L6 Tool Steel - 1.2714 - 55NiCrMoV7 - SAE L6 - JIS ~SKT 4
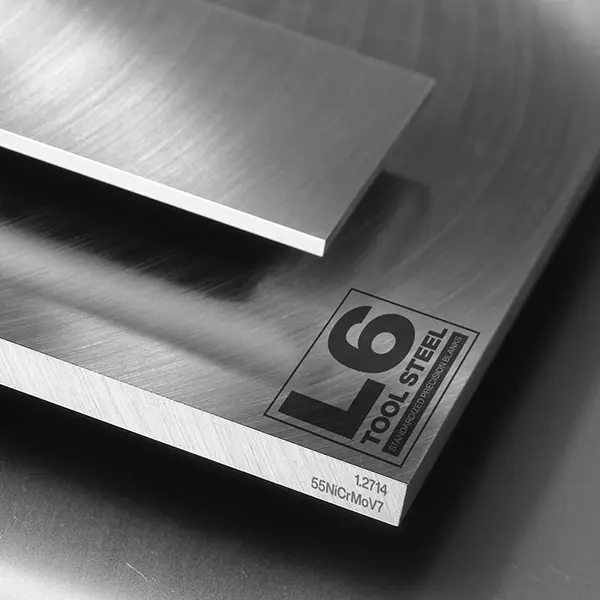
L6 Tool Steel - 1.2714 - 55NiCrMoV7 - SAE L6 - JIS ~SKT 4
Back to Steel OverviewGround Flat Stock and $mart Flat Stock comes always in a machined condition, that means:
NO decarburization on the surfaces (decarburization leads to unreliable components and tools)
Less dirt on your machines during further processing – nothing but clean chips
Stress-relieved flat steel avoids warping of components during further machining
Get the close-to-finish-size thickness and width you need for the components you plan
Ground Flat Stock and $mart Flat Stock comes always in a machined condition, that means:
NO decaburization on the surfaces (decarburization leads to unreliable components and tools)
Less dirt on your machines during further processing – nothing but clean chips
Stress-relieved flat steel avoids warping of components during further machining
Get the close-to-finish-size thickness and width you need for the components you plan
Ground Flat Stock and $mart Flat Stock comes always in a machined condition, that means:
NO decaburization on the surfaces (decarburization leads to unreliable components and tools)
Less dirt on your machines during further processing – nothing but clean chips
Stress-relieved flat steel avoids warping of components during further machining
Get the close-to-finish-size thickness and width you need for the components you plan
L6 STEEL PRICE CHART

L6 STANDARD VALUES
C
Si
Mn
P
S
Cr
Mo
Ni
V
55NiCrMoV7
40 HRC - 54 HRC
max. 250 HB
55NiCrMoV7
40 HRC - 54 HRC
max. 250 HB
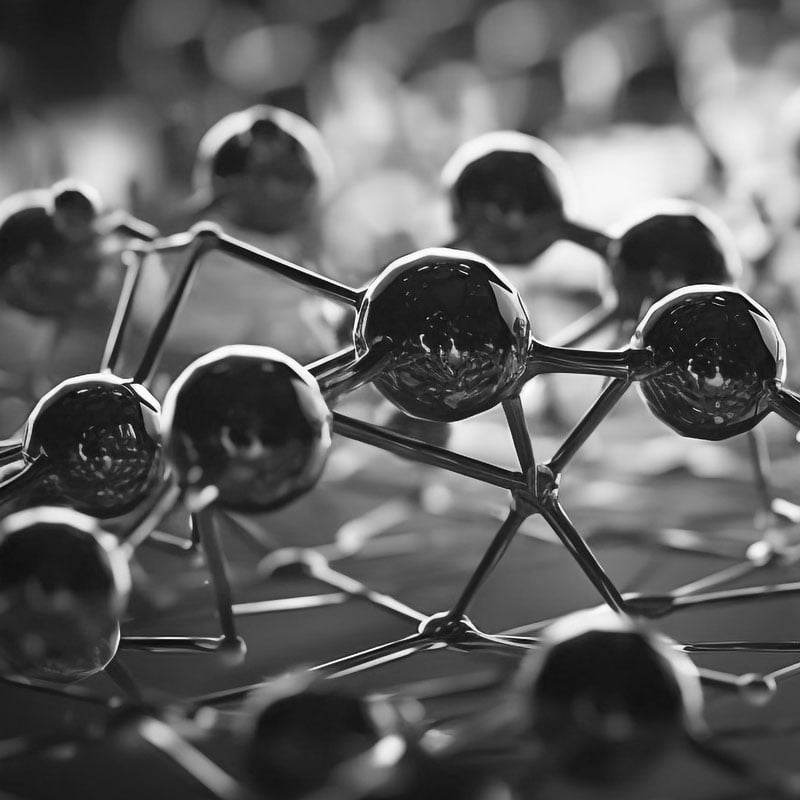

L6 PHYSICAL PROPERTIES
As an oil hardening chrome nickel tool steel, L6 is often used for applications needing a greater toughness. This steel grade has a better toughness due to the nickel content, at the same time retaining good hardness and wear resistance. With its lower carbon content, it has a slightly better shock resistance in comparison to higher alloyed steels and can be used if wear resistance is secondary to increased toughness.
