316L / 316 Stainless - X2CrNiMo17-12-2 / X5CrNiMo17-12-2
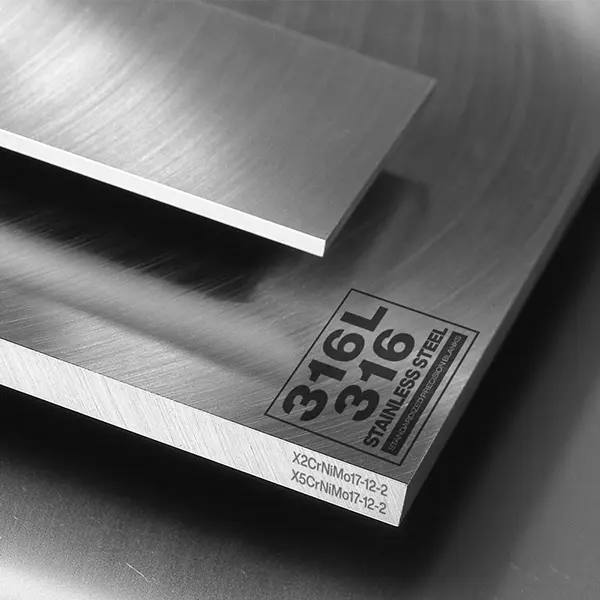
316L / 316 Stainless - X2CrNiMo17-12-2 / X5CrNiMo17-12-2
Back to Steel OverviewGround Flat Stock and $mart Flat Stock comes always in a machined condition, that means:
NO decarburization on the surfaces (decarburization leads to unreliable components and tools)
Less dirt on your machines during further processing – nothing but clean chips
Stress-relieved flat steel avoids warping of components during further machining
Get the close-to-finish-size thickness and width you need for the components you plan
Ground Flat Stock and $mart Flat Stock comes always in a machined condition, that means:
NO decaburization on the surfaces (decarburization leads to unreliable components and tools)
Less dirt on your machines during further processing – nothing but clean chips
Stress-relieved flat steel avoids warping of components during further machining
Get the close-to-finish-size thickness and width you need for the components you plan
Ground Flat Stock and $mart Flat Stock comes always in a machined condition, that means:
NO decaburization on the surfaces (decarburization leads to unreliable components and tools)
Less dirt on your machines during further processing – nothing but clean chips
Stress-relieved flat steel avoids warping of components during further machining
Get the close-to-finish-size thickness and width you need for the components you plan
316L / 316 STEEL PRICE CHART

316L / 316 STANDARD VALUES
C
Si
Mn
P
S
Cr
Mo
Ni
N
X2CrNiMo17-12-2 / X5CrNiMo17-12-2
approx. 215 BHN (delivery condition)
max. 215 HB
X2CrNiMo17-12-2 / X5CrNiMo17-12-2
approx. 215 BHN (delivery condition)
max. 215 HB
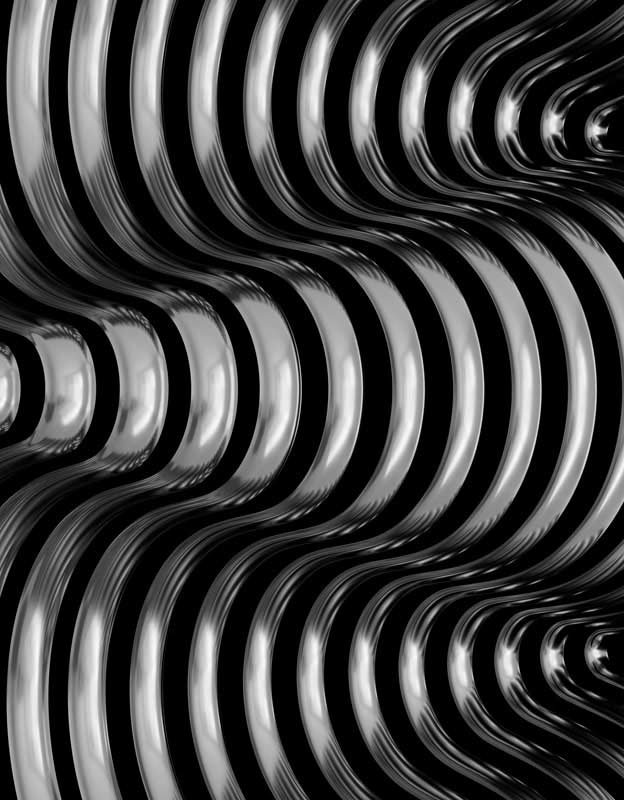

316L / 316 PHYSICAL PROPERTIES
316L / 316 are austenitic chromium-nickel-molybdenum stainless steels, resistant to general corrosion and pitting, polishable, good weldability and non-magnetizable.
