Hot work steel - the best steels for hot working!
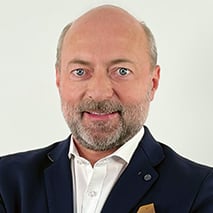
Written by Dr. Juergen Abrams on August 26, 2024.
Hot work steel has an excellent combination of mechanical and metallurgical properties. It is used for applications with a surface temperature above 392 °F (200 °C) and has to withstand extended thermal loads, changing temperatures and thermal abrasion.
During hot working metal, it is deformed above the recrystallization temperature but below the melting point. Working with this kind of heat, controlling the temperature of the workpiece is crucial to get the best results.
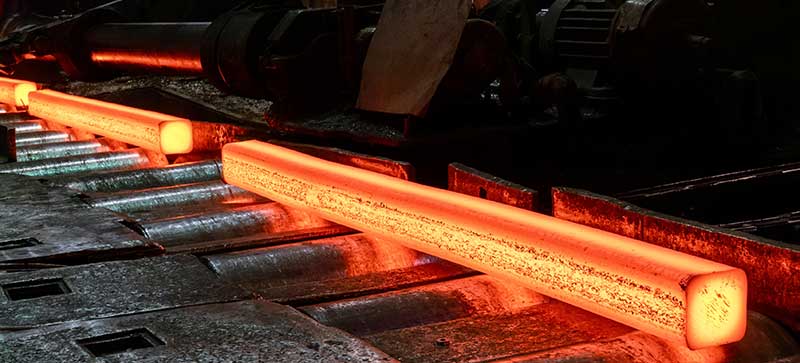
THE ESSENTIAL PROPERTIES OF HOT WORK STEEL
Hot work steel has to be able to withstand cycles of high heat and cooling down as well as keeping its mechanical properties.
Hot work tool steel has the ability to maintain its structural integrity, mechanical properties and dimensional stability when exposed to high temperatures.
Thermal fatigue occurs when parts are subjected to recurring high temperatures and cooling. Hot work steel has a resistance to thermal fatigue and can endure the constant change in temperatures.
Thermal conductivity is a very important property of hot work steel. Heat has to be distributed evenly as not to crack or warp the material and improve tool life as well as process stability.
Toughness is important for hot work steel as it not only has to withstand high heat but also impact at the same time. Toughness is important to keep the ductility needed when great forces are used on the workpieces.
Hot working metals have a good hardness to give it the needed wear resistance, durability and edge retention and has to be carefully balanced with toughness to ensure an overall reliability.
Fatigue resistance is needed when parts or workpieces are exposed to repeated or cyclic stresses.Hot work steels have to resist high temperatures as well as mechanical stresses.
The combination of toughness, formability, a refined grain structure, balanced hardness and suitable heat treatment adds to the high impact strength of hot work tool steel grades and makes them indispensable for reliable and long-lasting performance in demanding industrial environments.
Applications like hot forging, hot extrusion or die casting expose the material to tough working conditions. High wear resistance ensures a long service life by maintaining shape, dimension and integrity.
Hot work tool steel has the ability to maintain its structural integrity, mechanical properties and dimensional stability when exposed to high temperatures.
Thermal fatigue occurs when parts are subjected to recurring high temperatures and cooling. Hot work steel has a resistance to thermal fatigue and can endure the constant change in temperatures.
Thermal conductivity is a very important property of hot work steel. Heat has to be distributed evenly as not to crack or warp the material and improve tool life as well as process stability.
Toughness is important for hot work steel as it not only has to withstand high heat but also impact at the same time. Toughness is important to keep the ductility needed when great forces are used on the workpieces.
Hot working metals have a good hardness to give it the needed wear resistance, durability and edge retention and has to be carefully balanced with toughness to ensure an overall reliability.
Fatigue resistance is needed when parts or workpieces are exposed to repeated or cyclic stresses.Hot work steels have to resist high temperatures as well as mechanical stresses.
The combination of toughness, formability, a refined grain structure, balanced hardness and suitable heat treatment adds to the high impact strength of hot work tool steel grades and makes them indispensable for reliable and long-lasting performance in demanding industrial environments.
Applications like hot forging, hot extrusion or die casting expose the material to tough working conditions. High wear resistance ensures a long service life by maintaining shape, dimension and integrity.
WHAT ARE HOT WORKING PROCESSES?
The following methods are metal forming processes at a high temperature and also shows some of the stresses tools are exposed to when used in those operations.