No, the L6 is not a stainless steel. Stainless steel has a mass fraction of 10.5% of chromium, the L6 has a range of 0.8 to 1.2% of chromium.
L6 tool steel is not a corrosion resistant steel. In order to be corrosion resistant steel has to have a minimum chromium content of 10.5% to make it corrosion resistant like stainless steel.
Though the L6 has some corrosion resistance it will corrode when exposed to corrosive environments or moisture. To protect this steel grade, it can be coated or the surface may be additionally treated against corrosion.
The wear resistance for the L6 is 2 on a scale where 1 is low and 6 is high.

L6 TECHNICAL PROPERTIES
The combination of high carbon, toughness, decent wear resistance and that the L6 is easy to sharpen and holds an edge reasonably well make this steel grade a steel that is suitable for knife making.
As L6 is not a stainless steel, knives should be maintained, kept dry and clean to prevent corrosion.
The working hardness for the tool steel L6 is in the range of 373 - 534 BHN (40 - 54 HRC).
Hot working, hot rolling, forging and extrusion, unlike cold working, does not work harden the L6 tool steel. It can be formed extensively, can reduce porosity and can improve the overall structure.
Care, while hot working, needs to be taken to prevent scaling, potential distortion and excessive grain growth.
Cold working, cold drawing, rolling and cold forging, can induce work hardening, achieve tighter tolerances and a smooth surface finish without further machining.
The increased hardness might in turn aid cracking but can also lead to increased tool wear and any internal stresses introduced in this process might need to be followed up with a stress relieving treatment.
Typically the density of tool steel O1 is 0.282 lb/in3 (7.8g/cm3) at room temperature.
L6 tool steel has a tensile strength of approx. 123.2 KSI on delivery (0.145 KSI = 1MPa). In order to reach this value, a tensile test is performed to show how much force is needed to stretch or elongate a sample before it breaks.
The heat conductivity for tool steel L6 is at 36.0 W/(m*K) (250 BTU/(h-ft*°F)) at room temperature.
Heat conductivity table | |
Value | By temperature |
36.0 | 68°F |
38.0 | 662°F |
35.0 | 1292°F |
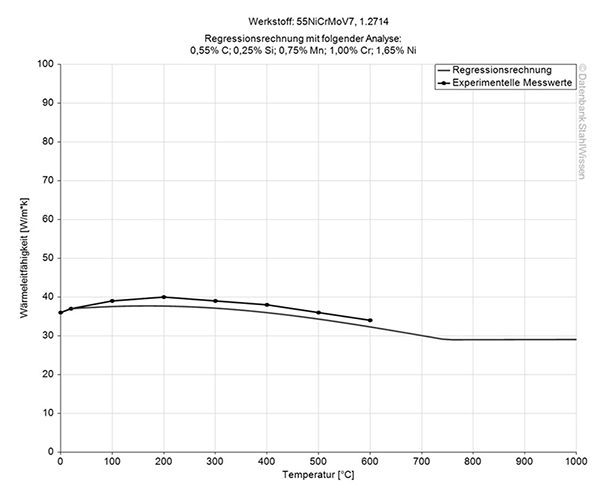
The L6 tool steel thermal expansion coefficient shows how much the material might expand or contract when the temperature is changed. This is very important information, especially when working with high temperatures, or where there are strong temperature changes during applications.
