P20 PH Tool Steel - ~1.2311 PH - ~40CrMnMo7 - Data Sheet
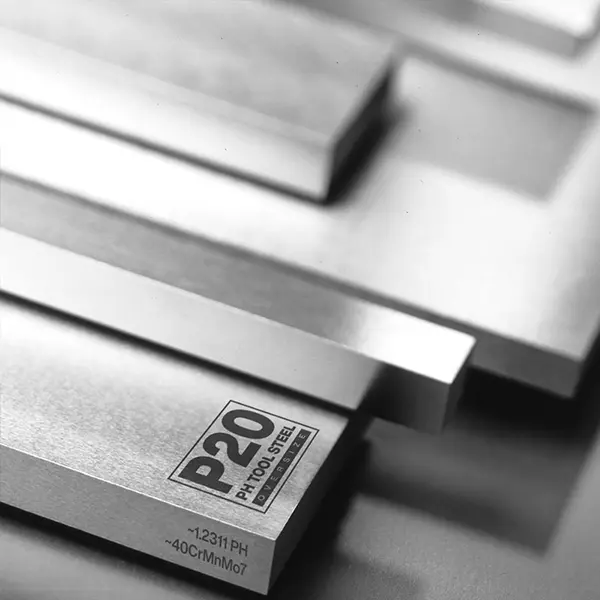
P20 PH Tool Steel - ~1.2311 PH - ~40CrMnMo7 - Data Sheet
Back to Steel OverviewGround Flat Stock and $mart Flat Stock comes always in a machined condition, that means:
NO decarburization on the surfaces (decarburization leads to unreliable components and tools)
Less dirt on your machines during further processing – nothing but clean chips
Stress-relieved flat steel avoids warping of components during further machining
Get the close-to-finish-size thickness and width you need for the components you plan
Ground Flat Stock and $mart Flat Stock comes always in a machined condition, that means:
NO decaburization on the surfaces (decarburization leads to unreliable components and tools)
Less dirt on your machines during further processing – nothing but clean chips
Stress-relieved flat steel avoids warping of components during further machining
Get the close-to-finish-size thickness and width you need for the components you plan
Ground Flat Stock and $mart Flat Stock comes always in a machined condition, that means:
NO decaburization on the surfaces (decarburization leads to unreliable components and tools)
Less dirt on your machines during further processing – nothing but clean chips
Stress-relieved flat steel avoids warping of components during further machining
Get the close-to-finish-size thickness and width you need for the components you plan
P20 PH STEEL PRICE CHART

P20 PH STANDARD VALUES
C
Si
Mn
P
S
Cr
Mo
~40CrMnMo7
approx. 32 HRC (delivery condition) - 50 HRC
max. 325 HB
~40CrMnMo7
approx. 32 HRC (delivery condition) - 50 HRC
max. 325 HB
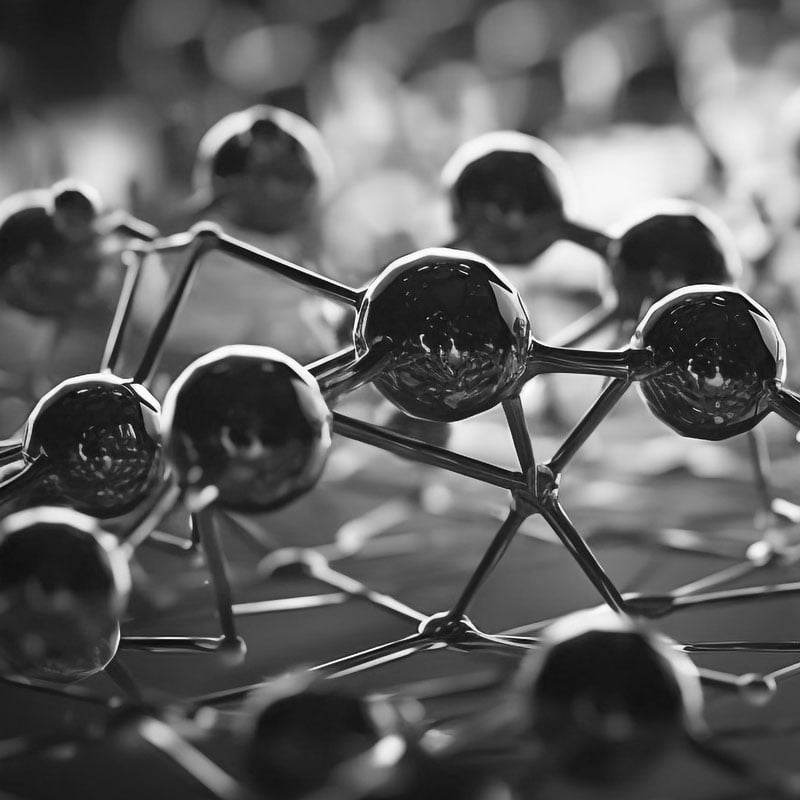

P20 PH PHYSICAL PROPERTIES
The P20 Ph is delivered as pre-hardened material and can be used in its delivered condition which is beneficial when mold making. In general, P20 PH tool steel is mainly used for plastic molds, die casts and tools but is also suitable for applications such as rails and shafts. The steel grade has good weldability and can be polished to an excellent finish.
