2990 mod. Tool Steel - 1.2990 mod. - X100CrMoV8-2
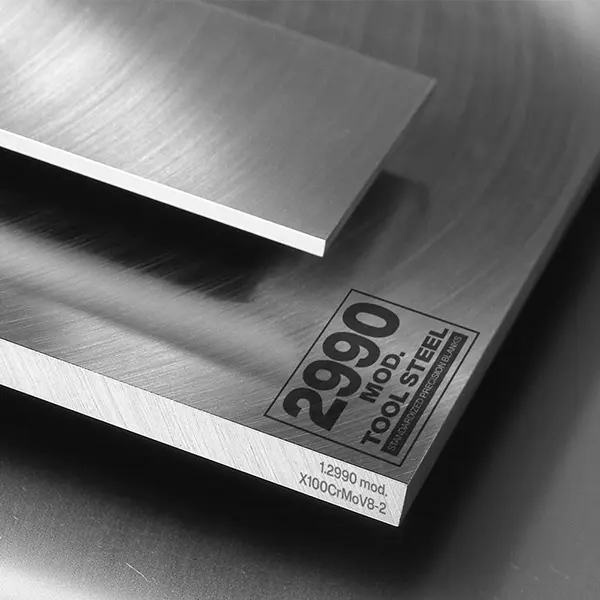
2990 mod. Tool Steel - 1.2990 mod. - X100CrMoV8-2
Back to Steel OverviewGround Flat Stock and $mart Flat Stock comes always in a machined condition, that means:
NO decarburization on the surfaces (decarburization leads to unreliable components and tools)
Less dirt on your machines during further processing – nothing but clean chips
Stress-relieved flat steel avoids warping of components during further machining
Get the close-to-finish-size thickness and width you need for the components you plan
Ground Flat Stock and $mart Flat Stock comes always in a machined condition, that means:
NO decaburization on the surfaces (decarburization leads to unreliable components and tools)
Less dirt on your machines during further processing – nothing but clean chips
Stress-relieved flat steel avoids warping of components during further machining
Get the close-to-finish-size thickness and width you need for the components you plan
Ground Flat Stock and $mart Flat Stock comes always in a machined condition, that means:
NO decaburization on the surfaces (decarburization leads to unreliable components and tools)
Less dirt on your machines during further processing – nothing but clean chips
Stress-relieved flat steel avoids warping of components during further machining
Get the close-to-finish-size thickness and width you need for the components you plan
2990 MOD. STEEL PRICE CHART

2990 mod STANDARD VALUES
C
Cr
Mo
V
X100CrMoV8-2
57 HRC - 63 HRC
max. 250 HB
X100CrMoV8-2
57 HRC - 63 HRC
max. 250 HB
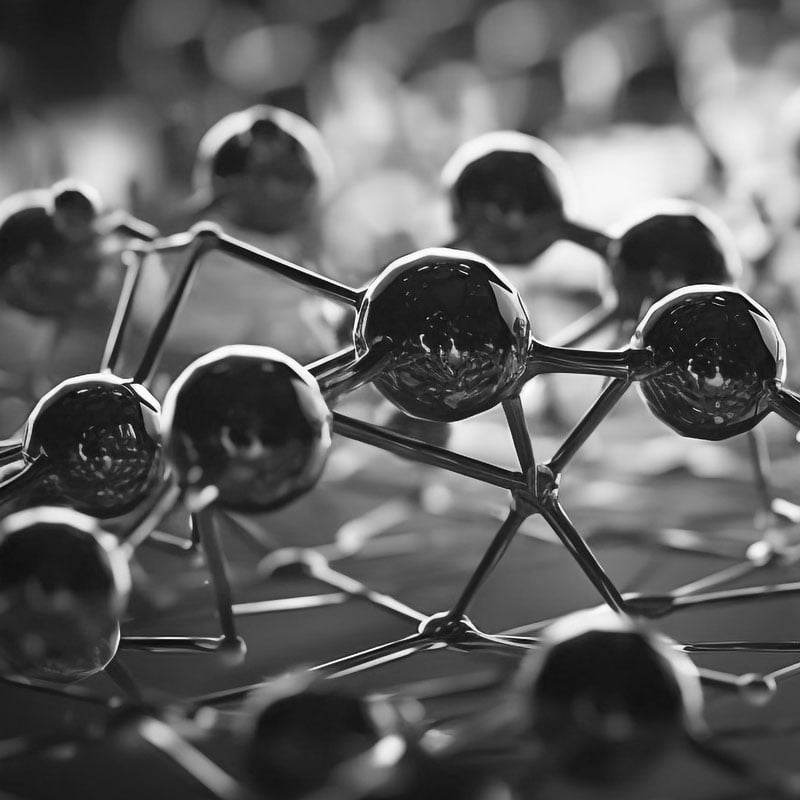

2990 mod. PHYSICAL PROPERTIES
Tool steel 2990 mod. has compared to 12% Cr steels and conventional 8% Cr steels finer and more evenly distributed carbides. The more homogeneous structure improves machinability and toughness. Due to the lower carbon and chromium content the ledeburitic 2990 mod. can be easily machined, has a lower scrap time, low tooling costs, less edge chipping, good production reliability and good tool life.