Medium thermal expansion coefficient | |
10-6m/(m • K) | At a temperature of |
12.2 | 68 - 212°F |
13.0 | 68 - 392°F |
13.3 | 68 - 572°F |
13.7 | 68 - 752°F |
14.2 | 68 - 932°F |
14.4 | 68 - 1112°F |
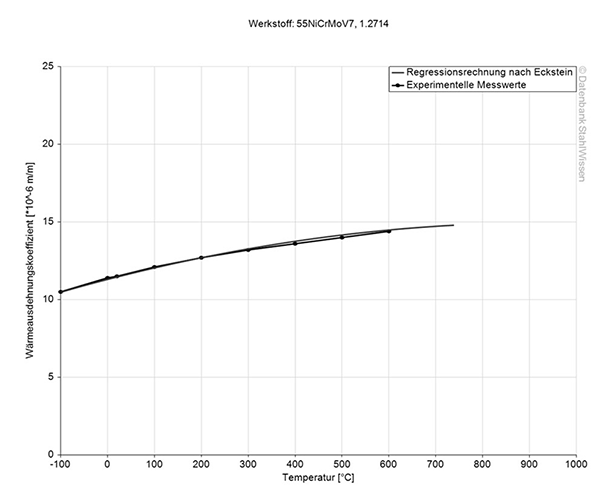
The specific heat capacity of the tool steel L6 at room temperature is 0.46 J/g-°C (0.109 BTU/lb-°F). This value shows how much heat is needed to heat 1lb of material by 1 Fahrenheit.
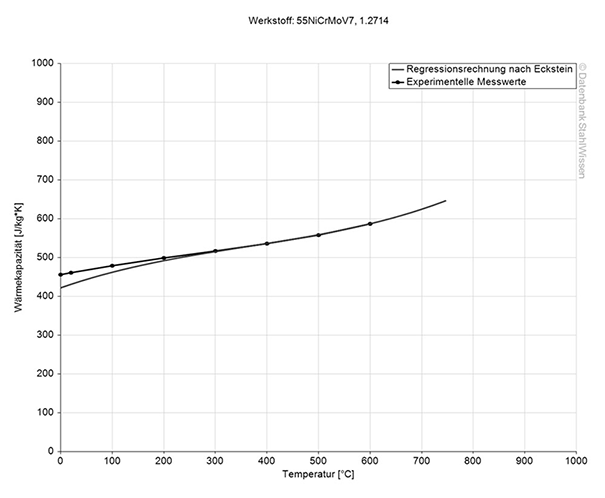
You can find the temperature dependent material constant (Resistivity) in the following table. The electrical conductivity is the reciprocal value of the specific resistance.
Table of the specific electrical resistivity | |
Value | At a temperature of |
0.3 (Ohm*mm²)/m | 68°F |
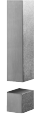
PERFECT MATERIAL SELECTION WITH THE ABRAMS STEEL GUIDE®: STEEL-GUIDE.US
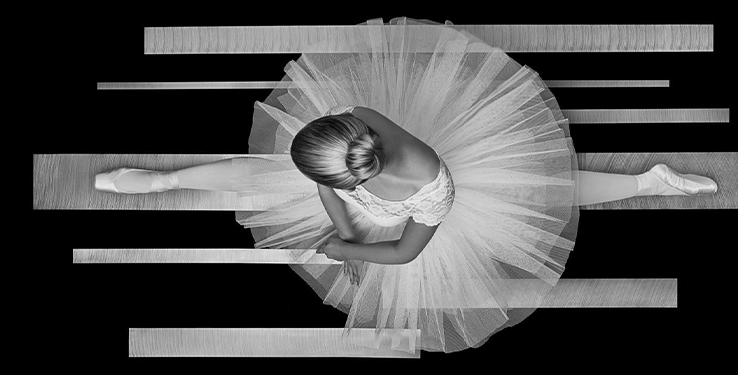
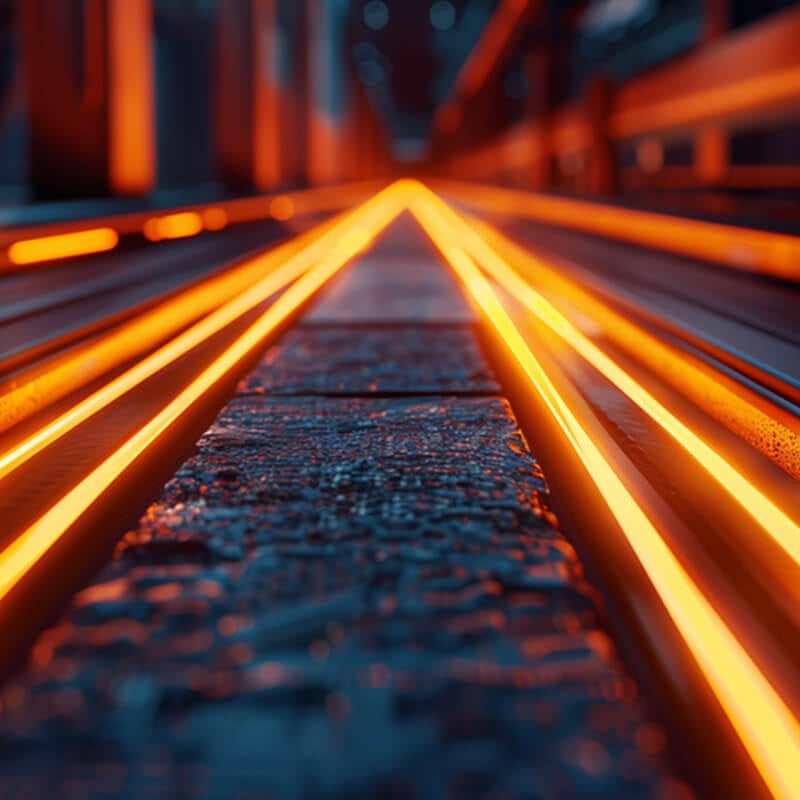

L6 PROCEDURE
Heat the material slowly and uniformly to a temperature of 1202 - 1292°F (650 - 700°C) and hold at that temperature for 1 hour per inch (25.4 mm) of thickness, but a minimum of 2 hours. Cool slowly in the furnace by 50°F (10°C) per hour to 1000°F (538°C), then continue cooling in air.
