304 Stainless Steel - DIN 1.4301 - X5CrNi18-10 - ~SUS 304
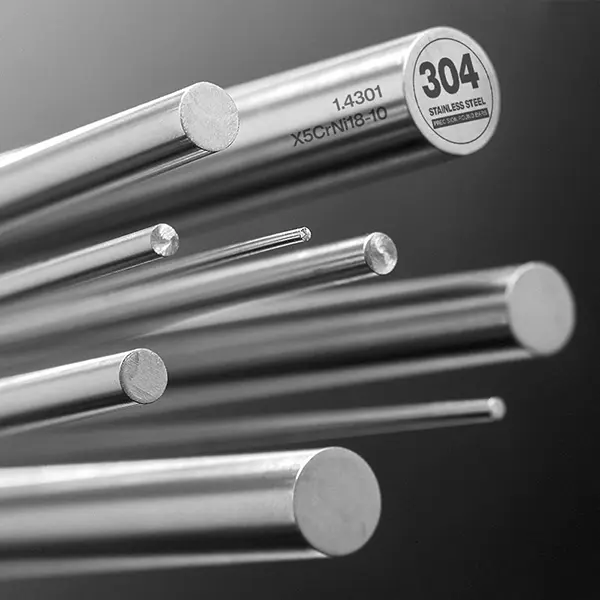
304 Stainless Steel - DIN 1.4301 - X5CrNi18-10 - ~SUS 304
Back to Steel OverviewGround Flat Stock and $mart Flat Stock comes always in a machined condition, that means:
NO decarburization on the surfaces (decarburization leads to unreliable components and tools)
Less dirt on your machines during further processing – nothing but clean chips
Stress-relieved flat steel avoids warping of components during further machining
Get the close-to-finish-size thickness and width you need for the components you plan
Ground Flat Stock and $mart Flat Stock comes always in a machined condition, that means:
NO decaburization on the surfaces (decarburization leads to unreliable components and tools)
Less dirt on your machines during further processing – nothing but clean chips
Stress-relieved flat steel avoids warping of components during further machining
Get the close-to-finish-size thickness and width you need for the components you plan
Ground Flat Stock and $mart Flat Stock comes always in a machined condition, that means:
NO decaburization on the surfaces (decarburization leads to unreliable components and tools)
Less dirt on your machines during further processing – nothing but clean chips
Stress-relieved flat steel avoids warping of components during further machining
Get the close-to-finish-size thickness and width you need for the components you plan

304 STANDARD VALUES
C
Si
Mn
P
S
Cr
Ni
N
X5CrNi18-10
195 BHN - 215 BHN (delivery condition)
max. 215 HB
X5CrNi18-10
195 BHN - 215 BHN (delivery condition)
max. 215 HB
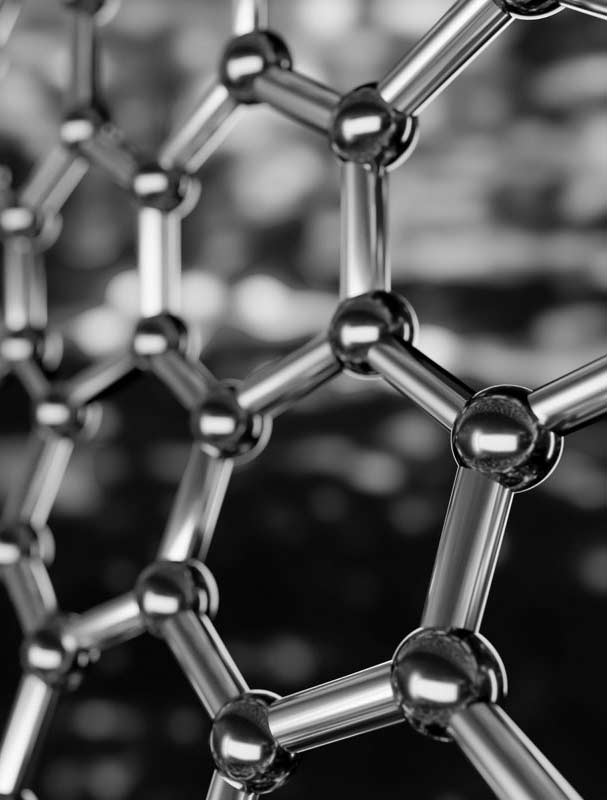

304 PHYSICAL PROPERTIES
The 304 stainless steel is an austenitic steel which is also known as the 18/8 due to its 18% chromium and 8% nickel composition. It has good workability, weldability, heat resistance, strength and good mechanical properties at low temperatures, good hot workability for such as stamping and bending.
