W1 Tool Steel - 1.1535 - C90U - SAE W109 - JIS ~SK 90
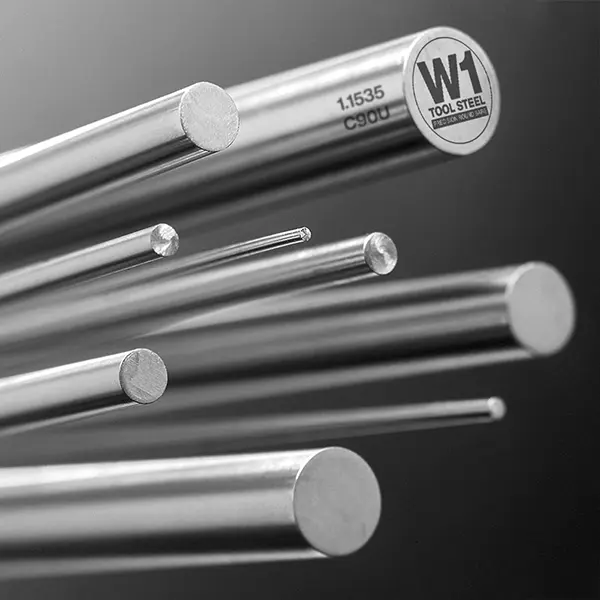
W1 Tool Steel - 1.1535 - C90U - SAE W109 - JIS ~SK 90
Back to Steel OverviewGround Flat Stock and $mart Flat Stock comes always in a machined condition, that means:
NO decarburization on the surfaces (decarburization leads to unreliable components and tools)
Less dirt on your machines during further processing – nothing but clean chips
Stress-relieved flat steel avoids warping of components during further machining
Get the close-to-finish-size thickness and width you need for the components you plan
Ground Flat Stock and $mart Flat Stock comes always in a machined condition, that means:
NO decaburization on the surfaces (decarburization leads to unreliable components and tools)
Less dirt on your machines during further processing – nothing but clean chips
Stress-relieved flat steel avoids warping of components during further machining
Get the close-to-finish-size thickness and width you need for the components you plan
Ground Flat Stock and $mart Flat Stock comes always in a machined condition, that means:
NO decaburization on the surfaces (decarburization leads to unreliable components and tools)
Less dirt on your machines during further processing – nothing but clean chips
Stress-relieved flat steel avoids warping of components during further machining
Get the close-to-finish-size thickness and width you need for the components you plan
W1 STEEL PRICE CHART

W1 STANDARD VALUES
C
Si
Mn
P
S
Cr
Mo
V
W
C90U
55 HRC - 65 HRC
max. 200 HB
C90U
55 HRC - 65 HRC
max. 200 HB
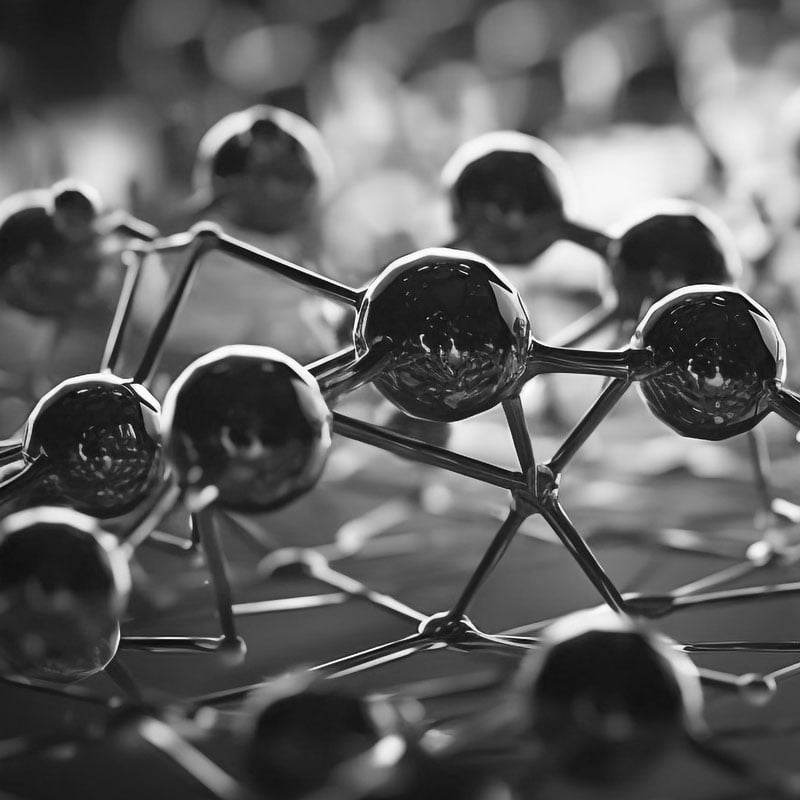

W1 PHYSICAL PROPERTIES
Tool steel W1 is a water hardening, cold work and carbon tool steel. The carbon content gives this steel grade its keen cutting edge and it can be hardened by heating and quenching.