For improved machinability, cool slowly in the furnace to a temperature of 1250°F (677°C) and hold at that temperature for 8 hours, then cool it to room temperature in air.
Normalizing the L6 can benefit its machinability, mechanical properties and reduce internal stresses as the process gives it a finer and more uniform pearlitic grain structure.
Heat the work pieces uniformly to a temperature range of 1050 - 1250°F (566 - 677°C) and soak for 2 hours. Finish this process off by cooling the parts down in the furnace to 900°F (482°C) and then to ambient temperature in air.
Preheat the parts uniformly to a temperature of 1250 - 1350°F (677 - 732°C), then continue to an austenitizing temperature of 1500 - 1550 (816 - 843°C) and hold for 10-30 minutes at this temperature.
To protect the material from excessive scale or decarburization either heat the parts in neutral salt, pack it in cast-iron chips or spend coke or heat in a protective atmosphere or vacuum furnace.
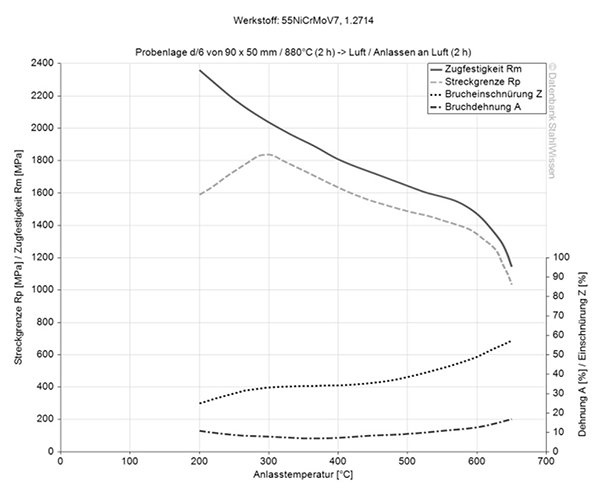
Oil, warmed – parts should be cooled down to 120 - 150°F (49 - 66°C) or until it can be held by hand and then tempered immediately.
