6F7 ESR Tool Steel - 1.2767 ESU - 45NiCrMo16 - JIS ~SKT 6
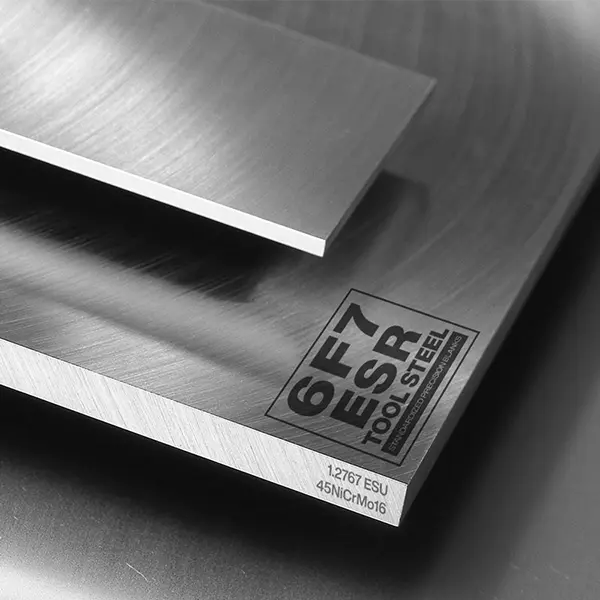
6F7 ESR Tool Steel - 1.2767 ESU - 45NiCrMo16 - JIS ~SKT 6
Back to Steel OverviewGround Flat Stock and $mart Flat Stock comes always in a machined condition, that means:
NO decarburization on the surfaces (decarburization leads to unreliable components and tools)
Less dirt on your machines during further processing – nothing but clean chips
Stress-relieved flat steel avoids warping of components during further machining
Get the close-to-finish-size thickness and width you need for the components you plan
Ground Flat Stock and $mart Flat Stock comes always in a machined condition, that means:
NO decaburization on the surfaces (decarburization leads to unreliable components and tools)
Less dirt on your machines during further processing – nothing but clean chips
Stress-relieved flat steel avoids warping of components during further machining
Get the close-to-finish-size thickness and width you need for the components you plan
Ground Flat Stock and $mart Flat Stock comes always in a machined condition, that means:
NO decaburization on the surfaces (decarburization leads to unreliable components and tools)
Less dirt on your machines during further processing – nothing but clean chips
Stress-relieved flat steel avoids warping of components during further machining
Get the close-to-finish-size thickness and width you need for the components you plan
6F7 ESR STEEL PRICE CHART

6F7 ESR STANDARD VALUES
C
Si
Mn
P
S
Cr
Mo
Ni
45NiCrMo16
50 HRC - 54 HRC
max. 260 HB
45NiCrMo16
50 HRC - 54 HRC
max. 260 HB
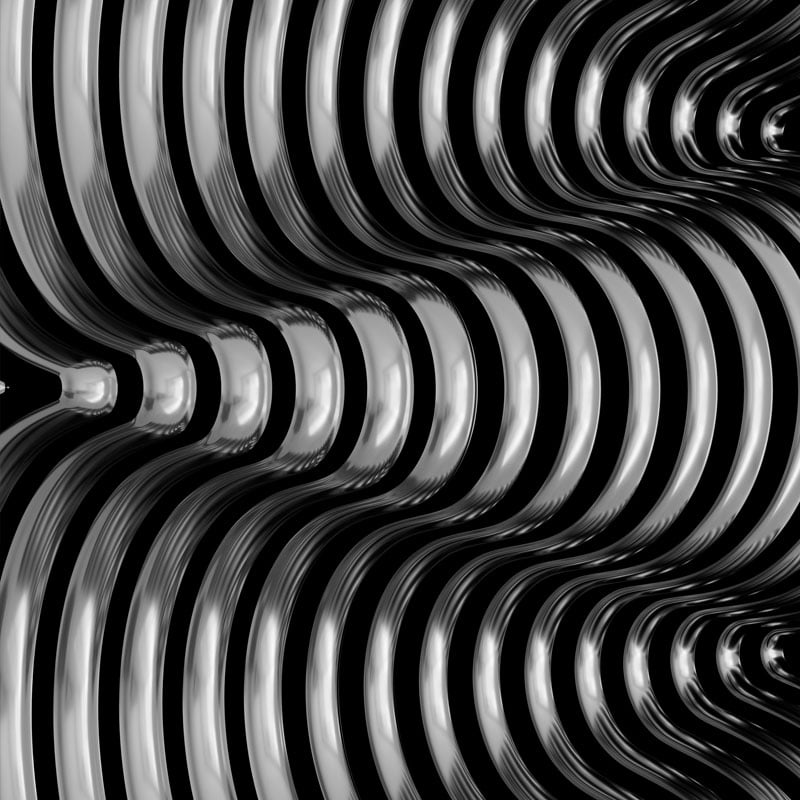

6F7 ESR PHYSICAL PROPERTIES
6F7 ESR (ESR = Electro-Slag-Refined or Remelted) has, with the addition of nickel, the ability, even for large cross sections, to be through-hardened very well. With its high compressive strength this tool steel grade lends itself for stamping or demanding coining tools for example. It has a very high resistance against bending which is an advantage when used as bending inserts. 6F7 ESR is exceptionally suitable to be polished to a high mirror finish and therefore is a fitting choice to process plastics that require a high surface finish.
