420 Stainless Steel - 1.4034 - X46Cr13 - 51420 - ~SUS 420J1
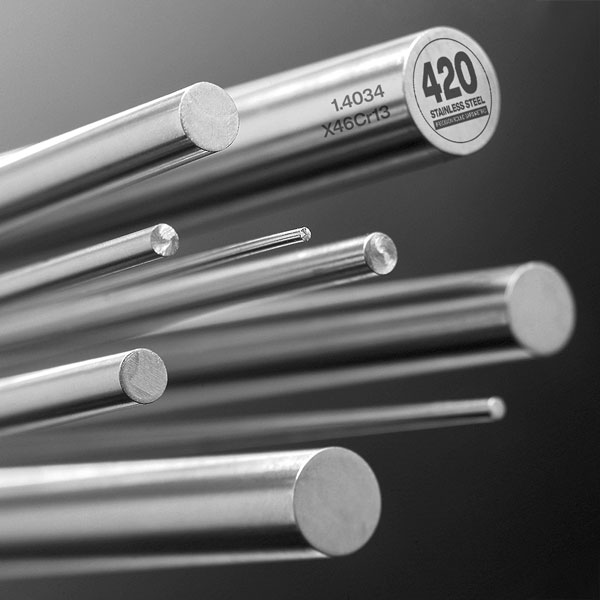
420 Stainless Steel - 1.4034 - X46Cr13 - 51420 - ~SUS 420J1
Back to Steel OverviewGround Flat Stock and $mart Flat Stock comes always in a machined condition, that means:
NO decarburization on the surfaces (decarburization leads to unreliable components and tools)
Less dirt on your machines during further processing – nothing but clean chips
Stress-relieved flat steel avoids warping of components during further machining
Get the close-to-finish-size thickness and width you need for the components you plan
Ground Flat Stock and $mart Flat Stock comes always in a machined condition, that means:
NO decaburization on the surfaces (decarburization leads to unreliable components and tools)
Less dirt on your machines during further processing – nothing but clean chips
Stress-relieved flat steel avoids warping of components during further machining
Get the close-to-finish-size thickness and width you need for the components you plan
Ground Flat Stock and $mart Flat Stock comes always in a machined condition, that means:
NO decaburization on the surfaces (decarburization leads to unreliable components and tools)
Less dirt on your machines during further processing – nothing but clean chips
Stress-relieved flat steel avoids warping of components during further machining
Get the close-to-finish-size thickness and width you need for the components you plan
420 STEEL PRICE CHART

420 STANDARD VALUES
C
Si
Mn
P
S
Cr
X46Cr13
50 HRC - 55 HRC
max. 241 HB
X46Cr13
50 HRC - 55 HRC
max. 241 HB
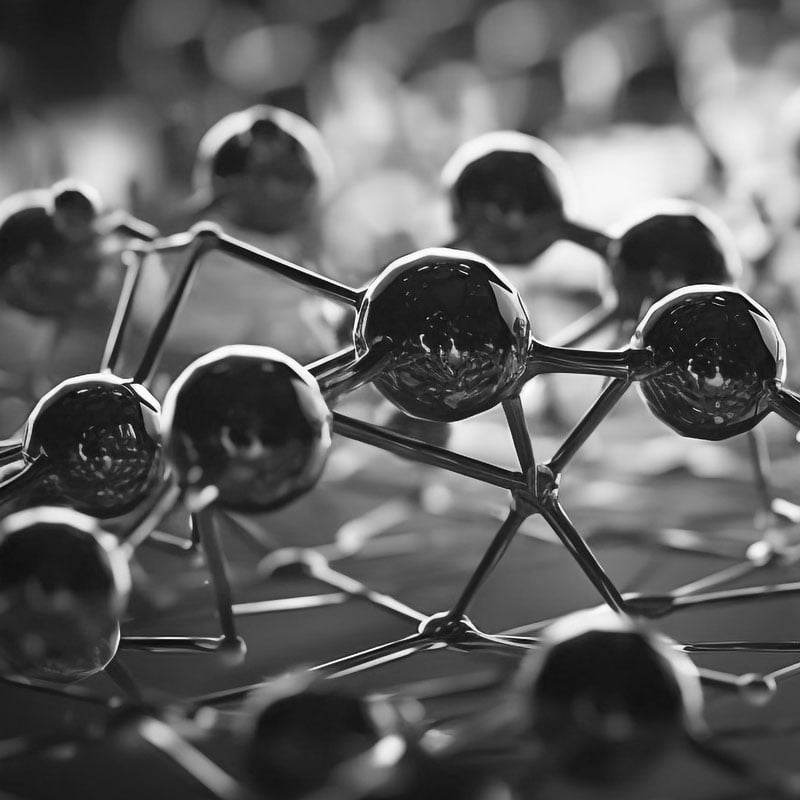

420 PHYSICAL PROPERTIES
420 stainless steel has, in its annealed condition, good ductility and can, when hardened, reach a hardness of min. 469 BHN (50 HRC). As a martensitic stainless steel 420 is optimized for its high hardness, while other properties are compromised to some degree. 420 loses ductility at sub-zero temperatures and is in comparison to austenitic steels less corrosion resistant, has poor weldability and loses strength when over-tempered at elevated temperatures.
Yes, the 420 is a martensitic stainless steel with a chromium content of approx. 12,5 to 14,5% of chromium which offers the corrosion resistance that makes it stainless.
420 stainless steel has a good resistance to water and steam, and a moderate resistance to corrosive environments free of chlorides. 420 is not resistant to intergranular corrosion after being welded or in its annealed condition. Where corrosion resistance is an issue, care should be taken not to over temper the material or to use it in its annealed condition, but to use it in the hardened condition with a high finished, smooth surface.