Air – this method of quenching is done for tools with less than 1 inch (25.4 mm) sections. Air quenching is the safer option for intricate sections as air quenching compared to oil quenching will distort parts less.
To avoid cracking, temper L6 immediately after quenching. Hold at the chosen tempering temperature for 1 hour per inch (25.4 mm) of thickness, but for at least 4 hours and cool to room temperature. L6 can be tempered at a temperature range of 450 - 800°F (232 - 427°C) without getting brittle. To minimize internal stresses for parts with a greater cross section than 6 inches (152.4 mm) and/or to improve stability in tools being EDMed after the heat treatment, it is recommended to soak the material for 8 - 10 hours.
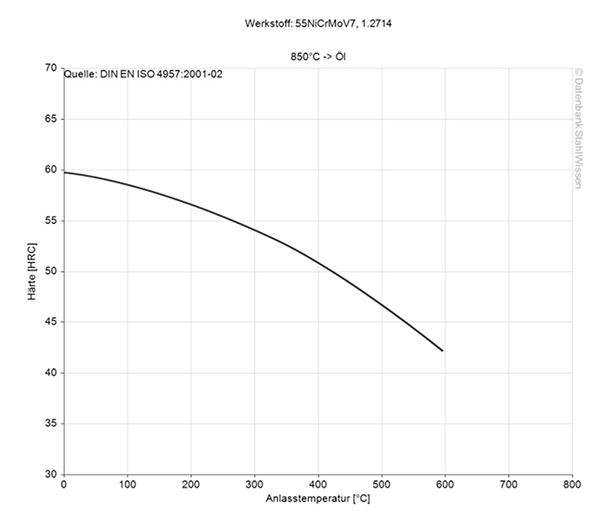
Sub-zero treatment can be done as an extension of a quench from the austenitizing treatment and before tempering.
Sub-zero treatment can improve the hardness of the L6, increase its wear resistance and stability, improve toughness, all of which are advantages that can give tools a longer service life. However duration of treatment and cooling rate have to be taken in consideration when deciding if sub-zero treatment is beneficial for this material grade.
To avoid cracking, temper L6 immediately after quenching. Hold at the chosen tempering temperature for 1 hour per inch (25.4 mm) of thickness, but for at least 4 hours and cool to room temperature. L6 can be tempered at a temperature range of 450 - 800°F (232 - 427°C) without getting brittle. To minimize internal stresses for parts with a greater cross section than 6 inches (152.4 mm) and/or to improve stability in tools being EDMed after the heat treatment, it is recommended to soak the material for 8 - 10 hours.
This diagram shows the micro changes at different temperatures which are important during heat treatment. They show the optimum condition for the hardening, annealing and normalizing process.
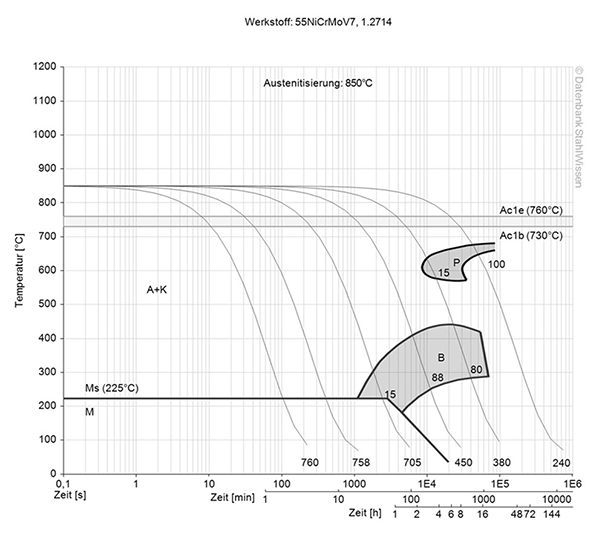
This diagram shows the structural changes at micro level over time at a constant temperature. It shows at what temperature and after what time different phases, e.g., perlite, martensite or bainite start to build.