With its durability, longevity, high hardness and toughness and its resistance to thermal fatigue and cracking the 6F7 ESR is suitable for many applications and industries like the manufacturing, machining, automotive, plastics, toolmaking and medical industry.
To be classed as stainless steel a steel grade has to have a minimum mass fraction of 10.5% of chromium. The 6F7 ESR has a mass fraction of 1.2 - 1.5% of chromium and will therefore stain in corrosive or wet environments.
To be corrosion resistant the 6F7 ESR should have a minimum of 10.5% of chromium. As it only has a content of 1.2 - 1.5% of chromium it is not classed as a corrosion resistant steel.
Like most tool steels the 6F7 ESR is composed of iron and carbon, the iron makes the steel grade magnetizable and are so called ferromagnetic steels.
Grinding, milling and eroding for example can be done on machines using magnetic clamping.
The wear resistance for tool steel 6F7 ESR scores a 2 on a scale where 1 is low and 6 is high.
Cold work steels are used for working temperatures up to 392°F (200°C) and are suited for applications like molds, cutting tools and cold hobbing for example.

6F7 ESR TECHNICAL PROPERTIES
Tool steel 6F7 ESR can be used to make knives as it has high hardness, wear resistance and toughness which are needed in knife making. Due to its high hardness it is harder to sharpen, its low corrosion resistance means it should be regularly maintained to prevent corrosion.
ESR material has fewer inclusions and its carbides are distributed more uniformly this might give the knife a better finish and can have a sharper edge.
The working hardness for tool steel 6F7 ESR is 469 - 534 BHN (50 - 54 HRC).
Typically the density of 6F7 ESR tool steel is 0.284 lb/in3 (7.85g/cm3) at room temperature.
Tool steel 6F7 ESR has a tensile strength of approx. 127.6 KSI on delivery (0.145 KSI = 1MPa). In order to reach this value, a tensile test is performed to show how much force is needed to stretch or elongate a sample before it breaks.
Heat conductivity table | |
Value | By temperature |
31.0 | 73.4°F |
34.0 | 302°F |
33.9 | 572°F |
34.1 | 662°F |
33.2 | 752°F |
31.2 | 932°F |
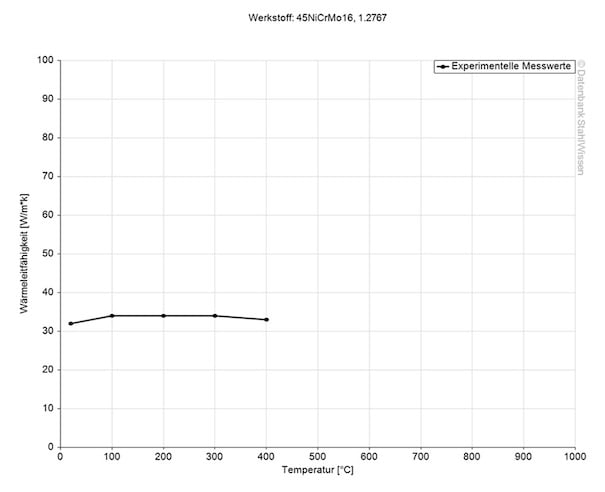
The following table shows expansion or contraction at various temperatures, which may be very important for high temperature works or when working with high temperature changes.