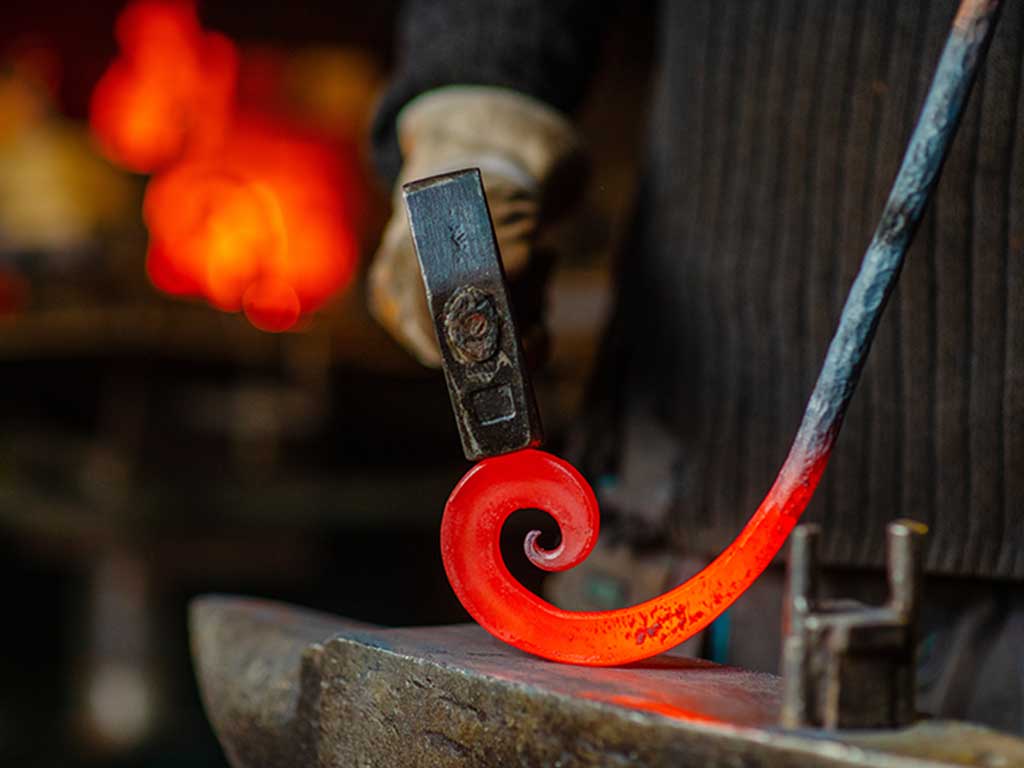
Hot Forging
Forging with dies is carried out by hitting the material with a hammer or by applying high pressure from a forging press.
In addition to withstanding the temperatures of the forging, the die must have good mechanical properties such as toughness in order to withstand the pressures or blows.
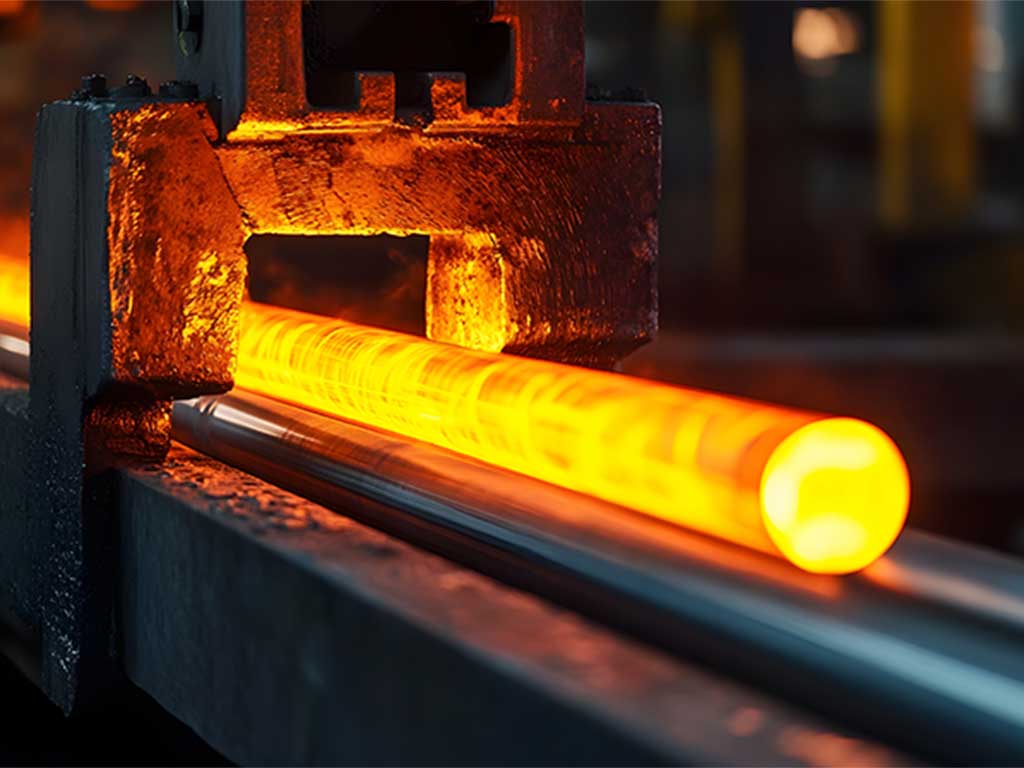
Hot Rolling
During hot rolling, heated steel is rolled between rollers to the desired shape and thickness.
