Steel Types
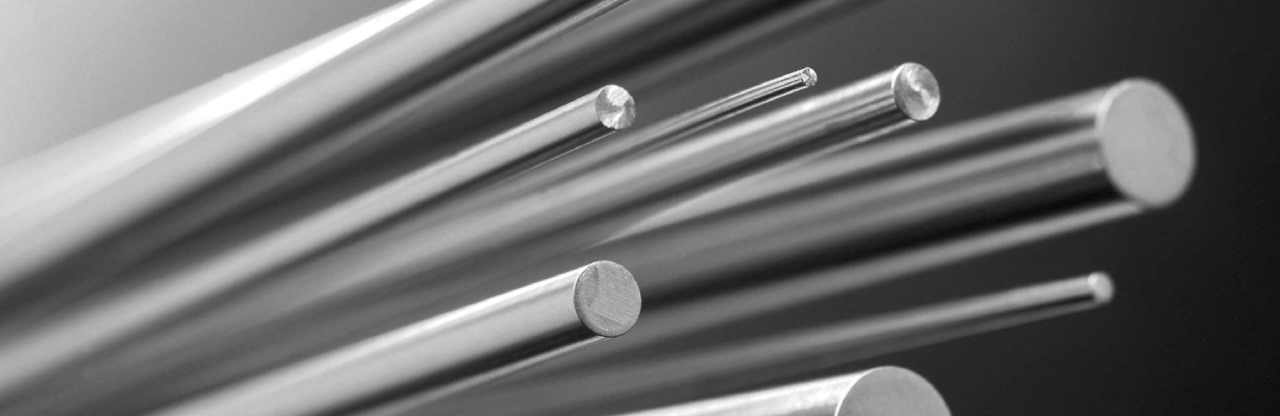
High-grade steel
High-grade steels can be either alloyed or unalloyed steels. They usually have very few defined properties e.g. a minimum yield strength for structural steel: AISI / SAE 1018 / A36 with a minimum yield strength of 370 MPa.
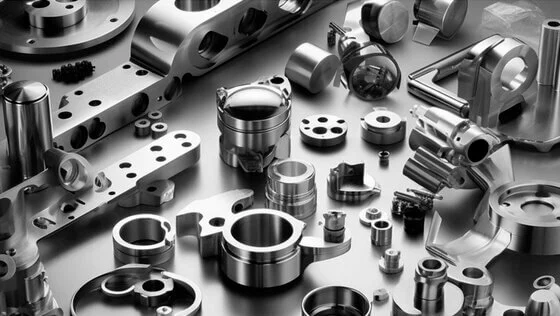
Unalloyed tool steel
In accordance with DIN 10 020, the proportion of alloying elements must be below specific limits regarding unalloyed steels. They are primarily defined as having a carbon content of between 0.40 - 1.40 %. Heat treatment of unalloyed steel results in high surface hardness, high wear resistance and good cutting ability, characterised by a tough core (pure, surface-hardening steel). They are well suited for easy-to-use tools that are subject to low stress. Unalloyed tool steels can be subjected to working temperatures of up to 392 degrees Fahrenheit. (e.g. AISI 1045).
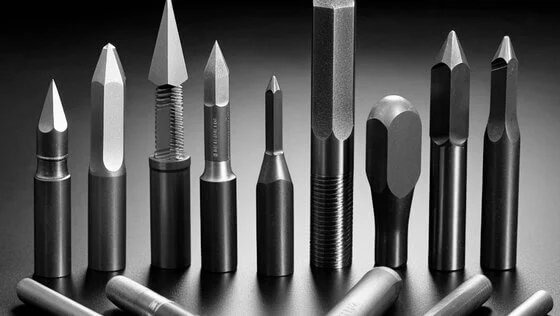
Alloyed tool steel
Alloy tool steels are named in this way because they contain at least one alloying element, the proportion of which is within specific limits set in accordance with DIN 10 020. Thus, a very high hardness is possible (depending on the alloy, also good through-hardenability over the entire component cross-section), in addition to a high wear resistance and / or a high toughness, which makes them suitable for the processing of various materials such as sheet metal or plastic. They are divided into categories according to working temperature: cold work steel (permanent working temperatures up to 392degrees Fahrenheit), hot work steel (permanent working temperatures > 392 degrees Fahrenheit) and high-speed steel (permanent working temperatures up to 1112 degrees Fahrenheit). Regardless of temperature, an additional application-oriented classification of plastic mold steel is often made, whereas the nature of steel meets the special requirements of plastic processing. This basically includes all conventional tool steels and stainless steels.
