contain chrome or nickel which makes this steel susceptible to rust and corrosion. So 1045 is not a stainless steel in the classic sense of stainless steel.
On a scale where 1 is low and 6 is high, 1045 reaches a 2. Though it has some corrosion resistance and is more durable than stainless steel this medium carbon steel can rust when exposed to moisture.
Yes, 1045 is magnetizable but processes like the heat treatment can influence these abilities.
The max. operating temperature for this medium carbon steel is at 392°F which makes 1045 a cold work steel.

1045 TECHNICAL PROPERTIES
With an approx. amount of 0.45% of carbon 1045 holds has a good edge retention and can easily be sharpened. Therefore it is a popular choice as a knife steel.
1045 has a working hardness of 469 - 627 BHN (hardness Brinell) (50 - 60 HRC(hardness Rockwell)).
With a tensile test this material is tested how much it will stretch or elongate before it breaks. 1045 has a tensile strength of approx. 72.5 KSI on delivery (0.145KSI = 1MPa).
At room temperature the density for 1045 is 0.284lb/in3 (7.85g/cm3).
The yield strength shows the plastic deformation point of the material under stress, for 1045 this is at approx. 45 - 55 KSI (approx. 310 - 379MPa).
The heat conductivity of 1045 is 44.9W/m*K (346 BTU/(h-ft*°F)) at room temperature.
Heat conductivity table | |
Value | By temperature |
44.9 | 68°F |
41.6 | 662°F |
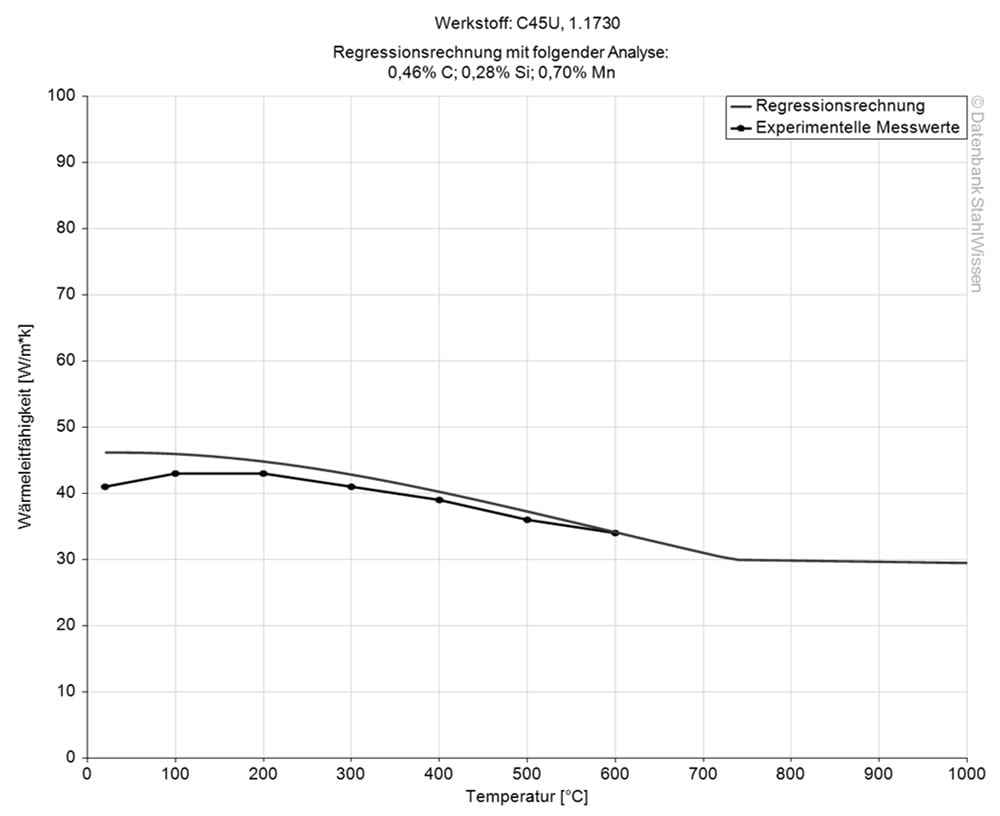
This diagram shows how much the 1045 might expand or contract when the temperatures change which can be very important when working with high temperatures or strong temperature changes.