W1, is the most widely used in the water hardening group. It finds its uses in applications which require a softer core, high hardness, and machinability. Though corrosion resistance is low, this steel grade is good for knife blades as it not only has a high hardness, due to the high carbon content, but very good edge retention as well.
With the addition of chromium, this steel can increase its wear resistance and hardenability. Vanadium maintains the grain size in this steel, and enhances the toughness of this steel grade.
As a high carbon steel the W1 does not have the significant amount of chromium needed to make it a stainless steel. A stainless steel grade has a chromium content of 10.5%, the W1 has a chromium content in the range of 0.0 - 0.2% and is therefore not a stainless steel. W1 can rust if exposed to moisture and corrosive environments. To protect the W1 a protective coating or surface treatment should be considered or it should be considered to use stainless steel instead.
W1 does not have a standalone corrosion resistance and the high carbon content can make steel more susceptible to certain types of corrosion.
W1 is ferromagnetic steel and cannot only be magnetized but is attracted to magnets in its original form. The W1 can be used on machines using magnetic clamping. As the W1 may lose some or all magnetization after heat treatment, remagnetization might be necessary for clamping or some applications where it is needed. Remagnetization can be achieved by direct contact with a magnet or by using an electromagnet.
On a scale of 1 to 6 where 1 is low and 6 is high the W1 scores a 4.
It is possible for this steel grade, W1, to be hot worked.
W1 has very good ductility in its annealed condition and it is possible to cold work this steel grade by conventional practices.

W1 TECHNICAL PROPERTIES
The W1 tool steel can be used as a knife steel. With its high carbon content it achieves a high hardness which is ideal for the edge retention in a knife blade. It is easy to sharpen to a very fine edge due to a fine grain structure.
However, as theW1 is not a stainless steel, if not maintained properly it can rust easily in humid and salty environments. Regular maintenance and oiling the blade can prevent this from happening.
The working hardness for the W1 tool steel is in a range of 552 - 711 BHN (55 - 65 HRC).
Typically the density of W1 tool steel is 0.282 lb/in3 (7.8g/cm3) at room temperature.
The W1 tool has a tensile strength of approx. 97.5 KSI on delivery (0.145 KSI = 1MPa). In order to reach this value, a tensile test is performed to show how much force is needed to stretch or elongate a sample before it breaks.
The heat conductivity for the W1 is at 45.0 W/(m*K) (26018 BTU/(h-ft*°F)) at room temperature.
The following table shows expansion or contraction at various temperatures, which may be very important for high temperature works or when working with high temperature changes.
Medium thermal expansion coefficient | |
10-6m/(m • K) | At a temperature of |
11.1 | 68 - 212°F |
12.1 | 68 - 392°F |
12.9 | 68 - 572°F |
13.5 | 68 - 752°F |
13.9 | 68 - 932°F |
The specific heat capacity of the W1 at room temperature is at 0.460J/g-°C (0.110BTU/lb-°F). This value shows how much heat is needed to heat 1lb of material by 1 Fahrenheit.
You can find the temperature dependent material constant (Resistivity) in the following table. The electrical conductivity is the reciprocal value of the specific resistance.