To be classed as a stainless steel a mass fraction of a minimum of 10.5% of chromium is needed. The 2990 mod. has a mass fraction of 8% and can therefore not be classed a stainless steel.
Tool steel 2990 mod. has some corrosion resistance, though to be classed as a corrosion resistant steel it has to have a chromium content of at least 10.5%, the 2990 mod. only has 8% of chromium and cannot be put into the category of stainless steels.
As a ferromagnetic metal the 2990 mod can be magnetized. Grinding, milling and eroding for example can be done on machines using magnetic clamping.
The wear resistance for tool steel 2290 mod. is a 6 on a scale where 1 is low and 6 is high.

2990 mod. TECHNICAL PROPERTIES
Due to its high hardness the 2990 mod. has an excellent edge retention and wear resistance. On the other hand its hardness makes it harder to grind and sharpen. It offers good toughness which reduces the risk of chipping or breaking. Though it has some corrosion resistance it has to be regularly maintained to protect the material in corrosive environments. Regular cleaning and oiling can help when maintaining the 2990 mod.
The working hardness for tool steel 2990 mod. is 592 - 681 BHN (57 - 63 HRC)
The tensile strength for 2990 mod. tool steel is approx. 123.2 KSI (0.145KSI = 1MPa). This value is the result from a tensile test to show how much force is needed before the material starts to stretch or elongate before it breaks.
The following table shows the thermal conductivity of tool steel 2990 mod. at various temperatures.
Heat conductivity table | |
Value | By temperature |
24.0 | 68°F |
25.9 | 212°F |
26.8 | 302°F |
27.1 | 392°F |
27.4 | 572°F |
27.2 | 752°F |
26.8 | 932°F |
This diagram shows how much tool steel 2990 mod. might expand or contract when the temperatures change which can be very important when working with high temperatures or strong temperature changes.