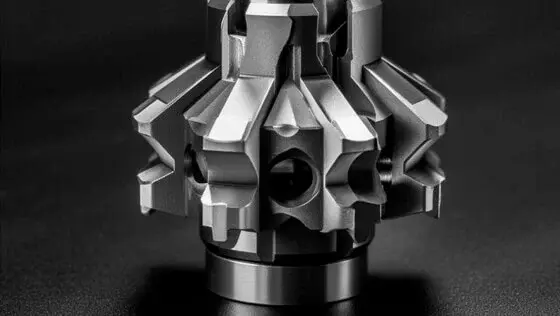
Cold work steel
Within the category of alloyed steels, cold work tools can be constructed that allow either machining (e.g. cutting) or non-machining (e.g. stamping) up to temperatures of 392 degrees Fahrenheit. They mustbe sufficiently tough and pressure-resistant and have high wear resistance. The properties arise from specific combinations of alloying elements: a higher content of chromium, for example, generates hard carbides which increase wear resistance. The addition of molybdenum, vanadium and tungsten can optimise this property. Primarily, cold work steels should be sufficient for machining and exhibit the lowest possible dimensional change over subsequent heat treatments (e.g. AISI / SAE O1).
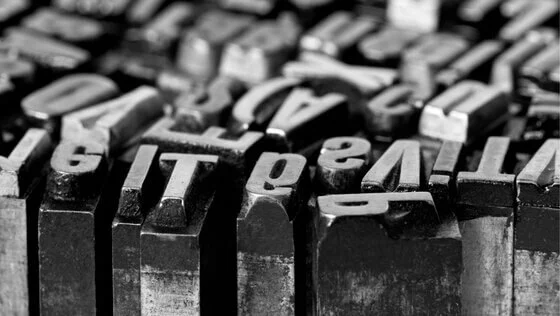
Hot work steel
Also in the category of alloyed steels, hot work tools can be created for processes which, with temperatures reaching less than 392 degrees Fahrenheit, can also be performed by cold work tools (e.g. clamping tools, armours). Their particular alloys however, allow durable, continuous use at temperatures of over 392 degrees Fahrenheit (e.g. forging, hot-rolling or hot shearing). These steels have high temperature strength, toughness, resistance to wear and thermal shock, as well as a high resistance to tempering. Significant alloying elements, in addition to those of cold-work steels, include nickel, molybdenum and cobalt (e.g. AISI / SAE H13).
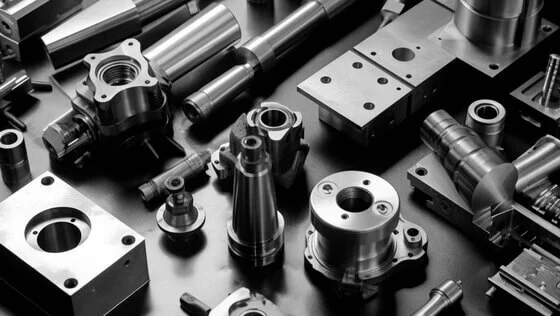
High speed steel
High speed steels are used primarily for the tools engaged in very high cutting speeds (e.g. milling).They are highly alloyed with carbide-forming elements such as chromium, molybdenum, tungsten and vanadium and, alternatively, cobalt for special thermal burdens. In comparison to low-alloy steels, high speed steels are capable of up to a 10-fold increase in cutting speed, as they have very high temperature strength, wear resistance, resistance to tempering and thermal hardness (red hardness). They are also referred to as HSS (e.g. AISI / SAE M2).
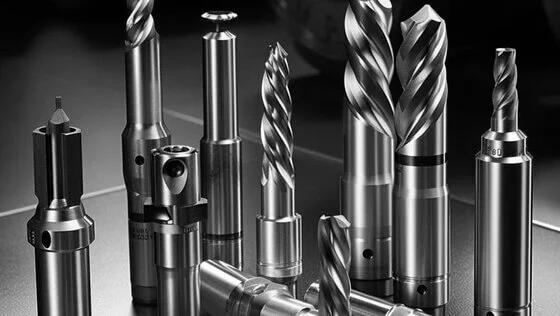
Plastic mold steel
Plastic mold steel is the generic term for steels which, in addition to other cold or hot work, can also be used in the machining and processing of plastics. As the requirements are very diverse, there are many tool and engineering steels available for use in the manufacture of plastic parts. Distinctions are made between injection tools (in this case, the plastic hardens in the mold, for example in the mold inserts) and die-casting tools (here the steel only comes in contact with liquid plastic, such as extrusion dies). Plastic mold steels need to be easily polishable, due to the high surface quality of the final products (degree of purity), must be heat resistant, as well as pressure and wear resistant and, in the processing of PVC products, also rust and acid resistant (e.g. AISI / SAE H10).