Medium thermal expansion coefficient | |
10-6m/(m • K) | At a temperature of |
12.5 | 68 - 212°F |
13.0 | 68 - 392°F |
13.6 | 68 - 572°F |
14.1 | 68 - 752°F |
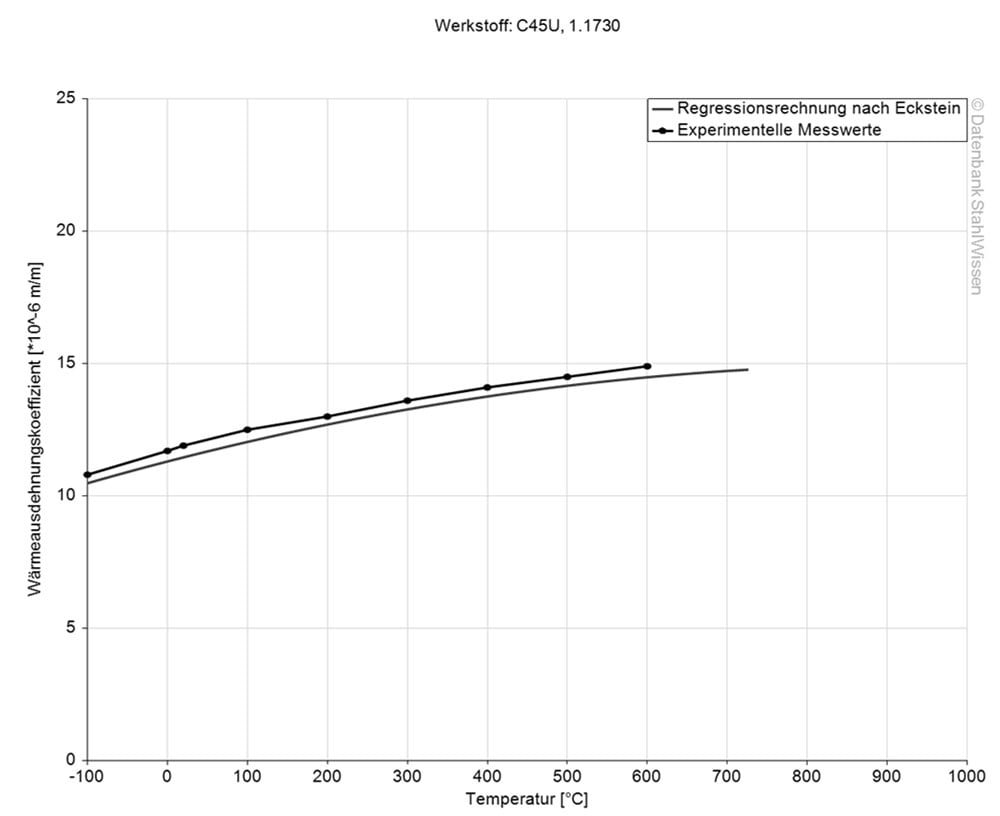
The specific thermal capacity for 1045 at 212°F (100°C) is at 0.486 J/g-°C (0.116 BTU/lb-°F). This value shows how much heat is needed to heat 1 lb of material by 1°F.