Medium thermal expansion coefficient | |
10-6m/(m • K) | At a temperature of |
11.4 | 68 - 212°F |
11.6 | 68 - 302°F |
11.7 | 68 - 392°F |
12.0 | 68 - 572°F |
12.3 | 68 - 752°F |
12.4 | 68 - 842°F |
12.6 | 68 - 932°F |
The specific heat capacity of the 2990 mod. at room temperature is 0.49 J/g-°C (0.117 BTU/lb-°F). This value shows how much heat is needed to heat 1lb of material by 1 Fahrenheit
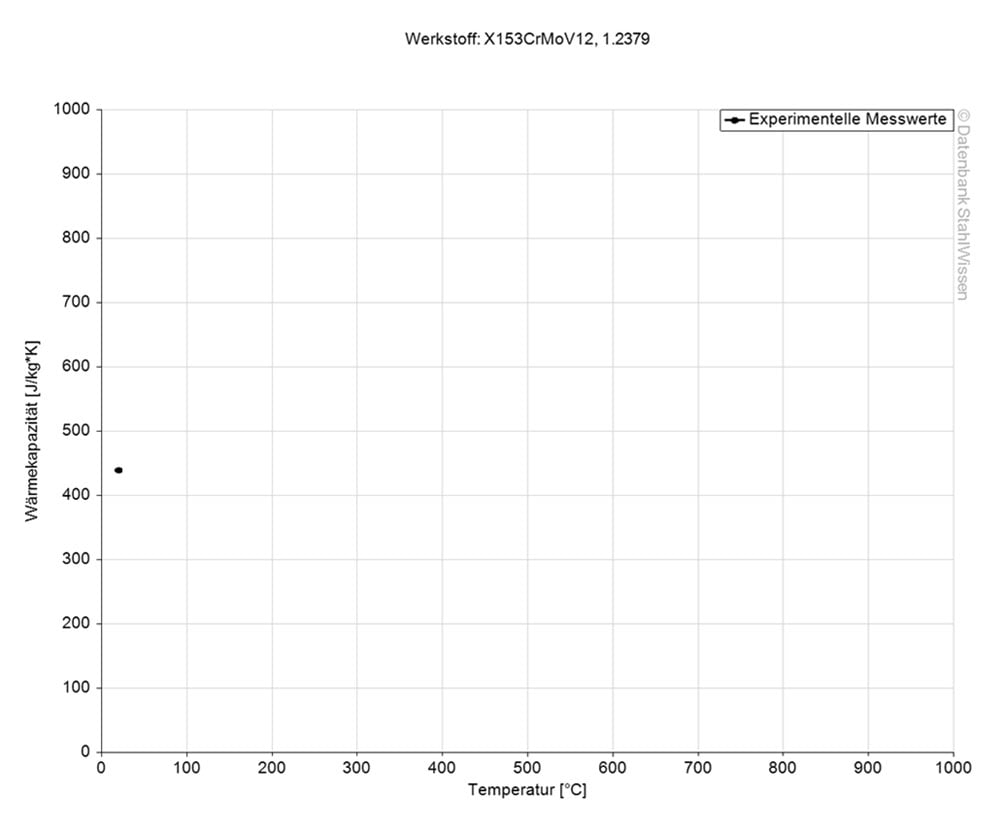
You can find the temperature dependent material constant (Resistivity) in the following table. The electrical conductivity is the reciprocal value of the specific resistance.
Table of the specific electrical resistivity | |
Value | At a temperature of |
0.64 (Ohm*mm²)/m | 68°F |
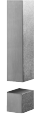
ABRAMS STEEL – QUALITY THAT WILL IMPRESS YOU!
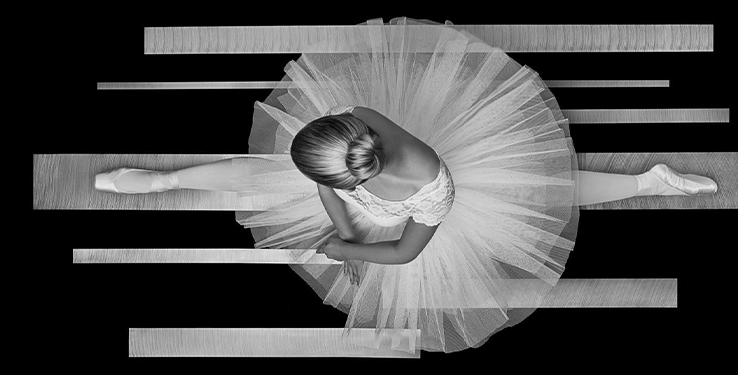
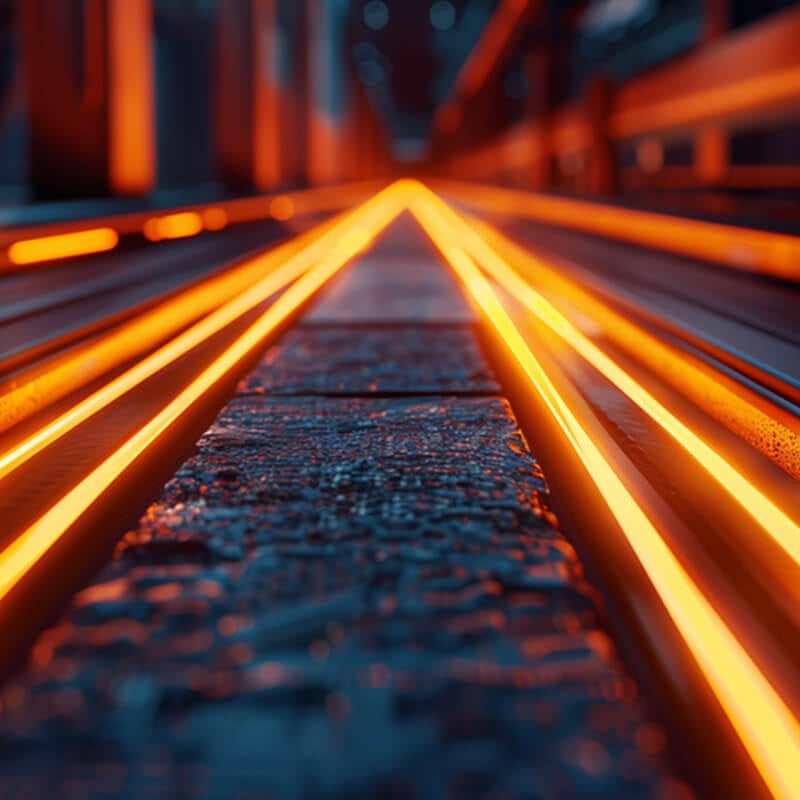

2990 mod. PROCEDURE
2290 mod. tool steel is typically air hardened in a vacuum furnace but can also be hardened by using a gas or electric furnace with or without a controlled atmosphere wrapped in stainless foil or salt bath hardened immersing the work piece in high temperature salts.
Heat the material uniformly to a temperature of 1475 - 1550°F (800 - 850°C) and hold for 2 hours. Follow this up with a slow cool in the furnace to below 930°F (500°C), then remove it from the furnace and continue cooling in still air to ambient temperature.