Medium thermal expansion coefficient | |
10-6m/(m • K) | At a temperature of |
11.3 | 68 - 212°F |
11.9 | 68 - 392°F |
12.5 | 68 - 572°F |
12.2 | 68 - 662°F |
12.0 | 68 - 752°F |
12.1 | 68 - 842°F |
12.4 | 68 - 932°F |
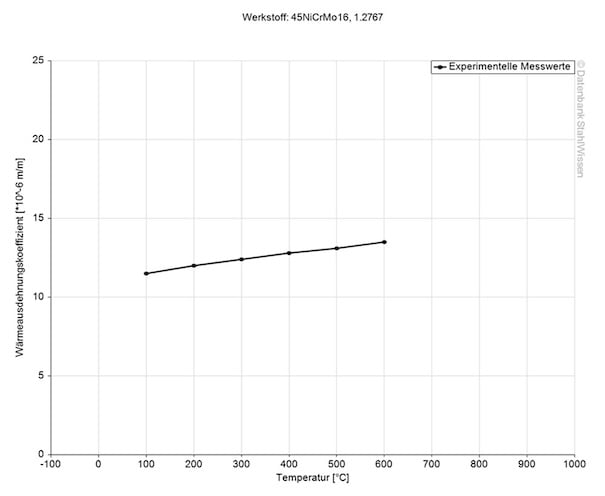
The specific heat capacity of tool steel at room temperature is 460 J/g-°C (0.109 BTU/lb-°F). This value shows how much heat is needed to heat 1lb of material by 1 Fahrenheit.
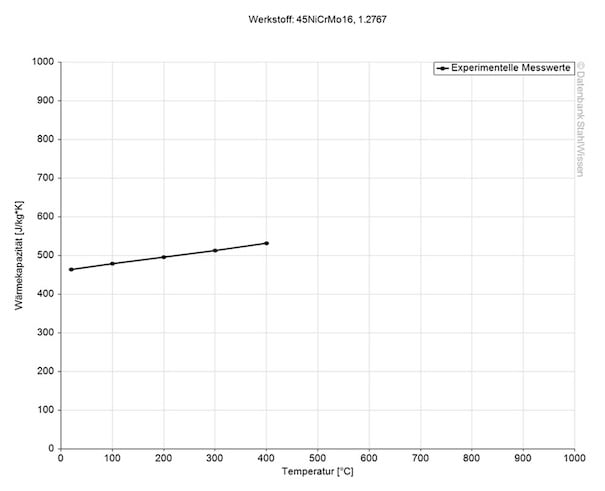
The following table shows the electrical resistivity of tool steel 6F7 ESR.
Table of the specific electrical resistivity | |
Value | At a temperature of |
0.3 (Ohm*mm²)/m | 68°F |
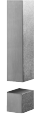
6F7 ESR AS $MART FLAT STOCK.