Table of the specific electrical resistivity | |
Value | At a temperature of |
3.0 x 10-10 (Ohm*mm²)/m | 68°F |
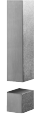
PERFECT MATERIAL SELECTION WITH THE ABRAMS STEEL GUIDE®: STEEL-GUIDE:US
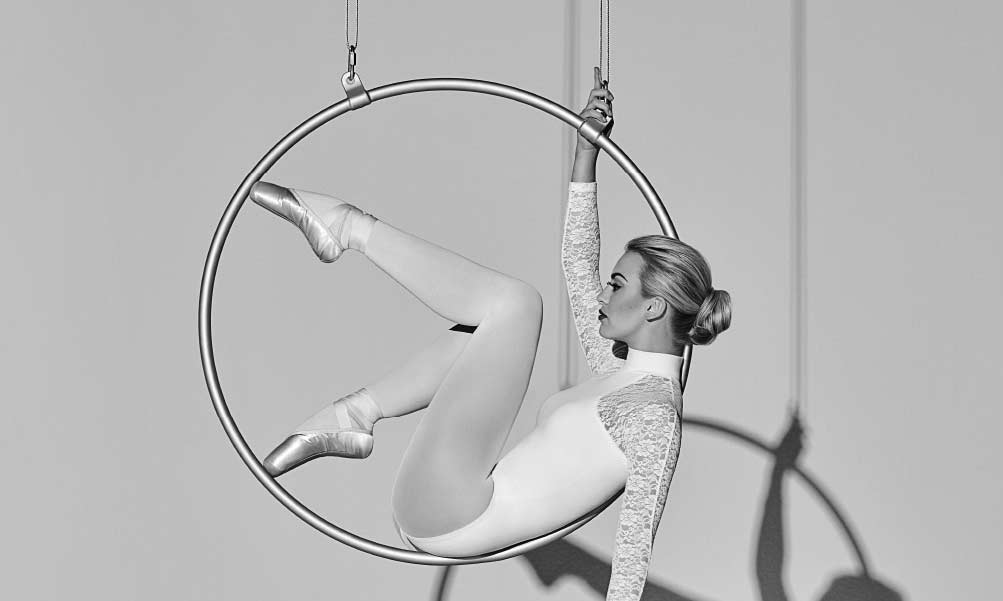
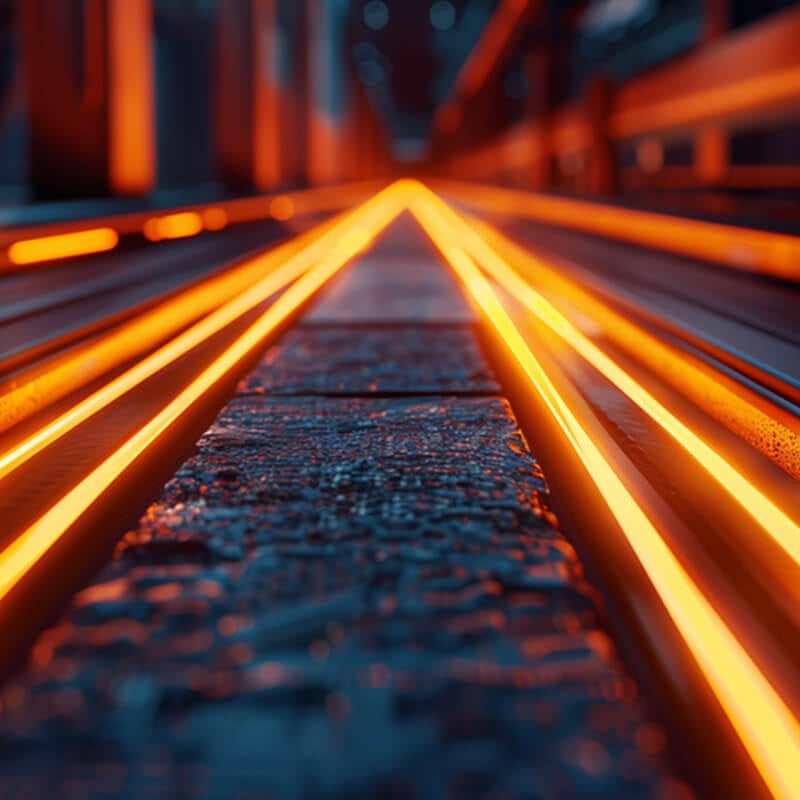

W1 PROCEDURE
Heat the material uniformly to a temperature of 1256-1310°F (680-710°C) and hold at that temperature for approx. 1 hour per 1 inch of thickness. Then cool slowly in the furnace by 50-60°F (10-20°C) per hour to approx. 1112°F (600°C) and finish the process cooling the parts further in air. Instead of leaving the material in the furnace it can also be moved and covered by an insulating material like ash or lime to slow the cooling rate down.