Due to the contact heat and the required pressure, the rolls must not deform, break or crack.
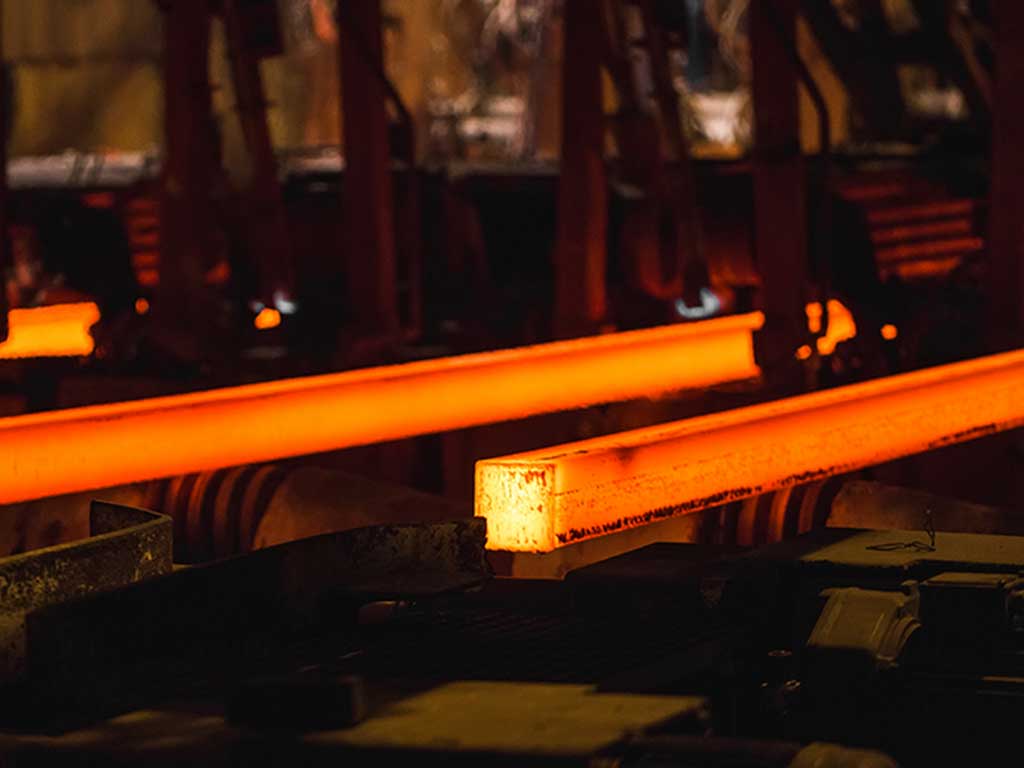
Extrusion Molding
During the hot extrusion of steel a hollow or full bodied piece of metal is pushed through a die to produce rods, wires, tubes, and contoured profiles.
The dies used for extrusion molding have to have durability and toughness as well as high heat resistance with the constant passing of hot materials and pressures used to do this.