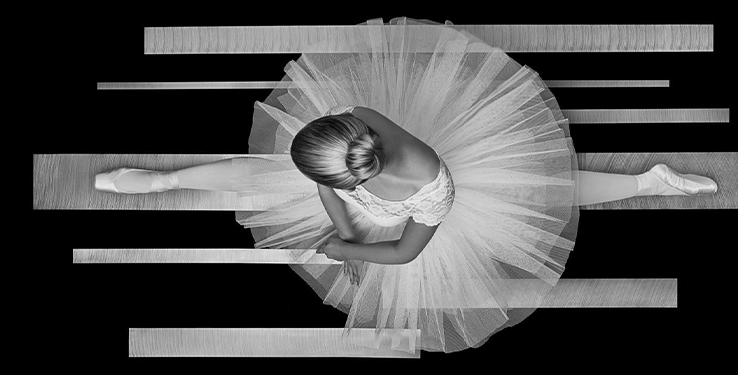
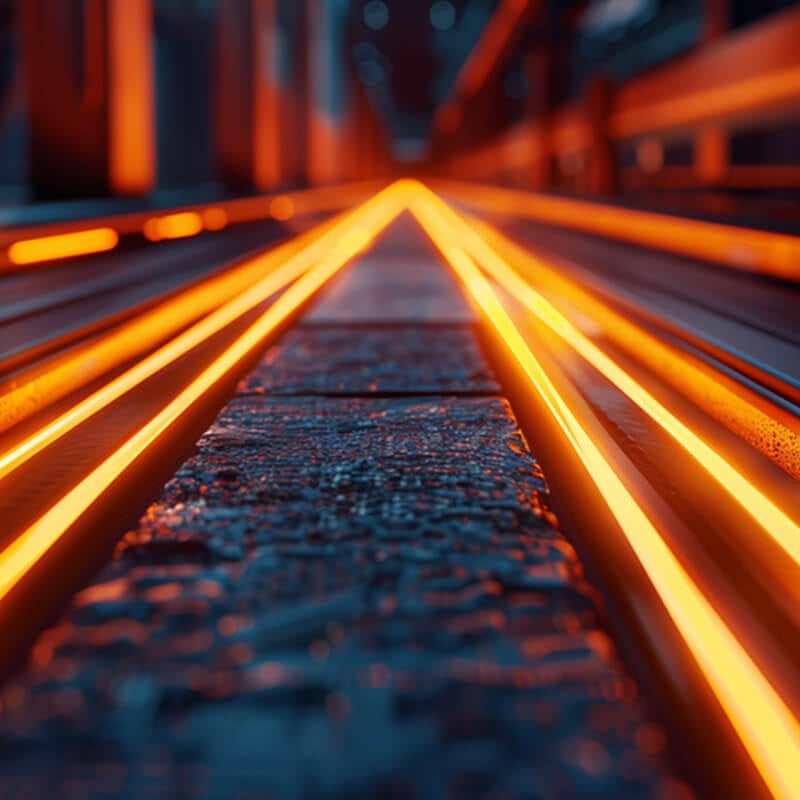

6F7 ESR PROCEDURE
Heat the material to a uniform temperature of 1130 - 1202°F (610 - 650°C) and hold for 2 - 5 hours and slowly cool at a rate of 50 - 68°F (10 - 20°C) to about 1112°F (600°C) in the furnace and then continue the cooling phase in air.
After rough machining, grinding or shaping, heat the parts uniformly to a temperature of 1202°F (650°C) and hold for 2 hours in a neutral atmosphere. To finish the process let the parts cool slowly in the furnace. Uniform and controlled heating and cooling the 6F7 ESR can avoid creating new thermal stresses and possible dimensional changes.
Preheat the material to 1202°F (650°C) uniformly, then take the temperature to 1544 - 1598°F (840 - 870°C) and hold for 15 - 30 minutes when the temperature has equalized.
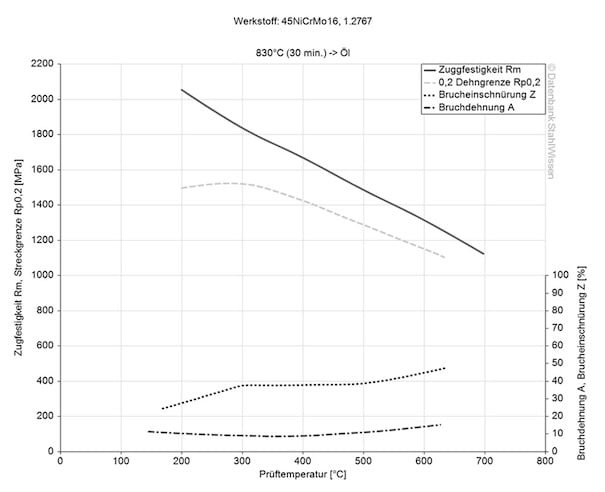
Following are a few quenching methods, they should be chosen carefully and with properties and applications, they are selected for, in mind.