As a martensitic stainless steel the 420 has a crystal structure that is ferromagnetic, this makes the 420 magnetizable in its annealed and hardened condition. The 420 steel is suitable for magnetic clamping.
On a scale where 1 is low and 6 is high the 420 stainless steel comes in at 4.

420 TECHNICAL PROPERTIES
The 420 can be used as a knife steel. It is easily sharpened, has good corrosion resistance, and good toughness. One drawback is its edge retention which means it needs to be sharpened more often.
The working hardness for the AISI 420 stainless steel is in a range of 469 - 552 BHN (50 - 55 HRC).
Typically the density of 420 stainless steel is 0.278 lb/in3 (7.7g/cm3) at room temperature.
The tensile strength for the 420 is approx. 118.2 KSI (0.145KSI = 1MPa). This value is the result from a tensile test to show how much force is needed before the material starts to stretch or elongate before it breaks.
The yield strength shows how much stress can be applied to a material before it plastically deforms. Beyond this point it does not return to its original form when the stresses have been removed.The material deforms permanently or breaks past that point.
The range for the stainless steel 420 is between 74.4 to 200 KSI (512.9 - 1378.9 MPa).
The heat conductivity for the 420 stainless steel is at 30 W/(m*K) (208 BTU/(h-ft*°F)) at room temperature.
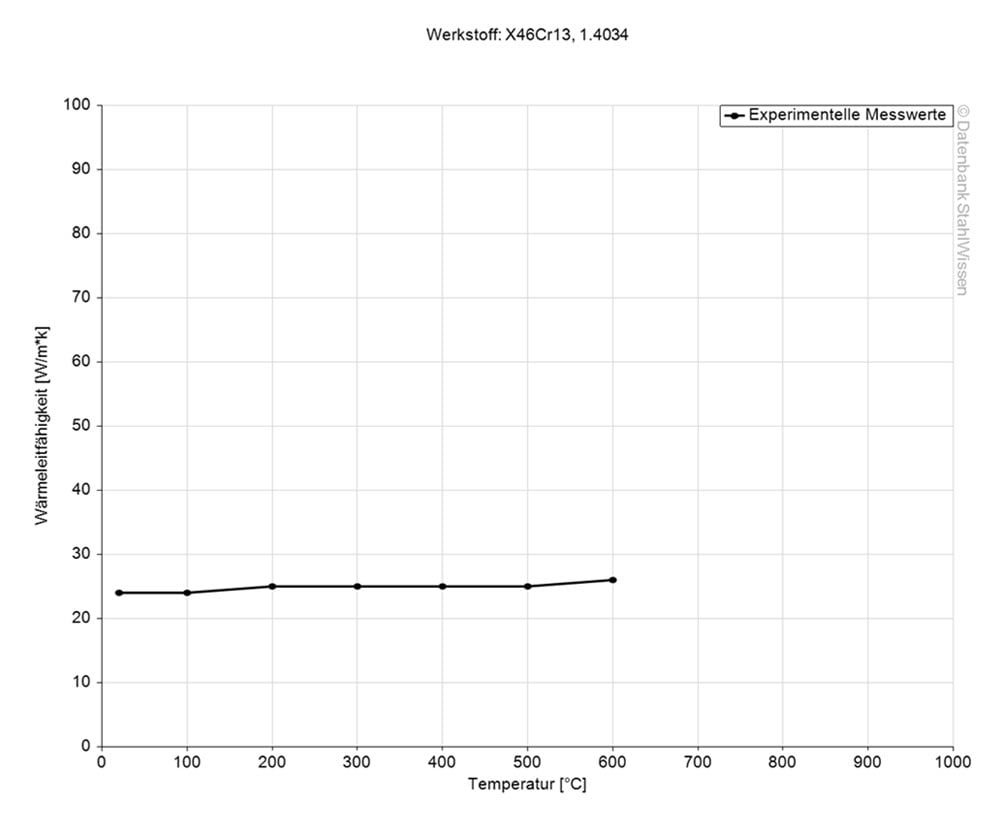
The thermal expansion coefficient shows how much the 420 might expand or contract when the temperature is changed. This is very important information, especially when working with high temperatures, or where there are strong temperature changes during applications.
