Plastic Mold Steel - Choose the right one!
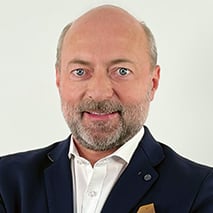
Written by Dr. Juergen Abrams on August 13, 2024.
THE REQUIRED PROPERTIES OF PLASTIC MOLD STEEL
Mold steels are used in industrial production for the manufacture of molds and tools. They can be utilized for injection molding, die casting, blow molding, and other manufacturing processes.
Due to various requirements, mold steel must possess a range of important properties. This ensures that the molds produced have a long lifespan, fulfill their function and deliver high-quality end products.
Plastic mold steel is a combination of hardness, toughness, wear resistance, corrosion resistance, thermal conductivity, polishability, dimensional stability and form stability.
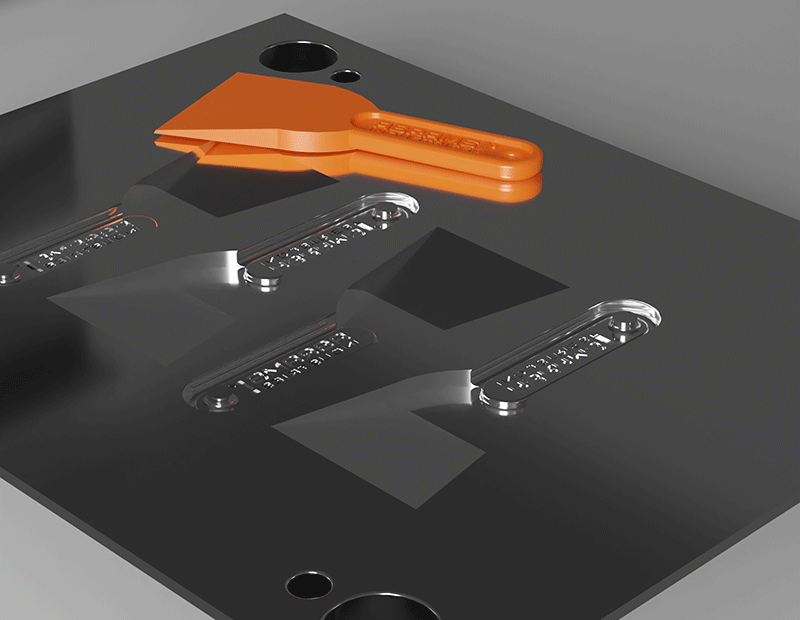
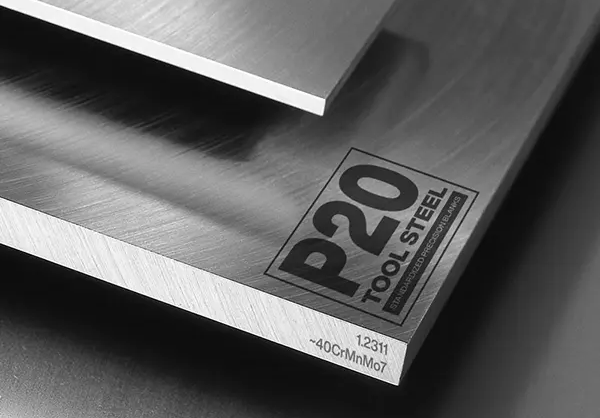
Since the molds produced in mold making are often used thousands of times, the hardness of the plastic mold steel is very important. It is associated with wear resistance. High hardness ensures that a mold can be used for a long time without deforming or wearing out.
Mold steel must be impact-resistant and shock-resistant to withstand sudden loads. Therefore, in addition to hardness, toughness also plays an important role. Good toughness prevents the mold from breaking or chipping during use.
The wear resistance of plastic molds is a crucial factor in production. They are subjected to mechanical stresses during each production cycle. Therefore, the steel used must meet high standards. High wear resistance means that the surface of the steel remains smooth for a long time, ensuring consistent quality of the produced parts.
Plastic molds are often in contact with corrosive materials or humid environments. Therefore, a certain level of corrosion resistance is important. This prevents rust formation and other corrosion damage that could shorten the mold's lifespan.
Good thermal conductivity is especially important in thermal processes like injection molding. The mold needs to be evenly tempered during the injection and cooling of the plastic melt. Good thermal conductivity ensures that heat is distributed quickly and evenly.