• Air
• Warm oil (approx.176°F / 80°C)
• Salt bath (572 - 752°F / 300 - 400°C)
• Gas
Immediately after hardening the 6F7 ESR, heat the parts slowly to the chosen tempering temperature. It is recommended to temper the parts twice. Let parts cool to room temperature between tempers. The chosen temperature should be held for a minimum of 2 hours or 1 hour per inch (25.4 mm) of thickness.
To avoid undesirable deformation during plastic molding, the tempering temperature after hardening should be 122°F (50°C) higher than the operating temperature.
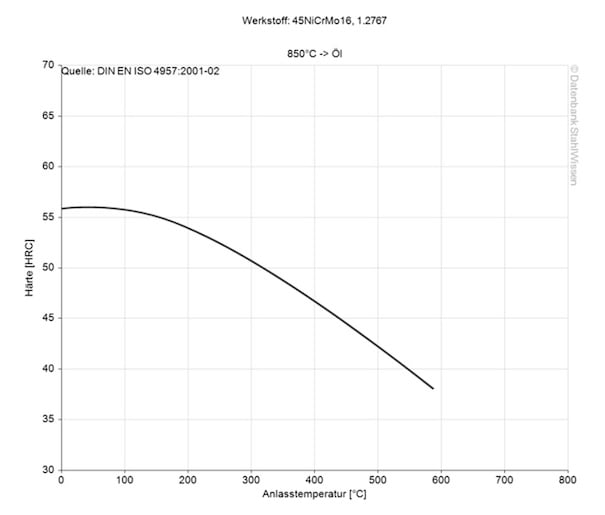
This diagram shows the micro changes at different temperatures which are important during heat treatment. They show the optimum condition for the hardening, annealing and normalizing process.
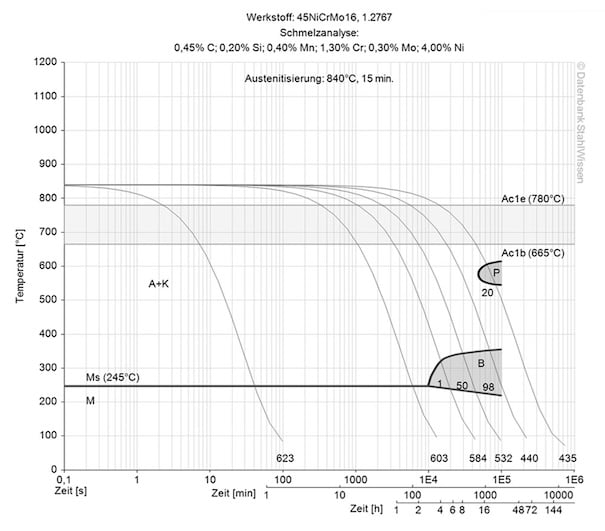
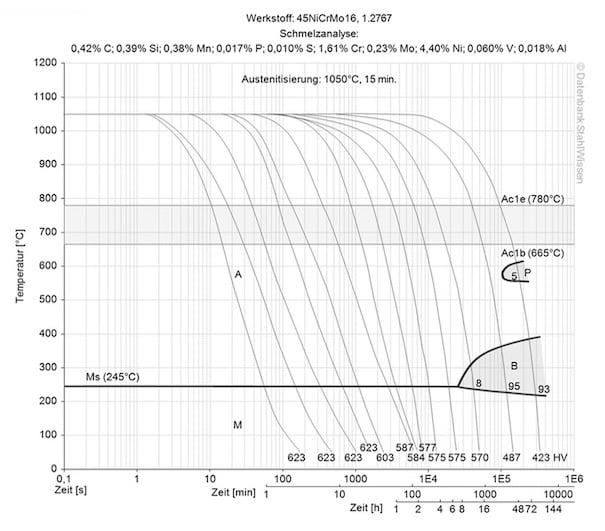
The following diagram shows the structural changes at micro levels over time at a constant temperature. It shows at what temperatures the different phases, e.g., perlite, martensite and bainite start to form.