Medium thermal expansion coefficient | |
10-6m/(m • K) | At a temperature of |
10.5 | 68 - 212°F |
11.0 | 68 - 392°F |
11.5 | 68 - 572°F |
12.0 | 68 - 752°F |
12.0 | 68 - 932°F |
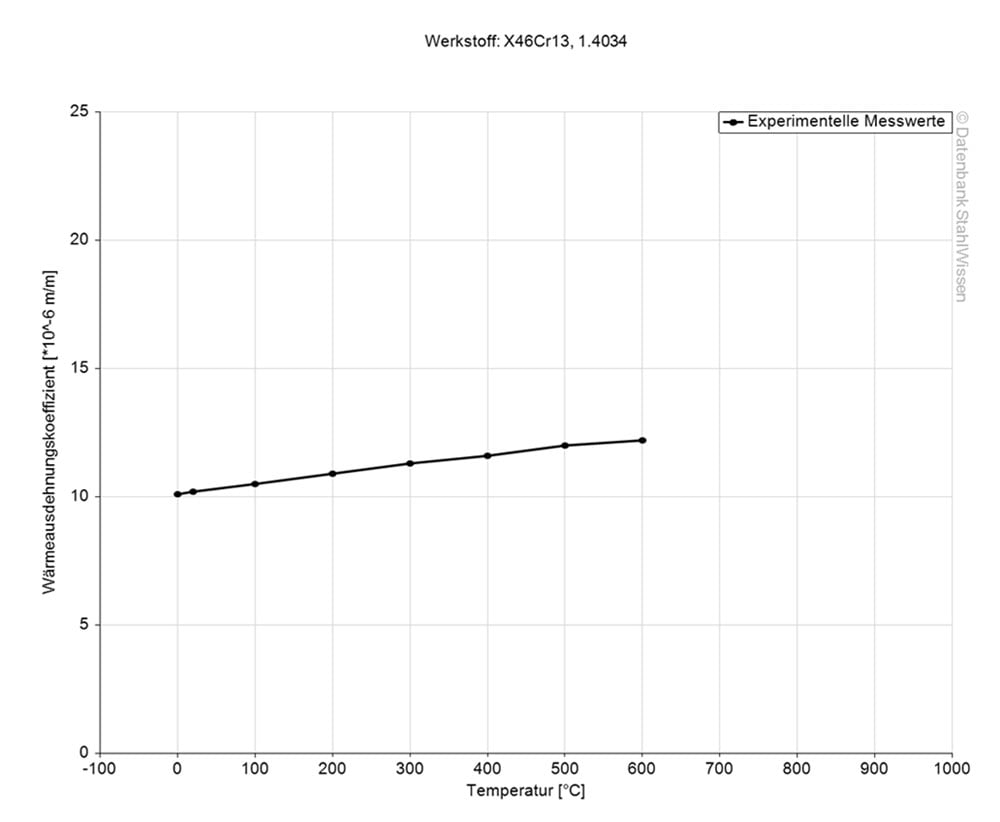
The specific heat capacity of the 420 stainless steel at room temperature is at 0.46 J/g-°C (0.109 BTU/lb-°F). This value shows how much heat is needed to heat 1lb of material by 1 Fahrenheit.
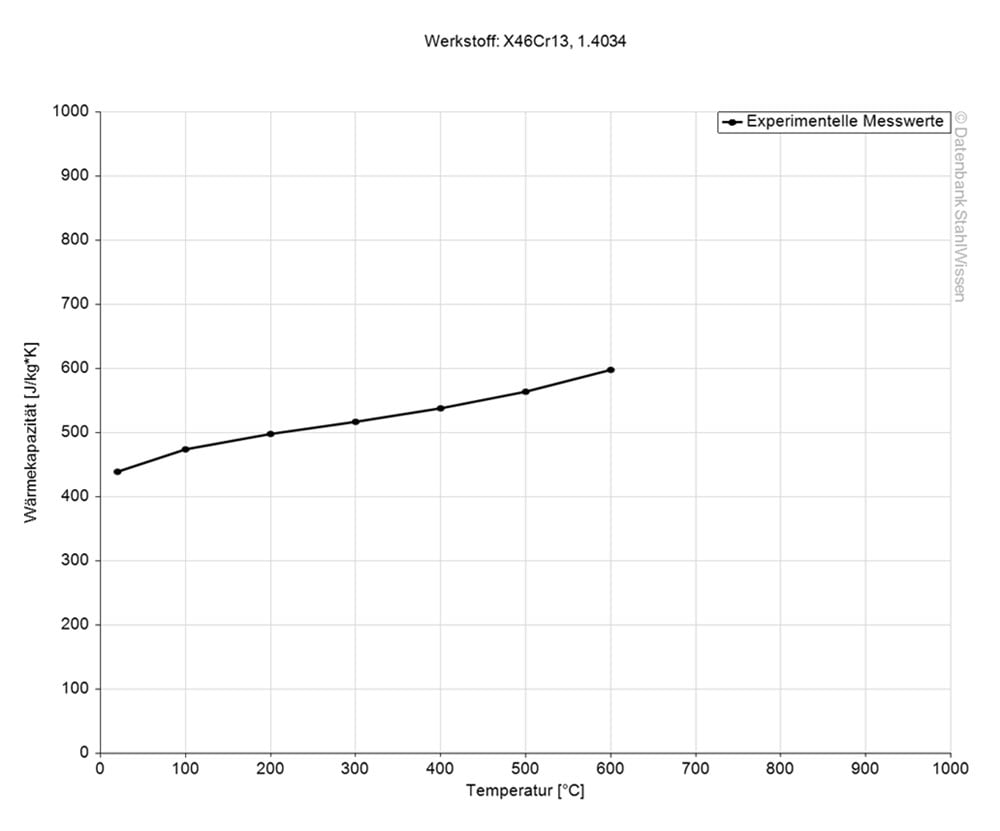
You can find the temperature dependent material constant (Resistivity) in the following table. The electrical conductivity is the reciprocal value of the specific resistance.
Table of the specific electrical resistivity | |
Value | At a temperature of |
0.55 (Ohm*mm²)/m | 68°F |
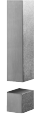
ORDER THE SMALLEST AMOUNT - WITHOUT A MINIMUM ORDER VALUE!