It has a high through-hardenability and uniform component strength which is an advantage when maintaining a consistent performance of tools and molds. For a higher hardness the P20 PH can be further hardened but its hardenability compared to other tool steels is limited and it is not suitable for applications with high stresses.
P20 PH has a chromium content of 1.8 - 2.1% and is therefore not a corrosion resistant steel in the classic sense like stainless steel.
Additional surface treatment and maintenance as well as keeping parts in a dry environment may prolong the resistance to corrosion but can not hold it back completely.
P20 PH can be readily cold worked using regular tooling methods.

P20 PH TECHNICAL PROPERTIES
The working hardness for the P20 PH is in the range of 300 - 469 BHN (32 - 50 HRC).
Typically the density of P20 tool steel is 0.284 lb/in3 (7.85g/cm3) at room temperature.
The yield strength shows how much stress has to be applied to plastically deform and when the point is reached for the material not to return to its original state after stresses have been removed. It then either stays in the mischaped form or breaks.
The P20 PH range for this tool steel is between 120 - 125 KSI (827 - 862 MPa).
The heat conductivity for the P20 PH tool steel is at 34.5 W/(m*K) (19.95 BTU/(h-ft*°F)) at room temperature.
Heat conductivity table | ||
Value W/(m*K) | Value BTU/(h-ft*°F) | By temperature |
34.5 | 19.95 | 68°F |
33.5 | 19.37 | 662°F |
32.0 | 18.50 | 1292°F |
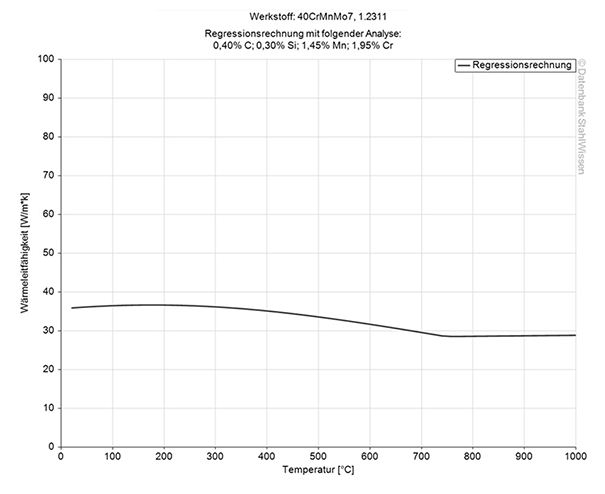
The following table shows expansion or contraction at various temperatures, which may be very important for high temperature works or when working with high temperature changes.