To relieve stresses brought on by e.g., heavy machining, heat the part uniformly to a temperature of 1200°F (650°C) and hold 1-2 hours in a neutral atmosphere. Cool slowly in the furnace.
Heat the material uniformly to a temperature of 1900 - 1940°F (1040 - 1060°C) and hold for 15 - 30 minutes. Hardening can be done for example in a salt bath, compressed air, air, and vacuum:
Air hardening
Preheat the material uniformly to a temperature of 1475°F (800°C), then increase the temperature to 1885°F (1030°C). Parts smaller than 1 inch (25.4 mm) can be soaked for up to one hour, parts up to 4 inches (101.6 mm) for 25 - 30 minutes per inch (25.4 mm). For parts over 4 inches (101.6 mm) thickness in cross section, soaking time should be 10 - 25 minutes per inch (25.4 mm) of thickness. Then quench with inert gas pressure, for example nitrogen, then cool rapidly with 2 bar atmosphere pressure or high velocity equivalent.
Salt bath hardening
Preheat the part uniformly to 1550°F (850°C) and soak in the molten salt bath at 1885°F (1030°C)for a minimum of 5 minutes. Then quench in salt and let the temperature cool in still air to 120 - 150°F (45 - 65°C) before tempering.
Tool steel 2990 mod. can be quenched with the following:
• Air
• Oil
• Hot basin (932 - 1022°F / 500 - 550°C)
Double temper the 2990 mod. with a cool to ambient temperature between subsequent tempers. A third tempering at 750°F (400°C) can be added on to the initial heat treatment, if distortion from machining, surface treatment or EDM is a concern. The third temper is not necessary if parts have been hardened in the salt bath.