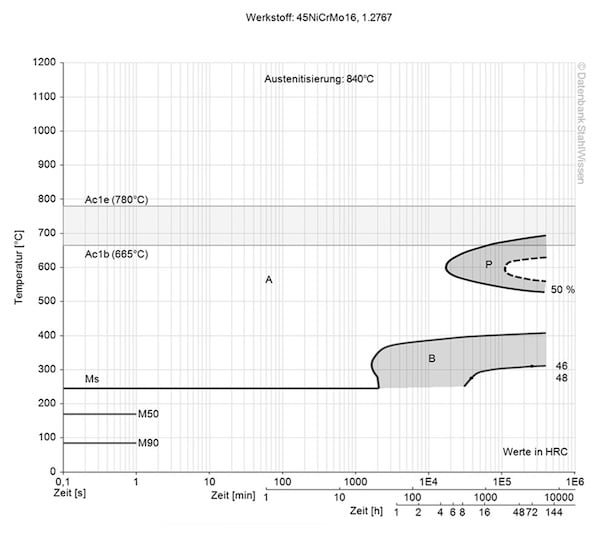

6F7 ESR SURFACE TREATMENT
There are a variety of surface treatments available for tool steel 6F7 ESR to enhance wear resistance, hardness and corrosion resistance. The surface treatment should be carefully chosen with consideration to where and what the material will be used for. Following are a few examples of surface treatments for the 6F7 ESR.
Nitriding diffuses nitrogen into the surface of the steel and gives it a harder and more wear resistant surface. It can improve the fatigue life and corrosion resistance of the 6F7 ESR.
Carburizing diffuses carbon into the surface of the material which gives the surface a higher hardness and wear resistance.
This process diffuses nitrogen and carbon into the surface of the metal giving it a higher hardness and wear resistance.
Boronizing layers the material surface with a very hard boride layer. This praxis is used for tools or components with high abrasive wear.
This process adds a layer of chromium on the surface of the steel. Chrome plating improves wear and corrosion resistance.
Both processes overlay the material with a thin, hard coating. The process can enhance hardness, improve wear resistance and reduce friction.
It is possible to polish this material grade to a high gloss finish.

6F7 ESR PROCESSING
EDM is used for parts made from one individual piece, for cutting dies or when making intricate shapes and sharp corners. The former can be achieved when choosing the correct EDM process, electrode and parameters. The recast layer can be removed through stoning or polishing.
This steel grade, like most metals, can contract and expand when heated or cooled. Also during phase changes, from residual stresses and with decarburization there can be some dimensional changes which can affect the properties for this steel grade.
Controlled heating and cooling, stress relieving and avoiding overheating can reduce the risks of thermal shock and unwanted dimensional changes like warping or distortion but also cracking which potentially means to start a project anew.
Slowly and uniformly heat the material to a temperature range of 1562 - 1922°F (850 - 1050°C). Soak and then cool slowly in the furnace to 1112°F (600°C) and then cool the 6F7 ESR further down in air.
Due to cracking and mechanical property changes in the weld area, welding should be avoided. If welding is unavoidable the material should be welded in the annealed condition and pre- and post heat treatment is advised.
Select the correct grade of grinding wheel and make sure it is in good condition with suitable dressing tools.

6F7 ESR APPLICATION OPTIONS
With its durability, longevity, high hardness and toughness and its resistance to thermal fatigue and cracking the 6F7 ESR is suitable for many applications and industries like the manufacturing, machining, automotive, plastics, toolmaking and medical industry.