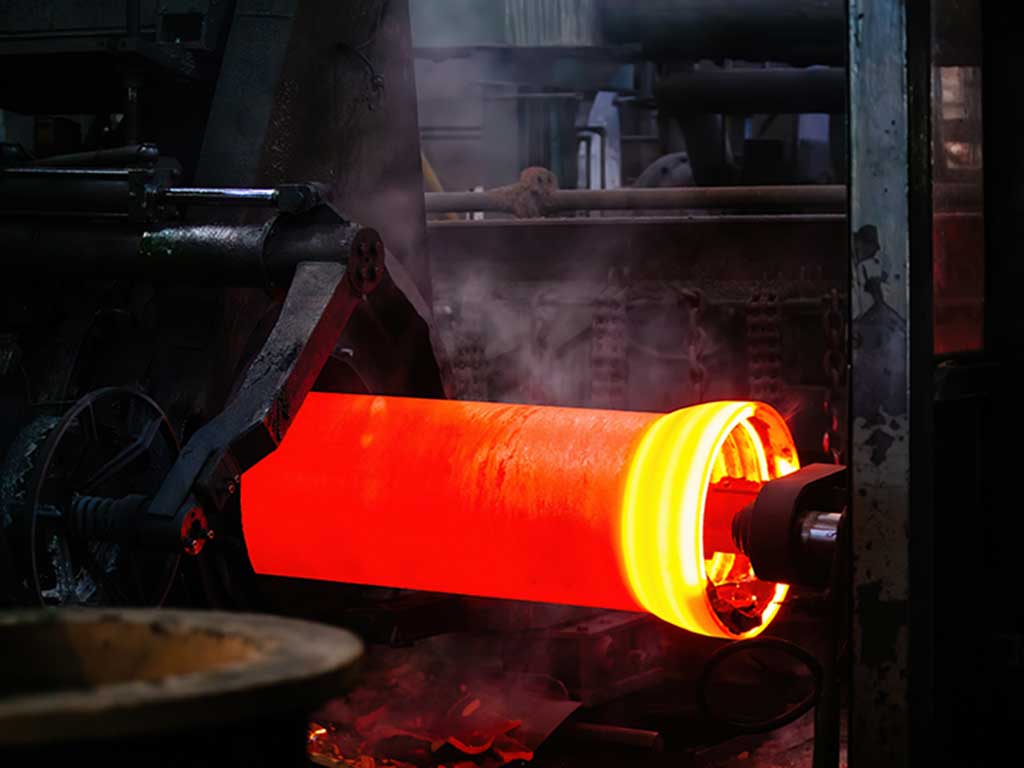
Drawing
During this process heated material is drawn through a die to increase its length.
Dies and tools used to draw hot material have to be heat resistant, and wear resistant to keep the exact shape for the continuous production of precise parts.
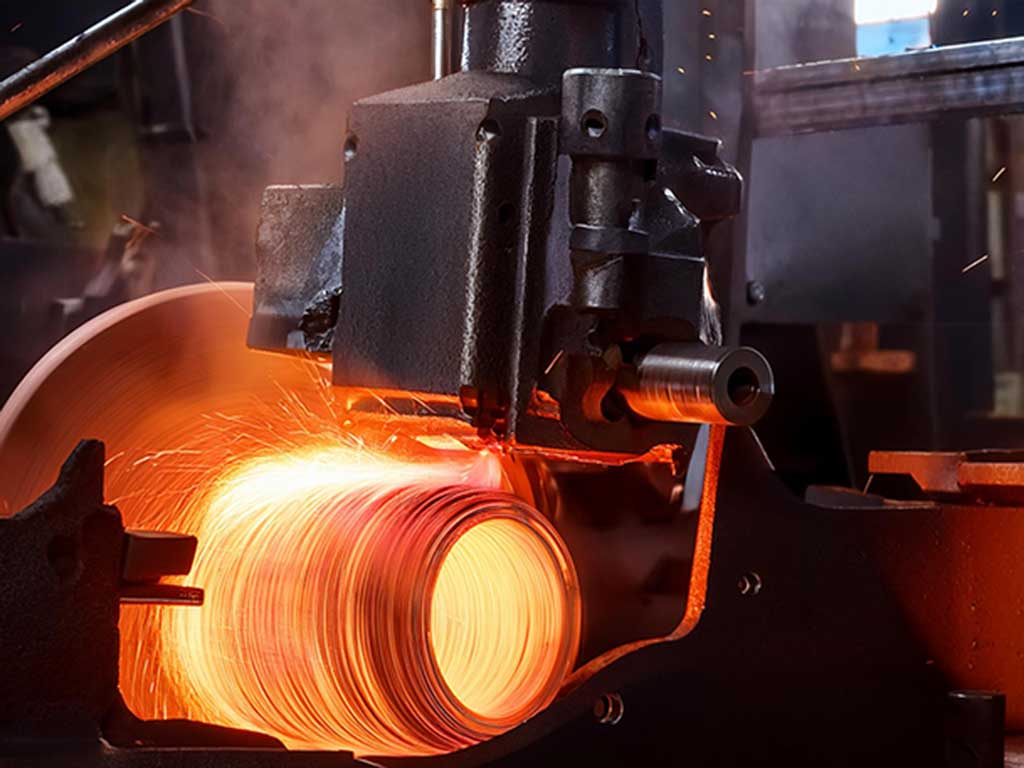
Hot spinning
Hot spinning, the metal which needs to be formed rotates while it is heated by an external heat source and then formed by pressure.