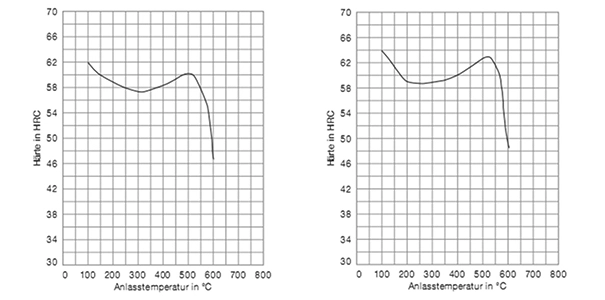
Treating the 2990 mod. at a temperature of -300°F (-185°C) between the first and second temper can be beneficial to the toughness of the workpiece.
Note: Sub-zero treatment should always be followed by a temper.
The following diagram shows the micro changes over time at different temperatures which are important during heat treatment. They show the optimum conditions for the processes such as hardening, annealing and normalizing.
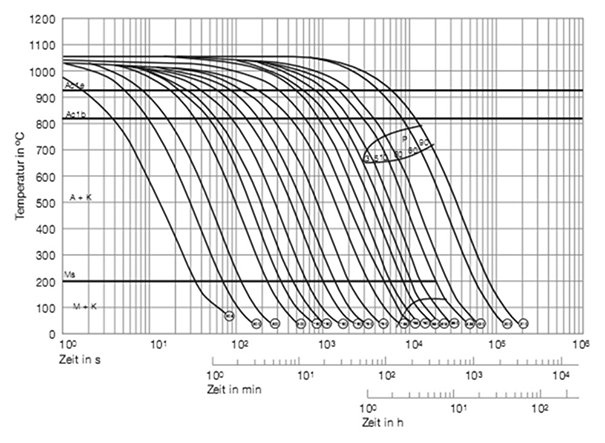

2990 mod. SURFACE TREATMENT
Nitriding gives the surface of this material grade a hard layer with an excellent resistance to wear and galling. To suit the application, the thickness of the layer should be considered well.
Physical vapor deposition (PVD) is a process applying a thin wear resistant coating to the material / work piece at a temperature range of 390 - 930°F (200 - 500°C).
Chemical vapor deposition (CVD) is a process that involves the reaction of a volatile precursor, which is usually injected under vacuum into a chamber. Heating the chamber to reaction temperature, causes the precursor gas to react or break down, which in turn coats and bonds with the material surface.
Thermal diffusion (TD) is the process of diffusing zinc into steel to form an anti-corrosive layer at the surface of the steel.

2990 mod. PROCESSING
As a non contact process removing material or shaping the 2990 mod. with EDM can eliminate distortion and stress conventional machining can cause. With optimized parameters, adequate electrodes, set up and tooling will produce high precision parts. Care should be taken not to cause surface cracking as this material grade has a high hardness already.
As for all metals the 2990 mod. expands and contracts with heating and cooling. Controlled heating during the hardening and tempering process as well as throughout the cooling period can minimize distortion and other dimensional changes. Furthermore reducing stress and/or allowing for dimensional changes by putting an allowance onto the dimensions should be considered.
Heat to forge to a temperature of 1650 - 2010°F (900 - 1100°C). It is recommended to anneal the workpiece after forging to ensure to minimize stresses and optimized heat treatment responses.
Low pre- and post-heating temperatures, in comparison to D2, will reduce weld cracking and make welding easier. The low hardness decline, in the affected zones, minimizes any deterioration in its performance.

2990 mod. APPLICATION OPTIONS
The 2990 mod. can be used in a variety of industries and applications like the automotive industry for components that require high wear resistance and strength. It can be used for dies and punches, molds and extrusion dies, blades and slitters as well as for woodworking tools.