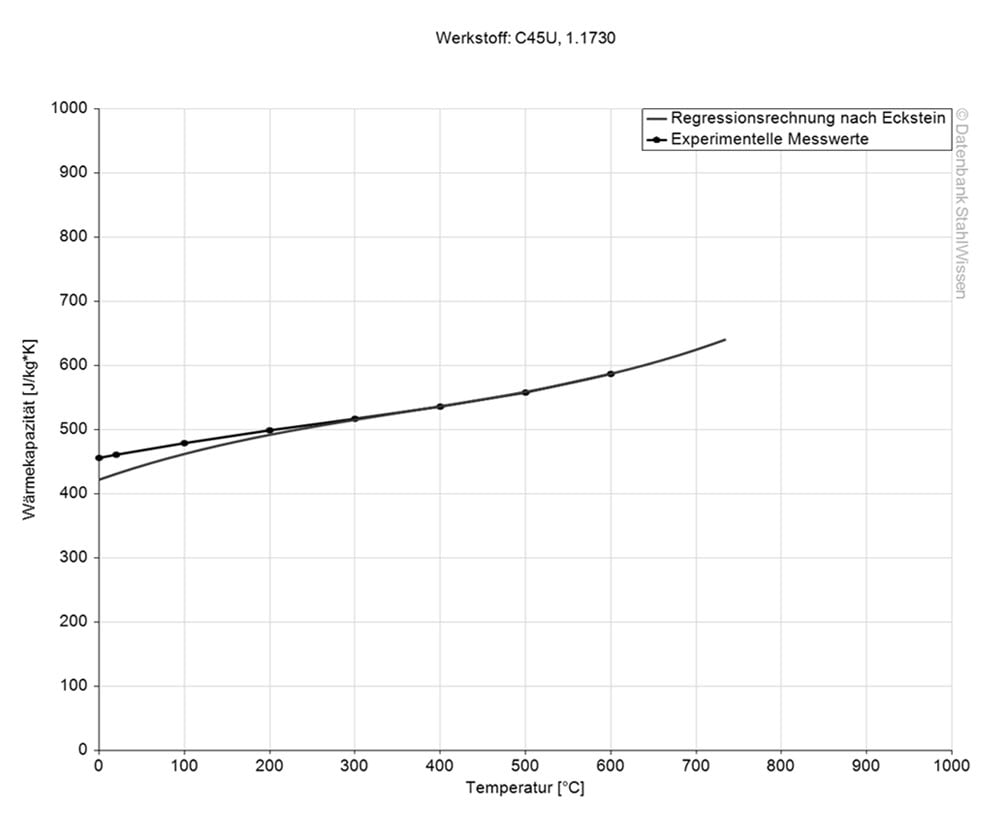
You can find the temperature dependent material constant (Resistivity) in the following table. The electrical conductivity is the reciprocal value of the specific resistance.
Table of the specific electrical resistivity | |
Value | At a temperature of |
0.162 (Ohm*mm²)/m | 32°F |
0.223 (Ohm*mm²)/m | 212°F |
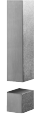
70 STEEL GRADES IN THOUSANDS STANDARD DIMENSIONS AVAILABLE FROM STOCK!
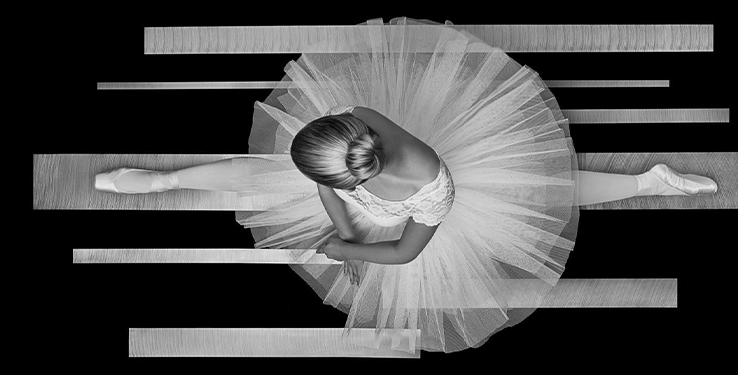
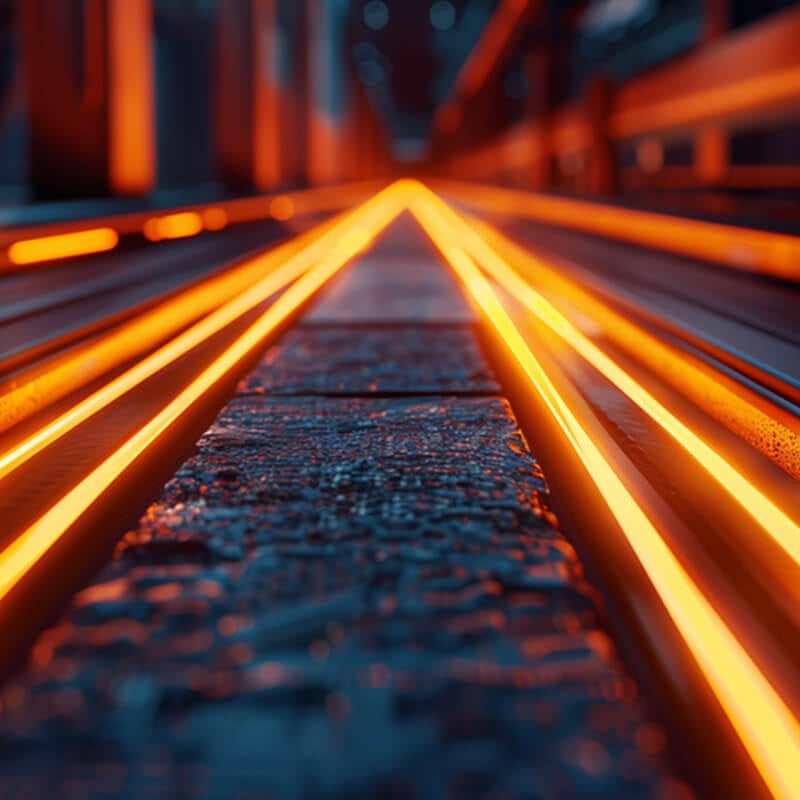

1045 PROCEDURE
Protect the steel and heat the work piece uniformly to 1290°F (700°C). Following this, cool the parts down to 1110°F (600°C) in the furnace at a rate of 78°F (25°C) per hour, then continue to cool further in air.