• Cutting tools
• Cutlery punches
• Embossing tools
• Bending tools
• Cold hobbing tools
• Pressure bars
• Billet shear knives
• Cold shear knives
• Plastic molds
• Hot press tools
• Light metal processing
• Heavy metal processing
• Drawing jaws
• Reinforcements
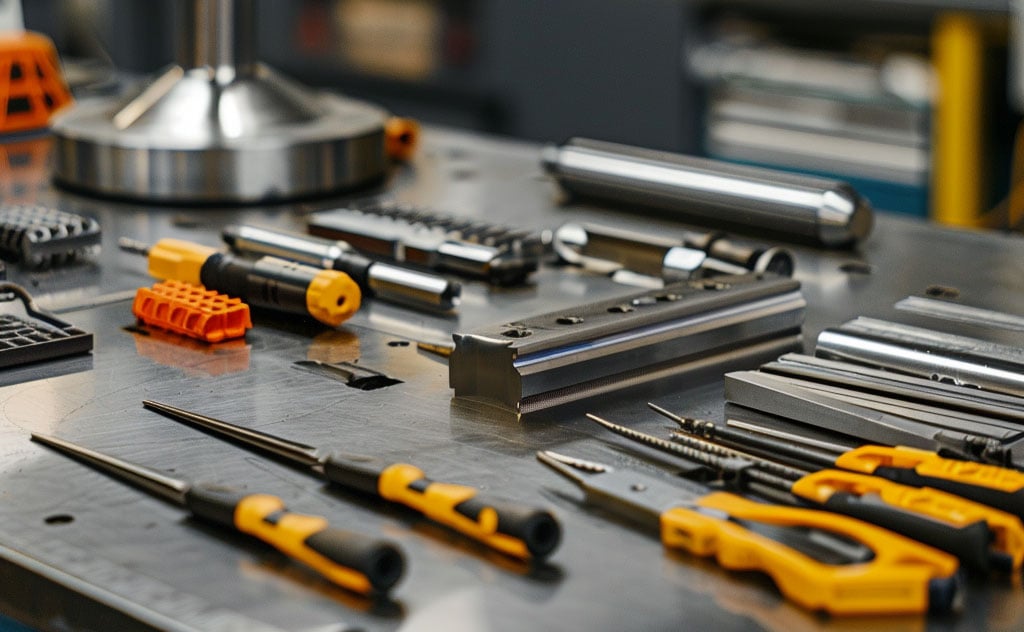

6F7 ESR CONCLUSION
As an ESR steel with a special purity and homogeneousness the 6F7 ESR has a unique combination of wear resistance, toughness and hardness. Those properties make the 6F7 ESR a great choice for applications which are demanding and use high stress components. Careful consideration of use, properties needed, appropriate heat treatment and maintenance is required to reduce unwanted changes or risks.
Practically, this means:
- High compressive and flexural strength
- Good through-hardenability, even with large cross-sections
- Good polishability
- Good etchability
- Good erodibility
- High toughness
- Working hardness is a maximum of 54 HRC
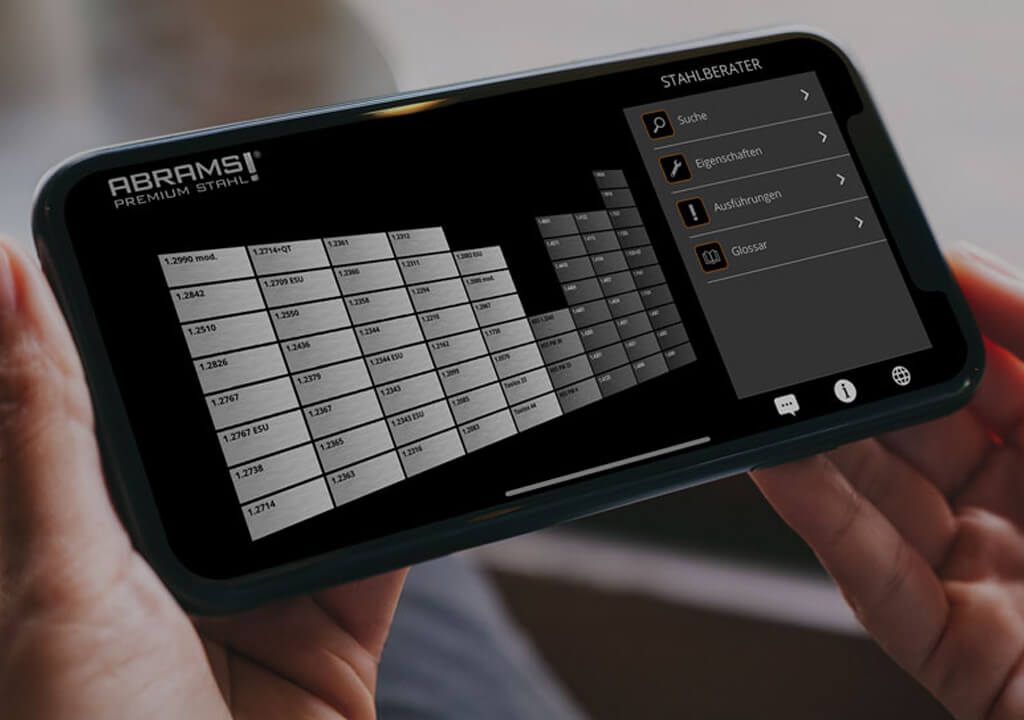

6F7 ESR ALTERNATIVES
Are you looking for an alternative steel grade?