The tools used to form the metal are usually made from hot work steel so as not to be affected by the heat the material reaches.
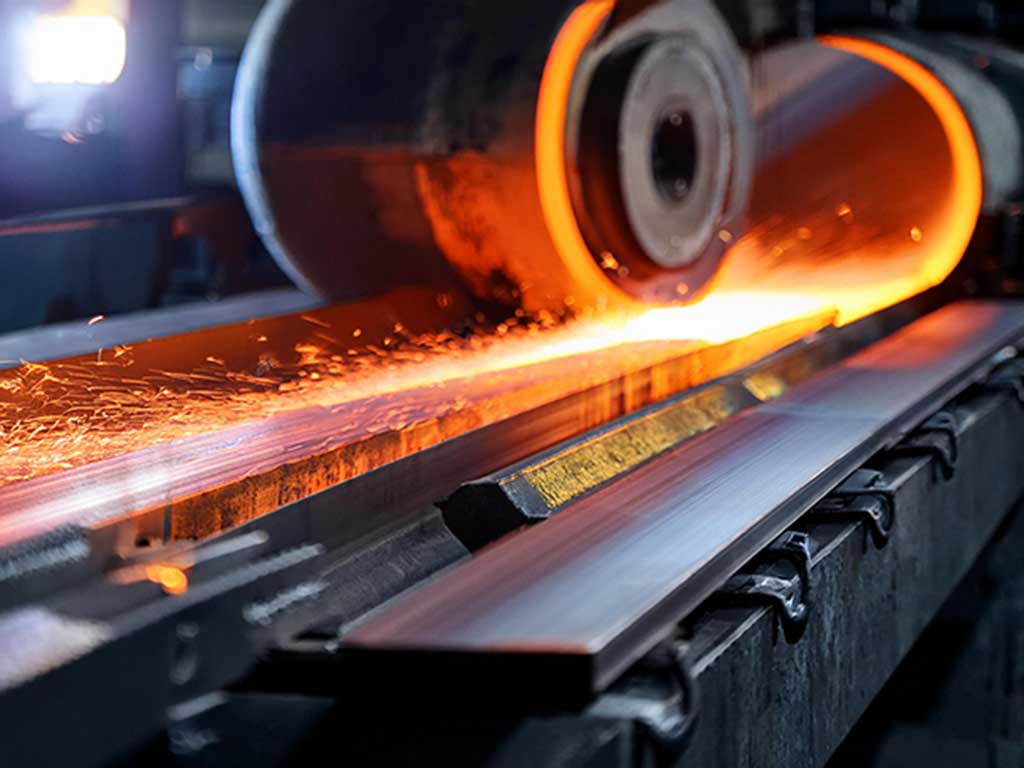
Rotary Piercing
Rotary piercing is used to produce seamless pipes. The heated billet passes through to cross rollers and then gets pushed onto a piercer.
By this process the billet gets hollowed out without creating a seam. The cross rollers and piercer are made from hot working tool steel.
DISTINCTION FROM COLD WORKING
The main difference to cold work steel is the working temperature. Cold work steel is used to work at and around room temperature while hot work steel is used above the recrystallization temperature and very high temperatures.
Hot work steel vs cold work steel | |
Hot working steel | Cold working steel |
Working temperature is above recrystallization temperature. | Working temperature is below recrystallization temperature. |
Retains its hardness at high temperatures. | Retains its hardness during work at and around room temperature. |
Retains its wear resistance at high temperatures. | Retains its wear resistance at low temperatures. |
To prevent thermal fatigue or cracking under heavy loads, hot work steel retains its toughness at high temperatures. | Though harder and more brittle, cold work steel still has a toughness sufficient for cold work. |
Resistant to thermal fatigue. | Less resistant to thermal fatigue. |
Resistant to oxidation. | Resistance to oxidation is not needed due to the working temperatures. |
Rougher surface due to scaling and oxidation | Smoother surface, no scaling or oxidation |
Good dimensional accuracy | Better dimensional accuracy |
COMMON GRADES OF HOT WORK STEEL
Tool steels like H10, H13, L6 and S7 are used for hot works like hot forging, extrusion or rotary piercing.