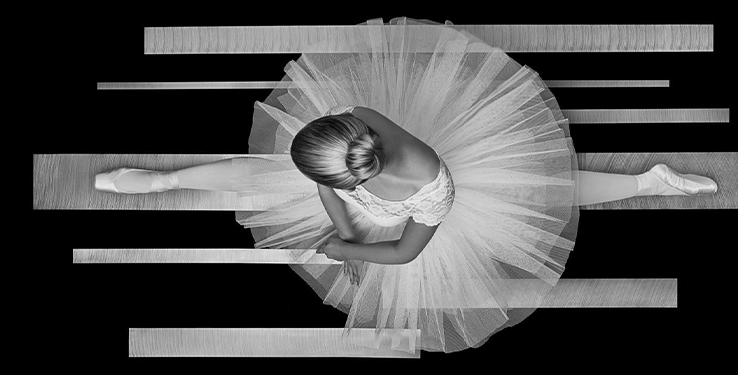
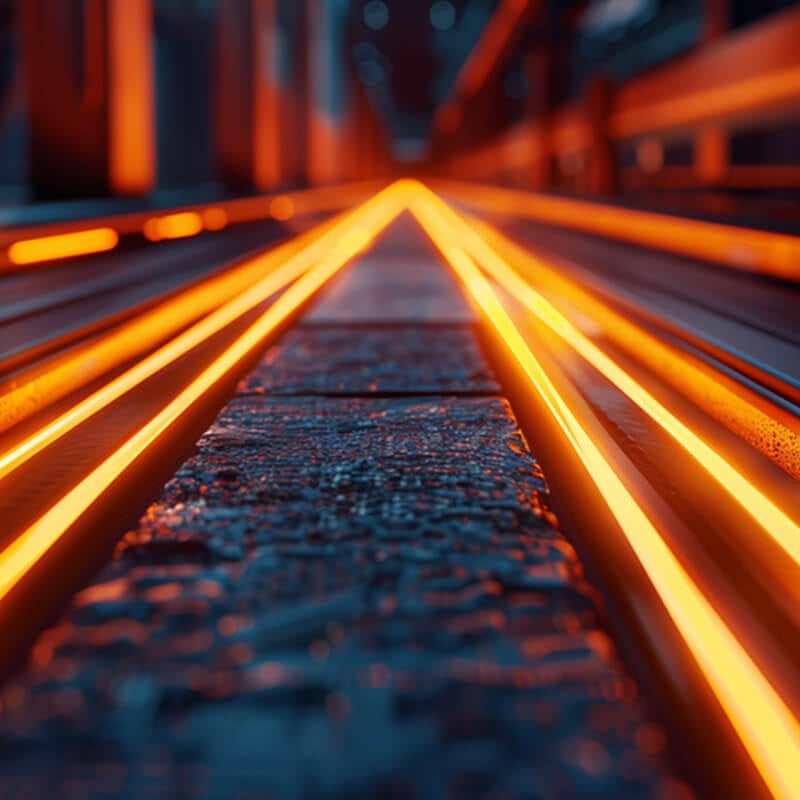

420 PROCEDURE
To anneal 420 stainless, hold the material at a temperature range of 1382-1562°F (750-850°C) and cool slowly in the furnace or in air.
Heat the workpiece to a temperature of 300-800°F (149-427°C) and hold for 1-3 hours, then cool in air or quench in oil or water.
Heat the steel uniformly to a temperature range of 1742 - 1922°F (950 - 1050°C) and follow this up with a rapid cooling in air or oil.
During quenching the 420 stainless steel undergoes the phase transformation from austenite to martensite. Quick cooling can achieve a higher hardness, the quicker the material is cooled down the more martensite form whereas a slow cooling of this material may leave some austenite or other phases behind. Rapid cooling though has its risks too, it may introduce stresses that can lead to quench cracking and may cost the parts its toughness.
To reach a variety of hardness values and mechanical properties, heat the work piece to 300 - 1292°F (150 - 700°C) and cool in still air. For optimal corrosion resistance and mechanical properties, the temperature range of 797-1112°F (425-600°C) should be avoided.
Tempering this steel grade at low temperatures will achieve a higher hardness, while higher temperatures improve the toughness but will decrease the hardness.
Reduced impact toughness might be the result of temper embrittlement which might occur when tempering in a range of 800 - 1100°F (425 - 595°C).
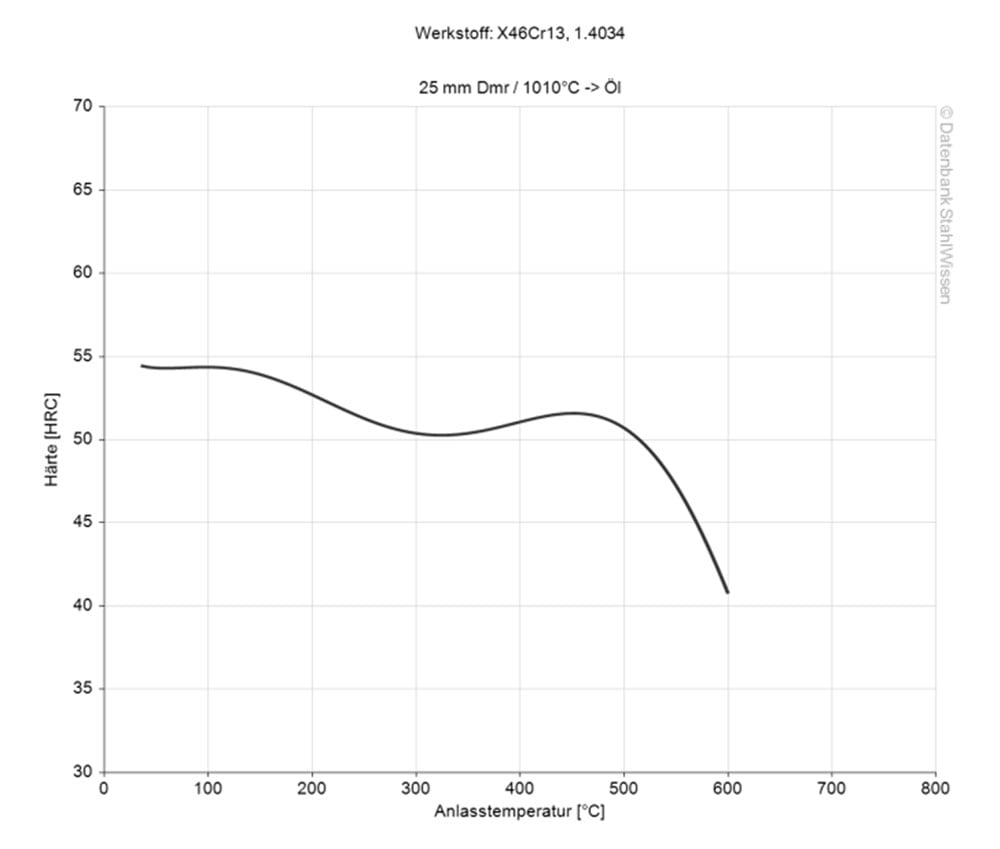
To reach a variety of hardness values and mechanical properties, heat the work piece to 300 - 1292°F (150 - 700°C) and cool in still air. For optimal corrosion resistance and mechanical properties, the temperature range of 797-1112°F (425-600°C) should be avoided.