The combination of low yield strength and high elongation benefits manufacturing parts such as sinks and saucepans or hollow ware. 304 stainless steel is easily molded or rolled into a multitude of forms for industrial, architectural and transportation applications.
With an 18% content of chromium, the 304 forms a protective chromium oxide layer. This layer is passive and non-reactive and seals and protects the iron below it from external influences. When scratched or damaged the oxide layer is able to “heal” itself providing there is enough oxygen available.
This process of renewal makes stainless steel resistant to rusting compared to regular steel. The 8% nickel enhances the overall corrosion resistance and contributes to the formability as well as its polished and bright appearance.
304 has excellent corrosion resistance in many environments and when in contact with different corrosive media. The formation of chromium carbides on the grain boundaries and the resulting chromium depletion in the surrounding areas makes the 304 susceptible to intergranular corrosion. 304 exhibits good corrosion resistance in natural environmental media in the absence of chlorine and salt concentrations.
In general, 304 stainless steel can be used in environments with gasses though the composition, concentration, temperature, pressure and other factors should be taken in consideration before exposing this steel grade to them. Where the 304 performs well in an oxidizing atmosphere it does not perform as well in a reducing atmosphere for example.
Therefore the corrosion resistance of the 304 in gaseous environments depends on the specific gas as well as the conditions to which the steel is exposed.
When in contact with chloride solutions or oxidizing media, pitting resistance is important as those conditions may facilitate the penetration of the passive surface film in places. A single deep point of entry may cause more damage than many shallow ones.
Intergranular corrosion is the result due to the precipitation of chromium carbides at the grain boundaries when cooled after welding at the sensitizing temperature range of 840-1560°F (450-850°C). Therefore, sensitized materials should not be exposed to corrosive environments as intergranular corrosion may occur at the welding point.
304 performs well in urban and rural areas. In industrial environments with high concentration of industrial pollutants e.g., sulphur or in a marine environment with a high concentration of salt the corrosion resistance of the 304 can be compromised.
Regular maintenance as well as a polished or smooth surface can make it harder for any contaminants to adhere to the material. If the material has to withstand more aggressive environments an additional protective layer or a different material grade should be considered.
Austenitic steels are prone to stress corrosion cracking, as can be encountered at temperatures above 140°F (60°C) when the steel is exposed to tensile stresses or comes into contact with solutions containing chlorides at the same time for example.
As the 304 has a protective chromium oxide layer it prevents further penetration of oxygen and protects the steel under this layer from corrosion. While resistant to oxidation in ambient temperatures, exposure to continuous high temperatures can lead to heavy scale formation and may result in a reduction of mechanical properties due to grain growth.
At temperatures above 1560°F (850°C) the 304 might experience sensitization which makes the steel susceptible to intergranular corrosion. To restore the appearance of the 304 if it has oxidized in high temperatures it can be pickled or electropolished to remove oxide scaling.
As an austenitic steel the 304 is not magnetizable.
The wear resistance of the AISI 304 stainless steel is a 1 on a scale where 1 is low and 6 is high.

304 TECHNICAL PROPERTIES
The 304 is not usually used for knife making as it has poor edge retention due to the low carbon content and is difficult to sharpen.
Typically the density of the 304 is 0.285 lb/in3 (7.8g/cm3) at room temperature.
The working hardness for 304 steel is in the range of 195 - 215 BHN (50 - 56 HRC).
The 304 has a tensile strength of approx. 100.0 KSI on delivery (0.145 KSI = 1MPa). In order to reach this value, a tensile test is performed to show how much force is needed to stretch or elongate a sample before it breaks.
The heat conductivity for the 304 is at 15 W/(m*K) (8.667 BTU/(h-ft*°F)) at room temperature.