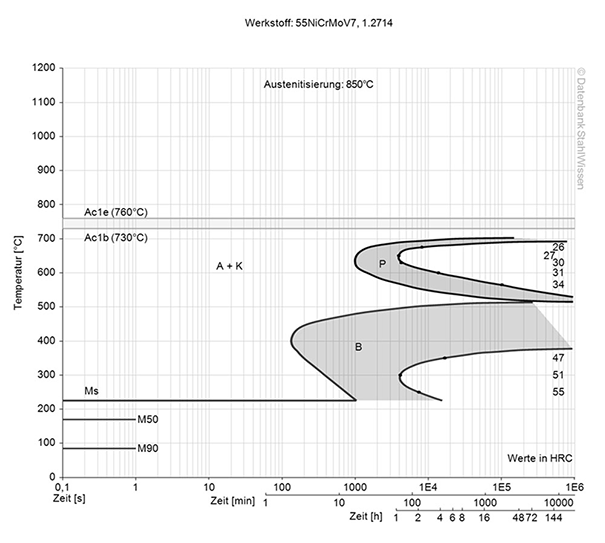

L6 SURFACE TREATMENT
Nitriding introduces nitrogen into the surface to increase the surface hardness and improve the corrosion resistance. As a low temperature procedure the possibility of distortion is low. When the process is not done correctly it can leave the material brittle.
This process introduces carbon into the surface to enhance wear resistance and surface hardness. As a high temperature process care has to be taken as this might change the overall material properties and the material might distort.
Black oxide coating is often used for aesthetic purposes as it provides a black-blue finishing touch that is often used for tools and firearms as it will reduce light reflecting off the surface.
Physical Vapor Deposition (PVD) as well as Chemical Vapor Deposition (CVD) deposit a thin layer on the material surface which can enhance wear resistance and reduce friction.
Shot peening is an impact treatment where multiple high velocity shots are blasted onto the material surface leaving small indentations which replace the tensile stress on the surface with a compressive layer. It solidifies the material and makes the surface more resistant which can prevent fatigue and can optimize the form and weight of the parts.
Note: Protective gear like goggles, masks, helmets, gloves and protective clothing should be worn and adequate ventilation or dust extraction should be provided.
Appropriate guards to prevent shot spillage should be in place, equipment regularly maintained and shot should be free from contaminants.

L6 PROCESSING
With good electrical conductivity and hardness the L6 can be EDMed, it is often used to achieve tight tolerances or cut intricate details out of hardened material.
Steel in general and in this case the L6 may undergo volume changes when it changes from one phase to another. Heating and cooling the material may also lead to dimensional changes and if done unevenly may even lead to distortion. To prevent the former it may be advantageous to preheat parts, heat parts slowly to temperature, make sure to use the right quenching method and medium or use protected atmospheres.
Heat the workpiece slowly and uniformly to a temperature of 1800 - 1900°F (982 - 1038°C). Do not let the temperature drop below 1600°F (871°C) and reheat the material as often as needed. After the forging process is done slowly cool the parts in lime, dry ash or in the furnace.
L6 is generally weldable. Weld preparation, like a grease and dirt free surface and a rust and paint free surface, is important and the first step when welding. To avoid cracking, excessive hardening and loss of properties the material should be preheated slowly, fillers similar to the base material can be used and the weld process should be chosen in accordance with specific requirements of application needed.
Overheating can lead to grain growth which in turn can weaken the weld and can be avoided with the right combination of current, voltage and travel speed. To relieve stresses from welding a post weld temper can be beneficial.

L6 APPLICATION OPTIONS
L6 tool steel can withstand sudden stresses and impacts, has a good toughness and wear resistance as well as a reasonable hardness. These properties lend themselves to applications like knives and blades, cold work tools, bearings, bushings, woodwork tools, spindles, cams, and springs.