As mentioned earlier, an extremely smooth surface is important and a quality feature for plastic molds. This is where the polishability of the steel used comes into play. Good polishability in mold manufacturing ultimately ensures a high-quality surface finish. This, in turn, guarantees precise and high-quality end products.
Mold steel must not warp or shrink during mold manufacturing and later use. Therefore, dimensional stability and form stability are essential. These properties of plastic mold steel ensure that the produced parts meet exact specifications and tolerances.
COMMON GRADES OF MOLD STEEL
There are many grades of plastic mold steels, each with specific
properties that make them particularly suitable for certain applications.
Common steel grades include P20, P20 PH, P20+Ni, H13, and 420 stainless steel.
PLASTIC MOLD STEEL CHART
The listed table shows the plastic mold steels in our portfolio. For each application, we offer the suitable type of plastic mold steel.
If you require other grades of steel, please feel free to contact us.
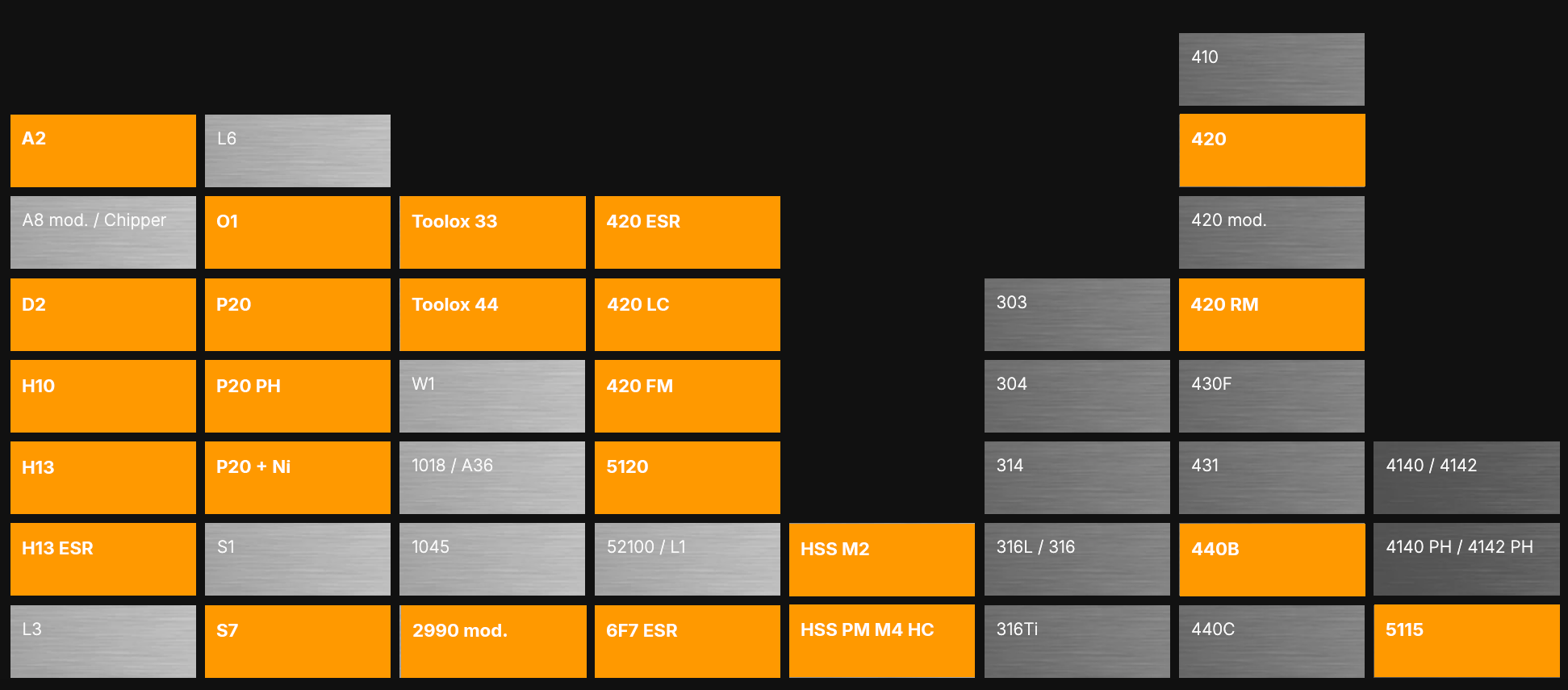
Mold steel grades | Steel types | Properties | |
AISI / SAE A2 | • Tool steel | • X100CrMoV5 • High wear resistance • Tensile strength (on delivery): 118.2 KSI • Cold work steel | |
AISI / SAE D2 | • Tool steel | • X153CrMoV12 • Excellent wear resistance • Good toughness • Tensile strength on delivery: 124.7 KSI • Working temperature: 68 – 392 °F | |
AISI / SAE H10 | • Tool steel | • 32CrMoV12-28 • High toughness • Hot work steel • Working temperature: 68 – 842 °F | |
AISI / SAE H13 | • Tool steel | • X40CrMoV5-1 • Excellent heat resistance • High wear resistance • Good toughness • Tensile strength on delivery: 111.6 KSI • Hot work steel • Working temperature: 68 – 932 °F | |
AISI / SAE H13 ESR | • Tool steel • Plastic mold steel | • X40CrMoV5-1 • Excellent heat resistance • Excellent wear resistance • Good toughness • Tensile strength on delivery: 111.6 KSI • Hot work steel • Working temperature: 68 – 932 °F | |
AISI / SAE O1 | • Tool steel | • 100MnCrW4 • High degree of dimensional stability • Good toughness • Full hardenability • Tensile strength on delivery: 111.6 KSI • Cold work steel • Working temperature: 68 – 392 °F | |
AISI / SAE P20 | • Tool steel | • ~40CrMnMo7 • Good polishability • Good etchability • High through-hardenability • Tensile strength on delivery: 108.8 KSI • Cold work steel • Working temperature: 68 – 392 °F | |
AISI / SAE P20 PH | • Tool steel | • Optimized AISI P20 • Good polishability • Good etchability • High through-hardenability • Uniform component strength • Tensile strength on delivery: 159.5 KSI • Cold work steel • Working temperature: 68 – 392 °F | |
AISI / SAE P20 + Ni | • Tool steel | • Optimized AISI P20 • ~40CrMnNiMo8-6-4 • Better through-hardenability • Low sulphur steel • Polishable • Grainable • Tensile strength on delivery: 159.5 KSI • Cold work steel • Working temperature: 68 – 572 °F | |
AISI / SAE S7 | • Tool steel | • 50CrMoV13-1 • High impact resistance • High shock resistance • Good resistance to softening • Tensile strength on delivery: 110.2 KSI • Hot work steel • Working temperature: 302 – 752 °F | |