Heat the material to 1545-1066°F (840-870°C) until it is heated through evenly. Then allow parts to cool in air.
Heat the work pieces to a temperature of 1200°F (650°C), hold for 2 hours that the entire piece is heated through to temperature. Then bring the temperature of the work pieces down to 930°F (500°C) in the furnace and continue to cool them further in air.
Preheat the work pieces to 1200°F (650°C).
Austenitizing temperature: 1510-1600°F (820-870°C), soak parts for a minimum of 1 hour or for 10-15 minutes per inch (25.4 mm) of thickness and protect them against decarburization. Quench in water or brine.
Flame and induction hardening can be accomplished by rapidly heating the material to the desired case depth followed by quenching in oil or water. This is followed up with a temper at 300-400°F (150-200°C) to reduce stresses, but without affecting the hardness.
The most used quenching medias for this cold work steel are:
• Water
• Oil
• Brine
To temper 1045 after hardening or oil and water quenching, heat the material to a temperature range of 750 - 1260°F (400 - 680°C) for 1 hour per inch (25.4 mm), then cool in still air.
1045 will be tempered at a temperature range of 750 - 1260°F (400 - 680°C) depending on the desired application the material is used for.
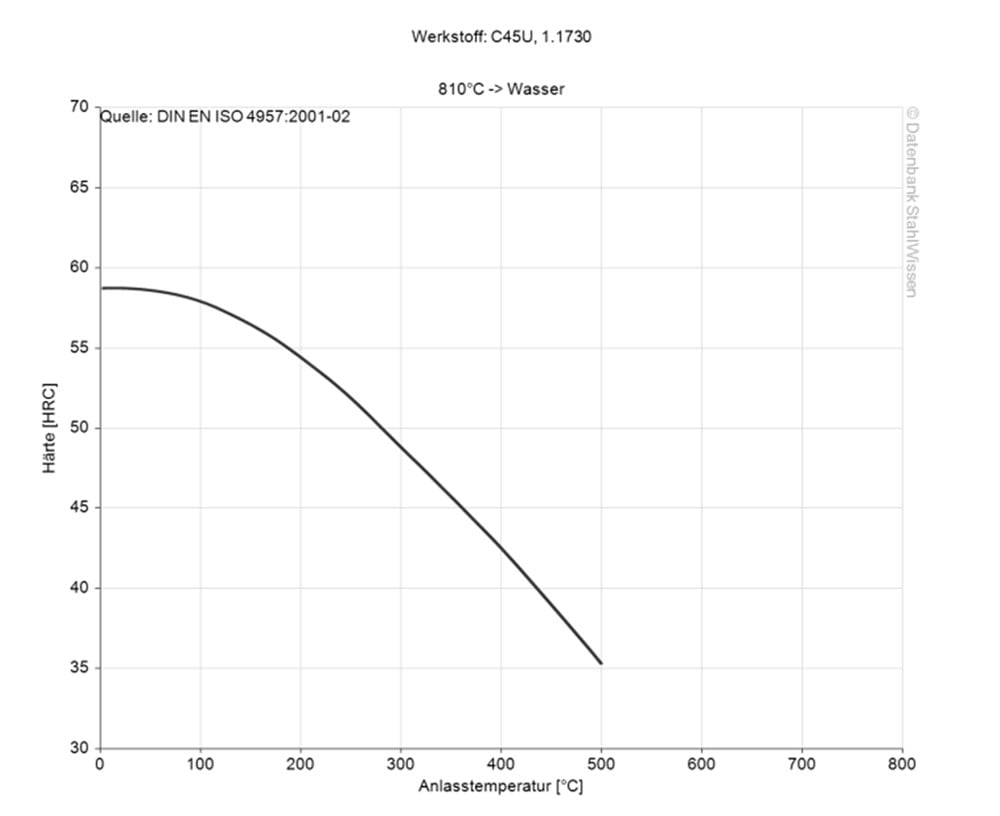
Though the benefits for sub-zero treatment are better in high alloyed steels, 1045 can benefit by enhancing its mechanical and physical properties.