• Forging dies
• Slides
• Punch heads
• Extruding stamps
• Press tools
• Hot shear knives
• Extrusion press tools
• Support tools
• Pressure plates
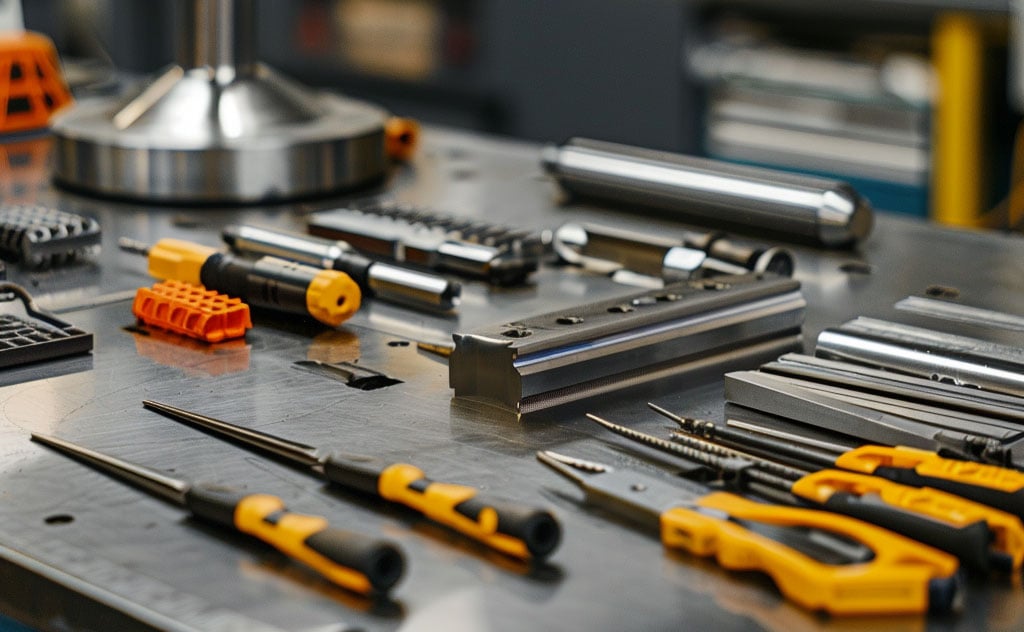

L6 CONCLUSION
L6 tool steel has a unique blend of properties, its high carbon content makes it a good choice for applications needing a high wear resistance. Its exceptional toughness gives the L6 a resistance to impacts and makes it less prone to chipping and breaking.
Possible corrosion should be managed and should be considered when choosing the L6 as well as the correct heat treatment needs to be chosen as many of the properties of the L6 may be affected when not heat treated correctly.
Practically, this means:
- High carbon content
- For applications that require high wear resistance
- Exceptional toughness makes it impact resistant
- Less susceptible to chipping and cracking
- High tempering resistance
- Good through hardenability
- Can be nitrided and eroded
- Working hardness is in the range of 40 - 54 HRC
- High compressive strength
- Water coolable
- High impact strength
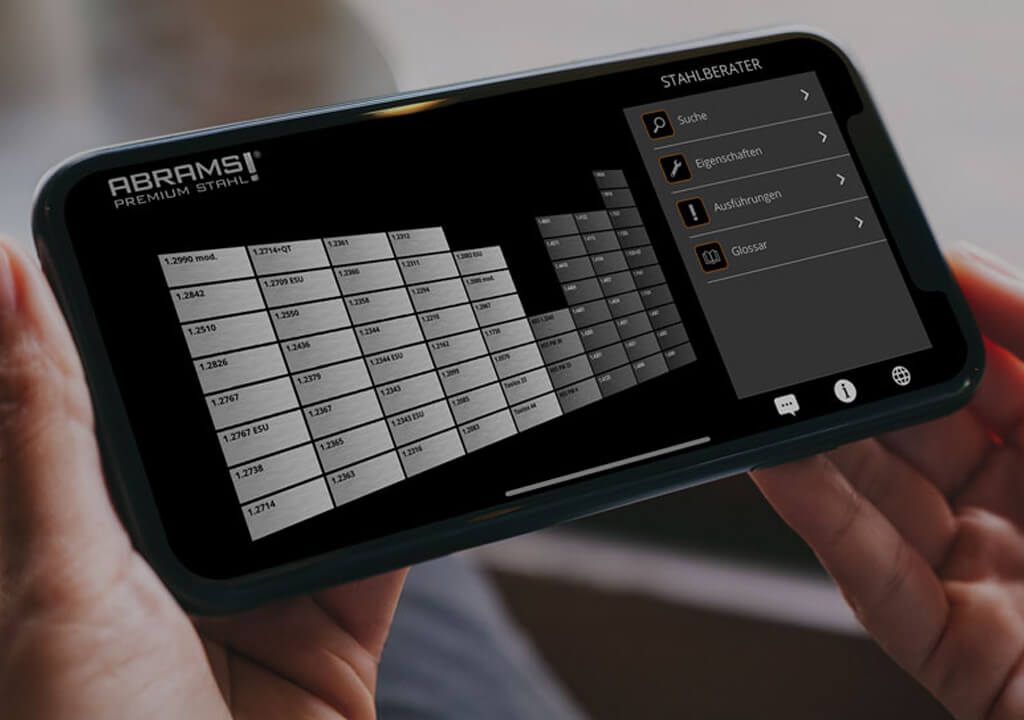

L6 ALTERNATIVES
Are you looking for an alternative steel grade?