• Blanking tools
• Stamping tools
• Precision cutting tools
• Dies, punches
• Thread rolling tools
• Cold pilger mandrels
• Plastic molds
• Cold rollings
• Cold extrusion tools
• Cold forming tools
• Deep drawing dies
• Woodworking tools
• Embossing tools
• Bending tools
• Machine knives
• Circular shear knives
• Machine parts
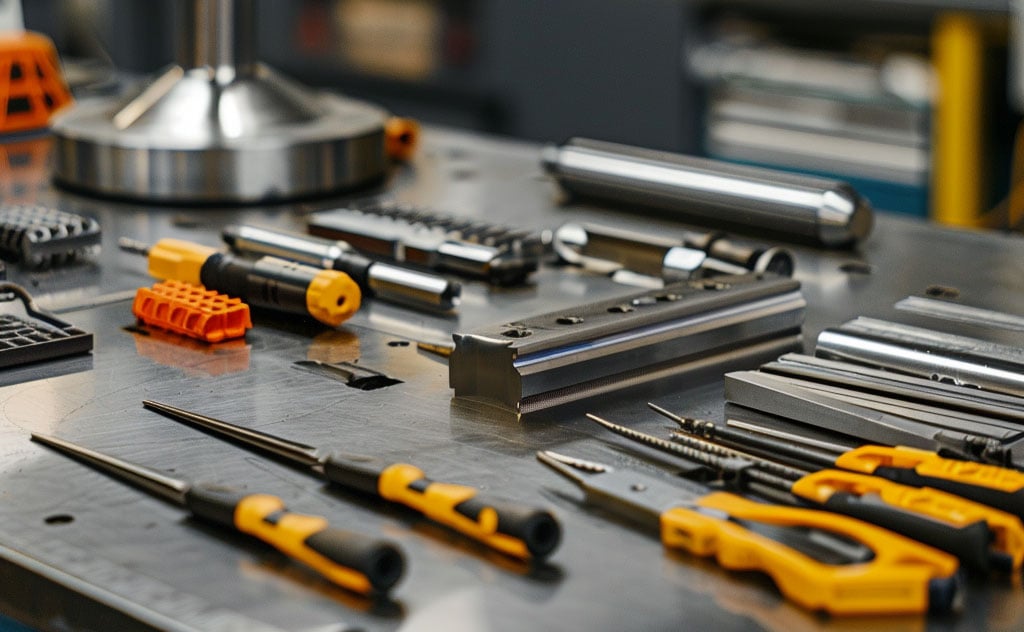

2990 mod. CONCLUSION
Tool steel 2990 mod. stands apart from other tool steels due to its unique combination of toughness, wear resistance and strength. It does achieve a high hardness without losing its toughness. Those properties make it a reliable choice for many applications where high performance, versatility and longevity is needed.
- High toughness
- Excellent compressive strength
- Excellent adhesive wear resistance
- Secondary hardening steel
- Low dimensional change
- Erodible
- Very good nitridability
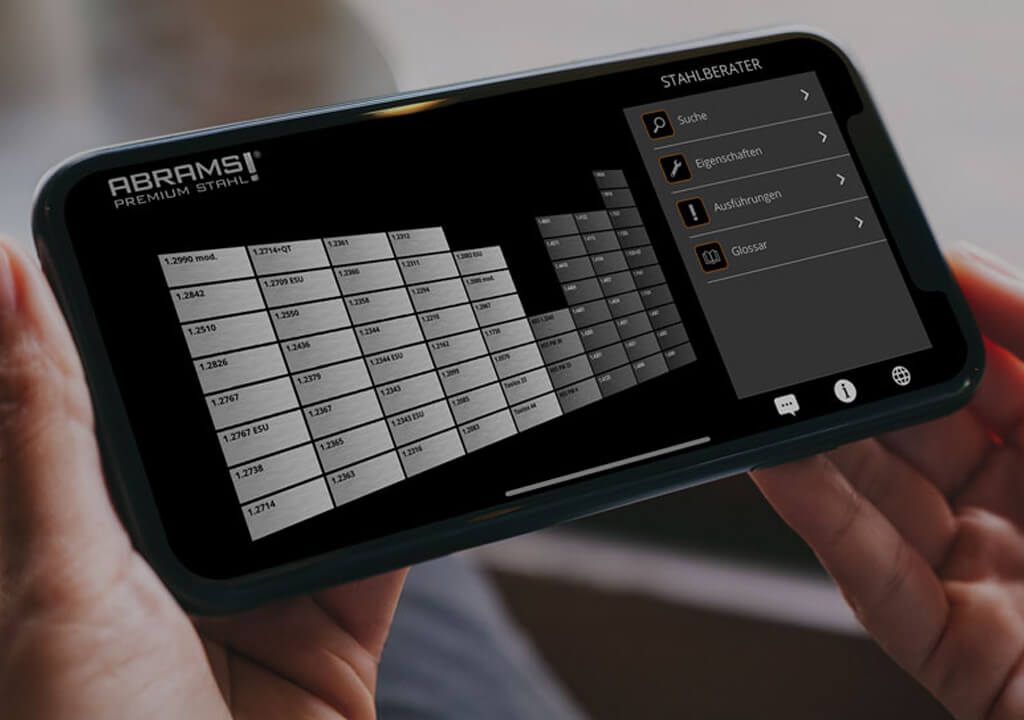

2990 mod. ALTERNATIVES
Are you looking for an alternative steel grade?