Medium thermal expansion coefficient | |
10-6m/(m • K) | At a temperature of |
11.1 | 68 - 212°F |
12.9 | 68 - 392°F |
13.4 | 68 - 572°F |
13.8 | 68 - 752°F |
14.6 | 68 - 932°F |
14.9 | 68 - 1292°F |
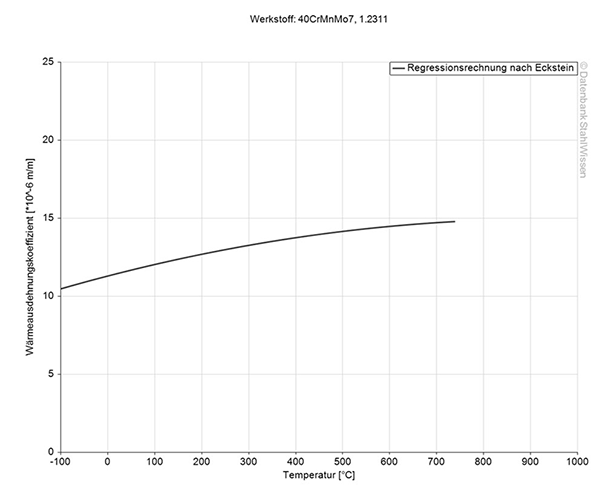
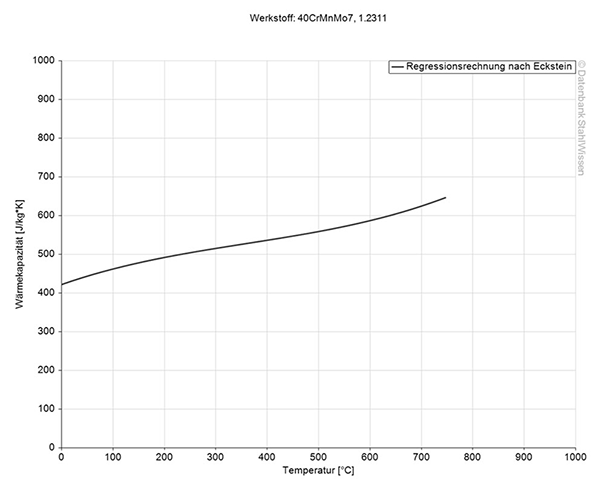
The following table shows the electrical resistivity of the P20 PH tool steel.
Table of the specific electrical resistivity | |
Value | At a temperature of |
0.47 (Ohm*mm²)/m | 68°F |
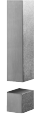
P20 PH AS PRECISION GROUND FLAT STOCK OR $MART FLAT STOCK.
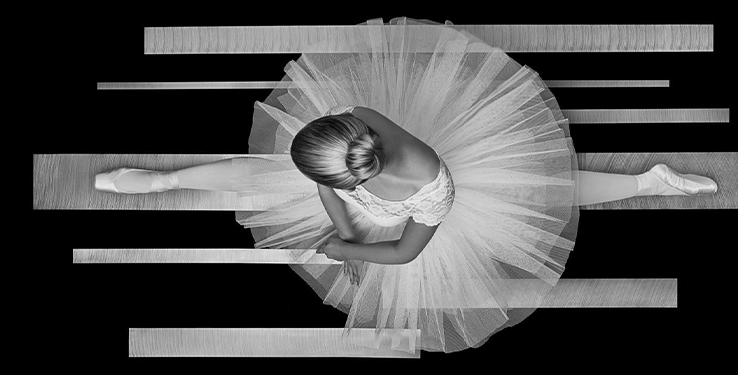
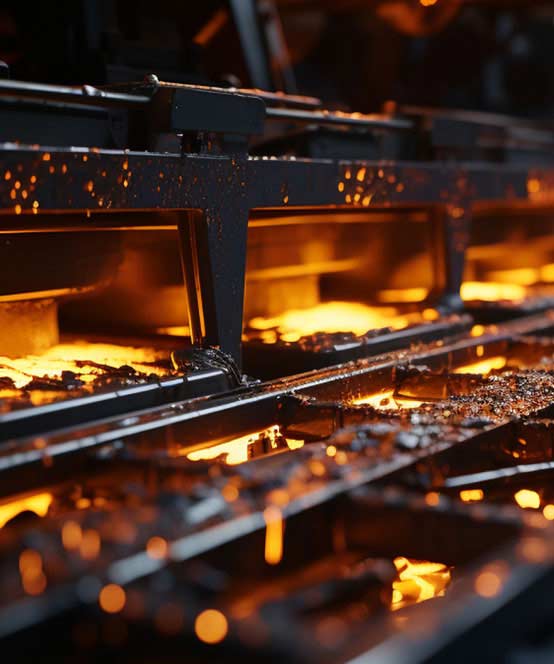

P20 PH PROCEDURE
Normalizing will refine the grain structure and give the steel a uniform microstructure. It can help to improve machinability and can relieve internal stresses which may have been introduced during former heat treatment, forging or casting for example.