HOT WORK STEEL CHART
Below you can find our portfolio with all our hot work steels. We offer a suitable type of hot steel for many applications. If you require other grades, please feel free to contact us.
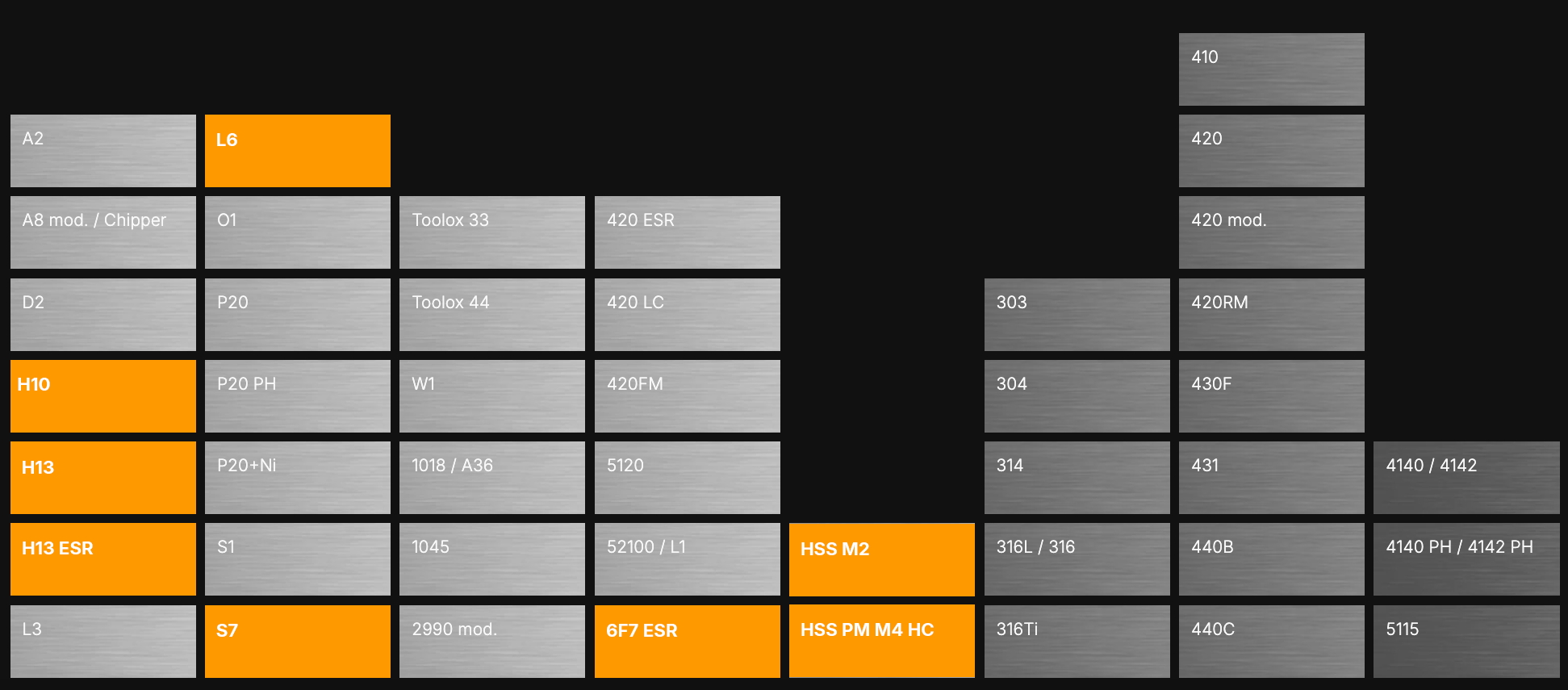
Hot work grades | Properties | Applications | |
H10 | • 32CrMoC12-28 • High machinability • High wear resistance • Working temperature: 68 – 842 °F Working hardness: • 50 HRC - 52 HRC • Delivery condition: max. 229HB | • Brass casting • Tube extrusion mandrels • Piercer plugs • Hot shear knives | |
H13 | • X40CrMoV5-1 • Good machinability • Working temperature: 68 – 932 °F Working hardness: • 50 HRC - 56 HRC • Delivery condition: max. 229HB | • Hot extrusion tools • Die casting tools • Light metal die casting • Plastic Molds | |
H13 ESR | • X40CrMoV5-1 • High toughness • Good machinability • Working temperature: 68 – 932 °F Working hardness: • 50 HRC - 56 HRC • Delivery condition: max. 229HB | • Forging tools • Extrusion press tools • Press mandrels • Screw and rivet production | |
L6 | • 55NiCrMoV7 • High toughness • Good machinability • Working temperature: 68 – 752 °F Working hardness: • 40 HRC - 54 HRC • Delivery condition: max. 250HB | • Forging dies • Punch heads • Die holders • Pressure plates | |
S7 * | • 50CrMoV13-1 • Good machinability • Working temperature: 68 – 752 °F Working hardness: • 56 HRC - 60 HRC • Delivery condition: max. 225HB | • Cutting tools • Plastic molding dies • Shear blades • Driver bolts | |
6F7 ESR * | • 45NiCrMo16 • High toughness • Working temperature: 68 – 572 °F Working hardness: • 50 HRC - 54 HRC • Delivery condition: max. 260HB | • Cold hobbing tools • Cutlery punches • Embossing tools • Cold shear knives | |
HSS M2 * | • HS6-5-2C • High wear resistance • Working temperature: 68 – 1022 °F Working hardness: • 62 HRC - 65 HRC • Delivery condition: max. 270HB | • Broaching tools • Milling cutters • Twist drills • Screw taps | |
HSS M4 HC * | • ~PMHS6-5-4 • High wear resistance • Working temperature: 68 – 932 °F Working hardness: • 62 HRC - 65 HRC • Delivery condition: max. 270HB | • Stamping tools • Screw dies • Countersinks • Broaching tools |
(* these steel grades can be used for cold work as well as for hot work)
VARIOUS TYPES OF STEEL FOR HOT WORKING
Hot work steel is one of the three main categories of tool steel, the other two are cold work and plastic mold steel.
TOOL STEEL FOR HOT WORKING