WE HAVE THE SOLUTION!
With the ABRAMS STEEL GUIDE, you can obtain an alternative or equivalent steel grade with just a few clicks.

6F7 ESR DATASHEET
Download the technical data sheet in PDF format here.
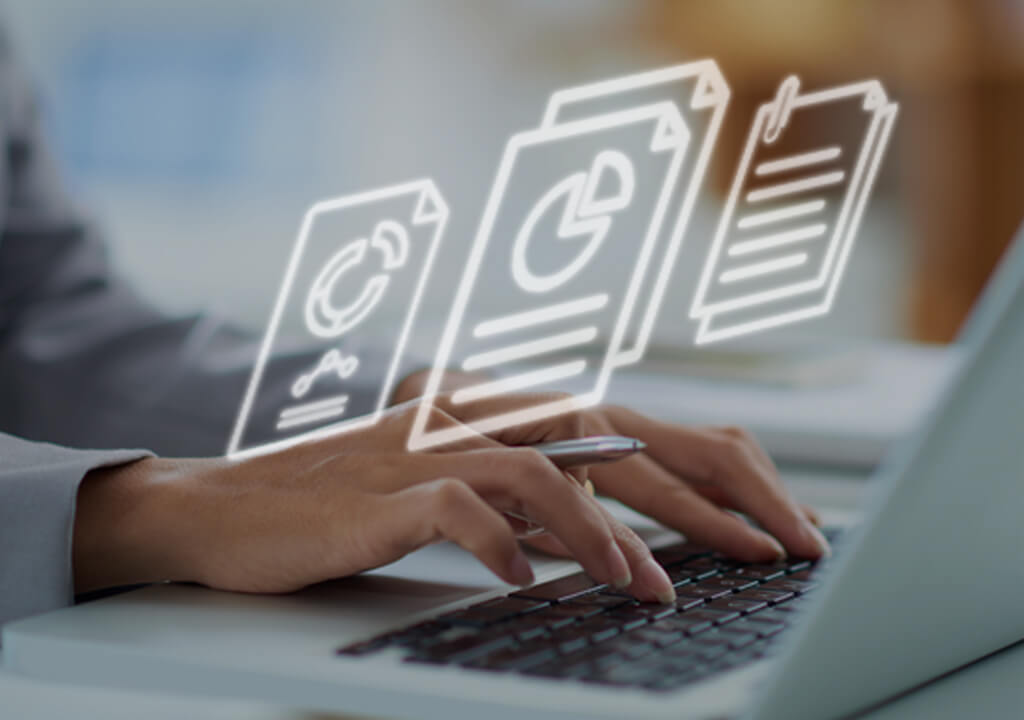
The data shown here has been compiled with the greatest diligence and is regularly updated with regard to the correctness and completeness of its content. The content is indicative only and should not be taken as a warranty of specific properties of the product described or a warranty of suitability for a particular purpose. All information presented is given in good faith and no liability will be accepted for actions taken by third parties in reliance on this information. ABRAMS Industries reserves the right to change or amend the information given here in full or parts without prior notice.