After the initial heat treatment the material is cooled down to room temperature and then placed into the cooling chamber at -320°F (-196°C) for approx. 24 hours. Then the material will be warmed back up to room temperature gradually.
When the 1045 has reached room temperature it is recommended to undergo another temper cycle at a temperature range of 400 - 1300°F (205 - 705°C) for at least one hour. The tempering will relieve possible stresses added by the sub-zero treatment and will make sure that the new microstructure will be stabilized.
This diagram shows the micro changes at different temperatures which are important during heat treatment. They show the optimum condition for the hardening, annealing and normalizing process.
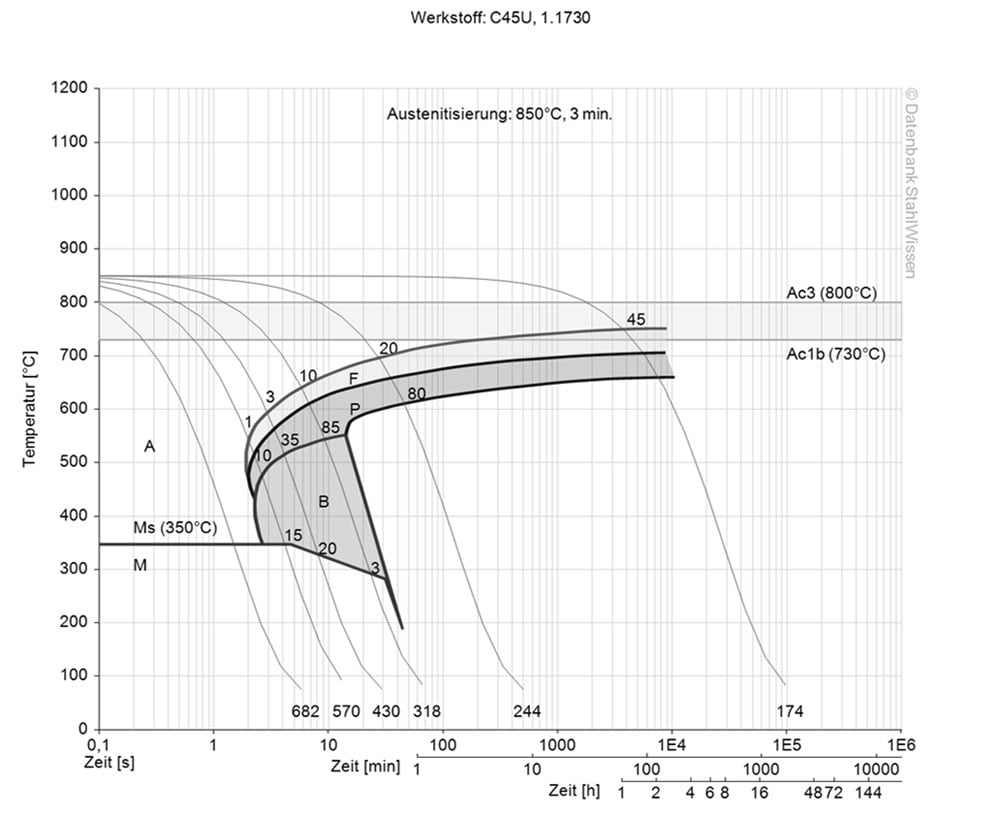
This diagram shows the structural changes at micro level over time at a constant temperature. It shows at what temperature and after what time different phases, e.g., perlite, martensite or bainite start to build.