Hot work tool steel, with its special properties like maintaining its mechanical properties during high temperatures, thermal fatigue resistance or wear resistance, can be used in a wide range of high temperature applications like forging dies, extrusion dies or hot shearing tools. This makes hot working tool steel the choice for industries like the automotive and manufacturing industry.
WHAT ARE THE EFFECTS OF HOT WORKING STEEL?
Hot working gives the steel a more uniform and finer grain structure for better mechanical properties.The finer grain structure improves ductility and toughness making it more pliable and less susceptible to cracking.
It can reduce impurities and improve structural integrity. The reduction of internal stresses improves dimensional stability and during the hot working of metal the material is not strain hardened due to the high temperatures used.
Initially the yield strength is reduced due to the softening of the material. The recrystallization process and the finer grain structure though can enhance the yield strength after cooling down. A post heat treatment can further support the enhancement of the yield strength.
Elevated temperatures result in the softening of the material causing recrystallization and therefore forming new grains as well as eliminating strain hardening.
The material is more malleable, easier to deform, has uniform mechanical properties, a better grain structure, less flow stresses and the applied pressure reduces porosity. The hot working process also eliminates impurities by breaking them up or pushing them out during the process.
The hot working of metal is done above the recrystallization temperature but below the melting temperature. The temperatures that are being allowed are different for the various steel grades.
If the chosen temperature is too low for the particular steel it might not be ductile enough for the needed metal forming process. Too hot on the other hand might promote unwanted grain growth and can reduce needed properties of the end product.
Choosing the correct temperature is crucial for the tool as well as the end product. So the lower limit temperature as well as the upper limit temperature depend on the used material and the properties needed.
WHAT ARE THE ADVANTAGES AND DISADVANTAGES OF HOT WORK STEEL?
Like any process, hot working has some advantages but also disadvantages. Find some of them below.