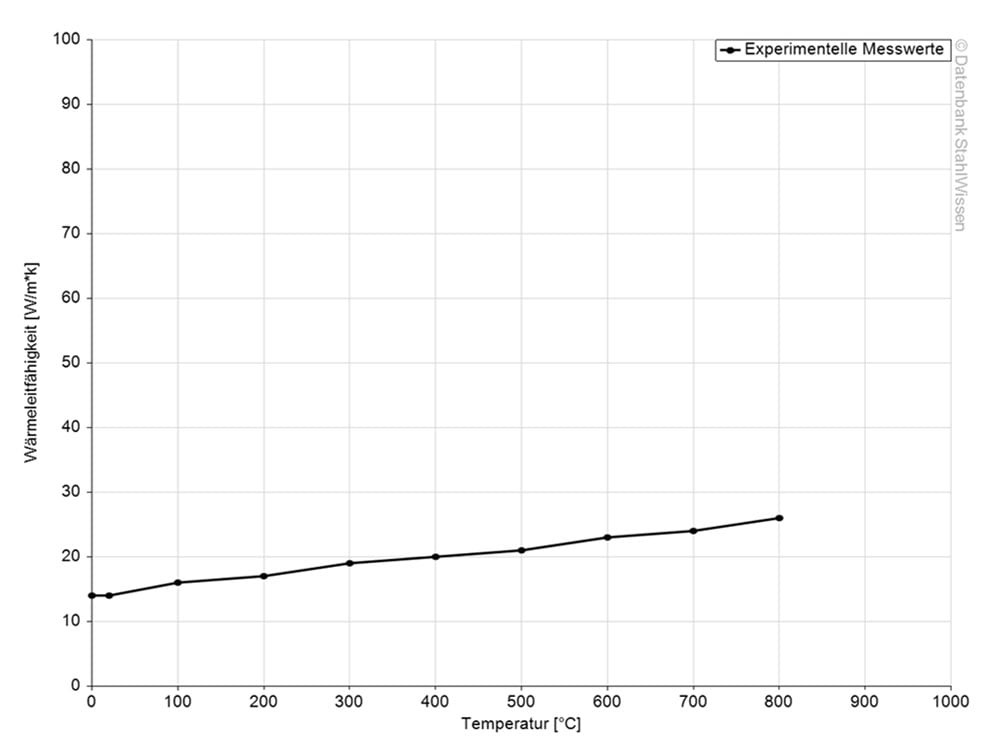
304 steel has good oxidation resistance in intermittent service to 1598°F (870°C) and in continuous service to 1697°F (925°C). Not recommended is continuous use in the range of 797-1580°F (425-860°C) if aqueous corrosion resistance is important later on.
The following table shows expansion or contraction at various temperatures, which may be very important for high temperature works or when working with high temperature changes.
Medium thermal expansion coefficient | |
10-6m/(m • K) | At a temperature of |
16.1 | 68°F |
16.7 | 68 - 212°F |
17.2 | 68 - 392°F |
17.7 | 68 - 572°F |
18.1 | 68 - 752°F |
18.4 | 68 - 932°F |
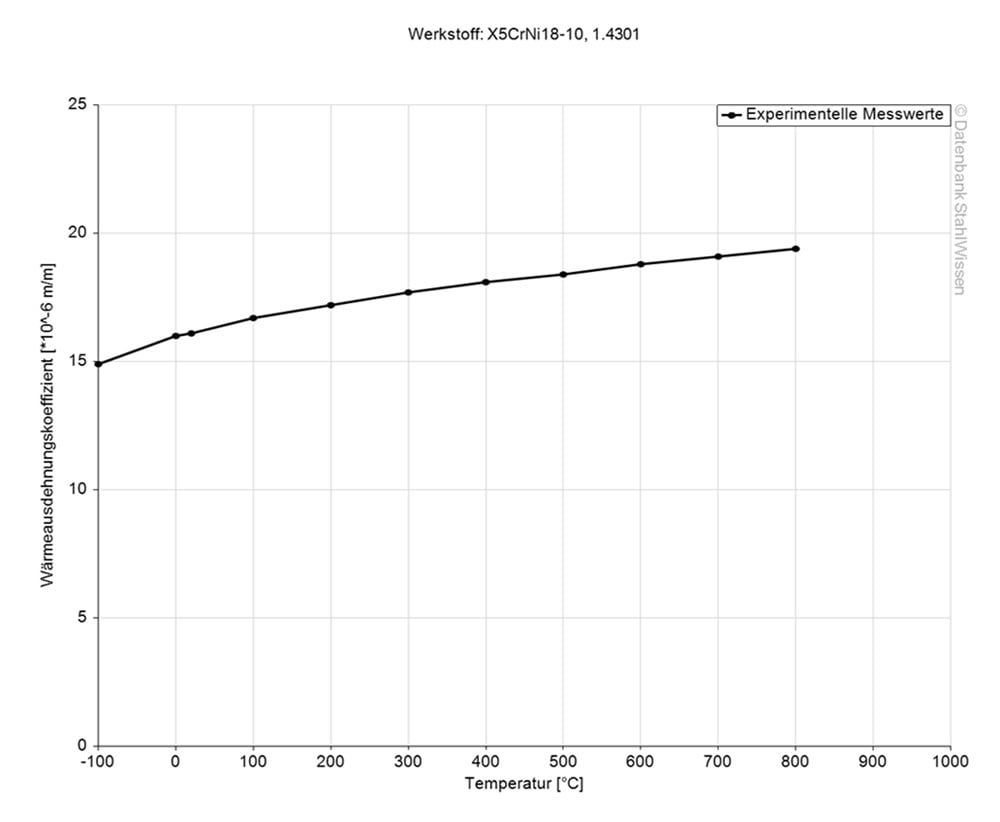
The specific heat capacity of the 304 is at room temperature at 0.5J/g-°C (0.119BTU/lb-°F) This value shows how much heat is needed to heat 1lb of material by 1 Fahrenheit.