WE HAVE THE SOLUTION!
With the ABRAMS STEEL GUIDE, you can obtain an alternative or equivalent steel grade with just a few clicks.

L6 DATASHEET
Download the technical data sheet in PDF format here.
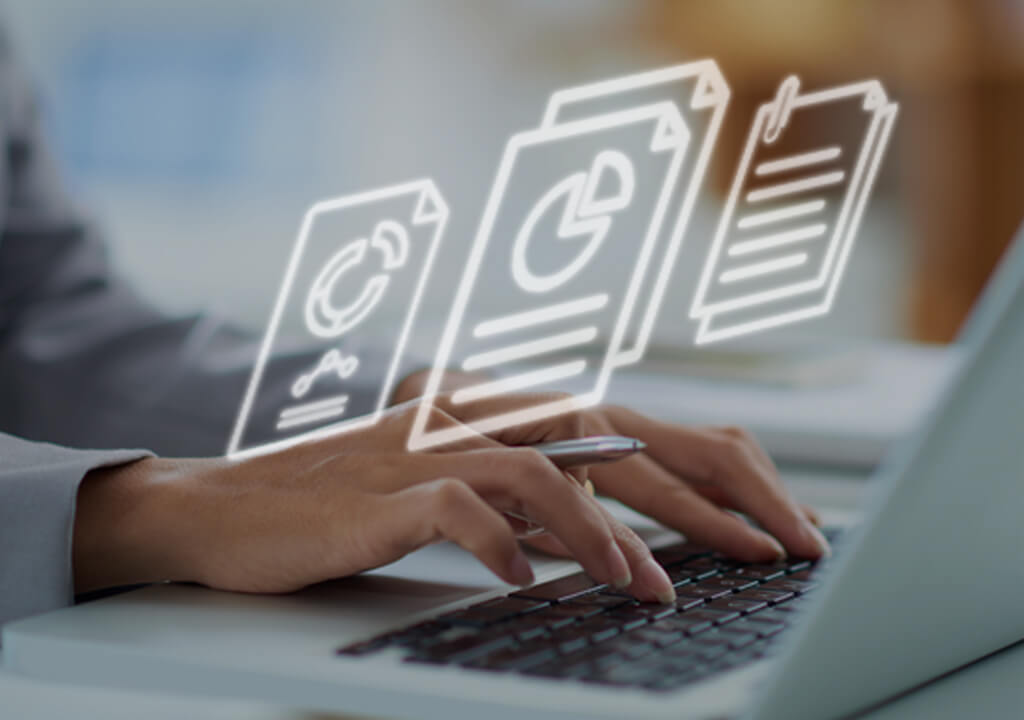
The data shown here has been compiled with the greatest diligence and is regularly updated with regard to the correctness and completeness of its content. The content is indicative only and should not be taken as a warranty of specific properties of the product described or a warranty of suitability for a particular purpose. All information presented is given in good faith and no liability will be accepted for actions taken by third parties in reliance on this information. ABRAMS Industries reserves the right to change or amend the information given here in full or parts without prior notice.