Heat the material uniformly above its critical temperature and soak for approx. 1 hour per 1 inch (25.4 mm) of thickness. Then remove the parts from the furnace and cool them in still air.
Finish the process with a thorough inspection that the parts have the desired microstructure and properties.
P20 PH should be stress relieved after machining and occasionally during service. Heat the work piece uniformly to 1022 - 1112°F (550 - 600°C) and hold for 1 hour per inch (25.4 mm) of thickness and cool in the furnace.
Reducing stresses prevents the P20 PH from distorting or cracking, improves the mechanical properties of the material and it enhances the dimensional stability which is important for molds.
The parts should be quenched in the following media with a temperature of 356 - 392°F (180 - 200°C):
- • Oil
- • Saltbath
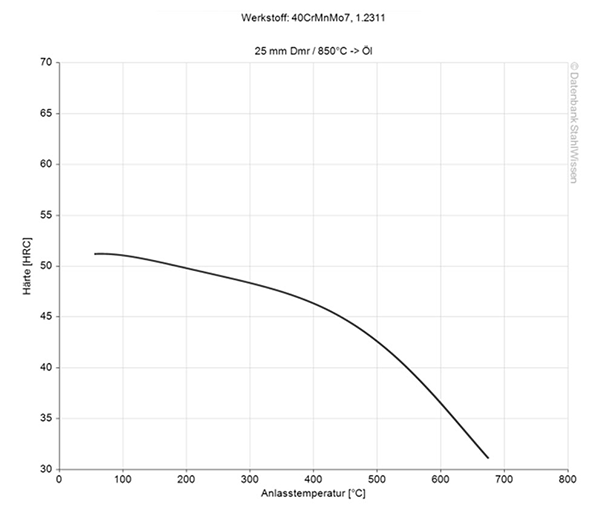
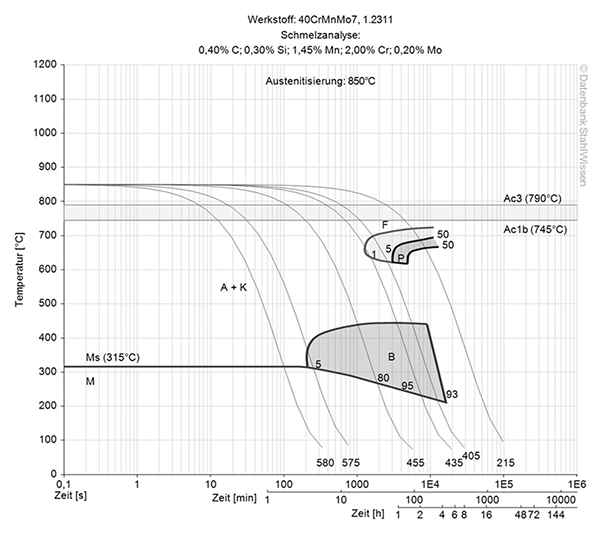
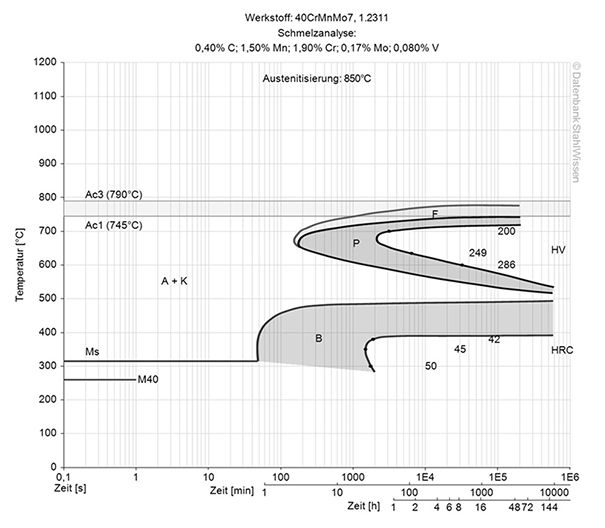

P20 PH SURFACE TREATMENT
Following are a few examples of surface treatments that can be given to P20 parts.
P20 PH can be polished to a high finish when the correct procedures are applied. To avoid an orange peel effect and pitting,care should be taken not to over polish this material.