As the second most commonly used stainless steel and with the addition of 2 - 2.5% of molybdenum, 316L / 316 exhibit better corrosion resistance, even in the presence of chlorides, and are stronger at elevated temperatures. Both, low temperature applications are possible, as well as applications up to 1022°F (550°C).
Both alloys provide higher creep resistance, stress rupture and tensile strength at elevated temperatures. Typical for austenitic stainless steels they are both non-hardenable by heat treatment and provide excellent processing capability and formability.
Corrosion resistance is reduced in sulphurous flue gases. In such environments, 316L / 316
can be used at temperatures up to 1110 - 1380°F (600 - 750°C), depending on service conditions. Consideration must be given to whether the atmosphere is oxidizing or reducing, e.g. the oxygen content, and whether impurities such as sodium and vanadium are present.
In the presence of chloride or halide ions, austenitic stainless steels are resistant to pitting and/or crevice corrosion when higher chromium, molybdenum and nitrogen content is present. The molybdenum in these steels will handle water with up to about 0.017lb/gal. (2,000 ppm) of chloride. Although considered adequate for some marine environment applications such as boat rails or facades of buildings near the ocean, it is not recommended in seawater containing 0.159lb/gal. (19,000ppm) of chloride.
Intergranular corrosion is the result due to the precipitation of chromium carbides at the grain boundaries for the 316 when exposed to a temperature range of 800-1500°F (427-816°C).
To avoid intergranular corrosion, 316L with its lower carbon content can be used for applications where heavy cross-sections cannot be annealed after welding or if lower temperatures for stress relieving are wanted or when exposed to short periods of temperatures of 800-1500°F (427-816°C).
Without affecting the normal excellent corrosion resistance of 316L, short stress relieving treatment can be applied. When heavy and bulky parts have been annealed, it is not necessary to cool them rapidly from high temperatures.
With the addition of molybdenum stainless steel develops a maximum resistance to staining and pitting, therefore austenitic stainless steels surpass virtually all other engineering materials. In atmospheres where chlorides, sulfur compounds and solids are found either individually or in combination, these grades are regularly used.
Austenitic steels are prone to stress corrosion cracking, as can be encountered at temperatures above 140°F (60°C) when the steel is exposed to tensile stresses or comes into contact with solutions containing chlorides, for example, at the same time.
Austenitic steels are prone to stress corrosion cracking, as can be encountered at temperatures above 140°F (60°C) when the steel is exposed to tensile stresses or comes into contact with solutions containing chlorides, for example, at the same time.
316L / 316 stainless steel used for short periods at temperatures up to 1600°F (870°C) or a constant temperature of 1700°F (925°C) have good oxidation resistance. Temperature ranges of 850 - 1550°F (454 - 845°C) are not recommended for 316 stainless steel as there is the possibility of carbide precipitation but it performs well in varying temperatures above or below that range. For those applications in the former mentioned temperature range the 316L should be used.

316L / 316 TECHNICAL PROPERTIES
Typically the density of 316L / 316 stainless steel is 0.289 lb/in3 (8.0g/cm3) at room temperature.
The 316 stainless steel grade has a good resistance to oxidation at temperatures up to 1598°F (870°C) in intermittent operations and up to 1697°F (925°C) for continuous operations. For the 316 it is not recommended to use temperatures in the range of 797 - 1580°F (425 - 860°C) for continuous operations if the parts are used in a water based environment as the corrosion resistance in water will deteriorate.
The 316L can be used for the former mentioned temperature range as it is more resistant to carbide precipitation.
The heat conductivity for 316L / 316 Steel is at 15.0 W/(m*K) (104 BTU/(h-ft*°F)) at room temperature.
Heat conductivity is a physical property that shows how wella material conducts heat. Heat conductivity is very important for applications which transfer heat or need tight temperature controls. In the following table you can find the heat conductivity values listed for D2.
Medium thermal expansion coefficient | |
10-6m/(m • K) | At a temperature of |
16.0 | 68 - 212°F |
16.5 | 68 - 392°F |
17.0 | 68 - 572°F |
17.5 | 68 - 752°F |
18.0 | 68 - 932°F |
You can find the temperature dependent material constant (Resistivity) in the following table. The electrical conductivity is the reciprocal value of the specific resistance.