AISI / SAE Toolox 33 | • Tool steel | • Toolox33 • Quenched and tempered • High toughness • Low residual stresses • Tensile strength on delivery: 163.1 KSI • Cold work steel • Working temperature: 68 – 1094 °F | |
AISI / SAE Toolox 44 | • Tool steel | • Toolox44 • Quenched and tempered • High impact toughness • Good dimensional stability • Tensile strength on delivery: 205.9 KSI • Cold work steel • Working temperature: 68 – 1094 °F | |
AISI / SAE 2990 modified | • Tool steel | • X100CrMoV8-2 • High toughness • Good dimensional stability • Tensile strength on delivery: 123.2 KSI • Cold work steel • Working temperature: 68 – 932 °F | |
AISI / SAE 420 ESR | • Tool steel | • X40Cr14 • Good hardenability • Excellent polishing properties • Tensile strength on delivery: 118.2 KSI • Working temperature: 68 – 392 °F | |
AISI / SAE 420 LC | • Tool steel | • ~X5CrS12 • Pre-hardened • Resistant to aggressive plastics • Resistant to humid conditions • Tensile strength on delivery: 163.1 KSI • Working temperature: 68 – 212 °F | |
AISI / SAE 420 FM | • Tool steel | • X33CrS16 • Pre-hardened • Corrosion resistant • Resistant to aggressive plastics • Resistant to humid conditions • Tensile strength on delivery: 163.1 KSI • Working temperature: 68 – 572 °F | |
AISI / SAE 5120 | • Tool steel | • 20MnCr5 • High surface hardness • High core toughness • Excellent machinability • Good polishing properties • Tensile strength on delivery: 104.4 KSI • Cold work steel • Working temperature: 68 – 392 °F | |
AISI / SAE 6F7 ESR | • Tool steel | • 45NiCrMo16 • High toughness • Good through-hardenability • High impact strength • Tensile strength on delivery: 127.6 KSI • Focus on cold work • Working temperature: 68 – 572 °F | |
AISI / SAE M2 | • High speed steel | • HS6-5-2C • High impact toughness • Good compression strength • Excellent wear resistance • Tensile strength on delivery: 133.4 KSI • Hot & Cold work steel • Working temperature: 68 – 1022 °F | |
AISI / SAE M4 | • High speed steel | • ~PMHS6-5-4 • Based on powder metallurgy • Tensile strength on delivery: 133.4 KSI • Hot & Cold work steel • Working temperature: 68 – 932 °F | |
AISI / SAE 420 | • Stainless steel | • X46Cr13 • Good machining properties • Low distortion through-hardening steel • Full hardenability • High wear resistance • Conditionally acid resistant • Tensile strength on delivery: 118.2 KSI • Cold work steel • Working temperature: 68 – 392 °F | |
AISI / SAE 420 RM | • Stainless steel | • X39CrMo17-1 • Good polishing properties • Good heat resistance • Good wear resistance • Tensile strength on delivery: 159.5 KSI • Working temperature: 68 – 392 °F | |
AISI / SAE 440B | • Stainless steel | • X90CrMoV18 • Corrosion resistant • High hardness • High gloss polishable • Tensile strength on delivery: 134.1 KSI • Cold work steel • Working temperature: 68 – 752 °F | |
AISI / SAE 5115 | • Case hardening steel | • 16MnCr5 • High surface hardness • Excellent machinability • Good polishing properties • Tensile strength on delivery: 104.4 KSI • Cold work steel • Working temperature: 68 – 392 °F |
HOW HARD IS MOLD STEEL?