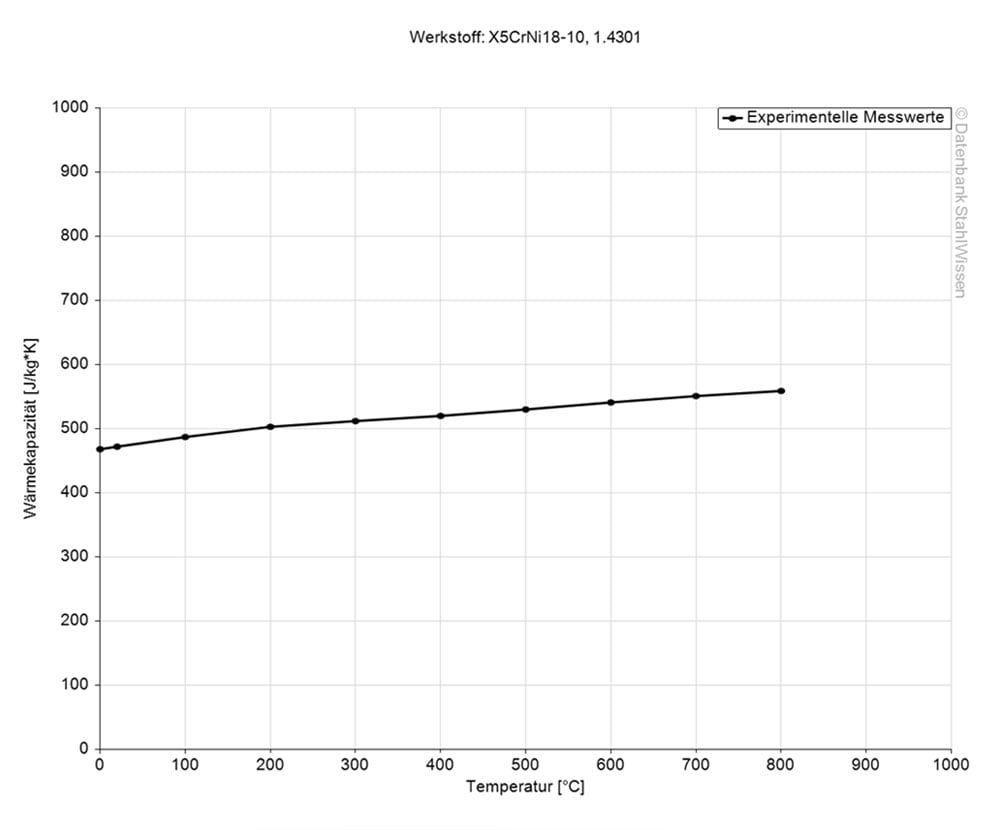
You can find the temperature dependent material constant (Resistivity) in the following table. The electrical conductivity is the reciprocal value of the specific resistance.
Table of the specific electrical resistivity | |
Value | At a temperature of |
~ 0.692 (Ohm*mm²)/m | ~ 68°F |
~ 0.758 (Ohm*mm²)/m | ~ 212°F |
~ 0.836 (Ohm*mm²)/m | ~ 392°F |
~ 0.907 (Ohm*mm²)/m | ~ 572°F |
~ 0.973 (Ohm*mm²)/m | ~ 752°F |
~ 1.02 (Ohm*mm²)/m | ~ 932°F |
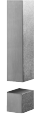
STAINLESS STEEL!