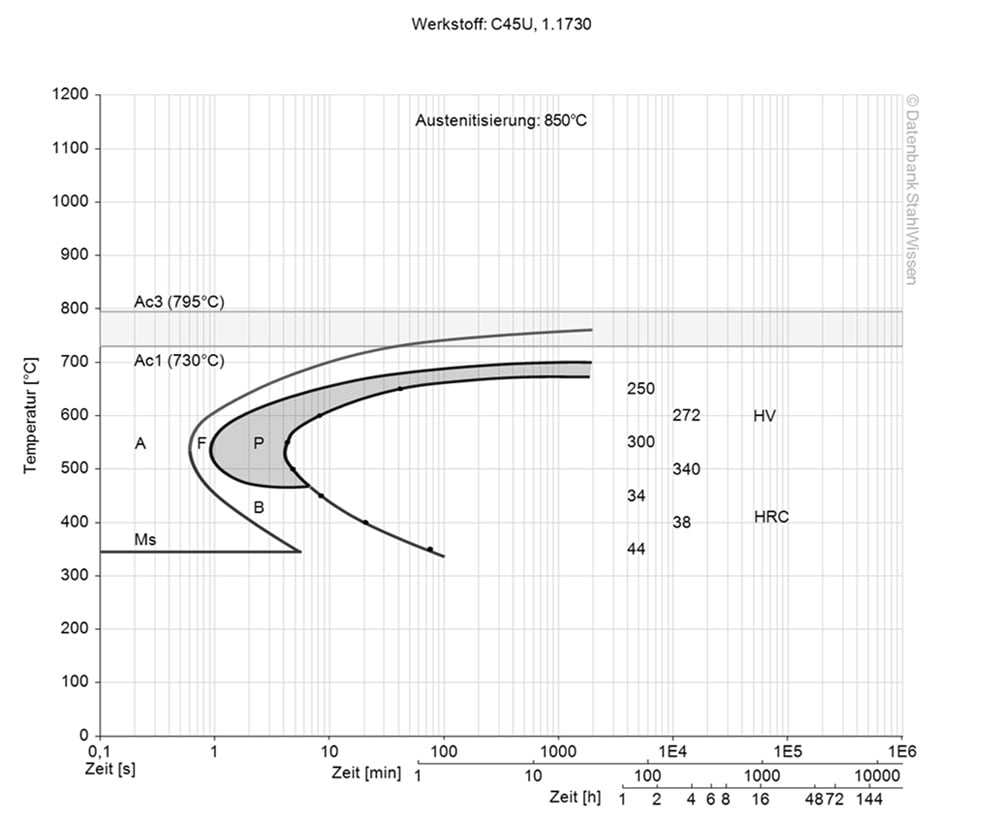

1045 SURFACE TREATMENT
As this steel grade lacks the needed alloys, 1045 is not suitable for nitriding.

1045 PROCESSING
1045 has good machinability and can be used for tapping, drilling, milling, turning, and broaching provided this is executed adequately, applying sufficient feeds, speeds, and tools.
1045 responds very well to forging which makes it suitable to forge tool and machine parts. Follow the practice below to use this steel grade to its best abilities.
Preheat parts to 1382-1472°F (750-800°C), then increase the temperature to 2012-2192°F (1100-1200°C) and hold at this temperature until the material is uniformly heated through. Forge the work piece immediately and finish with a furnace cooling. Do not continue forging below 1562°F (850°C).
Welding 1045 can be done by all conventional welding processes, assuming all the correct processes are used. To avoid cracking, pre-, and post-heating is required.
Preheat at 210-660°F (100-350°C) and maintain this temperature during welding. When finished, cool slowly in sand or ash and relieve stress at 1022-1220°F (550-660°C). Welding 1045 is preferably carried out using low hydrogen electrodes.

1045 APPLICATION OPTIONS
As a medium carbon tool steel this steel grade has got good mechanical properties and can be used to manufacture a great variety of products. As for any other steel grade 1045 depends on the correct treatments to give it its optimum hardness, wear resistance or machinability for the many possible applications.