Tempering this steel grade at low temperatures will achieve a higher hardness, while higher temperatures improve the toughness but will decrease the hardness.
Reduced impact toughness might be the result of temper embrittlement which might occur when tempering in a range of 800 - 1100°F (425 - 595°C).
This diagram shows the micro changes at different temperatures which are important during heat treatment. They show the optimum condition for the hardening, annealing and normalizing process.
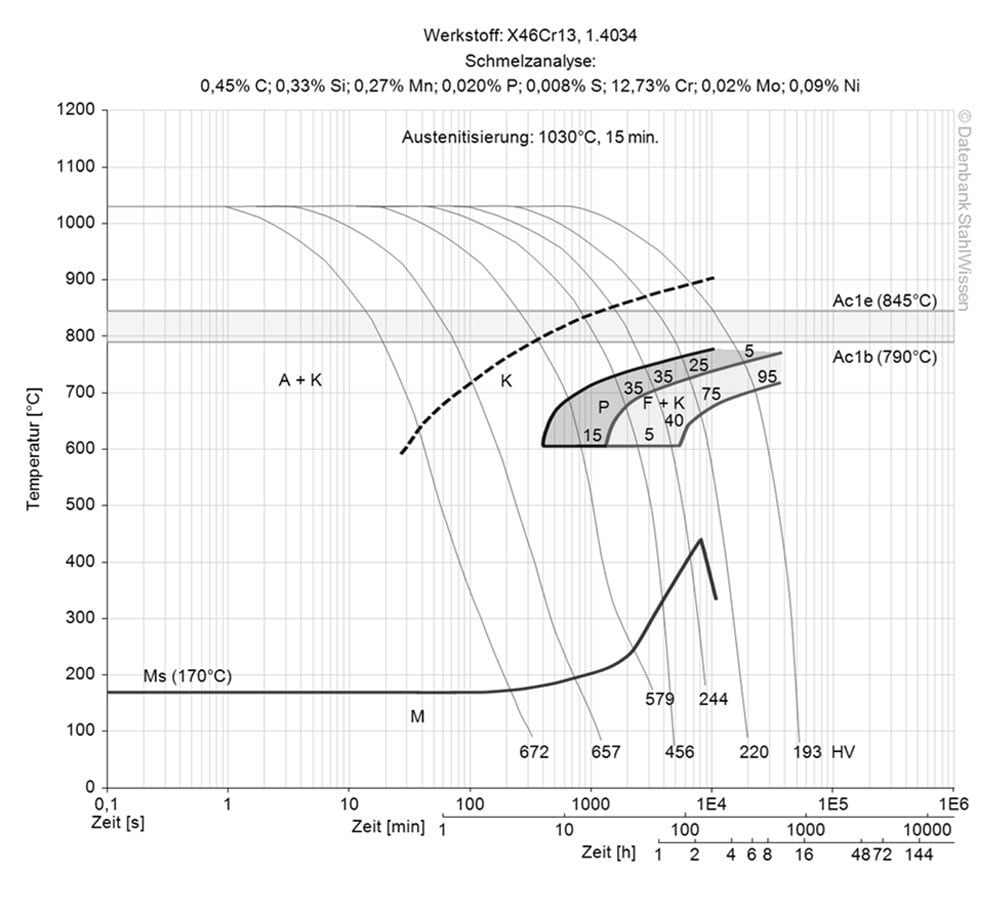
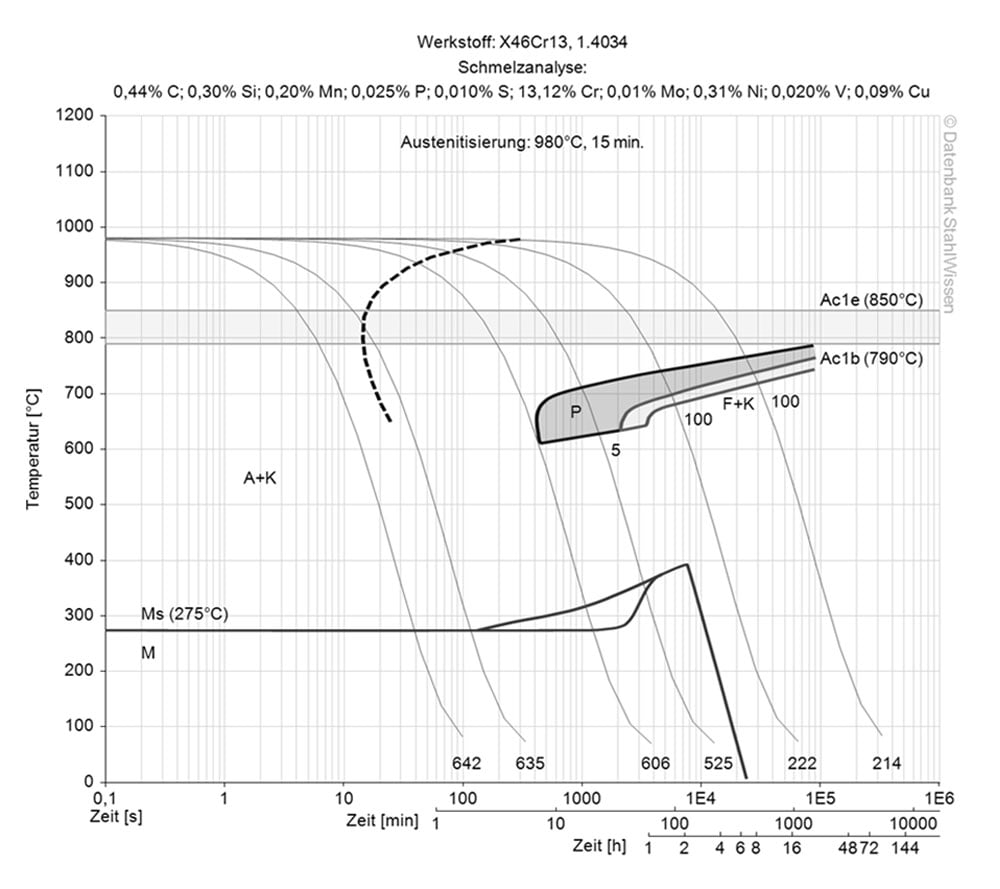
This diagram shows the micro changes at different temperatures which are important during heat treatment. They show the optimum condition for the hardening, annealing and normalizing process.
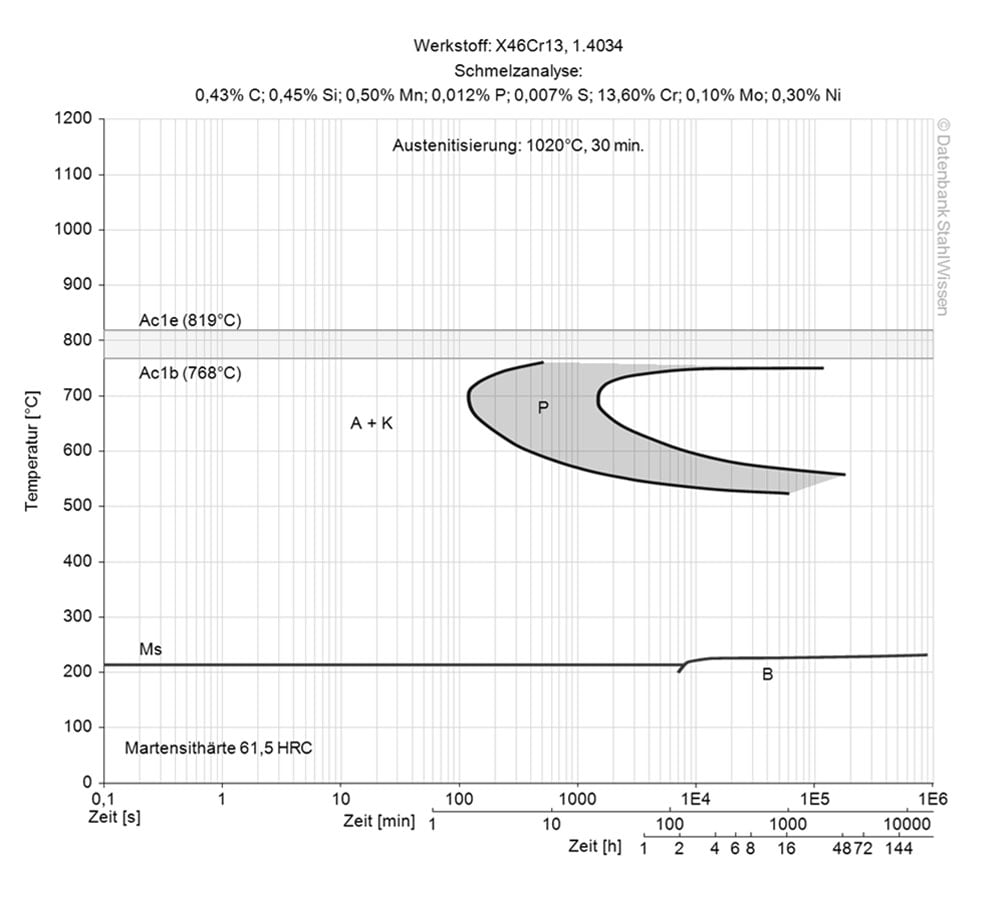

420 SURFACE TREATMENT
When contemplating a surface treatment the finish and intended application should be taken in consideration. Some surface finishes can impact properties needed, if corrosion resistance is a needed property, a surface treatment that enhances the natural corrosion resistance should be chosen.
Below are some examples for possible surface treatments.
Passivation increases corrosion resistance by treating the surface with an acid solution to remove free iron from the surface.
Polishing the surface to a mirror finish can improve its own corrosion resistance as a smooth finish can minimize adhesion of contaminants.
As a non-mechanical chemical process using an electric current to remove a thin layer of material will give the 420 a smooth and shiny surface. It can minimize bacterial adhesion which can be an advantage for medical tools and /or food processing equipment.
As well as the surface treatments before, nitriding can enhance the natural corrosion resistance by introducing nitrogen into the surface. This process can also improve its wear resistance.