Advantages | Disadvantages |
High temperature strength: Suitability of the material for high heat applications with the retention of strength and hardness | Surface oxidation and scaling: Due to the high temperatures the surface can oxidate and form scale. This does lead to an additional work step to eliminate the scaling. |
Enhanced toughness and ductility: Due to a finer grain structure hot work steel has a better toughness and ductility, preventing cracking and breaking while absorbing high impacts. | Dimensional accuracy: To achieve precise dimensional tolerances can be challenging as hot worked material might experience thermal expansion. |
Grain refinement: Hot working leads to a more uniform and finer grain structure. This improves the mechanical properties of the material. | Energy consumption: To maintain the hot working temperature a significant energy input is needed. |
Reduction of internal stresses and defects: Hot worked metal has fewer internal stresses and defects. | Potential of grain growth: Uncontrolled temperatures during the hot working process can lead to grain growth and the reduction of mechanical properties. |
Longer tool life: With its resistance to high temperatures and wear, tools made from hot worked steel have a longer tool life. | Material loss due to scaling: If the material scales during hot working it may require additional machining resulting in possible material loss. |
SUMMARY
Hot working steel is used for a multitude of hot working applications like hot rolling, hot spinning or rotary piercing. Due to its toughness and ductility it is used in a variety of applications and industries.
• Temperature above the recrystallization
• Enhanced mechanical properties
• Refined grain structure
• Reduced internal stresses and defects
• Less flow stresses
• No strain hardening
• Longer tool life
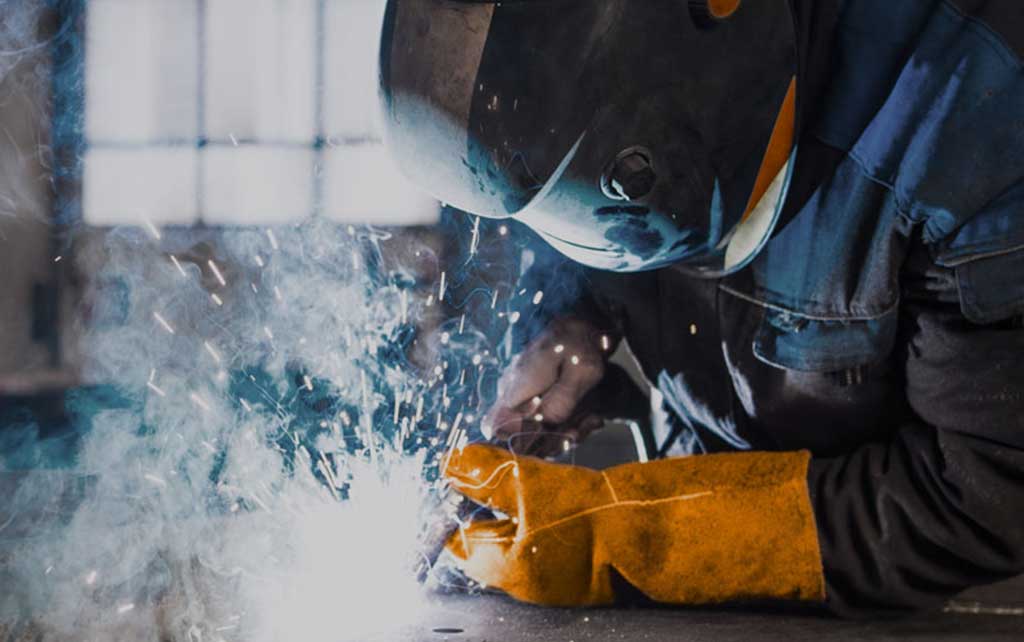
ABRAMS INDUSTRIES® HOT WORK STEEL
As a steel supplier with no minimum order quantity or value we have been supplying steel to a wide variety of industries and manufacturers in Germany since 2003, Europe since 2011 and now since 2020 across the U.S.A. and Canada.
We pride ourselves in supplying you with precision in tool steel, high speed steel, stainless steel, heat-treatable steel and case hardening steel in 44 steel grades with 83,928 dimensions.
As a hot work steel supplier we saw, mill and grind for you in our Warehouse in Illinois.
Customized hot work steel
Hot work steel plates
Hot word steel rods
ABRAMS INDUSTRIES® INC. - YOUR STEEL PARTNER
Your success is our success!
References:
Hot work tool steel, by Joachim Schlegel and Till Schneider (Print): https://www.lehmanns.de/shop/technik/63441267-9783658430153-hot-work-tool-steel
Metallurgy for dummies. Metal Hot Working Process. [Online]: https://www.metallurgyfordummies.com/metal-hot-working-process.html
Verhoeven, John (2007). Steel Metallurgy for the Non-Metallurgist [Online Reading sample]: https://books.google.de/books?id=brpx-LtdCLYC&pg=frontcover&redir_esc=y#v=onepage&q&f=false