Are you asking yourself how high the hardness of mould steel is? The working hardness of mold steel ranges from 277 to 711 BHN. Each type of steel has different properties and a specific hardness. The individual values are listed in the table.
Molding steel | Range of Hardness (Brinell Hardness Number) |
AISI / SAE A2 | 601 - 658 BHN |
AISI / SAE D2 | 592 – 658 BHN |
AISI / SAE H10 | 469 - 504 BHN |
AISI / SAE H13 | 469 - 572 BHN |
AISI / SAE H13 ESR | 469 - 572 BHN |
AISI / SAE O1 | 592 - 658 BHN |
AISI / SAE P20 | 300 - 469 BHN |
AISI / SAE P20 PH | 300 - 469 BHN |
AISI / SAE P20 + Ni | 300 - 469 BHN (delivery condition, quenched and tempered) |
AISI / SAE S7 | 572 - 627 BHN |
AISI / SAE Toolox 33 | 277 - 331 BHN (on delivery, without nitriding) |
AISI / SAE Toolox 44 | 419 BHN (on delivery) |
AISI / SAE 2990 mod. | 592 - 681 BHN |
AISI / SAE 420 ESR | 469 - 552 BHN |
AISI / SAE 420 LC | approx. 308 BHN (on delivery) |
AISI / SAE 420 FM | approx. 308 - 456 BHN (on delivery) |
AISI / SAE 5120 | 601 - 627 BHN |
AISI / SAE 6F7 ESR | 469 - 534 BHN |
AISI / SAE M2 | 658 - 711 BHN |
AISI / SAE M4 | 658 - 711 BHN |
AISI / SAE 420 | 469 - 552 BHN |
AISI / SAE 420 RM | 277 - 456 BHN |
AISI / SAE 440B | approx. 513 - 601 BHN |
AISI / SAE 5115 | 601 - 627 BHN (on the surface) |
VARIOUS TYPES OF STEEL FOR MOLD MAKING
Mold making plays a crucial role in the production of plastic parts. Key industries include the automotive industry, medical technology, electronics, and consumer goods.
The success of these industries largely depends on the quality and precision of the tools and molds used. The right steel is essential in this context. To meet the specific requirements and challenges of plastic injection molding, various grades or types of steel are used.