W1 should undergo the normalizing treatment to refine grain size and to relieve residual stresses. Normalizing should be done before full annealing and after forging. Pack the work pieces in a protective atmosphere to avoid decarburization. Heat the material to a temperature of 1450-1700°F (790-925°C), hold small sections for 15 minutes and large sections for up to 1 hour at temperature then air cool after.
Note: Normalizing is no low temperature annealing. The difference between annealing and normalizing is the way this material grade is cooled. After the annealing process the W1 is cooled slowly, that way it ensures a maximum softness, while after normalizing the steel is cooled down in air to give it properties like strength, ductility and toughness.
Uniformly heat the parts to a temperature of 1112-1202°F (600-650°C) after rough machining to relieve stresses and reduce distortion during heat treatment, hold for 2 hours in a neutral atmosphere. Follow this up with a slow furnace cooling or cool the parts in still air to an ambient temperature.
Heat the parts slowly and uniformly to a temperature of 1400-1454°F (760-790°C). Soak for 10 minutes per inch (25.4 mm) of thickness, but a minimum of 30 minutes. Small parts can be heated in a salt bath or molten lead.
After the hardening process the W1 is rapidly cooled. Rapid cooling in water ensures the transformation of austenite to martensite, hardening the W1. After quenching the material is hard but also brittle and to relieve the material from this brittleness and also achieve a balance between hardness and toughness it has to be tempered as shown below.
• Water (may result in warping and cracking)
• Brine
Heat the material to a temperature of 350-650°F (177-343°C) and soak for 1 hour per inch (25.4 mm) thickness but at least 1 hour. Finish with cooling the parts in air. This process will leave the W1 with reduced brittleness and improved toughness.
Heat the material to a temperature of 350-650°F (177-343°C) and soak for 1 hour per inch (25.4 mm) thickness but at least 1 hour. Finish with cooling the parts in air. This process will leave the W1 with reduced brittleness and improved toughness.
Sub-zero treatment of the W1 is primarily done to transform remaining austenite, after quenching, to martensite, making the W1 harder and more stable.Remaining austenite can affect the dimensional stability, wear resistance and the overall performance of the W1 parts.

W1 SURFACE TREATMENT
As a high carbon steel, the W1 can undergo a variety of surface treatments. Find below some surface treatments as an example. When choosing a surface treatment, desired properties and where the parts are used as well as the environment in which the parts are working should be taken in consideration.
Case hardening like nitriding or carburizing creates a harder more wear resistant surface with a tough core.
This coating of material gives it a mild corrosion resistance. It is often used for decorative purposes but also to reduce light reflection.
Physical Vapor Deposition (PVD) and Chemical Vapor Deposition (CVD) deposit a thin, hard coating over the material surface which strengthens wear and oxidation resistance as well as the hardness of the W1 tool steel.

W1 PROCESSING
The machinability of the W1 tool steel actually depends on the condition in which it is being machined. In its annealed condition it is easy to machine, however in its hardened condition the machinability does decrease and tooling and methods should be taken in consideration.
W1 can be machined by EDM in its annealed and hardened condition. As for other steels EDM will achieve a smooth and precise finish but will also create a heat affected zone which has to be taken in consideration for further processes.
Dimensional change may occur during heat treatment as steel might expand with heat and contract while cooling down, during phase changes or by processing the material and introducing internal stresses to the material. Internal stresses can be relieved by heat treatment which again can lead to their own dimensional changes. Cooling this tool steel rapidly as done after hardening or heating it up unevenly may distort the W1.