• Chisels
• Punch holders
• Guide plates
• Backing plates
• Simple bending dies
• Simple structural components
• Top and bottom die casting
• Tongs
• Leather knives
• Forged connecting rods
• Torsion bars
• Fixtures as well as machinery parts
• Automotive components
• Gears
• Shafts
• Rods
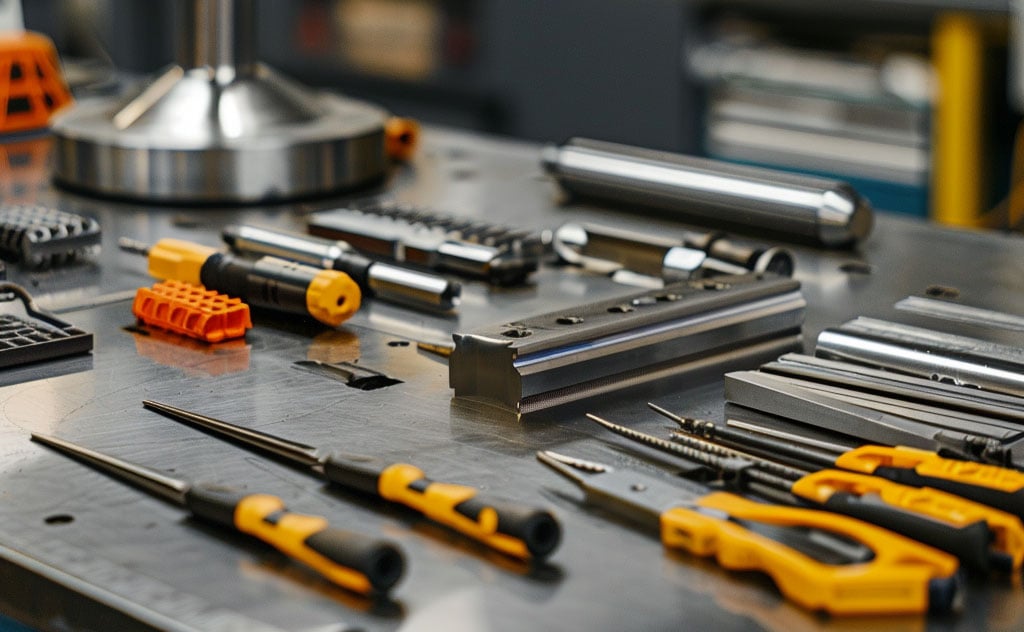

1045 CONCLUSION
1045 is a versatile cold work tool steel that is used in many industries and is used in an even greater number of applications. Due to its medium carbon content, this steel grade is easy to machine and weld. It can also be case-hardened, albeit to a shallow depth of hardness.
• Unalloyed tool steel
• Cold work steel
• Hardenable, due to a carbon content of 0.45 %
• Shell hardener with low hardening depth
• Can be used in the naturally hard state
• Very good machinability
• Good impact strength
• Suitable for inductive and flame hardening
• Nitriding is not common for this material
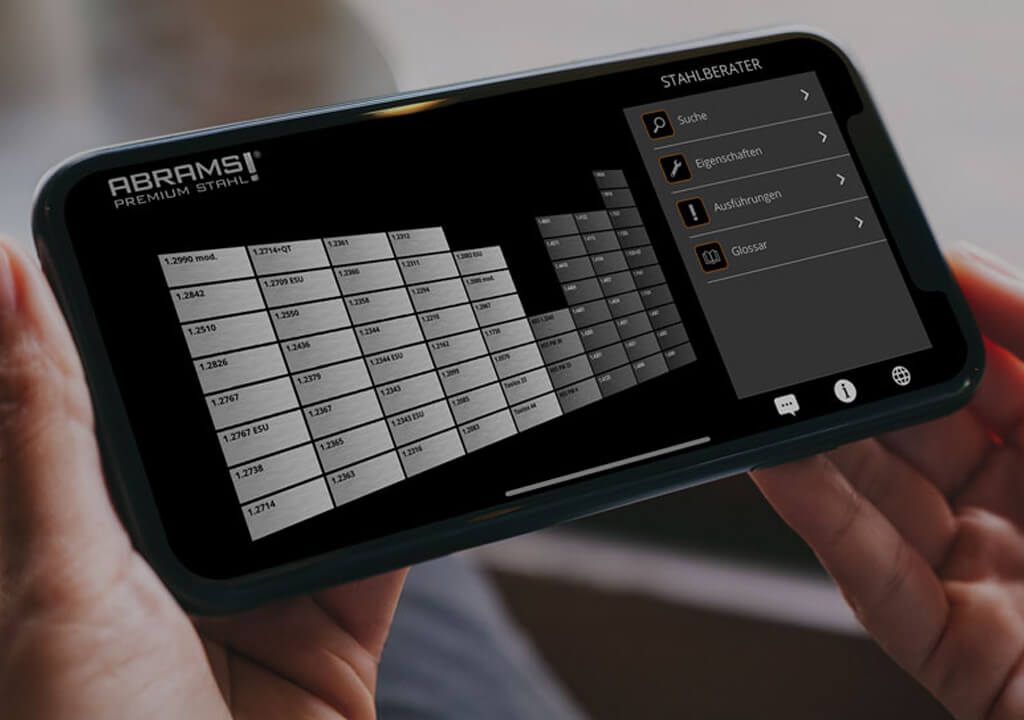

1045 ALTERNATIVES
Are you looking for an alternative steel grade?