Table of the specific electrical resistivity | |
Value | At a temperature of |
0.74 (Ohm*mm²)/m | 68°F |
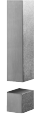
316L / 316 AS PRECISION GROUND FLAT STOCK, EDM BLOCK, HARD FLAT OR DRILL ROD.
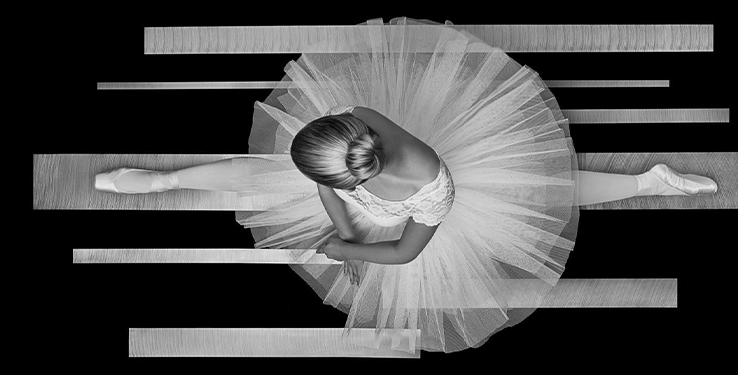
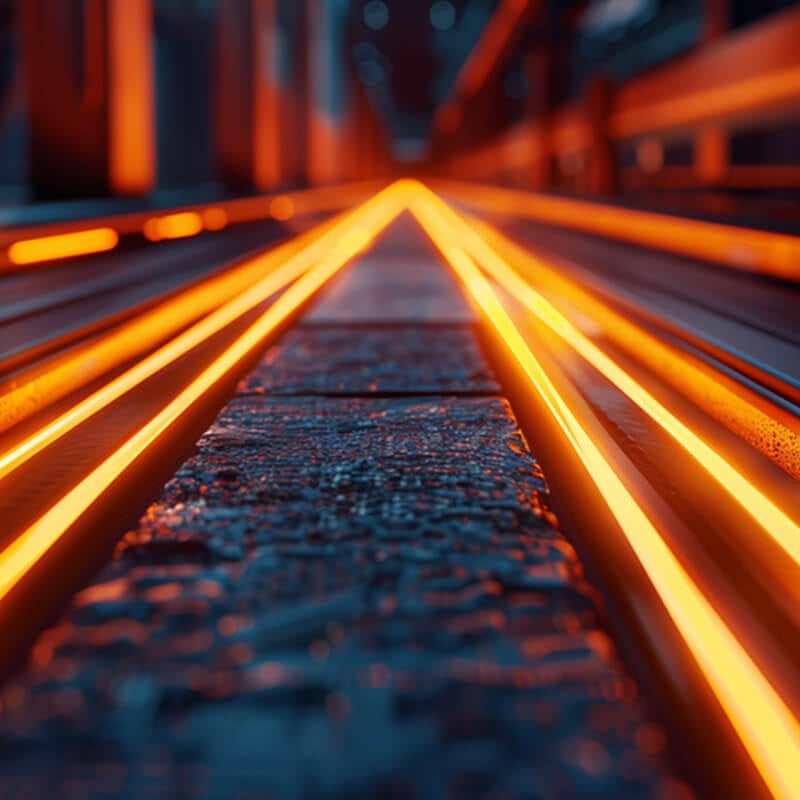

316L / 316 PROCEDURE
316L as the lower carbon steel grade can be stress relieved at 850 - 1100°F (454 - 593°C) for 60 minutes with minimum danger of sensitization.
316 should be done at a lower temperature not exceeding 750°F (399°C) but with a longer soaking time. As there is a risk of grain boundary sensitization occurring, resulting in the loss of its corrosion resistance, stress relieving above 1100°F (593°C) is not recommended.The 316L / 316 is not hardenable by heat treatment.
As an austenitic stainless steel the 316L / 316 can be hardened by cold working it. Care should be taken as to the extent to which it can be hardened by cold work as the material will get brittle and sensitive to stress corrosion cracking.