Physical Vapor Deposition (PVD) deposits a thin film on the surface of the material, this treatment enhances wear resistance and can reduce friction.
This process deposits a nickel-phosphorus coating, without the electrical current, by chemical reduction onto the surface of the material.
Black oxide coating can enhance the corrosion resistance of the parts but is mostly done for esthetic purposes. It will give parts a blue-black coloring that will reduce light reflecting off the surface.
Laser surface hardening can localize surface hardening without affecting the properties of the steel and provides better wear resistance in those areas. This is done by using a high powered laser that heats certain surface areas and rapidly cooling those areas again.

P20 PH PROCESSING
The P20 PH has a good balance of machinability and toughness. For extensive machining use the P20 in its annealed condition rather than in its prehardened state.

P20 PH APPLICATION OPTIONS
No further heat treatment for the P20 PH is intended, this makes it usable as delivered and without any delays.
As further heat treatment is not needed the risks of distortion during the treatment are eliminated and needed properties like high wear resistance, toughness for molds, dies, jigs and tooling is evenly spread throughout.
• Mechanical engineering
• Jigs
• Base plates
• Assembling parts
• Molding frames
• Plastic molds
• Plastic processing
• Injection molds
• Die casting molds
• Hydroforming tools
• Recipient sleeves
• Intermediate sleeves
• Folding bars
• Tool holders
• Extrusion presses
• Tube presses
• Die holders
• Die insert
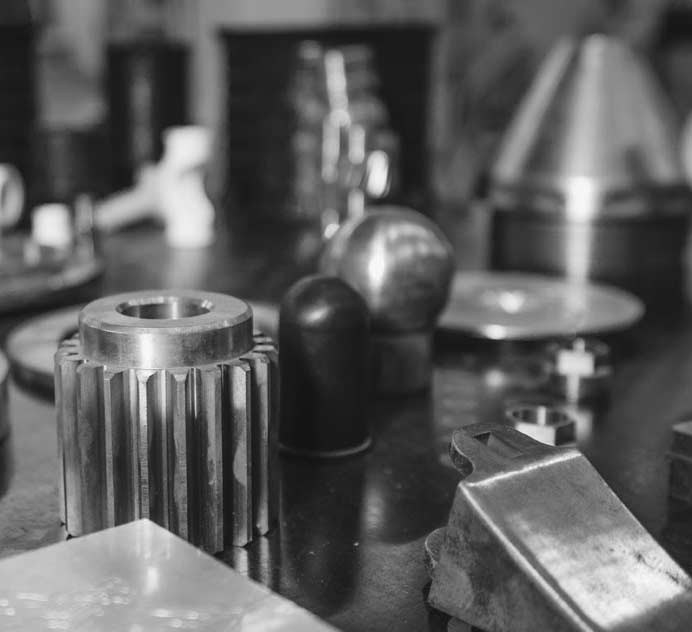

P20 PH CONCLUSION
- Quenched and tempered cold work steel
- Plastic mold steel
- Etchable
- High through-hardening
- Uniform component strength
- Nitridable
- Erodible
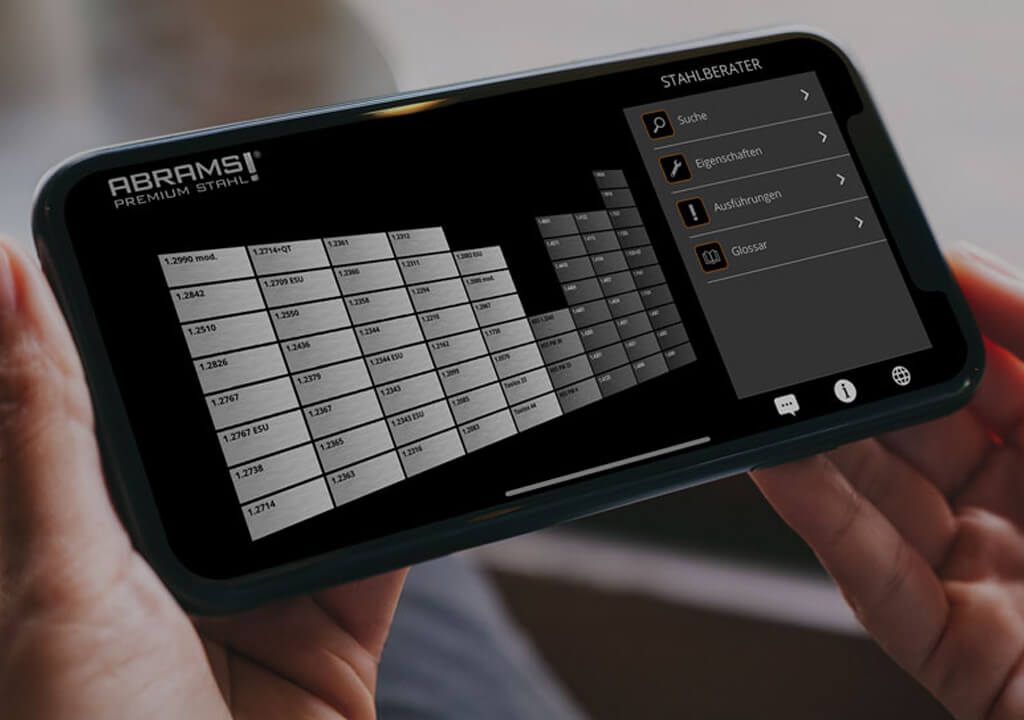

P20 PH ALTERNATIVES
Are you looking for an alternative steel grade?