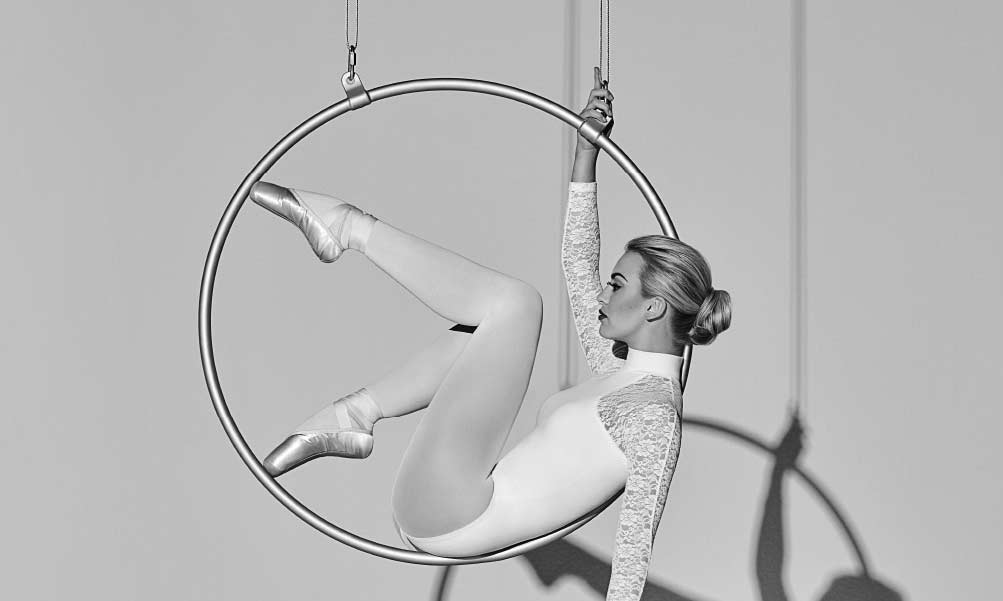
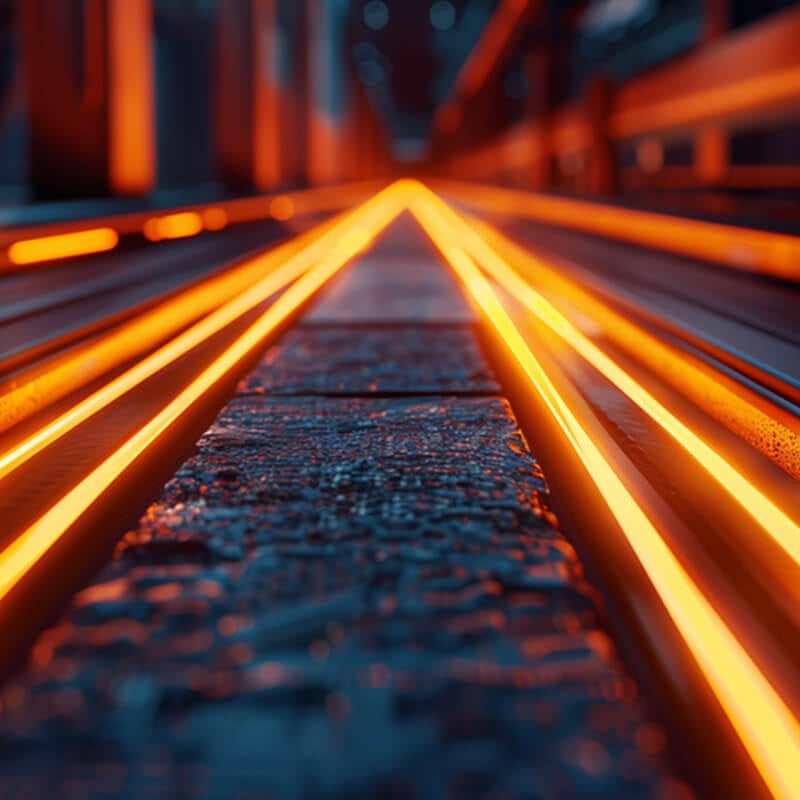

304 PROCEDURE
Unlike martensitic steel, 304 stainless steel cannot be hardened by heat treatment as no phase changes occur on heating and cooling.
Heat the protected steel through to 1630°F (890°C) and then rapidly cool the material in flowing air or water. This process dissolves any chromium carbides that may have formed. The rapid cooling results in a single phase austenitic microstructure, the preferred structure for the 304 stainless steel and results in achieving the maximum corrosion resistance.