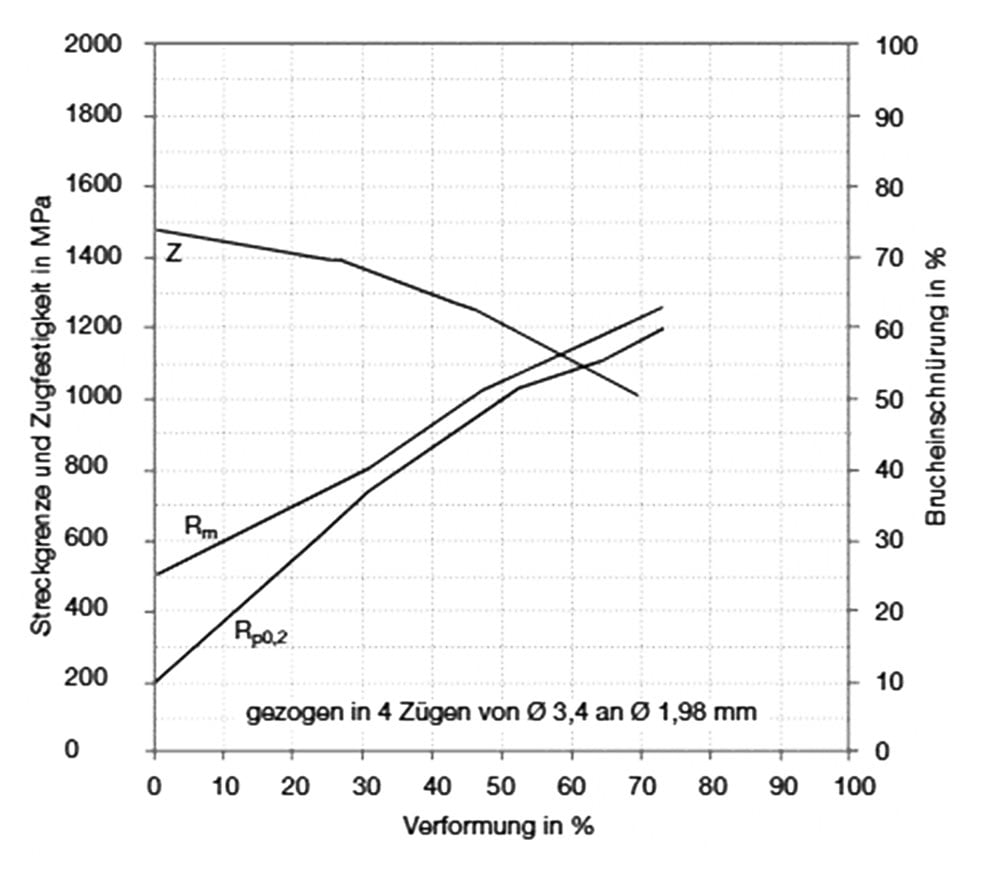
Usually sub-zero treatment is done to convert remaining austenite to martensite. As an austenitic stainless steel 316L / 316 will keep its austenitic structure.
Sub-zero treating the 316L / 316 can improve its mechanical properties, resistance to stress corrosion cracking and slightly improve pitting and wear resistance. Care should be taken as sub-zero treatment has the potential for cryogenic embrittlement, even though the 316L / 316 in general has good cryogenic properties.

316L / 316 SURFACE TREATMENT
In general passivation improves the corrosion resistance by giving the material a passive oxide layer to ensure the surface is less reactive to its surrounding environment.
Passivation ensures a contaminant free surface and prevents in turn contamination when used in the food processing industry as food containers for instance.Pickling is mainly done to remove impurities like rust or scale from the surface by immersing the parts into an acid bath. This process can be followed up by other surface treatments like passivation which is explained above.
Abrasive blasting is a process where abrasive particles are propelled against the surface under high pressure. It is used to clean contaminants but as well rust, paint or scale or to promote a surface texture or finish.
Abrasive particles can include glass beads, silica sand, steel grit, coal or copper slag and also organic materials like walnut shells or corn cob which are used for a less aggressive cleaning.
Abrasive blasting can be done by dry blasting where air propels the abrasive material for this method. Another methode is wet blasting, where the abrasive particles are mixed with water.
Note: Care has to be taken during this process as the process produces dust and small parts might be propelled back. Protective gear like masks, helmets and protective clothing should be worn and adequate ventilation or dust extraction should be provided.

316L / 316 PROCESSING
During deformation, 316L/316 is subject to work hardening and chip breaking. For the best machining results, it is better to use slower speeds, excellent lubrication, sharp tooling, heavier feeds and high performance equipment.
Stainless steel 316L / 316 can be worked by EDM. Adjusting the parameters, choosing the correct electrode and required surface finish should be taken into consideration. The recast layer should be removed and properties might be slightly altered in the heat affected zones. To have a clean and smooth surface, post treatments are necessary and should be factored in when the application requires a clean smooth surface.