In its annealed condition W1 can be formed by bending, stamping, punching or drawing. When forming the material in the hardened condition care has to be taken as it is brittle in this condition.
Heat the work pieces uniformly to a temperature range of 1500-1832°F (843-1000°C), do not forge this material below 1500°F (843°C). To finish this process slowly cool the work pieces in the furnace or heat insulating material. As a high carbon tool steel care should be taken not to overheat this material grade as this may lead to grain growth.
W1 can be welded by all conventional methods but there is a general tendency of cracking, brittleness and distortion after welding if this grade is not handled correctly. If welding cannot be avoided the correct consumables should be chosen. The weld parts should be cooled slowly to avoid added stress or rapid phase changes as they could lead to cracking.

W1 APPLICATION OPTIONS
W1 can be used for are stamping, slitting or pipes for example. It is used for cutting tools like chisels, punches or knives or wood working tools like carving tools or planes as it is suitable for tools needing a sharp edge.
It is used for tools like hand tools where shock resistance is not a necessity in comparison to what other tool steels can offer. As cold working tools it is used to shape materials without using heat.
Due to its hardness it can be used for drills and taps and if not used too heavily, it may be used for dies and mold as well.
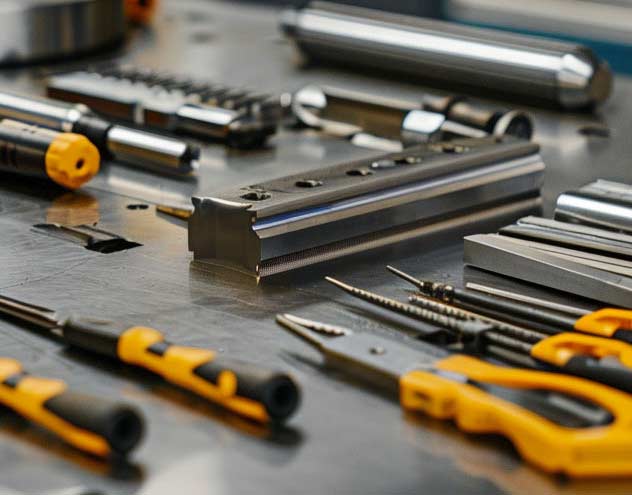

W1 CONCLUSION
W1 tool steel can achieve a high hardness following a proper heat treatment, this results in a sharp edge with good edge retention. It is easy to sharpen, with its fine grain structure it has a good edge stability, can be honed to a very fine edge and consequently has a very keen edge. However, maintenance has to be considered due to the W1 not being stainless.
To recap, tool steel W1 has a good balance of qualities which makes this steel grade suitable to a variety of applications.
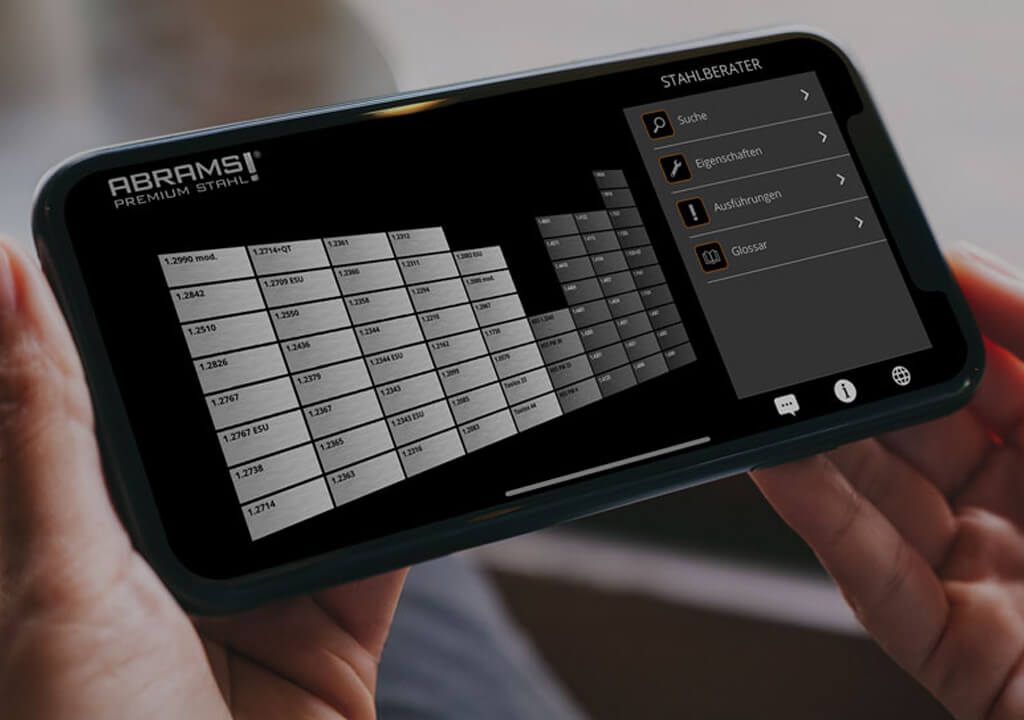

W1 ALTERNATIVES
Are you looking for an alternative steel grade?