Heat the material through to 1112°F (600°C) after rough machining and hold for 2 hours. Cool slowly to 930°F (500°C), then it can be freely cooled further in air. Stress relieving above 1112°F (600°C) will cause a serious threat of grain boundary sensitization accompanied with loss of corrosion resistance.
Preheating temperature: 1110-1560°F (600-850°C)
Austenitizing temperature: 1830-1920°F (1000-1050°C), should usually be done at 1870-1885°F (1020-1030°C)
Parts need to be protected against decarburization and oxidation during the hardening process.
To obtain its greatest properties cool the parts as quickly as possible, but care should be taken to maintain acceptable distortion. The parts have to be tempered as soon as they reach the temperature of 120-160°F (50-70°C).
• Fluidized bed or salt bath at 480-1020°F (250-550°C) followed by cooling in an air blast
• Vacuum with sufficient positive pressure
• High speed gas/circulating atmosphere
Choose the tempering temperature that needs to be achieved, temper twice and cool between tempering to room temperature. Do not let the tempering temperature drop below 480°F (250°C) and hold at the chosen temperature for a minimum of 2 hours. At the tempering temperature of 480°F (250°C) the best combination of toughness, hardness and corrosion resistance can be achieved.
As an austenitic steel grade, unlike for tool steel the sub-zero treatment to convert retained austenite does not have the same purpose. It refines the microstructure of the 304 to enhance the corrosion resistance and improve the mechanical properties. It can increase the tensile and yield strength while retaining its high ductility during this treatment.
While sub-zero treatment can be beneficial the overall processing and compatibility should be considered.

304 SURFACE TREATMENT
Choosing the surface treatment for the 304 stainless steel, the desired outcome and application should be considered. As well, some treatments can impact the corrosion resistance positively but also negatively, so if corrosion resistance is a priority, it should be considered to use a surface treatment to enhance the natural corrosion resistance of this grade.
To remove free iron from the surface of the material, the surface is treated with an acid solution, this will leave the passive chromium layer with an even richer and purer chromium layer that enhances the natural corrosion resistance of the 304.
Various finishes, from brushed to mirror finish, can be achieved by polishing the surface of the 304 stainless steel.
This process blasts abrasive particles against the surface under high pressure. This process is used to clean contaminants, rust, paint or scale of the surface or can promote a surface texture or finish.
The 304 stainless steel can get blasted with glass or ceramic beads to promote a matte or satin finish.
Note: Care has to be taken during this process as the process produces dust and small parts might be propelled back. Protective gear like masks, helmets and protective clothing should be worn and adequate ventilation or dust extraction should be provided.
With a mixture of strong acids oxide scales and surface contaminants are removed. This process is often done after welding for example.
Electropolishing is a non-mechanical chemical process using an electric current to remove a thin layer of material to give the material a smooth and shiny surface. This process is not to be confused with passivation which also is a non-mechanical chemical process but does not use the electric current.
During PVD treatment a thin layer of material is introduced onto the surface of the material. This treatment can give the steel a unique color or enhance the surface properties.

304 PROCESSING
While machining the 304 stainless steel only tools dedicated to work with stainless steel should be used and surfaces and tools kept clean to avoid cross contamination. Contamination of the 304 stainless steel can introduce particles that attack the material.
Cutting edges should be kept sharp as dull edges can promote excess work hardening. The low thermal conductivity of austenitic steels may impact the cutting edges by concentrating heat there. Lubricants and coolants should be liberally used to avoid the heat concentration in the cutting edges.
Due to its good conductivity the 304 stainless steel can be EDMed at relatively high speed. The surface may have a rougher finish due to the chromium content which necessitates fine tuning the machining parameters or additional finishing operations may be needed.
After the EDM process the recast layer, a thin white layer, should be removed. This can be done by polishing or electropolishing the parts.
Depending on temperature, equipment and cooling media used during heat treatment, dimensional changes of approx. 0.15% per side should be taken into account. Also important is the size and geometric shape of the tool and a stress relief should be done between rough and semi-finishing.
Forging temperatures for the 304 are in the range of 2010 - 2280°F (1100 - 1250°C).
Heat uniformly to the higher end of the temperature range and forge while the material is cooling. After this process let the material cool in air or in a dry environment. To adjust the structure and mechanical properties after forging the material should be solution annealed as described above. This will remove forging stresses and restore its austenitic structure.
To avoid excessive work hardening extreme working temperatures and low temperatures during forging should be avoided. High temperatures and the presence of air may lead to oxide scaling which may need to be removed depending on the following application and the desired finish. To reduce friction appropriate lubricants should be used.