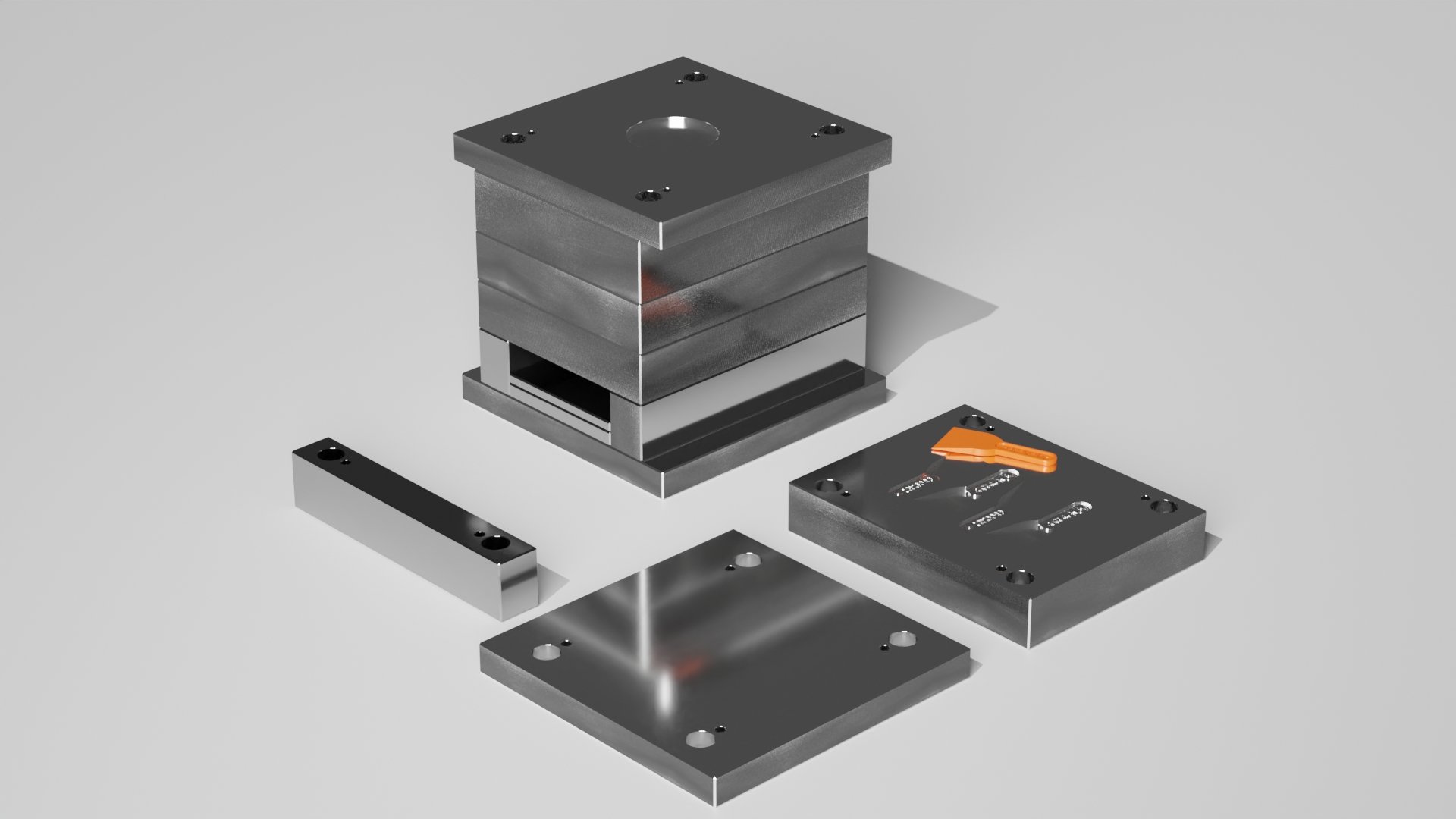
Tool steels such as P20 and H13 are commonly used in mold making. They can produce durable and precise tool steel molds. Plastic mold tool steel offers a balanced ratio of hardness, toughness, and wear resistance.
Therefore, they are ideal for manufacturing molds that are subjected to high mechanical stresses. Typical applications include injection molds for large plastic parts like automotive components and housings for household appliances.
Stainless steels like 420 are particularly popular in mold making due to the corrosion resistance, high-quality, and smooth surface they offer. They are also ideal for environments where the molds are exposed to moisture or corrosive chemicals.
Stainless steel molds can be polished to a mirror finish, making them indispensable for applications where surface quality is critical to the end product, such as medical technology and optical components.
HSS mold steels offer excellent wear resistance and hardness. HSS has high creep resistance and can withstand a continuous operating temperature of up to 1022 °F. This operating temperature is unique and sets it apart from cold work steel and hot work steel.
Therefore, they are ideal for extremely high temperatures and speeds. In mold making, HSS mold steel is often used for inserts in molds needed for processing hard plastics and high-speed production operations.
Case-hardening steels like 5115 (16MnCr5) feature a combination of a hard, wear-resistant surface and a tough core. These steels are surface-hardened to create a hard layer that protects the plastic mold from wear. The tough core makes them resistant to mechanical stresses.
This type of steel is commonly used for making mold inserts and cores that are subjected to high mechanical and thermal loads.