WE HAVE THE SOLUTION!
With the ABRAMS STEEL GUIDE, you can obtain an alternative or equivalent steel grade with just a few clicks.

D2 DATASHEET
Download the technical data sheet in PDF format here.
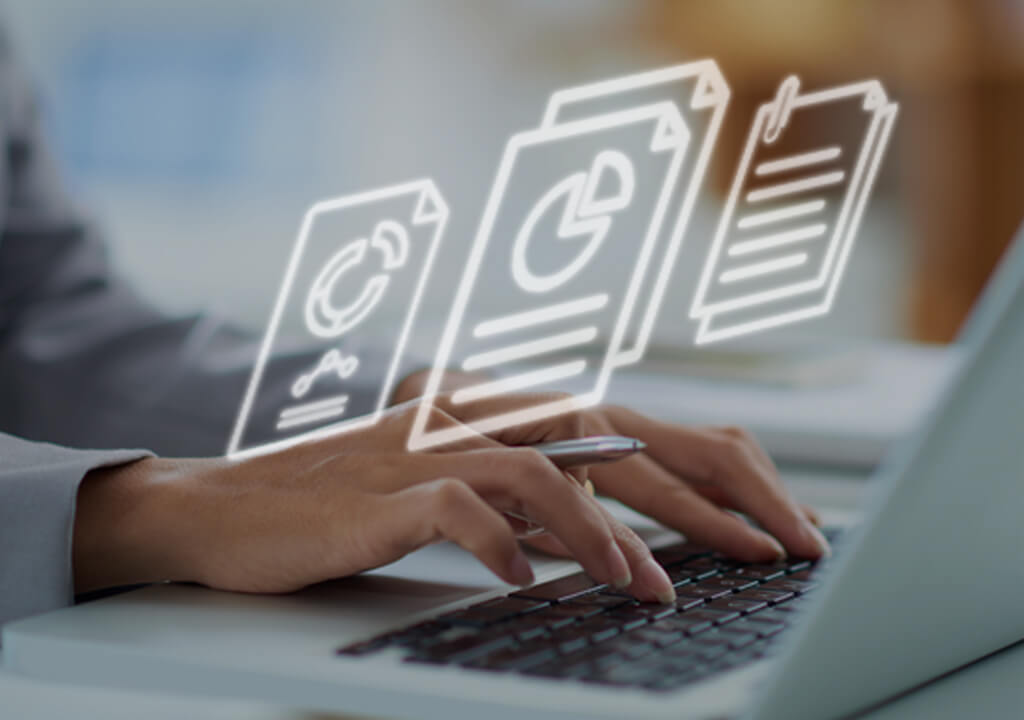
The data shown here has been compiled with the greatest diligence and is regularly updated with regard to the correctness and completeness of its content. The content is indicative only and should not be taken as a warranty of specific properties of the product described or a warranty of suitability for a particular purpose. All information presented is given in good faith and no liability will be accepted for actions taken by third parties in reliance on this information. ABRAMS Industries reserves the right to change or amend the information given here in full or parts without prior notice.