The 304 stainless steel can be welded by a variety of methods like Gas Tungsten and Gas Metal Arc Welding (GTAW/TIG and GMAW/MIG) or Shielded Metal Arc Welding (SMAW) and Resistance Welding.
With the correct choice of filler, technique and post-weld treatment this material grade has a good weldability. Care has to be taken against distortion, intergranular corrosion, residual weld stresses, oxide formation and sensitization by choosing the correct temperature and taking the thermal expansion in consideration.

304 APPLICATION OPTIONS
304 stainless steel, as the most commonly used steel grade of stainless steel, can be used in various applications and in environments that expose it to moisture.
• Photographic industry
• Paint industry
• Oil industry
• Soap industry
• Paper industry
• Textile industry
• Mechanical engineering
• Turned parts
• Fittings construction
• Kitchen equipment
• Decoration
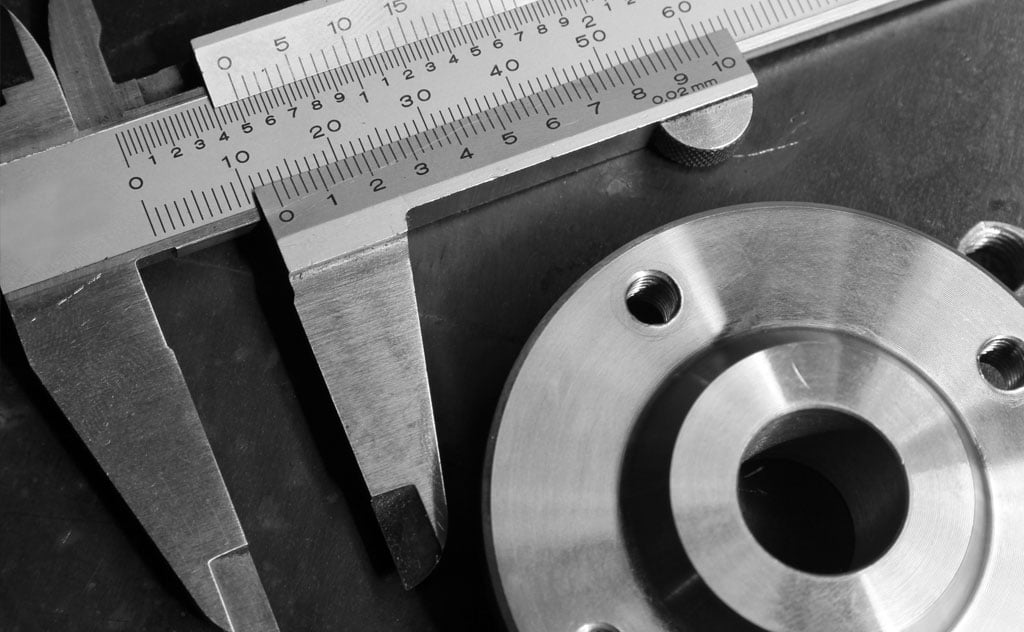

304 CONCLUSION
304 stainless steel one of the most commonly used stainless steel grades due to its high corrosion resistance to a wide range of environments and media. It is easy to form and weld and does not become magnetic when annealed. It is available in many forms and has an attractive and easy-to-clean surface.