Corrosion resistant steel
Corrosion-resistant steels generally have a high alloy of chromium (at least 12 %), (e.g. AISI / SAE 420). They do not necessarily guarantee full rust resistance, but they do prevent the technically problematic occurence of rust corrosion. Basically, every corrosion-resistant steel is also "conditionally acid-resistant",depending on the aggressive agent and concentration. Steels with at least 8 % nickel, for example, are more resistant (e.g. AISI / SAE 304). Corrosion and acid-resistant steels are generally used in the food processing and chemical industries. Depending on alloy composition, the structure is classified as either martensitic (magnetisable, e.g. AISI / SAE 440C) or austenitic (not magnetisable, e.g. AISI / SAE 304).
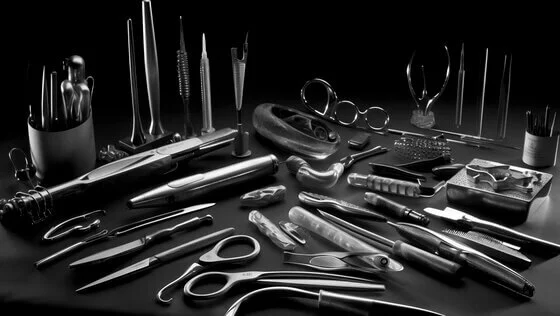
Case Hardening Steel
Hardening steels range from medium-alloyed to unalloyed steels, which generally have less than 0.25 % carbon. At temperatures > 1688 degrees Fahrenheit, these steels can be enriched with carbon (carburisation), (e.g. using powder / granules, gas or salt bath). The carbon diffuses into the surface zone up to a depth of 0.0591 - 0.0787 inches. After carburisation, a combination of various hardening processes are applied, taking into account the need for different curing temperatures, corresponding with different carbon concentrations in surface and core. Case hardening steels have a working hardness up to 62 HRC, whereas the core hardness is determined by the degree of alloy content (e.g. AISI / SAE 5115, AISI / SAE 5120).
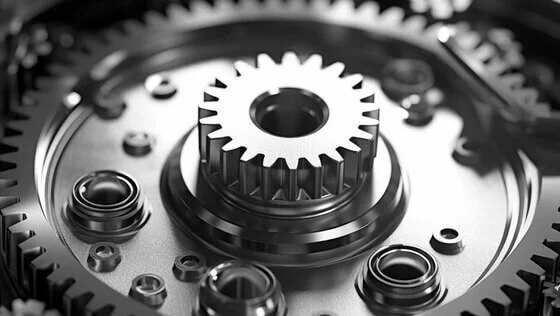
Heat-Treatable Steel
Quenched and tempered steels (quenched and tempered = hardened) can be either alloyed or unalloyed steelsgenerally have a carbon content between 0.25 and 0.60 %, are particularly suitable for tempering, and possess special mechanical properties after tempering (e.g. a desired tensile strength and good toughness, which would be otherwise unavailable under normal conditions). Upon request, the steel can be delivered partially annealed (e.g. AISI / SAE 1045) or rather the steel can be delivered in a tempered condition, (e.g. AISI / SAE P20 PH).
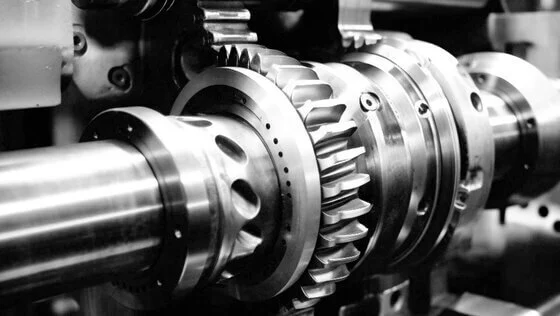
Search for steel with the ABRAMS STEEL GUIDE®
It is possible to find an alternative steel grade in no time at all!
Steel search ABRAMS STEEL GUIDE® (Registration is not needed).
With just one click to your chosen steel grade and an alternative grade with its properties.