316L / 316 APPLICATION OPTIONS
316L can be used in the food processing industry, and the 316 as a pharmaceutical grade steel for chemical processing and storage of chemicals, paper industry, pharma industry due to its high resistance to chloride and acids. They will also find its uses in the automotive and aviation industries.
• Chemical industry
• Pharmaceutical industry
• Food industry
• Valve and plant construction
• Building industry
• Automotive industry
• Aviation industry
• Mechanical engineering
• Offshore
• Petrochemical industry
• Electrical equipment
• Decorative uses
• Kitchen equipment
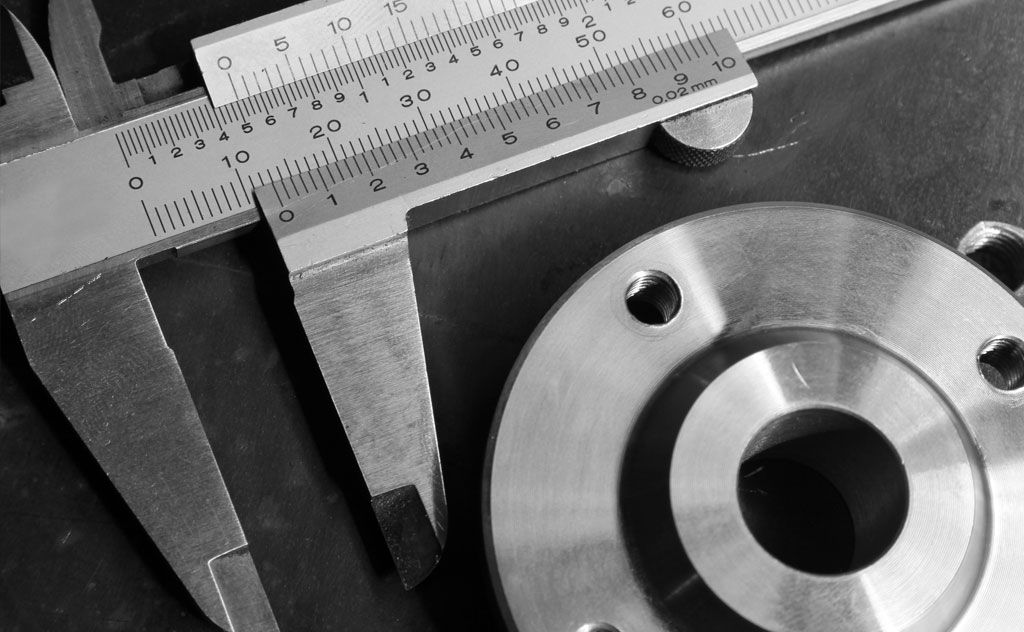

316L / 316 CONCLUSION
These two stainless steel grades are widely used due to their excellent corrosion resistance. They offer excellent resistance in a wide range of chemicals and find their use in chemical processing equipment but also in marine applications.
Dual certification is given to the 316L / 316 which means both materials meet the chemical and mechanical properties and strictest requirements of both grades. This gives the user more flexibility and the confidence to interchange the materials in applications either one is specified.
The “L” for the 316L stands for Low carbon, which makes it highly resistant to sensitization (grain boundary carbide precipitation) and therefore is used extensively in heavy gauge welded components and allows the use of this grade in the as-welded condition in a wide variety of corrosive applications.