This process is an impact treatment where multiple high velocity shots are blasted onto the material surface leaving small indentations removing stress risers. It makes the surface more resistant and can prevent fatigue and stress corrosion failure.
Note: Protective gear like goggles, masks, helmets, gloves and protective clothing should be worn and adequate ventilation or dust extraction should be provided.
Appropriate guards to prevent shot spillage should be in place, equipment regularly maintained and shot should be free from contaminants.
Abrasive particles like glass or ceramic beads are blasted against the surface to remove contaminants like rust, paint or scale and to promote a uniform matt finish.
Note: Care has to be taken during this process as the process produces dust and small parts might be propelled back. Protective gear like masks, helmets and protective clothing should be worn and adequate ventilation or dust extraction should be provided.
This is a superficial treatment that may enhance corrosion resistance but is most often used to color the surface blue-black to reduce the reflection of light.
Physical Vapor Deposition (PVD) and Chemical Vapor Deposition (CVD) deposit a thin layer over the material surface to give it additional protection, enhance wear resistance and lubricity.

420 PROCESSING
420 stainless steel machines similar to some high carbon steels and creates tough stringy chips.
Annealed the material is, to some extent, easier to machine than in its hardened condition.
EDM can be used to achieve various surface finishes but is mainly used to produce intricate shapes, small details and complex geometries in hard material. As the 420 is at the higher end of hardness EDM can be used successfully. Care with electrodes, dielectric fluid and cutting speeds should be taken with finish and applications in mind.
While transforming from austenite to martensite there can be a slight shrinkage which might have an impact on the dimensions of the parts and retained austenite might further impact dimensions during tempering.
Slowly heat the workpiece to a temperature of about 1472°F (800°C), then more rapidly to 1922-2084°F (1050-1140°C). Forging should be done in the temperature range of 2012-1472°F (1100-800°C), then slowly cool in the furnace, dry ash or materials that will promote slow cooling.
While forging has its advantages, like grain refinement, elimination of porosity, better directional strength and an improved microstructure to name just a few, it has some disadvantages as well. Forging can, especially in its hardened condition, be hard on tool wear, form an oxide scale that needs to be removed after forging, and may require a heat treatment after forging. Forging is reduced to the more rough shapes compared to casting, machining or EDM.
As an air-hardening steel the 420 stainless steel is rarely welded.
If welding cannot be avoided, preheat to 300-400°F (149-204°C) before welding, then anneal 6-8 hours at a temperature of 1350-1450°F (732-788°C) followed by air cooling. To retain its mechanical properties, if fillers are required, the filler should be similar to the base material.

420 APPLICATION OPTIONS
Due to the combination of high hardness, corrosion and wear resistance and polishability the 420 stainless steel can be used for applications like razor blades, dental and surgical instruments, plastic molds, and machine, valve and firearm parts.
• Mechanical engineering
• Medical technology
• Plastic molds
• Synthetic resin mold tools
• Die casting tools
• Cutting tools
• Machine knives
• Scraper blades
• Surgical instruments
• Measuring tools
• Ice-skates
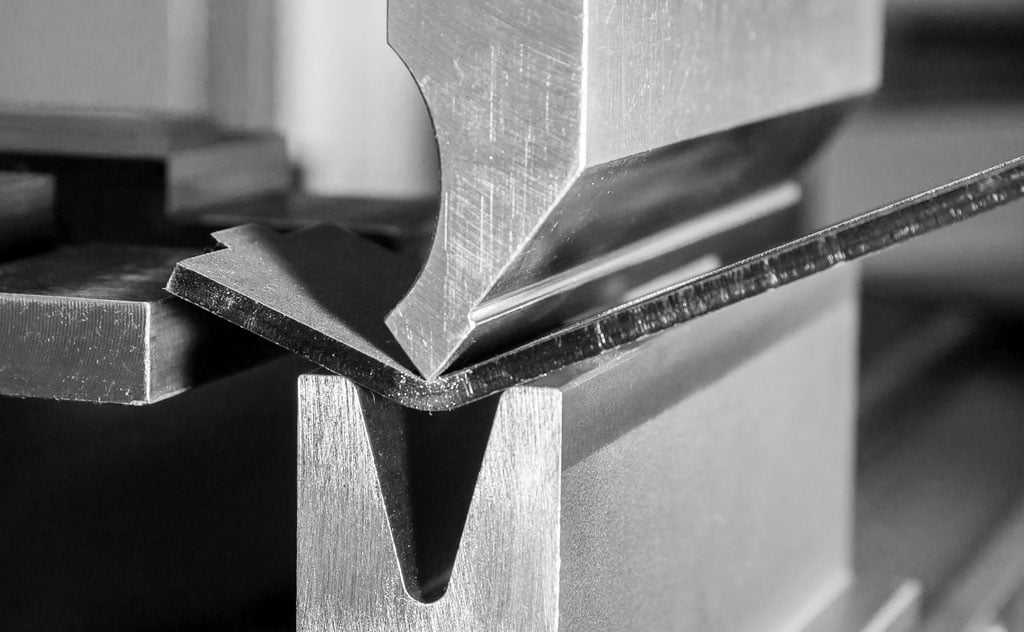

420 CONCLUSION
Considering the applications and properties, 420 achieves good hardness, strength and wear resistance when hardened and has good corrosion resistance, even if it is at the lower end compared to other stainless steels. This makes it a good choice not only for knives, but also for cutting instruments, tools and decorative applications.