WE HAVE THE SOLUTION!
With the ABRAMS STEEL GUIDE, you can obtain an alternative or equivalent steel grade with just a few clicks.

2990 mod. DATASHEET
Download the technical data sheet in PDF format here.
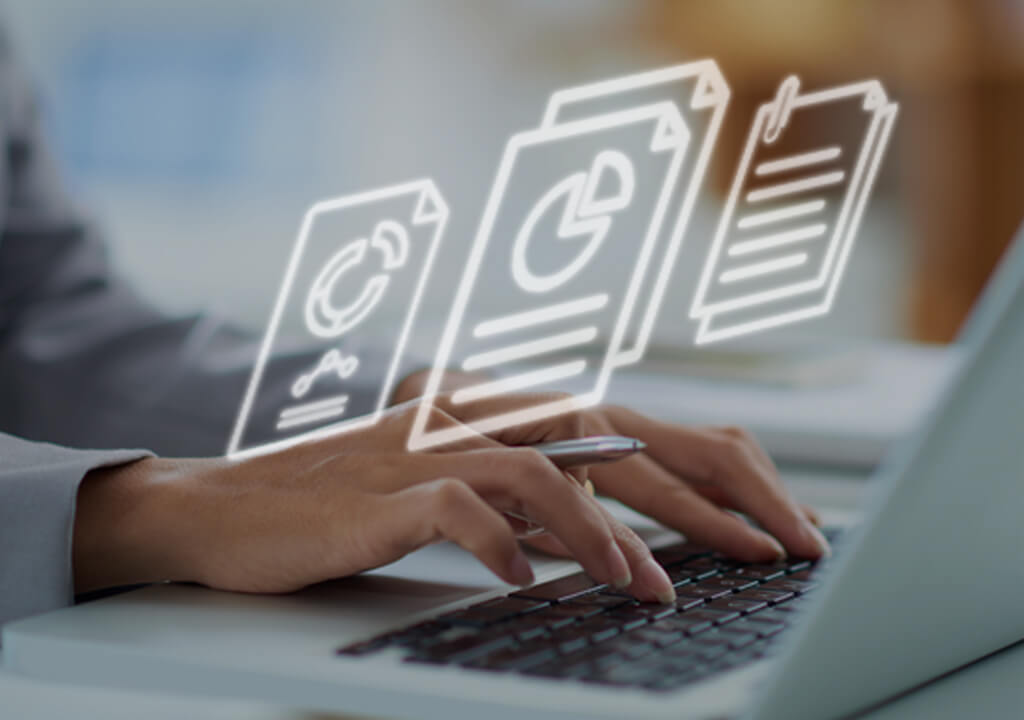
The data shown here has been compiled with the greatest diligence and is regularly updated with regard to the correctness and completeness of its content. The content is indicative only and should not be taken as a warranty of specific properties of the product described or a warranty of suitability for a particular purpose. All information presented is given in good faith and no liability will be accepted for actions taken by third parties in reliance on this information. ABRAMS Industries reserves the right to change or amend the information given here in full or parts without prior notice.