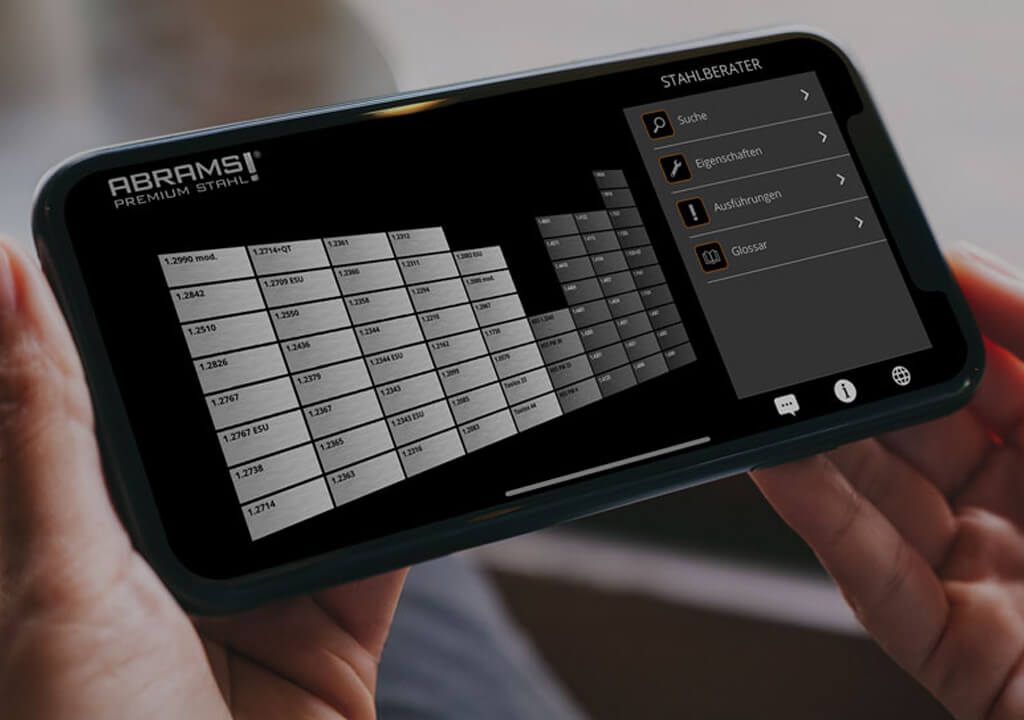

316L / 316 ALTERNATIVES
Are you looking for an alternative steel grade?
WE HAVE THE SOLUTION!
With the ABRAMS STEEL GUIDE, you can obtain an alternative or equivalent steel grade with just a few clicks.

316L / 316 DATASHEET
Download the technical data sheet in PDF format here.
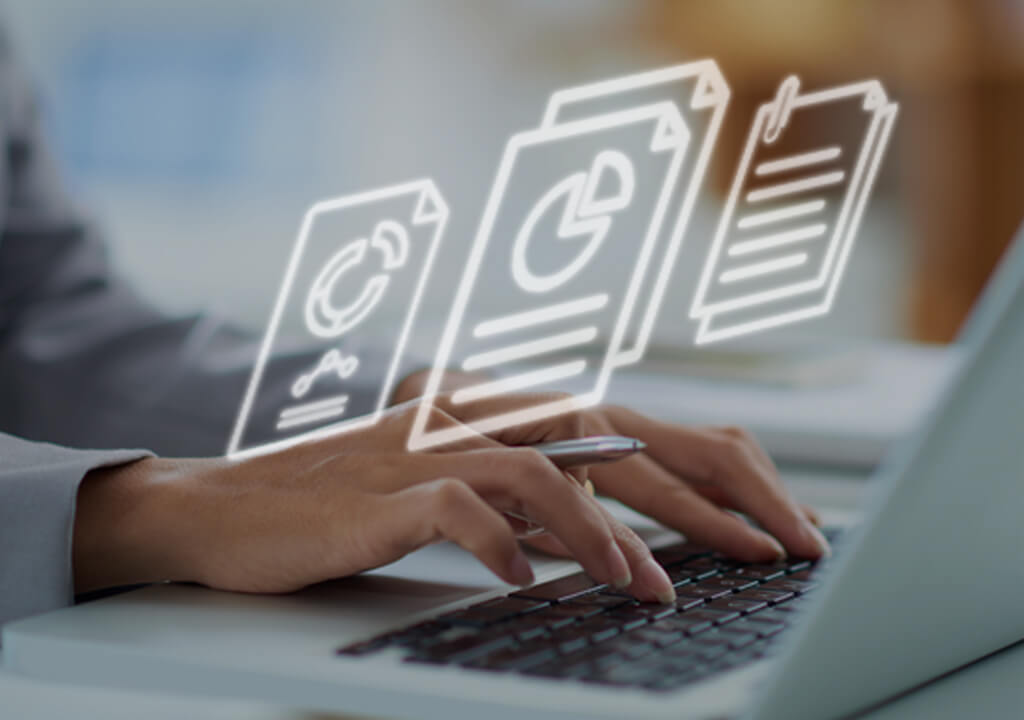
The data shown here has been compiled with the greatest diligence and is regularly updated with regard to the correctness and completeness of its content. The content is indicative only and should not be taken as a warranty of specific properties of the product described or a warranty of suitability for a particular purpose. All information presented is given in good faith and no liability will be accepted for actions taken by third parties in reliance on this information. ABRAMS Industries reserves the right to change or amend the information given here in full or parts without prior notice.