- Corrosion resistant cold work steel
- Plastic mold steel
- Martensite
- Good machinability
- Magnetizable
- Hardenable
- Polishable
- Low distortion through hardener
- High hardness acceptance
- Good wear resistance
- Poor weldability
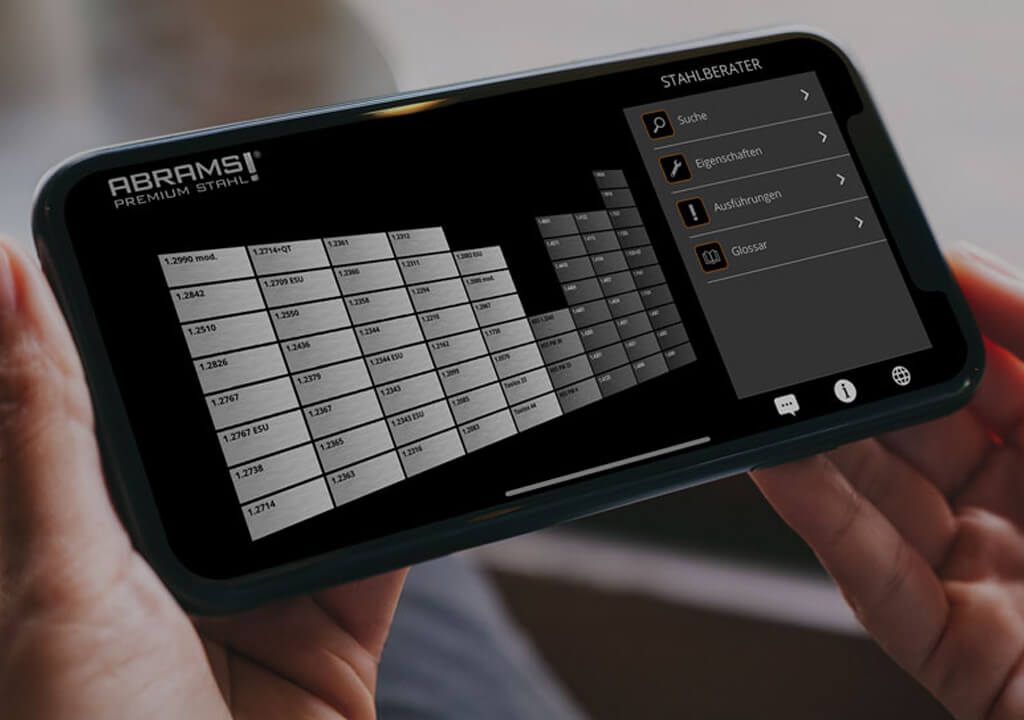

420 ALTERNATIVES
Are you looking for an alternative steel grade?
WE HAVE THE SOLUTION!
With the ABRAMS STEEL GUIDE, you can obtain an alternative or equivalent steel grade with just a few clicks.

420 DATASHEET
Download the technical data sheet in PDF format here.
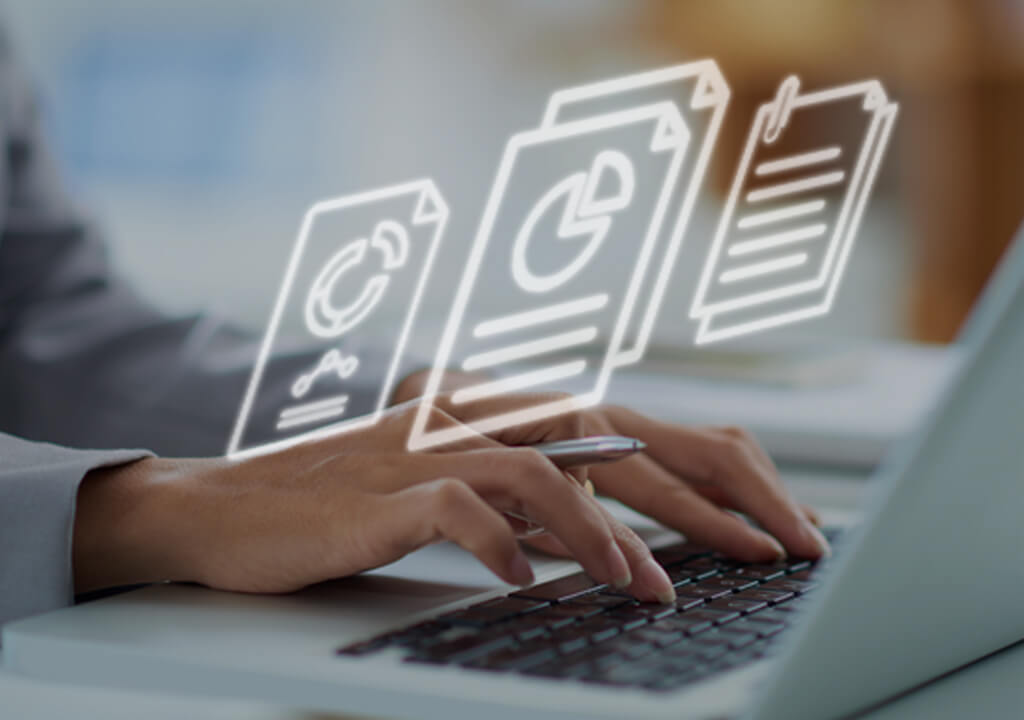
The data shown here has been compiled with the greatest diligence and is regularly updated with regard to the correctness and completeness of its content. The content is indicative only and should not be taken as a warranty of specific properties of the product described or a warranty of suitability for a particular purpose. All information presented is given in good faith and no liability will be accepted for actions taken by third parties in reliance on this information. ABRAMS Industries reserves the right to change or amend the information given here in full or parts without prior notice.