- Austenitic chromium-nickel steel
- Deep-drawable
- Weldable
- Polishable
- Finishes from brushed to high-gloss possible
- Very good corrosion resistance
- Not magnetizable
- Limited machinability
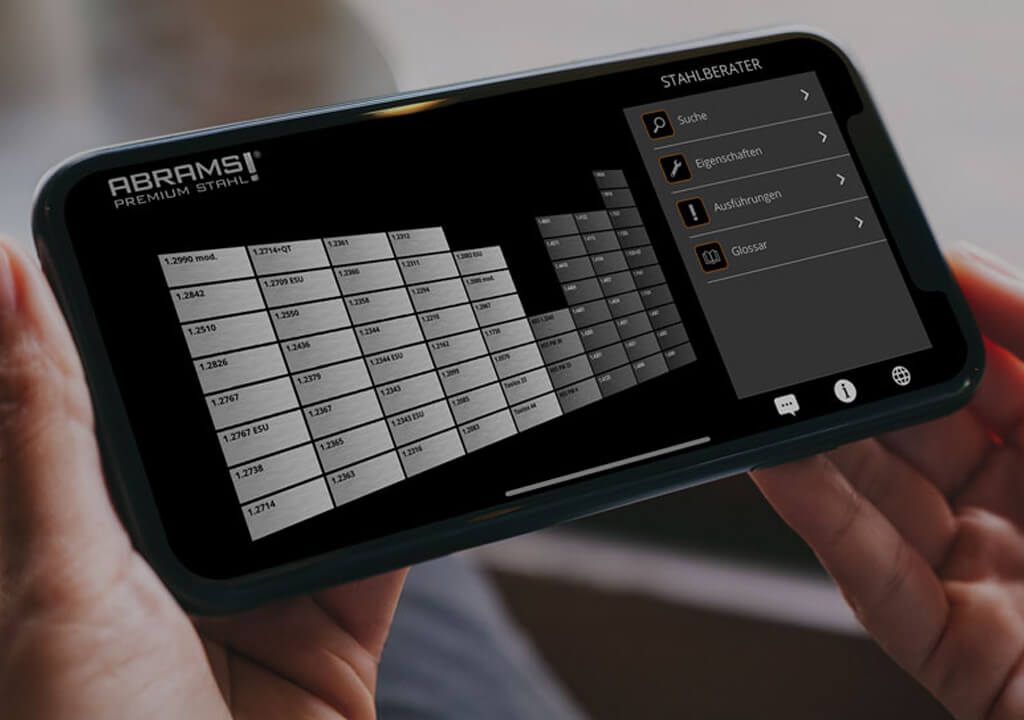

304 ALTERNATIVES
Are you looking for an alternative steel grade?
WE HAVE THE SOLUTION!
With the ABRAMS STEEL GUIDE, you can obtain an alternative or equivalent steel grade with just a few clicks.

304 DATASHEET
Download the technical data sheet in PDF format here.
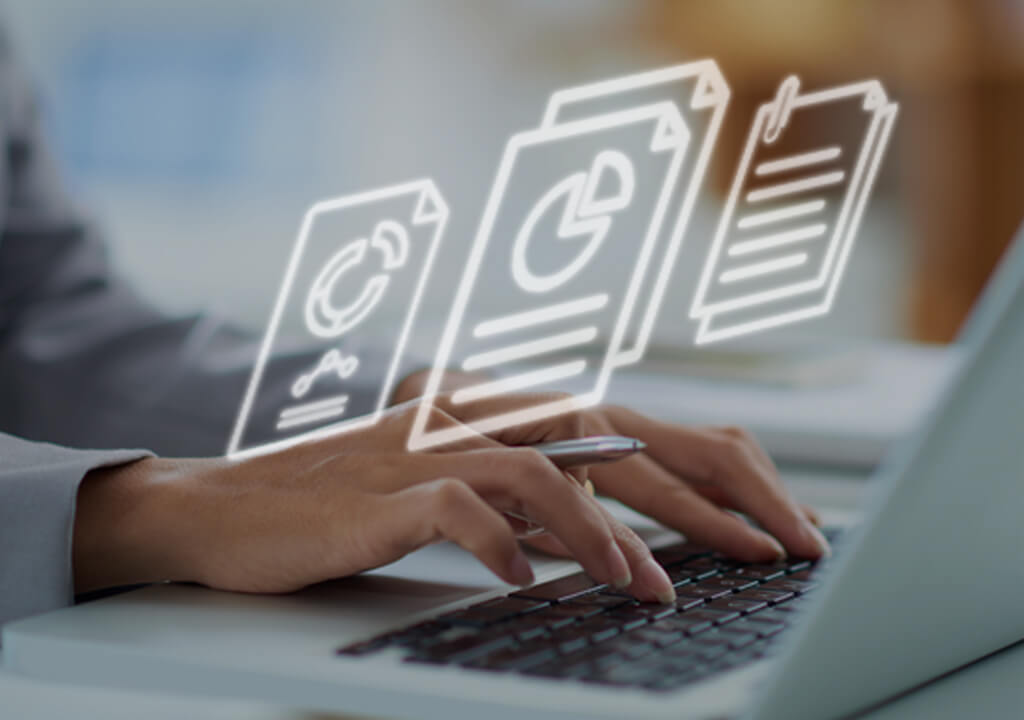
The data shown here has been compiled with the greatest diligence and is regularly updated with regard to the correctness and completeness of its content. The content is indicative only and should not be taken as a warranty of specific properties of the product described or a warranty of suitability for a particular purpose. All information presented is given in good faith and no liability will be accepted for actions taken by third parties in reliance on this information. ABRAMS Industries reserves the right to change or amend the information given here in full or parts without prior notice.