WE HAVE THE SOLUTION!
With the ABRAMS STEEL GUIDE, you can obtain an alternative or equivalent steel grade with just a few clicks.

W1 DATASHEET
Download the technical data sheet in PDF format here.
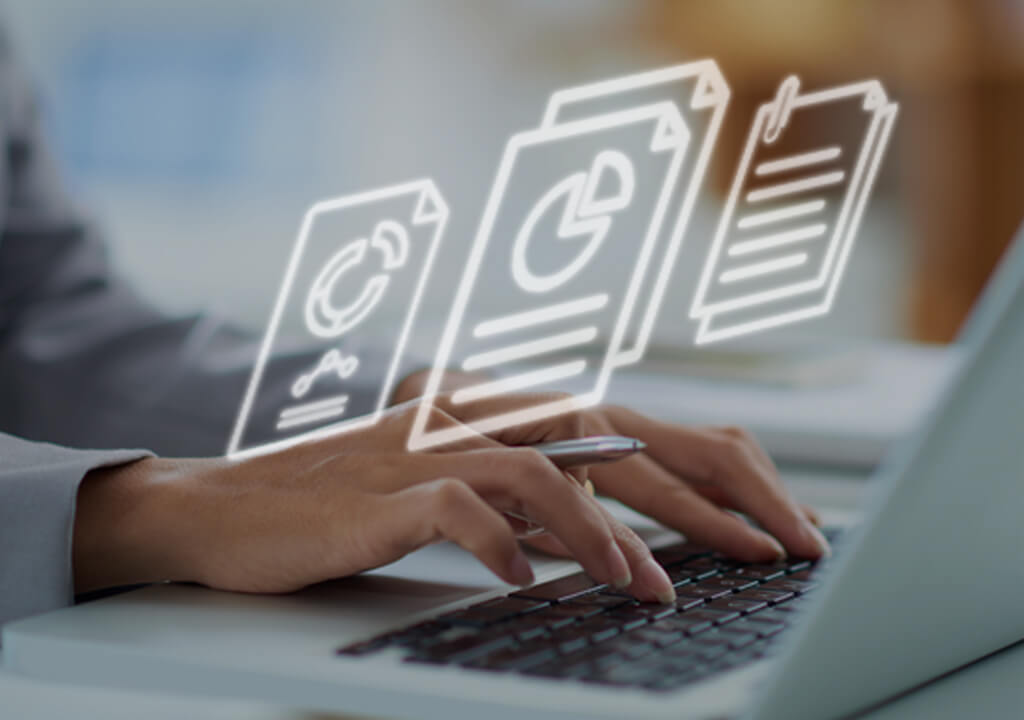
The data shown here has been compiled with the greatest diligence and is regularly updated with regard to the correctness and completeness of its content. The content is indicative only and should not be taken as a warranty of specific properties of the product described or a warranty of suitability for a particular purpose. All information presented is given in good faith and no liability will be accepted for actions taken by third parties in reliance on this information. ABRAMS Industries reserves the right to change or amend the information given here in full or parts without prior notice.