Tool steels such as P20 and H13 are commonly used in mold making. They can produce durable and precise tool steel molds. Plastic mold tool steel offers a balanced ratio of hardness, toughness, and wear resistance.
Therefore, they are ideal for manufacturing molds that are subjected to high mechanical stresses. Typical applications include injection molds for large plastic parts like automotive components and housings for household appliances.
Stainless steels like 420 are particularly popular in mold making due to the corrosion resistance, high-quality, and smooth surface they offer. They are also ideal for environments where the molds are exposed to moisture or corrosive chemicals.
Stainless steel molds can be polished to a mirror finish, making them indispensable for applications where surface quality is critical to the end product, such as medical technology and optical components.
HSS mold steels offer excellent wear resistance and hardness. HSS has high creep resistance and can withstand a continuous operating temperature of up to 1022 °F. This operating temperature is unique and sets it apart from cold work steel and hot work steel.
Therefore, they are ideal for extremely high temperatures and speeds. In mold making, HSS mold steel is often used for inserts in molds needed for processing hard plastics and high-speed production operations.
Case-hardening steels like 5115 (16MnCr5) feature a combination of a hard, wear-resistant surface and a tough core. These steels are surface-hardened to create a hard layer that protects the plastic mold from wear. The tough core makes them resistant to mechanical stresses.
This type of steel is commonly used for making mold inserts and cores that are subjected to high mechanical and thermal loads.
HOW TO SELECT THE RIGHT MOLD STEEL FOR MOLDING
As outlined above, there are many different types of plastic mold steels. Choosing the right mold steel depends on various factors. Quality, durability, and the cost of the steel are crucial considerations.
The following questions can help you select the right mold steel:
1. What type of casting process is being used?
2. What mechanical requirements are needed?
3. What thermal requirements are necessary?
4. What level of chemical resistance must the steel have?
5. Is machinability a critical factor?
6. What surface finish requirements are there?
7. Cost-effectiveness – How much can the steel cost?
The choice of the optimal plastic mold steel, therefore, involves carefully weighing these factors. Often, specific experience from steel manufacturers or toolmakers can be helpful in making the selection.
If you can’t find the right steel immediately or have questions, feel free to contact us. Our experienced team is always here to assist you.
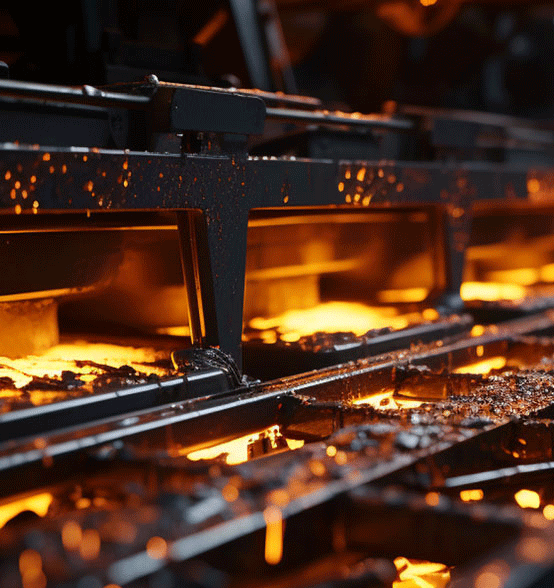
SUMMARY
Mold steel is the generic term for steels which, due to their properties, are used for plastics processing and machining as well as for cold or hot working applications.
Mold steels have to fulfill a great variety of properties. Therefore they can be found amongst tool steel, high speed steel, stainless resistant steel as well as case hardening steel.
The properties below are an overview of properties mold steels should have to guarantee a perfectly finished end product.
• Dimensional stability
• Corrosion resistant
• High wear resistant
• High thermal conductivity
• High polishable
• Good toughness
• Long service life
• Shock resistant
• Impact resistant
ABRAMS INDUSTRIES® PLASTIC MOLD STEEL
As a steel supplier with no minimum order quantity or value we have been supplying steel to a wide variety of industries and manufacturers in Germany since 2003, Europe since 2011 and now since 2020 across the U.S.A. and Canada.
We pride ourselves in supplying you with precision in tool steel, high speed steel, stainless steel, heat-treatable steel and case hardening steel in 44 steel grades with 83,928 dimensions.
As a mold steel supplier we saw, mill and grind for you in our Warehouse in Illinois.
Customized plastic mold steel
Mold steel plates
Mold steel rods
ABRAMS INDUSTRIES® INC. - YOUR STEEL PARTNER
Your success is our success!