WE HAVE THE SOLUTION!
With the ABRAMS STEEL GUIDE, you can obtain an alternative or equivalent steel grade with just a few clicks.

P20 PH DATASHEET
Download the technical data sheet in PDF format here.
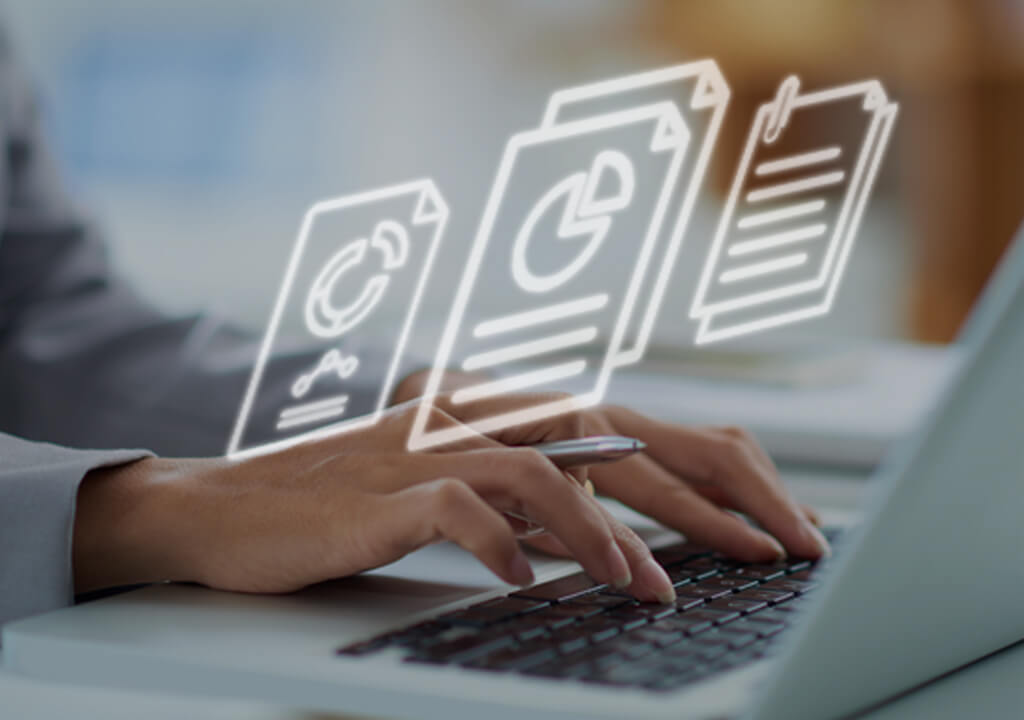
The data shown here has been compiled with the greatest diligence and is regularly updated with regard to the correctness and completeness of its content. The content is indicative only and should not be taken as a warranty of specific properties of the product described or a warranty of suitability for a particular purpose. All information presented is given in good faith and no liability will be accepted for actions taken by third parties in reliance on this information. ABRAMS Industries reserves the right to change or amend the information given here in full or parts without prior notice.